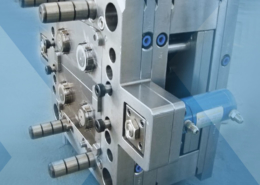
Xact Metal ‘breaks the mold’ to showcase metal Additive Manufacturing as
Author:gly Date: 2024-09-30
Shrink-wrapped and ready to go, these cases of Star Wars Lego sets will be shipped to the Czech Republic, where they will be handled by a giant distribution center there operated by DHL for Lego.
Now in the packaging department, most of the bricks are in packs that are dropped into a package automatically. But some of the packs are too big to fit in when dropped that way and must be shaken and flattened manually in order to fit properly.
Airplane wiring soon could be made of recycled plastic, and that would have a stunning impact on aircrafts’ carbon footprints. An article in The Conversation by Alvin Orbaek White, a Senior Lecturer in engineering at Swansea University in Wales, explains how replacing copper alloys with carbon wires made from recycled plastic can achieve a tenfold improvement in environmental impact.
Almost none of the plastic used in the Lego factory goes to waste, but a very small amount does get spilled. This giant bin is full of spaghetti-like plastic that has hardened and has no use.
A mold is used for about four weeks before it is pulled from the production line and completely cleaned out. Here, we see a Lego worker doing a meticulous cleaning of a mold.
Here we see two ellipsoid pieces that have just been pressed, still sitting in the mold. In a second, they will drop off and onto a belt below.
Here we see a robot arm inside the molding machine grabbing the waste from the injection and molding process. This plastic will be put into a grinder, and reused almost immediately.
The whole process is actually quite simple. Making the bricks involves injecting very hot plastic into a mold and pressing it. Cool it a bit, open the mold, and out drops Lego bricks.
This machine presses down into each Star Wars set that passes through to make sure that the packs of Lego bricks inside isn't too high up. If it is too high, the box may not be able to be closed correctly.
An average passenger plane contains 100 to 200 miles of wiring for everything from electronically dimmable windows to in-flight entertainment systems, writes White. He and his colleagues at Swansea University’s Energy Safety Research Institute have conducted research into decreasing mass in wires by using carbon nanomaterials instead of copper alloys. “Carbon wires can be made from many sources – including recycled plastics,” writes White. “By turning these discarded plastics into useful, high-quality wires, we’re turning waste into wealth.”
Part of Lego's system is to be as efficient as possible. That means making bricks and other elements that can be used in different ways. These blue pieces can either be used as heads for mini-figures, or as decorations for other pieces.
This is from the second part of the process, when bricks and other elements--such as these soon-to-be mini-figures--are finished by adding any additional parts, like legs, arms, and heads, and having anything they need printed on, like a suit and tie.
To determine the environmental impact of the new wires, White and his colleagues compared the carbon dioxide molecules that are absorbed and emitted during plastic recycling with the count for copper wire fabrication. Although the carbon count was higher for the recycling process than for industrial copper wire production, they found that the overall environmental impact of the copper was nearly 10 times worse. Notably, it created toxic freshwater that caused marine damage and ozone depletion.
All Lego bricks are made from the same ABS plastic. It comes to Lego from suppliers and is held in giant silos. Generally it is clear or red, and the color for specific bricks is added at the molding machine. This is a bin full of ABS plastic, with some additional colors mixed in.
In addition to conventional waste plastic, his team also uses plastic scrap from 3D printing projects. “These types of plastic are growing in popularity, thanks to being strong, lightweight, easily molded, and very cheap,” writes White in The Conversation. “But when mixed with other plastics, they tend to cause trouble in conventional recycling processes, meaning that they often go straight to landfill. We discovered that by dissolving these plastics before recycling them, we were able to make more, higher quality new material. This is promising for large-scale production of electrical wiring — what’s needed in aviation.”
This is the reception at Lego's world headquarters. Note the way the ceiling and the chairs make up what appears to be two interlocking Lego bricks.
The overall environmental impact of copper wiring currently used in airplanes reportedly is nearly 10 times worse than wiring made from recycled plastic.
Now in the processing part of the production system, this machine is dropping torsos for mini-figures onto a belt where they will have additional elements like arms and legs and heads added to them.
Road Trip 2011: They may be the most popular toy on Earth, and watching them get produced in Lego's home town is a rare treat.
Editor in chief of PlasticsToday since 2015, Norbert Sparrow has more than 30 years of editorial experience in business-to-business media. He studied journalism at the Centre Universitaire d'Etudes du Journalisme in Strasbourg, France, where he earned a master's degree.
This display shows the weight of a small bag of Lego bricks known as a pre-pack. The weight must be between 94.9 grams and 95.7 grams. Coming in at 94.94 grams, this back passes muster. However, as the display shows, five bags came in too light, and one was too heavy. But 5,354 were in the target range.
This is one of 12 molding 'modules' located in Billund. Each module, or room, has as many as 64 working molding machines, divided into two aisles of 32 machines each.
BILLUND, Denmark--If you're a Lego fan like me, visiting this little town in western Denmark is a little like making a religious pilgrimage.
The researchers also determined that the use of recycled plastic wires would result in a smaller carbon footprint over a typical commercial aircraft’s lifespan. White concludes in the article that these wires would decrease the emissions of each plane by 21 kilotonnes, which is equal to a saving of 14,574 kilotonnes of carbon dioxide for an average fleet of 694 planes.
These tubes carry ABS plastic into the molding rooms. The sound coming from the pipes is very much like what millions of grains of rice would sound like going through pipes.
Currently, there are about 7,000 active molds being used at Lego. All told, it keeps about 9,000 around, with many stored on shelves like this one. The average mold is worth $72,000, with the most valuable coming in around $360,000.
That's obviously an overstatement, but this is the home of Lego, maybe the world's most famous toy, and as part of Road Trip 2011, I got a chance not only to visit the company's headquarters but also to see the production, processing, and packaging of the famous bricks.
This is a cross-section of a Lego brick mold. First, very hot plastic is injected into the mold on the right side. It then spreads through little channels and is then pushed into the press area of the mold through very small slits. When cold water is then flushed through the mold, it cools down the plastic, and the mold opens, allowing the bricks to snap off and drop down onto a belt below.
GETTING A QUOTE WITH LK-MOULD IS FREE AND SIMPLE.
FIND MORE OF OUR SERVICES:
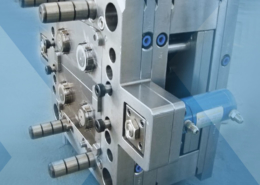
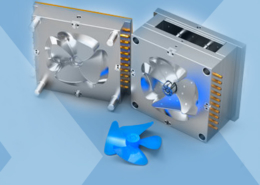
Plastic Molding

Rapid Prototyping
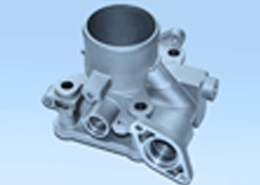
Pressure Die Casting
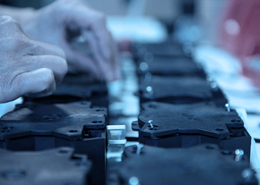
Parts Assembly
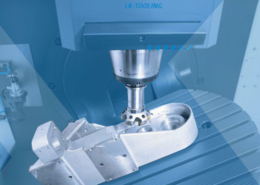