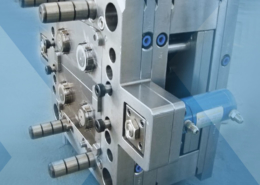
2-Shot Injection Molding Manufacturer | Injection Molding ... - plastics molding
Author:gly Date: 2024-10-15
Steel injection molds also come from the same process. However, they are expensive and take months to manufacture. This is due to the rigidity and hardness of steel. Due to steel’s hardness, it requires special manufacturing equipment and undergoes thermal processing to increase its mold life.
Silicon is the most suitable element employed as an alloy in designing aluminum plastic injection molds. This is due to its high specific heat capacity, i.e., it retains heat better than aluminum.
Due to steel’s extreme hardness, damaged or deformed steel molds may prove extremely difficult and expensive to fix. Often, a new mold is the only solution. However, aluminum plastic injection molds are from softer materials, and their design is separable and straightforward. This feature makes it easy to repair and modify in case of an error in the aluminum injection mold.
Upload your design files at RapidDirect to get manufacturing advice for your injection molded parts manufactured with aluminum tooling.
As for workpiece accuracy, a tool that has adequate mechanical strength and rigidity is necessary. Aluminum has strong metallic characteristics, which maintain its rigidity and strength to a certain level. It is also ductile making it the right material to use tooling.
Steel molds are not flexible as their hardness is due to the heat treatment after the design of vital parts of the mold. However, compared to steel injection molding, aluminum molds come from softer materials.
Mold robustness refers to the number of parts a mold can make before it becomes too corroded or worn out. This factor is hugely dependent on the design and the genetic makeup of the mold.
Based on different features, there are many differences between aluminum injection mold and steel plastic injection mold. This goes above the materials used in making them (Aluminum and Steel) and is more based more on their features, designs, and applications.
We at RapidDirect provide optimized aluminum injection mold design in product manufacturing. Consult with our support team for manufacturing advice. If you already have a CAD file, upload it now to get an instant quote for your design.
Engineers cannot improve aluminum mold design in case of a need to make modifications due to the ability of molded parts to impact the mold. However, steel molds can be toughened via heat treatment to handle developed materials of varying densities.
Doing this ensures the thickness of plastic part is constant, simplifies the aluminum molding process, and allows progressive solidification to occur quickly.
Aluminum is useful in tooling due to its many properties, which aid in creating low-volume injection molds at a reasonable cost. Of its features, below are the important ones that make it ideal in aluminum injection molding and tooling in general.
Inserts of different shapes and different materials such as brass thread inserts can be incorporated into aluminum mold design to enhance the durability of the mold and offer extra-hard surfaces where needed.
A tool must be strong enough during the manufacturing process. In aluminum injection molding, the correct choice of cutting parameters, grades, and geometries will also lead to a more efficient aluminum molding process. Therefore, aluminum alloys used in tooling will increase productivity while lowering the cost-per-component ratio.
This makes it an important material in the product manufacturing process that requires fast and effective production. It also makes it ideal for the injection molding process.
Silicon is not the only suitable alloy. Any alloy used should have a short freezing range as it helps to promote solid mechanical properties in products.
Conventional injection molding relies on steel injection molds to produce a large number of parts. However, steel molding possesses certain limitations. Therefore, there is a need for an alternative process like the aluminum molding process.
Aluminum mold is ideal because it guarantees the easy production of complex products with minimal parts. Also, it guarantees stable products with consistent structures, high accuracy, and smooth surfaces. This results from its properties such as its ability to effectively transfer heat from the mold and guarantee faster product formation.
Aluminum has a high coefficient of thermal expansion. Therefore, after heating to the right temperature, it can easily cool down which makes production fast.
You’re also likely familiar with the potential for aluminum injection molds instead of steel injection molds in certain scenarios, since the advantages of aluminum — in the right situations — have been broadly discussed regarding injection molding. Priorities and requirements are different for every project. In this piece, we’ll take a side-by-side look at some benefits and disadvantages of aluminum molds and steel molds for 10 key factors.
The extremely high level of precision needed within the aerospace industry makes CNC machining a suitable manufacturing process for the sector.
However, aluminum prototype mold come from aluminum which, compared to steel, is a soft material. Therefore, it has lesser mold robustness than steel injection molds. Nevertheless, alloys made from aluminum are strong and can guarantee a batch of up to 5000 parts.
Aluminum injection mold cost is lower compared to steel in manufacturing an injection mold. The overall worth and return on investment of a mold can depend significantly on mold usage. Nevertheless, the initial tool investment for aluminum is less if all other factors are equal.
Aluminum prototype molds dissipate heat much faster than steel molds. Hence, they can heat and cool much more quickly. During injection molding, the cooling time accounts for the overall cycle of the molding process. Therefore, choosing an aluminum molding process allows a shorter cycle, which translates into the faster production of parts.
For low-volume batch production of parts, aluminum plastic injection molds offer better value. This is due to their reliability in providing lower upfront costs and producing reliable parts in thousands.
If you want to produce high-quality machined parts with a sleek appearance, it’s essential to consider some critical factors related to CNC machining.
When designing aluminum plastic injection molds, rather than sharp corners in the design, use fillets. The presence of sharp corners in the procedure may significantly differ in shrinkage of the produced part, leading to cracking or permanent deformity.
Its design is such that it allows the creation of its mold parts separately, which allows easier removal to adjust prototypes.
One of the biggest reasons for defects in parts such as sink marks, voids, and burn scars is non-uniform heating and cooling. The excellent heat dissipation characteristics of aluminum molds provide the advantage of allowing the mold to heat and cool quickly and uniformly, thereby reducing the number of defective parts and rejects.
Injection molding is a manufacturing process used to produce prototypes and real products. It is reliable and efficient as it allows the production of complex product parts with better quality and yield. The injection molding process hugely depends on the design and materials used in better production. Therefore, manufacturers seeking simpler mold processes that allow for better products at a lower cost favor the use of aluminum injection molding.
Making revisions without creating capacities for such at the beginning start is possible. Nevertheless, in most cases, it involves sacrificing the tool.
Conventional injection molding process/steel injection molding process surely produces durable products. However, they leave a lot to be desired, as they do not guarantee quick production. In this article, we will discuss aluminum injection molds, their advantages, disadvantages, and features. Read on.
Steel injection molds are hard since their manufacturing process includes heat treatment. They also possess few joints, which makes them rigid and durable. Thus, steel injection molds can produce millions of parts.
Aluminum plastic injection molds are suitable for smaller part runs. However, steel molds are more durable as they are corrosion-resistant, wear-resistant, and thermally stable. This allows for the production of more products.
However, engineers can replicate the same durability of steel by nickel-plating or annealing aluminum mold design. It would increase aluminum injection mold cost which will negate the cost advantage associated with aluminum tooling.
Flashing is the formation of excess material on a mold due to worn-out cavities that no longer fit tightly. After several thousand production cycles, aluminum plastic injection molds will wear out and have non-conformities, leading to flashing in the product.
On the one hand, thinner sections in an aluminum mold design tend to cool and solidify first. On the other hand, dense areas act as reservoirs that feed the lighter cells as they cool and harden.
Aluminum injection molds are not strong enough to withstand intense pressure and temperature. Therefore, the production time for aluminum prototype molds is usually within 40 – 70 seconds. However, steel injection molds can withstand high temperatures and pressure better than aluminum molds and require only a few seconds to produce parts.
Aluminum prototype mold can seem overwhelming. However, with the right company with a heightened knowledge of the process and an excellent record of handling product development, you can guarantee better product formation.
Aluminum molds guarantee a faster path for the production of products. Steel injection molding can take months from designing the mold to realizing the final product. However, aluminum injection molds only require days to create molds, prototypes, and final products.
Aluminum plastic injection molds are manufactured using aluminum material by the CNC machining process. Sometimes manufacturers use Electrical Discharge Machining (EDM) when cavities must have sharp corners. Nevertheless, a typical aluminum cavity is made in about 10-15 days as the process requires only mechanical methods. There is no need for special manufacturing equipment or thermal processing is needed.
During aluminum mold design, it is beneficial that your design includes a procedure for potential revisions down the line. Although this may increase aluminum injection mold cost, it may prove cost-effective later when correction is needed.
Production time is the time taken from the injection of polymer to the ejection of the final product. It is an essential factor in the batch product manufacturing process and it depends on the material of the mold, temperature, and pressure.
Aluminum plastic injection molds offer limited surface finishes compared to steel molds due to their low density. The high density of steel allows for various texture selections and custom finishes by adding steel inserts.
The use of aluminum or steel injection molding would depend significantly on the nature of your design and the type of products you intend to achieve. While both injection processes are complementary alternatives, they both provide distinct advantages and disadvantages that engineers must consider before adopting a manufacturing process.
The lifespan of an aluminum injection mold depends on its use in product manufacturing. When used for prototyping, aluminum injection molds can produce a few thousand parts due to the density of their molds. However, the lifespan shortens when used for intense product manufacturing.In recent times, processes such as surface coating and anodizing have been incorporated to improve the durability of aluminum molds, making them useful in production cycles.
Despite this, most parts have varying cross-sections and tend to freeze faster than thicker parts. Hence, feed paths must be such that they consider the solidification in both the thick and thin sections.
If you’ve been reading our blog for any period, you’ve likely noticed that we’re big proponents of seeking the right material for the right application (whenever such flexibility is possible) in spite of what “conventional wisdom” might tell you. In the world of manufacturing and plastic injection molding, there are more variables and, thus, more options than you might think.
Aluminum injection molding cannot withstand the intense temperature and pressure associated with injection molding processes for extended periods. Therefore, they are not ideal for long-term and high volumes of part production.
As always, be sure to fully outline the requirements and specifications of your project before moving forward with manufacturing and material choices such as mold material. If you have any questions, RevPart is here to offer our expertise and help.
The failure of an aluminum mold for plastic injection molding is often due to a poor design or poor tooling practices, alongside a faulty aluminum alloy selection. Therefore, this article introduced aluminum injection molding, its characteristics, and some design tips.
The aluminum mold design is an essential step in the product manufacturing design process. This is because it determines the durability of products and the efficiency of the mold.
Aluminum injection molding is an innovative technique based on injection molding used to produce parts (either prototypes/real products) with aluminum tooling. It is a perfect alternative to steel injection molding in rapid prototyping and has wide adoption in automotive, aviation, and industrial processes.
GETTING A QUOTE WITH LK-MOULD IS FREE AND SIMPLE.
FIND MORE OF OUR SERVICES:
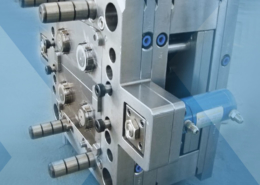
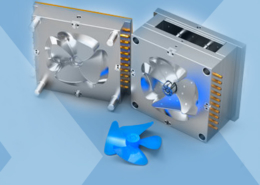
Plastic Molding

Rapid Prototyping
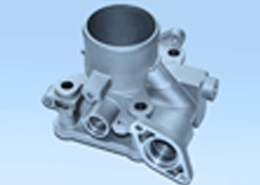
Pressure Die Casting
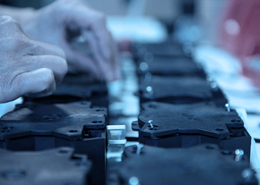
Parts Assembly
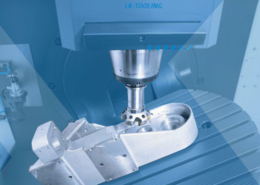