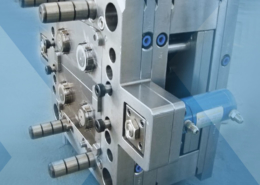
“Injection Molding at the Speed of 3D Printing” - short mould in injection mould
Author:gly Date: 2024-09-30
Some of the machines are equipped with automation systems, none of which are made by LS Mtron, a point of pride for Caprio. The company prefers to rely on forward-thinking automation experts that pursue innovation, said Caprio, rather than build an in-house team that may develop tunnel vision over time.
The modified rPET being processed at the K show comes from drinks bottles recycled in the plants of packaging and recycling specialists ALPLA Group, who are headquartered in Hard, Austria. The other collaborators involved with the project will also be at K 2022. This includes Brink (Harskamp, Netherlands) for the mould and IML automation and IPB Printing (Reusel, Netherlands) for the labels.
The companies add that the transparent, round containers feature a wall thickness of 0.32 and a volume of 125 ml. The containers are reportedly ready-for-filling as soon as they leave the production cell thanks to integrated in-mould labelling (IML).
By any measure, LS Mtron Injection Molding Machines USA has been remarkably successful at penetrating the US market in a short amount of time. In 2018, the Korea-based company had 1.5% market share in the North American injection molding machine space. By 2023, that share had grown to 7.5%. And that pales in comparison with the company’s goal of capturing 20% of the North American market. No deadline has been set as yet. It’s a tall order, but consider this, said Paul Caprio, president of sales, at a press conference at NPE2024: LS Mtron has shown consistent growth during fallow times for the plastics industry; imagine what it can achieve under better economic conditions.
According to the companies, an ENGEL e-speed injection moulding machine with a newly-developed and extremely powerful injection unit is being used to produce the thin-walled containers produced from recycled PET in a single step.
The company is exhibiting in booth W1101 at NPE2024, which is running at the Orange County Convention Center in Orlando, FL, through May 10.
LS Mtron is reinforcing that message of confidence on the NPE show floor, where it has tripled its footprint to 13,500 square feet and populated the space with several signature production cells. These include a 1400-ton hydraulic press molding an automotive part and a “sandwich” molder that processes virgin resin for the surface layer and recycled materials for the core. The result is a product with a quality appearance and sustainability cred.
PET offers the benefit of having a closed-loop recycling system already in place, the companies claim. They add that the innovation could remove the need to downcycle packaging into products other than bottles and provides an opportunity for bottle-to-bottle, bottle-to-cup, or even cup-to-bottle recycling.
To process rPET, ENGEL adds that it combines the new injection unit with a plasticising unit from in-house development and production specifically designed for processing recycled material. During the plasticising and injection, the viscosity of the PET is configured for thin-wall injection moulding.
In South Korea, Shin announced that it is expanding injection molding machine production at a new factory in Jinju. The 15,000-square-meter (3.7 acre) facility cost approximately $12 million and began operations last month. It will produce around 50 presses each month for shipment to customers in the United States, Europe, and Korea.
ENGEL says that it specifically developed the e-speed 280/50 injection moulding machine with its electrical clamping unit and hydraulic injection unit for the high-performance requirements of thin-wall injection moulding. The new injection unit allegedly achieves injection speeds of up to 1400 mm per second at a maximum injection pressure of up to 2600 bar when processing small shot weights with an extreme wall-thickness to flow path ratio
Editor in chief of PlasticsToday since 2015, Norbert Sparrow has more than 30 years of editorial experience in business-to-business media. He studied journalism at the Centre Universitaire d'Etudes du Journalisme in Strasbourg, France, where he earned a master's degree.
In Texas, meanwhile, LS Mtron has established a dual-purpose facility in Palestine, which will serve as a demonstration center and warehouse for its injection molding machine business as well as a second US production facility for the conglomerate’s popular tractors. The company produces more than 12,000 tractors a year at its Battleboro, NC, factory; the new Texas facility will produce another 12,000, doubling the company’s US output.
ENGEL will present solutions including a mould that can process different labels at the same time at K 2022 in Dusseldorf, running from the 19th to the 26th of October.
ENGEL, ALPLA Group, Brink and IPB Printing have collaborated to produce thin-walled containers made of PET and rPET in a single injection moulding process step.
The companies say that up until now, it has only been possible to process PET in thick-walled parts such as bottle preforms in injection moulding. The final packaging format was apparently created in a second step of the process, for example, by blow moulding.
There is ample space in the 210,000-square-foot facility on a 10.6-acre lot to manufacture injection molding machines, the company added, which is part of the company’s strategic plan for the United States.
During the NPE press conference, LS Mtron Global CEO Chai Ho Shin also shared some news about the company’s recent expansions.
The dyes used on in-mould labels for the American market can apparently be washed off before recycling, while ENGEL says that for the European market, the in-mould label floats off in the recycling process to allow for the dyes and the label to be separated from the PET.
LS Mtron is part of South Korean conglomerate LS Group, which employs more than 25,000 employees and has annual revenue in the neighborhood of $30 billion. LS Mtron Injection Molding Machines (LS IMM) is a division of LS Mtron, which was started in 1969 by another South Korean giant, LG Corp. Initially, LS IMM exclusively molded components for LG-branded TVs, appliances, and other products. As LG expanded across the globe, LS IMM followed and since then has installed thousands of machines across North America for automotive, appliance, and other applications. That heritage is valuable, according to Caprio, because it allows LS Mtron IMM to say that “we are molders ourselves. No other machine builder can make that claim,” said Caprio, adding that it gives the company a unique perspective on the best molding machine for a given application and an ability to communicate meaningfully with machine buyers.
GETTING A QUOTE WITH LK-MOULD IS FREE AND SIMPLE.
FIND MORE OF OUR SERVICES:
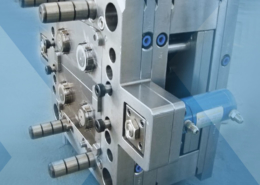
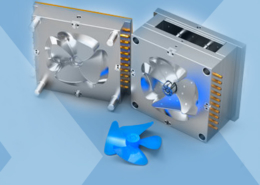
Plastic Molding

Rapid Prototyping
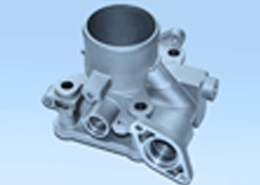
Pressure Die Casting
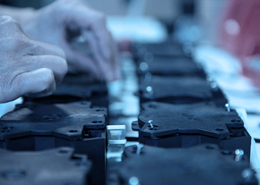
Parts Assembly
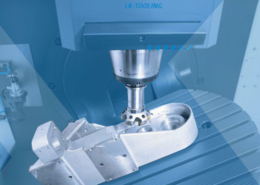