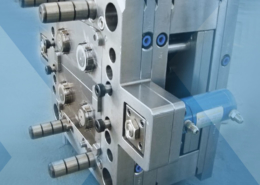
Wittmann’s FlexCell adds automation and efficiency to injection molding
Author:gly Date: 2024-09-30
When I worked for a Precious Plastic project in the UK we tested injection moulding (at 220C for polypropylene) into polycarbonate moulds inside a steel liner, that worked just fine. PEEK is significantly more temperature and pressure resistant that PC though! My co-founder designed a no-touch tool for COVID made from recycled LDPE injected into printed Nylon moulds. Those moulds lasted hundreds of injections at around 170C. I don't think they ever failed. Check the team out at Relic Plastic.
The team has already tested some of their molds at an injection-mold factory near Linz. “The factory employees were surprised at how easy it was to extract the finished objects, as well as how durable the 3D-printed molds were. Even after creating a hundred objects, the molds were still working,” says Auzinger. The team already has further improvements in mind. One idea is the inclusion of connectors that snap together to ease the final assembly of the object.
In the case study it is clear from the photos that the bottle's surface telegraphs the 3D printing texture. Ok for protos, but in production? Also, blow molding is a low pressure operation- I doubt these inserts could withstand injection molding temps and pressures. Still, very cool.
Most of the plastic objects we see are created using injection molding, but designing such molds is a difficult task, usually requiring experts. Now, computer scientists from the Institute of Science and Technology Austria (IST Austria), the University of Tokyo, and CONICET have created an interactive design tool that allows non-experts to create molds for an object of their choice. The software will be presented at this year’s prestigious SIGGRAPH conference, one of IST Austria’s five successful submissions.
The decompositions suggested by the design tool are often surprising: “The computer is able to find solutions that are very unintuitive,” says Bernd Bickel, professor at IST Austria. “The two halves of the rabbit, for instance, have a curving, complicated connection–it would have been extremely difficult for a human to come up with that.” Industry designers, as well as previous design programs, generally rely on straight cuts through the object. In practice, this often leads to a larger number of pieces, as well as “unnatural” divisions. “The software tool could also be extremely useful in industry–it would fit seamlessly into the production process,” adds Bickel.
To solve this, a research team led by Max Rodriguez, PepsiCo Senior Manager of Global Packaging R&D, turned to 3D printer manufacturer Nexa3D. The company used their NXE 400 Printer, an ultrafast machine "capable of printing at injection molding repeatability and tolerances, making it the fastest and most accurate production 3D printer in its category," the company says. It also costs just $60,000.
Hi Greg,The 3DP texture (stair stepping effect) can be significantly reduced through an automated post processing operation, which polishes the 3DP parts to a smooth finish. Visual comparison of bottles blown with this post process and polished metal tooling shows comparable bottle clarity and significant improvement on the stair stepping appearance. The post process takes 2-3 hours and it is fully automated. We are in the process of making production quality molds, which can potentially increase the output of the 3DP molds to up to 100,000 bottles, through mechanical electroplating. This will also help in improving the surface quality, while still keeping the cost of the tooling relatively low.Rain’s write up is the best one I’ve seen on this technology. It is poignant, as it comes from an ID’s POV. IDs come from a Design Thinking approach. Engineers as myself approach it from a Systems Thinking POV. We intersect on the need at some point to prototype and test. I developed this solution with this need in mind. I am very glad to see that this solution is appreciated by the ID community.Rain, this technology along with others that my team and I are engaged in is geared towards our sustainable efforts ad well as innovation, so please don’t be torn by this solution.Thanks,Max R.
CoreCavity, a new interactive design tool, solves this problem, and allows users to quickly and easily design molds for creating hollow, free-form objects. Created by Kazutaka Nakashima, a PhD student from the University of Tokyo visiting IST Austria, Thomas Auzinger (IST Austria), Emmanuel Iarussi (CONICET, IST Austria), Ran Zhang (IST Austria), Takeo Igarashi (University of Tokyo), and Bernd Bickel (IST Austria), this software tool opens up opportunities for small businesses and enthusiasts. Given a 3D-scan of an object, the software analyzes the object, and creates a “thin shell”, essentially a hollow version of the object, where particularly small gaps are considered solid–another of the team’s innovations. The software then proposes a decomposition of the object into pieces; each piece will be created by one mold, then joined together at the end. Moreover, the program is able to suggest slight modifications to the original design, for instance to eliminate tiny hooks that might complicate unmolding. “Previous tools were unable to suggest such changes,” says Thomas Auzinger, a postdoc at IST Austria. The user can adjust the decomposition simply by clicking, and choose to accept or reject any proposed modifications. When the user is satisfied, the software automatically produces the mold templates, which can then be 3D-printed and used for molding.
That was in the '90s, and today you can have steel cut for a new bottle mold in about 4 weeks. However, Pepsi has figured out how to get that time down to just 48 hours, and with a cost savings of up to $10,000. It's staggering.
Molding is a popular method for the mass production of objects. Essentially, two (or more) mold pieces are fit together, leaving the shape of the desired object as a hole. During fabrication, a fluid is introduced into this cavity and is allowed to harden. Once the fluid has solidified, the pieces of the mold are removed, leaving behind the molded object. While the process is fairly simple, creating the mold to produce an object is extremely difficult, and a multitude of considerations go into its creation. How should the object be oriented and divided to ensure that the pieces of the mold can be removed? If the object should be hollow, how should it be decomposed into pieces? Figures with loops or holes add further complications, as do aesthetic considerations, such as avoiding a parting line through a face. In mass fabrication, the high costs of the initial mold design are offset by the low per-unit cost of production. For a small-scale designer, however, or a novice interested in experimenting with injection molds, hiring a professional mold designer is impractical, and creating the molds unaided infeasible. Similarly, 3D-printing the desired number of objects would be far too time- and resource-intensive.
During my days as a structural package designer, when designing a new bottle, the last step for our department was to produce the CAD drawing of a new design. Then it went over to Engineering, who would tweak our CAD to produce the tooling drawing. Then we were ready to "cut steel," i.e. have the molds made for the blow-molding machine. That last step took months, and cost five figures.
The way they do it is by not cutting steel at all. Instead they use a universal mold shell, then they 3D-print an insert that goes inside the mold.
As a former package designer, I'm torn on this. I think it would've been so cool to be able to produce new bottle runs and design changes for small batches—new bottles for the World Cup and other major events. And I'm super-impressed with the technologies harnessed here. But then I start thinking wait…don't we have a plastic bottle problem?
Copyright © 2024 WTWH Media LLC. All Rights Reserved. The material on this site may not be reproduced, distributed, transmitted, cached or otherwise used, except with the prior written permission of WTWH Media Privacy Policy | Advertising | About Us
People have messed around with this before, but the problem has been durability and cost. A 3D-printed ABS insert is nowhere near as strong as steel, and you can blow-mold maybe 100 bottles before the insert fails. Hardly worth your time and money, particularly since the PolyJet 3D printers required cost $250,000, the Digital ABS material you print with runs $422 per kilogram, and the prints can take three days.
The obvious route to make the inserts would be to cnc them out of aluminium. Their geometry let you do this as one-sided milling from pre-sized blocks.In 48 hours, with a decent cnc machine, you would get a much better surface than the prints can provide. If it is about prototyping, then standard abs will work, if it is about production run of 10000 bottles, the superior surface finish of cnc milled aluminium would be desireable. The 3d printing technology here is cool, but I dont really see a benefit to use it to make these inserts.
Browse the most current issue of R&D World and back issues in an easy to use high quality format. Clip, share and download with the leading R& magazine today.
For material, the team used a polymer called xPEEK147, made by Henkel Loctite. xPEEK147 is tough, thermally stable and has high dimensional stability, and rings in at just $308 per kilogram.
GETTING A QUOTE WITH LK-MOULD IS FREE AND SIMPLE.
FIND MORE OF OUR SERVICES:
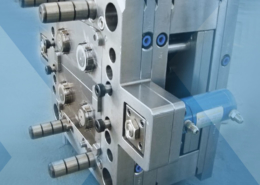
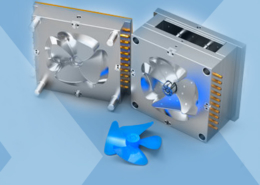
Plastic Molding

Rapid Prototyping
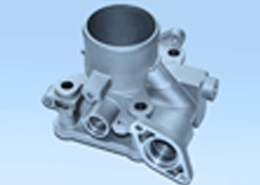
Pressure Die Casting
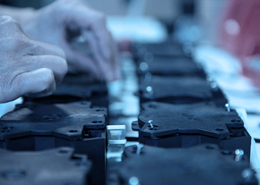
Parts Assembly
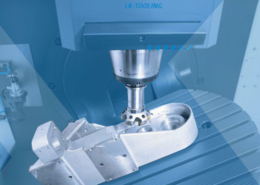