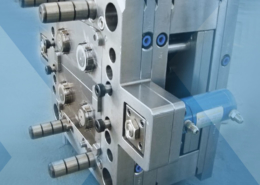
10 Popular Injection Moulding Materials - strongest injection molded plastic
Author:gly Date: 2024-10-15
Typical applications produced by injection molding are food containers, housewares, luggage, consumer goods, multimedia packaging, caps and closures, syringes and automotive parts for a wide range of market segments.
The production of automotive parts also extensively uses aluminum injection molds, including automotive components and communication parts.
Cost: Aluminum molds are cheaper to produce due to simpler processing, while steel molds are more expensive due to the need for higher precision and tougher materials.
Despite the multiple advantages that aluminum injection molds offer, their limitations in the injection molding process cannot be overlooked:
Aluminum alloy materials are typically less expensive than imported mold steel, and the unit volume weight of aluminum alloy molds is only one-third that of mold steel.
Aluminum injection molds play a vital role in the production of electronic products, such as laptop cases, smartphone housings and frames, and tablet cases.
The number or height of the ribs should be determined based on specific conditions, and the rib thickness should be less than the mold wall thickness, generally around 5mm.
In summary,aluminum molds are best for low-cost, short-lifespan, high-precision needs, while steel molds are better for long-lifespan, high-volume production requiring high precision.
Cutting speeds are 40% higher than those of mold steel, resulting in smooth and glossy mold surfaces that allow for easier demolding.
Compared to steel molds, the lifespan of aluminum molds is typically shorter, making them more suitable for small-batch production or prototyping.
The thermal conductivity of aluminum alloy is 4-5 times that of steel, enabling more efficient heating or cooling, reducing energy consumption, and significantly shortening demolding time, which effectively enhances mold production efficiency.
Guide pins and bushings should be placed between the upper and lower steel frames for precise alignment, and bolts should be used to achieve the desired tightening or opening effect of the mold.
Aluminum injection molds refer to injection molds made from aluminum alloy, which are considered the best alternative to steel molds.
ACIS®, Autodesk Inventor®, CATIA® V5,Creo™ Parametric, IGES, Parasolid®, Pro/ENGINEER®,Siemens PLM Software’s NX™, SolidEdge®, SolidWorks®, STEP
This is a high-strength, high-hardness aluminum alloy with excellent mechanical properties and machinability, making it suitable for producing large injection molds.
The thin-walled parts formed from this alloy have high hardness and strength, and it is widely used in the aerospace industry.
These products not only require a stylish appearance but also need excellent heat dissipation to ensure stability during high-performance operation.
After extended use, aluminum injection molds are prone to surface defects such as flashing, porosity, shrinkage, and warpage, which can affect product quality.
The design of aluminum injection molds is a critical step in the injection molding process, influencing the performance, lifespan, and quality of the molded products.
Aluminum molds are approximately 50% lighter than steel molds, which reduces costs associated with manufacturing, assembly, and installation, as it eliminates the need for expensive lifting equipment.
Aluminum molds also have a significant presence in the packaging industry, particularly in the manufacturing of lightweight, durable, and efficient packaging containers, such as thin walled plastic containers and food packaging.
This balance ensures effective heat conduction and dissipation, avoids energy waste, and improves production efficiency.
Aluminum injection molds, with their lightweight, excellent thermal conductivity, and ease of processing, have become the ideal choice for rapid prototyping, small-batch production, and specific industry applications.
Material: Aluminum molds are made from lightweight aluminum alloy, offering good thermal conductivity, corrosion resistance, and ease of processing.
To extend the lifespan of aluminum molds, manufacturers sometimes apply nickel plating or other surface treatments to enhance their wear resistance and corrosion resistance, though this also increases costs.
Generally , aluminum molds can withstand between 50,000 to 100,000 injection cycles, depending on the specific application.
Due to the inherent fragility of aluminum compared to steel, aluminum molds have a shorter lifespan, necessitating more frequent replacements and maintenance.
You must login to receive product stewardship and regulatory affairs information for purpose of receiving future change management communications.
When manufacturing aluminum molds, it is crucial to select the appropriate type of aluminum alloy based on the specific requirements of the mold.
The rear cylindrical diameter should be approximately φ30mm, connected to the mold cylinder through a specially designed steel frame.
The external fillet radius should range from R3 to 13mm, and the internal fillet radius should range from R1.5 to 6.5mm.
LyondellBasell serves the consumer, rigid packaging, automotive and healthcare market segments by offering a large range of polypropylene, polyethylene and specialty products (Moplen, Pro-fax, Alathon, Petrothene, Hostalen, Clyrell, Adstif, Adflex, Hifax, Purell, and Hostacom).
When frequent modifications to the mold design are required, aluminum molds are less adaptable than steel molds, making the modification process more challenging.
They are ideal for small parts and boiler components. Steel molds, made from strong and hard steel, are suitable for large parts and plastic components due to their high strength and wear resistance.
Injection molding is a manufacturing process in which a molten thermoplastic material is injected at high pressure into a mold, resulting in a desired product. Polyolefins are the most widely used plastic in this process.
As an essential aluminum tool in injection molding, aluminum injection molds have a wide range of applications across various industries:
While aluminum molds may not match steel molds in terms of durability and lifespan, they offer significant advantages in cost-effectiveness, production efficiency, and design flexibility.
If you already have 3D drawings, please upload them now, and FOWMOULD will provide you with a free quote in the shortest possible time!
Compared to traditional mold steel, the processing cycle of aluminum injection molds is shorter because aluminum alloy has excellent machinability.
Injection molds are essential tools in the injection molding process, and traditionally, they are made from carbon steel. However, in certain production scenarios, where reducing weight and enhancing thermal conductivity are important, aluminum alloys are also considered as mold materials.
This aluminum alloy has good machinability and high corrosion resistance, making it ideal for producing small and medium-sized injection molds.
As one of China’s leading injection mold manufacturers, FOWMOULD is committed to providing customized aluminum injection mold solutions, offering a one-stop service from mold design to manufacturing to meet the needs of various industries.
The use of aluminum alloy can enhance the hardness and strength of the mold, while also offering significant advantages in reducing weight and improving thermal conductivity.
Aluminum injection molds are used to manufacture components for machinery and ships, which need to be highly durable and stable to withstand complex working environments.
As a result, aluminum molds are becoming increasingly favored in the injection molding industry, especially in situations where rapid prototyping and small-batch production are required, where their advantages are particularly pronounced.
So, what are the unique characteristics of aluminum injection molds? When are they most suitable? In the following content, we will explore and answer these questions.
GETTING A QUOTE WITH LK-MOULD IS FREE AND SIMPLE.
FIND MORE OF OUR SERVICES:
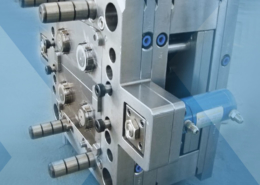
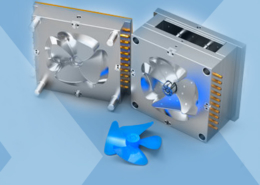
Plastic Molding

Rapid Prototyping
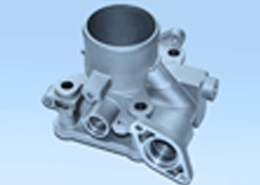
Pressure Die Casting
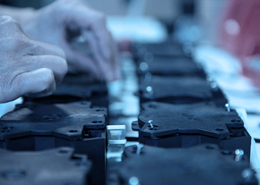
Parts Assembly
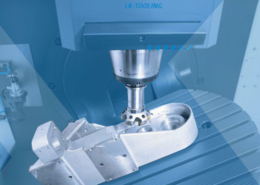