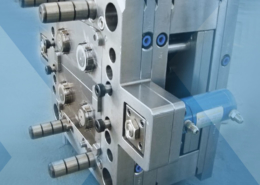
10 Best Plastic Injection Molding Companies in Australia - plastic injection mol
Author:gly Date: 2024-10-15
Specifically, products such as containers, hinges, casings and enclosures, devices, living caps, and hinges, and other functional molds across industries are made from injection molding.
Think of your favorite drink’s plastic cap. The strip of plastic which connects the lid from the cap is an example of a living hinge. Thus, in essence, living hinges connect plastics together, allowing them to be moved or rotated.
Since the shift to plastic casings, injection molding has paved the way for cost-efficient manufacture of equipment housings. One of the major benefits in using injection molding for equipment housings is that they become easier to produce, assemble, and disassemble.
You already know the products made from injection molding and why manufacturers are switching to injection molding thanks to its benefits. In this section, the most common industries where injection molding is applied are discussed.
Thus, if you are looking for a trusted and reliable custom plastic injection molding partner for parts and other products, you can check out the main site of Kemal Manufacturing.
The continued preference of manufacturers of injection molding is due to its significant benefits. Out of these, its cost-efficiency, accuracy, faster cycle time, and capacity to produce high volume, uniform products are the main reasons why injection molding is preferred.
As such, you can make hundreds of uniform molds and functional products in no time through insert molding. Otherwise, how would you think same sized plastic products are made?
If you are in the assembly line or part of the consumer products industry, you would know how snap fits make the assembly of plastic products easier. Snap fits are like puzzles, connecting plastic joints together to become more intact.
Some of the electronic applications of injection molding include the production of remote controls, appliances, fobs, computer parts, and medical devices.
Manufacturing companies rave over injection molding because it revolutionizes production. How? Because it offers cost-efficient production yet with high precision, aesthetics, and guaranteed high product value.
Instead of turning to traditional adhesives and fasteners, assembly is made less expensive by snap fits. According to Rapid Direct, the use of snap fits produced through insert molding, have made these products more flexible.
Our products and services have been a top choice for chemical processing, oil and gas, semiconductor, pulp and paper, medical, industrial, research & development, OEM, and other industries.
Our ability to manufacture, source, package, and ship parts on time even in an emergency makes CTG, Inc. your one stop sealing solution shop.
This is another product, found in plastic containers. They can also be found in the neck tetra packs like that for milk and PET bottles.
Did you know that there are at least 50 materials used in injection molding? Thermoplastics and polymers, like the ones used in beverage caps, and plastic containers are the most popular.
When designing custom Delrin injection molding, the staff at CTG, Inc. helps customers through the complete life cycle of customer input and design, prototyping (optional), tooling/mold production, and production. We may also make suggestions on seal modifications to design for assembly which will aid in installation, cleaning, and repairs.
Thus, aside from getting a lightweight, cost-efficient product, you are also using an environment friendly production method.
https://www.rapiddirect.com/blog/injection-molding-examples/https://www.ien.com/product-development/article/21014543/what-products-can-be-made-from-injection-moldinghttps://reliantplastics.com/what-products-can-be-made-from-injection-molding/https://www.msi-mold.com/injection-molded-products/https://adrecoplastics.co.uk/plastic-injection-moulding-products/
In addition to Delrin injection molding we specialize in Oil & Gas Seals, FKM Seals, Kalrez Seals, Custom Seals, High Temperature Seals, FKM Molding, FFKM Molding, PEEK Molding, PTFE Molding, 3D-Printing and many other high-performance products and services detailed on our website.
You can use your appliances, handheld equipment, and batteries, among others, without being electrocuted thanks to equipment housings. Plastic housings for medical devices, and electronics are also mass produced because of their durability and for being non-conductors.
This product is highly used in more convenient assembly. With press fittings, you can connect metals to metals, and metals with other materials without welding, or soldering, among others.
To do this satisfactorily, you must look for some of the most reputable and reliable injection molding companies which offer a convenient outsourcing service for you.
It is as if you have hit the injection molding jackpot if you make your custom plastic injection molding parts from Kemal. Founded in 1995, Kemal has mastered all the innovative production techniques to keep up with the times and a more up-to-date pool of clients.
With over 100 years of engineering expertise we are dedicated to offering the highest quality Delrin injection molding and other products.
This product is mainly found in the electronics industry. Insulators are mass produced to stop electric current in electronic products and wires by separating conductors using plastic. As is the case, what better way to produce plastic insulators than injection molding.
Like living hinges, living caps allow more flexibility without being torn apart. Living caps are often used in packaging and they come in various forms. The major types of living caps include the flat, the butterfly, the triple, and the child safe.
With all the benefits of injection molding and the range of materials you can use for your injection molding parts, outsourcing is a more convenient option.
Panels and airbag frames are easily incorporated through injection molding. Furthermore, custom made or brand-specific dashboards are now uniformly produced. These are called auto dashboards.
The technical part of knowing what injection molding is as a production technique can be too hard to swallow for the layman. Hence, what better way is there to present the applications of injection molding than to lay down what products are made with it.
Now that you already have a reference as to what everyday products are manufactured through injection molding, it is time to look more in-depth as to why producers are choosing injection molding. The following are the advantages of injection molding in manufacturing.
Everything that was covered in this section boils down to the benefit of high-volume production. This is the soul of mass production and injection molding offers that.
As have been previously mentioned, the most common, everyday application of injection molding is on consumer goods. The lightweight promise of injection molding creates more handy consumer goods.
But since plastic deck fasteners, made from resilient polymers through insert molding, are here, you now have a more durable, shock and UV ray resistant product to keep the deck boards in place.
Some are found inside these containers, hence, internal threads. The ones that are visible by the plastic bottle’s neck when you twist a bottle cap are external threads.
This has been emphasized time and again. As a production method, injection molding cycles only take a maximum of two to three minutes, overall. Just visualize. This means that you can make hundreds of uniform products in less than an hour.
Present day households highly depend on consumer products. From hangers, furniture, utensils, cups, caps, children’s toys, cribs, hampers, and more, injection molding creates lightweight, easy to store, and easy to clean household materials.
For your custom Delrin injection molding design, or reverse engineering, our exemplary service and efficient production ensures prompt deliveries coupled with outstanding service.
In this section, the answer to this question is affirmed and more, as you get to see how everyday products are, from the household to industries, are made more functional thanks to injection molding. Here are some examples of the products made from injection molding.
This could not be overemphasized. As have been mentioned in the previous sections, injection molding is behind the production of equipment housings and insulators. The main reason is that they stop electricity flow inside the electronics.
Of course, it is a different story with more geometrical products, say aeronautics or automotive gears, for example. Nonetheless, the cycle time is still 10 times faster compared to non-injection molding techniques.
It is easy to do the math here but injection molding leads to more cha-ching in your business with its high-volume production capacity.
Injection molding discards most production wastes. For starters, you no longer need fasteners. Aside from this, the post-assembly phase which makes use of more consumables is no longer needed too.
If you want a very cost-efficient production using recyclable molds, threaded inserts are the key. Threaded inserts aid production by making sure that the mold is intact without the use of additional consumables, fasteners, and adhesives.
In an economy that requires the balance of inventory and production, it's difficult to stay prepared when unforeseen issues result in equipment breaking down, power going out, or running over capacity. CTG, Inc. helps you avoid loss of production. We work around the clock to get your Delrin injection molding completed promptly while maintaining our high standards in quality and precision.
Thanks to insert molding, living hinges can be produced by the hundreds of thousands in just 500 or more cycles, according to Reliant Plastic.
Some of the major factors to consider when outsourcing your plastic injection molding parts are real-time consultation, injection molding capabilities, volume production, equipment, and tooling.
If you are wondering about the automotive parts made through injection molding, check your dashboard, glove box, door and dashboard panels, bumper, fender, tail light, among others.
In addition to custom seal design and reverse engineering we also provide emergency manufacturing and delivery, engineering, PTFE processing, Plastics Injection Molding, PEEK Processing, Rubber Molding and value-added manufacturing solutions.
As the name implies, deck fasteners are used to hold deck boards on all sides. Traditionally, deck fasteners are made from lightweight metals.
In the field of agriculture, equipment, small agricultural devices, sensors, fertilizer containers, and more, are made through injection molding. Injection molding highly benefits agriculture because of the extensive use of durable plastics.
Injection molding is full of possibilities, thus, there are other benefits of the technique that were not squared here. But if you are wondering about the immediate benefits of injection molding in your production, these are its upfront advantages.
As have been covered, injection molding is used to produce molds and parts found in the automotive, electronics, medicine, agriculture, and consumer goods industries.
To reinforce these products, thereby protecting your phone’s breakage due to slips and shocks, the most resilient plastic materials are used. These materials often include polypropylene and polycarbonate.
To make threads by the masses, injection molding is sought. According to MSI Mold, internal and external threads are made through different injection molding techniques. Nonetheless, both involve the use of polymers.
Note that the field of medicine is dependent on precision. Such is one of the benefits of injection molding. In this field, the materials commonly used in injection molding are ABS, silicone, and polyethylene.
Assessing the consumer products nowadays would make one realize how plastics have taken over consumerism. In terms of turning plastics into valuable products, one of the most effective and go-to production methods right now is injection molding.
With injection molding, you have shorter lead time due to faster cycles. You also get to use uniform molds throughout the cycle over and over. With automation, accuracy in the production of uniform materials becomes more possible.
According to Rapid Direct, through injection molding, you can produce 100,000 uniform molds and products before equipment maintenance or retooling.
From communication to delivery, our team works efficiently to provide the services you need through interaction and input from our clients. Every product we create is always made from top-quality materials on which you can depend.
The most common materials used in the production of threaded inserts are thermoplastics, thermosets, and plastics that can tolerate very high heat. Some specific examples of materials used in producing threaded inserts via injection molding are epoxies and resins.
To give you a more realistic backdrop of what you can make from injection molding, this post shall highlight the products and applications that you can get from the method. If you have ever wondered what these could be, read on.
Think about prosthetics, implants, highly sterilized medical equipment, syringes, stethoscopes, IV, and the casing of sophisticated medical devices. All of these are made from injection molding.
Through insert molding, living caps are made as extensions of their parent material, usually thermoplastics and thermosets. Living caps are usually used in packaging industries.
Yes, automobile dashboards are now made through injection molding. Since the common material is plastic and plastics are versatile and flexible, dashboards are now more conveniently produced.
Almost all the exterior parts and most of the key interior parts of automobiles benefit from injection molding. The main reason here is cost-efficiency, functionality, and durability.
When you contact us our experienced team will process your Delrin injection molding order quickly and economically without sacrificing quality.
To note, injection molding is basically used everywhere. Thanks to its applicability to most consumer grade plastics and even metals, its application to various fields as a production method is virtually endless.
Thus, industries like food, beverage, and packing industries, among others, benefit a lot from injection molding with the production of living hinges.
According to Rapid Direct, the best way to make sure that press fitting works is using inserts made from insert molding. The resilience of injection molding inserts keeps the materials intact during the fitting process.
We service the Houston, Texas, Arkansas, Oklahoma, Louisiana, Gulf Coast regions, and all of North America including Canada and Mexico.
What is a cellphone without a case, right? The most mundane example of a product made from injection molding are cell phone cases.
Furthermore, according to Adreco Plastics, using injection molding deck fasteners make it more flexible. As such, the usual contraction of wood decks is better managed.
GETTING A QUOTE WITH LK-MOULD IS FREE AND SIMPLE.
FIND MORE OF OUR SERVICES:
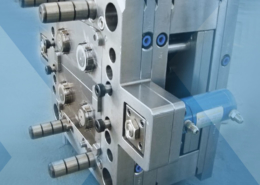
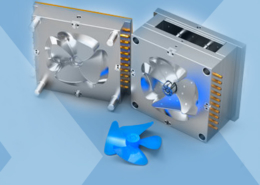
Plastic Molding

Rapid Prototyping
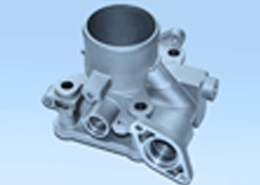
Pressure Die Casting
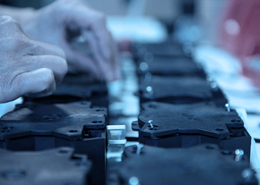
Parts Assembly
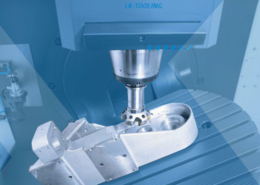