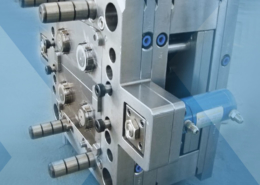
WITTMANN to present energy-efficient injection moulding machinery at FIP
Author:gly Date: 2024-09-30
Fusible-core injection molding technology has been employed to mold a fuel housing for an aircraft using PEEK (polyetheretherketone) resin supplied by Victrex (West Conshohocken, PA). The solution reportedly delivers a 30% cost saving and up to 50% weight reduction versus existing metal designs.Processor Egmond Plastic was able to consolidate the number of parts using a carbon fiber reinforced grade of Victrex PEEK polymer. A separate bearing, for example, was eliminated since it is now integrated into the overall design of the housing.Fuel housing molded for CF-PEEK compound using fusible core process.Fuel housings for aerospace applications have very complex inner geometries which are not moldable using conventional injection molding technology. Egmond Plastic's fusible-core technology enables moldings of complex hollow housings, manifolds, and pipes. Richard Brandwijk, Managing Director at Egmond Plastic, explains: "Our technology, in combination with carbon fiber reinforced Victrex PEEK polymer, delivers numerous benefits. These include cost reduction, enhanced manufacturing speed, and weight reduction leading to improved fuel efficiency and reduced CO2 emissions. Along with part consolidation, this exceptional technology and material combination enables the design of very complex parts, beyond the capabilities of standard injection molding and metal processes."Utilizing a near net-shape manufacturing process for the fusible core allows for an 80% time saving versus machined parts. Further, secondary treatments for corrosion protection, such as anodizing, can be eliminated. Lead times can be reduced by 50%. These factors combine to deliver part cost savings of more than 30% versus metal equivalents."The global aerospace industry stands to gain enormously by persistently replacing metals in key applications, in which Egmond has demonstrated tremendous leadership," said Uwe Marburger, Aerospace Business Development Manager at Victrex. "Clearly, our PEEK knowledge and material solutions help enable the use of a technology that addresses some of the toughest challenges in complex aerospace part design and productions."Previously, the end-user had generally specified aluminum for the production of fuel containing parts, but a carbon fiber reinforced PEEK polymer demonstrated superior fatigue performance when compared to aluminum. It does this while meeting all the engineering requirements for this application, including stiffness, effective flame, smoke and toxicity (FST) performance, and resistance to aggressive chemicals, including notably, for this aerospace application, resistance to jet fuel and Skydrol hydraulic fluid. Parts can range in size all the way up to 30 cm x 30 cm x 40 cm (11.8 in x 11.8 in x 15.8 in), and typically the process is used for production runs of up to 2,000 parts.Egmond's unique fusible-core technology has already established a proven track record using Victrex PEEK in a fuel pump for the Eurofighter Typhoon, a jet fighter in use in several European countries. This pump has been in successful operational use for more than 20 years.
“From the selection of 64 roll-to-roll printed modules, 32 of them were injected, and the other 32 modules were kept as references,” the researchers explained. “On average, the IM-OPV modules retained 98.1 of the original performance. Only 2 samples failed, and 28 samples preserved over 90% of the original performance, which sets the yield of the IM process close to 90%.”
The scientists inserted the modules horizontally into an injection mold of polyether copolymer-based thermoplastic polyurethane. This material was chosen due to its low process temperature, broad substrate compatibility, and flexibility. The injection was done using a 120 mm × 120 mm × 2 mm cavity insert, at a 90 mm −1s speed.
“This work represents the first demonstration of in-mold plastic solar cells and opens new possibilities for organic photovoltaics to enable specific applications that require simultaneous high optoelectronic and structural performances,” the researchers said. “We believe that future focus on injection plastic materials could further extend the benefits of in-mold photovoltaics in regards to structural and device stability, or even providing additional optical functionalities.”
Your personal data will only be disclosed or otherwise transmitted to third parties for the purposes of spam filtering or if this is necessary for technical maintenance of the website. Any other transfer to third parties will not take place unless this is justified on the basis of applicable data protection regulations or if pv magazine is legally obliged to do so.
The cookie settings on this website are set to "allow cookies" to give you the best browsing experience possible. If you continue to use this website without changing your cookie settings or you click "Accept" below then you are consenting to this.
“OPV product development demands photovoltaic materials with high morphological stability under thermal stress, such as the P3HT:O-IDTBR blend,” the academics emphasize. “In that respect, higher performing materials with such stability are urgently needed.”
You may revoke this consent at any time with effect for the future, in which case your personal data will be deleted immediately. Otherwise, your data will be deleted if pv magazine has processed your request or the purpose of data storage is fulfilled.
IM is a manufacturing technique for producing parts by injecting molten material into a mold and has the ability, according to the research group, to enable the development of in-mold plastic solar cells with improved performance and stability.
This content is protected by copyright and may not be reused. If you want to cooperate with us and would like to reuse some of our content, please contact: editors@pv-magazine.com.
As for mechanical and operational stability, the scientists found an average of more than 35% increase in the maximum stress point in the IM-OPV samples. The first fracture on the control devices occurred at 10–30% of strain, whereas this value jumped up to 70–150% on the IM-OPV modules. In addition, a power conversion efficiency retention of more than 90% was found after 50,000 cycles in the molded modules.
Fusible-core injection molding technology has been employed to mold a fuel housing for an aircraft using PEEK (polyetheretherketone) resin supplied by Victrex (West Conshohocken, PA). The solution reportedly delivers a 30% cost saving and up to 50% weight reduction versus existing metal designs.Processor Egmond Plastic was able to consolidate the number of parts using a carbon fiber reinforced grade of Victrex PEEK polymer. A separate bearing, for example, was eliminated since it is now integrated into the overall design of the housing.
“Due to their very thin layout, flexible solar cells can be sensitive to mechanical abrasiveness and, therefore, might require additional protection and integration strategies,” the research group explained. “Embedding a printed solar module into a plastic part simplifies integration challenges, while providing additional mechanical protection, shape adaptability, and streamlined contacts for connections.”
The researchers first created modules in roll-to-roll printing, using a photoactive blend known as P3HT:O-IDTBR. This blend was chosen due to its morphological and thermal stability, which are relevant to the later injection molding process.
A French-Spanish research team developed organic photovoltaic modules embedded into plastic parts through high throughput injection molding. The researchers injected thermoplastic polyurethane in the modules and found it enhances their mechanical stability while keeping a high flexibility.
Their findings were introduced in the paper “Injection Molding Plastic Solar Cells,” published in Advanced Science. The researchers come from the Eurecat Technology Centre of Catalonia, the University of Pardubice and the Centre for Organic Chemistry in the Czech Republic, as well as from French nano-metal producer GenesInk and Spanish injection molding provider Aitiip.
European researchers claim to have successfully demonstrated the embedment of organic PV (OPV) modules into structural plastic parts via large-scale industrial injection molding (IM).
GETTING A QUOTE WITH LK-MOULD IS FREE AND SIMPLE.
FIND MORE OF OUR SERVICES:
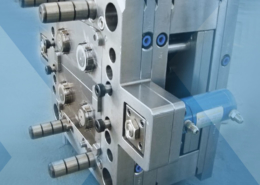
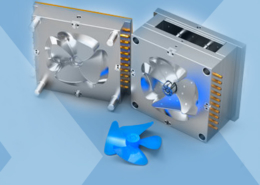
Plastic Molding

Rapid Prototyping
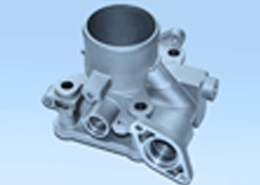
Pressure Die Casting
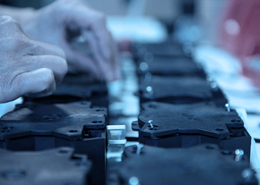
Parts Assembly
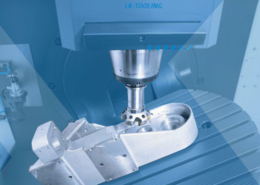