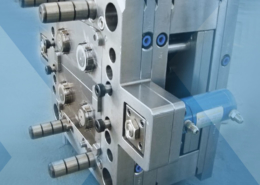
11 Most Popular Injection Molding Materials - injection moldable plastics
Author:gly Date: 2024-10-15
Double-shot moulding is suitable for backlighting: the first shot can be made from a translucent plastic. Vortex, Tai-Hao and Topre all offer backlit double-shot keycaps. In Topre's case, the first shot cannot support fully enclosed shapes, giving a stencil-like appearance.[4] Neither Vortex's or Tai-Hao's processes are affected by this limitation.
Comptec were one of the world's leading keycap manufacturers, whose keycaps have been found in a large variety of equipment including the Acorn BBC Microcomputer and Wyse terminal keyboards. Comptec USA became Signature Plastics, who remain a very prominent double-shot manufacturer. Tall Comptec keycaps often feature an inner step that appears to be specific to their manufacturing process.
Cherry produced double-shot keycaps in-house, they discontinued the manufacture of double-shot keycaps in 2011. The tooling was sold to GMK, who resumed manufacture of the parts.
For an ultra high-temp plastic like PEEK, the injection molding machine barrel will reach temperatures above 400 °C, with the molds around 160 °C. These high temperatures can pose certain issues, such as residue getting stuck in the barrel feeder areas. High-temp materials like PEEK often necessitate purging of the machine before use of a subsequent molding material.
3ERP has many years of experience making prototypes and production parts via injection molding, and we can mold parts in the above materials and many more besides. Request a free quote for your next batch of high-temperature plastic parts.
Polyether ether ketone (PEEK) is a high-performance polymer used for engineering purposes. With a melting temperature of 343 °C, it is as robust and strong as it is difficult to process. Its extremely high CST makes it suitable for applications in demanding industries like aerospace. Example PEEK parts include bearings, pumps, and compressor plate valves.
Engineers will select a thermoplastic based on the requirements of the molded part. Some moldings need to be impact-resistant, some need to be food-safe, while others need to be flexible. Another property that engineers and product designers often require is heat resistance. Heat-resistant molded parts can be used in a range of situations, such as near engines, within powerful electronic parts, and in extreme outdoor environments.
Nylon 66 is one of the more heat-resistant polyamides (PA) that is widely used in injection molding. With good mechanical strength and rigidity, nylon 66 has applications in the automotive industry for under-the-hood components like air intake manifolds. Glass-filled PA66 has a slightly higher CST, while PA46 is another good choice for high-temp applications.
The Topre Realforce RGB comes with backlit double-shot keycaps. These are one of the product ranges that show a stencil look to the first shot.[4] While sold by Topre, it is not confirmed that Topre manufacture the keycaps themselves.
Another molding consideration with high-temperature plastics is unwanted freezing off of the nozzle or mold gates. If temperatures are not quite high enough, gates or the machine nozzle can freeze off before the mold cavity is completely filled. Larger gates may mitigate this issue if it persists.
Despite the name, the moulding process is not restricted to two colours: triple and quadruple[2] shot keycaps exist, where two or three different legend colours are present on a single keycap. The use of more than three colours is however quite rare. More commonly, where multiple legend colours are required, the additional colours are provided using pad printing (dye sublimation would be unsuitable with the ABS material used in double-shot moulding). This is especially true where the extra text is printed on the front of the keycap, such as with NeXT keyboards.
Polyetherimide (PEI), often known by the brand name Ultem, is a high-performance polymer often used as a slightly more affordable alternative to PEEK. As well as performing well in high temperatures, it offers good strength, ductility, and chemical resistance. Applications of PEI include medical components, throttle bodies, and thermostat housings.
Polyoxymethylene (POM) or acetal is another engineering thermoplastic in a lower price bracket than ultra-premium materials like PEEK. It provides good stiffness and low friction, with a relatively high CST. Molded POM can be made into various engineering parts like gears and fasteners, as well as automotive and electronics parts.
Polyphenylene sulfide (PPS) is another high-performance polymer with engineering applications. As well as having a high CST, it exhibits excellent UV and chemical resistance, making it suitable for outdoor use. PPS parts include gaskets, seals, and electrical insulation. Polyphenylsulfone (PPSU) is slightly weaker and less thermally resistant, but exhibits greater hardness.
Because the injection molding machine must melt down pellets of the chosen thermoplastics, high-temperature materials are necessarily more difficult to process. However, with the right setup, it is still possible to achieve high-quality moldings using these engineering materials.
Vortex are one of the manufacturers of PBT double-shot keycaps. Vortex backlit keycaps use translucent POM for the first shot, and PBT for the second shot.[8] Vortex also offer non-backlit double-shot PBT keycaps.[9]
Double-shot moulding, double-shot, dual-injection moulding, two-shot moulding or insert moulding is the process of moulding plastic around a preformed metal or plastic insert. This has been a popular process to create very durable keycaps in the past, used extensively in the 70s and 80s and still found into the 90s. Once a staple of keyboard manufacturing, during the 1990s double-shot moulding faded into obsolescence as keyboards were reduced to a simple commodity.
So which are the best heat-resistant thermoplastics for injection molding? This article discusses some of the most popular thermally resistant injection molding materials, noting their respective advantages and applications, as well as discussing the complexities of using such materials during the injection molding process.
ABS is typically chosen because most other plastics shrink too much in the moulding process.[Citation needed] Modern ABS however lacks the desired wear resistance, leading to keycaps that develop shine too readily. However, PBT double-shot keycaps are now produced by both Vortex and Tai-Hao.
Engineers sometimes need temperature-resistant moldings that do not need to be of aerospace-grade quality. In these cases, they can choose from more affordable temperature-resistant polymers with good engineering properties. (For the lowest possible budgets, engineers might select a commodity polymer like ABS, which has a reasonable CST of 90 °C but which is also sold in various “high heat” ABS formulations resisting up to 110 °C.)
Until early 2010, Cherry still offered double-shot moulded keycaps as an option for their POS and special-order keyboards. Production ultimately stopped and all keyboards with double-shot moulded keycaps were called off. November 2012, it was announced that German company GMK had acquired the original tooling and moulds[5]. In December 2012, EliteKeyboards offered the first GMK product in the form of a double-shot Cherry Escape key[6].
Other manufacturers use a wholly or near-wholly solid first shot, that gives keycaps a "nested" or "stacked" appearance when viewed from below. Regardless of the specifics, double-shot keycaps can be identified by observing the underside where both colours are visible.
The technicalities of this process vary quite distinctly between manufacturers. In many cases, the process leads to a striped pattern within the keycap formed from the two different coloured plastics. This striped pattern remains even when keycaps are manufactured for engraving or other marking processes, as is clearly visible with Devlin Q series keycaps.
Polycarbonate (PC) is often used for its high-quality appearance — especially for transparent parts — and good impact resistance, but the thermoplastic also offers good heat resistance. PC can be molded for uses in electronics, automotive, and aerospace. It is also used for optical and lighting components like headlamp lenses.
SMK double-shot keycaps have varied in design over time. All their keycap styles have in common a completely solid first shot, without striped bands of colour. Older keycaps (from SMK vintage linear keyboards) had a large first shot (giving thick keycaps), while newer keycaps for SMK second generation switches reduced the size of the first shot. It is not known whether they were produced in-house or outsourced.
The majority of double-shot keycaps are made entirely from ABS plastic. Despite their greater wear resistance, Signature Plastics have confirmed that the majority of Comptec keycaps were nonetheless made from ABS, albeit of different formulations (the plastic formulations have since changed due to regulatory requirements).[3] Older Cherry catalogues show that in 1982, the tall Cherry M7 and Cherry M9 keycaps were made of double-shot Tenite, while their other double-shot keycaps were all ABS.
Tai-Hao are a long-time manufacturer of double-shot keycaps, both Cherry MX mount and Alps mount. Their widely-used TI series is still manufactured to this day, and has been extended to cover PBT keycaps. Tai-Hao keycaps were used by brands including Ortek, Focus Electronic and Northgate Computer Systems.
While Alps are better known for the dye sublimated keycaps used in Apple keyboards, Alps also produced distinctive double-shot keycaps. Alps are one of the companies whose moulding process did not show stripes of colour within the underside of the keycap. Many double-shot Alps keycaps feature a curious pattern of bars and square holes that aids in their identification.
The most temperature-resistant injection molding plastics come at a high cost but exhibit excellent thermal performance, both in terms of their continuous service temperature (CST) — how much heat they can withstand over long periods of time — and their resistance to even higher temperatures in short bursts.
Double-shot keycaps were a standard feature of many vintage keyboards, when keyboards were expected to be expensive. As a result, many manufacturers have produced double-shot keycaps. Only a small number of these product ranges are still known to be in production to this day. However, new product lines have arisen to cater for the gamer and enthusiast markets.
Double-shot moulding is enjoying a slow resurgence in the gamer and enthusiast markets: brands such as Vortex, Tai-Hao and Topre now provide modern backlit double-shot keycaps, and Tai-Hao double-shots are available for sale in a wide variety of colourways in both ABS and PBT plastic. These new product ranges demonstrate a willingness to invest in this technology.
Specialize in CNC machining, 3D printing, urethane casting, rapid tooling, injection molding, metal casting, sheet metal and extrusion
Injection molding can process a wide range of materials. In addition to metals and thermosets, injection molding is suited to a large number of thermoplastic polymers, from commodity polymers like ABS to high-performance materials like PEEK.
As the name suggests, double-shot moulding is a two-step process. In the first step, the legend or graphics to be placed on the keycap, are moulded in plastic[1]. The plastic insert, resulting from the first step, is then placed into another mould, and plastic is inserted under heat to combine both moulds to a single piece keycap.
GETTING A QUOTE WITH LK-MOULD IS FREE AND SIMPLE.
FIND MORE OF OUR SERVICES:
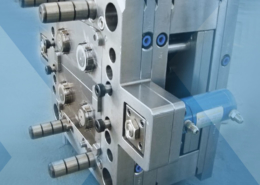
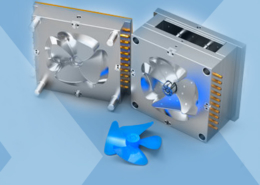
Plastic Molding

Rapid Prototyping
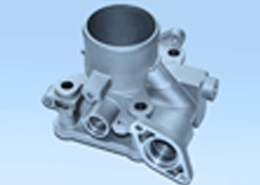
Pressure Die Casting
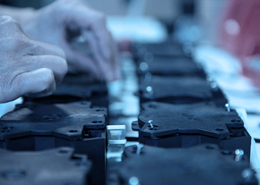
Parts Assembly
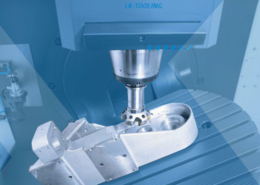