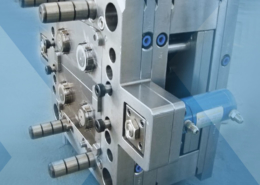
Unveiling the Potential of ABS Moulding
Author:gly Date: 2024-06-08
In the realm of plastic manufacturing, ABS (Acrylonitrile Butadiene Styrene) moulding stands as a cornerstone of innovation, offering unparalleled versatility and performance. This article embarks on a journey to explore the intricacies of ABS moulding, from its inception to its burgeoning role in shaping industries worldwide.
Introduction
ABS moulding represents a pinnacle of engineering ingenuity, leveraging the unique properties of Acrylonitrile Butadiene Styrene to create durable and aesthetically pleasing components. With its widespread adoption across industries ranging from automotive to consumer electronics, ABS moulding continues to redefine the possibilities of plastic manufacturing.
Historical Evolution
The roots of ABS moulding can be traced back to the mid-20th century, with the development of ABS resins as a viable alternative to traditional plastics. Initially utilized in automotive applications for its impact resistance and heat tolerance, ABS soon found its way into diverse industries due to its favorable balance of mechanical properties and processability.
Over the decades, advancements in polymer science and manufacturing technologies have further enhanced the performance and versatility of ABS moulding, cementing its status as a preferred choice for designers and engineers worldwide.
Material Properties and Advantages
ABS boasts a myriad of desirable properties that make it well-suited for a wide range of applications. Its excellent impact resistance, dimensional stability, and chemical resistance render it ideal for components subjected to harsh environments or mechanical stress.
Moreover, ABS exhibits superb surface finish, allowing for intricate detailing and decorative applications without sacrificing structural integrity. Its ability to be easily machined, painted, or plated further enhances its appeal for manufacturers seeking versatility and customization options.
Applications Across Industries
The versatility of ABS moulding transcends industry boundaries, finding applications in automotive, electronics, appliances, and beyond. In the automotive sector, ABS components adorn interiors, exteriors, and under-the-hood assemblies, offering lightweight solutions with superior impact resistance.
In consumer electronics, ABS housings and enclosures provide robust protection for delicate electronic components while maintaining an aesthetic appeal. Additionally, ABS's chemical resistance makes it a popular choice for medical devices, household appliances, and consumer goods where durability and safety are paramount.
Manufacturing Processes and Techniques
ABS moulding encompasses a variety of manufacturing processes, including injection molding, thermoforming, and extrusion. Among these, injection molding reigns supreme for its efficiency, precision, and ability to produce complex geometries with minimal waste.
Advanced techniques such as gas-assisted injection molding and co-injection molding further enhance the capabilities of ABS moulding, enabling the production of hollow or multi-material parts with enhanced strength and functionality.
Sustainability and Future Directions
As sustainability emerges as a critical imperative in manufacturing, ABS moulding is poised to embrace eco-friendly practices and materials. The development of bio-based ABS resins and recycling initiatives underscores the industry's commitment to reducing environmental impact while maintaining performance and quality standards.
Looking ahead, the future of ABS moulding holds promise for further innovation and integration with emerging technologies such as additive manufacturing and digital design. By leveraging these advancements, manufacturers can unlock new frontiers in design complexity, production efficiency, and sustainability.
Conclusion
In conclusion, ABS moulding epitomizes the synergy between innovation, versatility, and performance in the realm of plastic manufacturing. Its ability to combine aesthetic appeal with functional excellence has positioned it as a cornerstone of modern industry, driving progress and shaping the products of tomorrow.
As industries navigate the complexities of a rapidly evolving marketplace, the adoption of ABS moulding offers a pathway towards differentiation, efficiency, and sustainability. By harnessing the potential of ABS and embracing a culture of continuous improvement, manufacturers can embark on a journey towards a future characterized by ingenuity, resilience, and enduring value.
GETTING A QUOTE WITH LK-MOULD IS FREE AND SIMPLE.
FIND MORE OF OUR SERVICES:
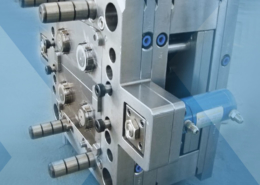
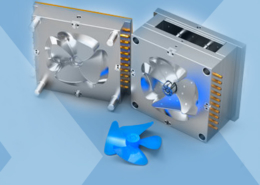
Plastic Molding

Rapid Prototyping
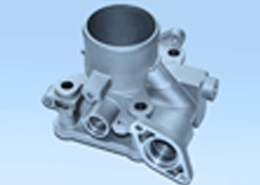
Pressure Die Casting
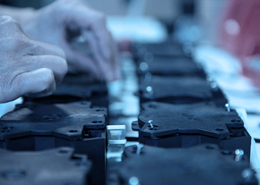
Parts Assembly
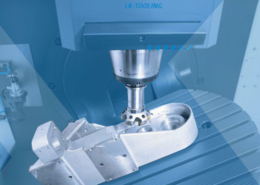