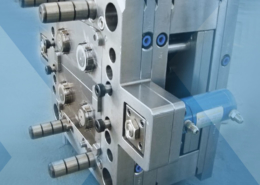
WITTMANN develops custom robot targeting stack mould applications - medical plas
Author:gly Date: 2024-09-30
“We produce under cleanroom conditions in the process. Thus, when the mould is open, no grain of dust can get between the coating and the substrate surface. We thus achieve very low reject rates,” Luckner said.
Using ColorForm tech means Techniplas doesn’t need to transport and paint components, or invest in a painting plant. The finished components are also ready for installation when they’re discharged from the automated production cell, saving on buffer storage and drying.
“Our ColorForm system is used to produce parts using the injection compression moulding process, which are given a high-quality, transparent PUR surface for a special depth effect. Another line for the project is currently being commissioned,” said Luckner.
The new Arburg press has faster robot-to-machine integration and helps to improve cycle times, according to Natech. Indeed, the company said the new machine improved cycle time by four seconds compared with the press it replaced.
ColorForm is KraussMaffei’s combination of injection moulding technology and surface finishing with polyurethane in a single step. The technology is designed to make large-scale production of high-quality components more economical and sustainable.
(Left to right) - Peter Giessmann (KraussMaffei), Eric Jan Frijters (Techniplas), Philipp Strasser (KraussMaffei), Michael Fuchs (KraussMaffei), Rene Rudolf (Techniplas), Sarah Seidel (Techniplas)
The new machines are a 470E 112-ton Arburg with integrated robot, Nissei FNX280 with YCII-250 servo-driven take-out Yushin robot, and Nissei FNX360 with a YCII-400 servo-driven take-out Yushin robot. Just four days after installation, Natech was able to begin production, the company said.
The MXW 1000 was not just retrofitted for ColorForm technology. Its control system was also completely upgraded to KraussMaffei’s MC6 control system, and a new ORCA cooling system was installed. "The system performs a contact-free temperature measurement, which minimises maintenance. The technology allows us to control the twenty cooling circuits of the MXW precisely and thus makes a critical contribution to the high, uniform quality of the components," explained Luckner.
The three older machines that are being replaced will be utilized at Natech’s mold-making facility for mold sampling and production. Natech has a total of 19 injection molding presses between its three facilities, two of which are in Ronkonkoma. The third plant, in Clark, NJ, houses mold-making operations.
“Because of the machine’s new technology, we can develop more stable processes. This ensures the processes will yield quality parts for clients,” commented Domingo Hernandez, Plant Manager.
"There, all necessary equipment is available on-site, and commissioning at the TechCenter was also completed on schedule – both for the injection moulding machine and for the PUR technology, that is, for the RimStar Flex with two MK 5-2K CCM mixing heads for simultaneous production of two components. This cannot be taken for granted under the current basic conditions determined by the pandemic," says Luckner.
The ColorForm process effectively works by combining injection moulding and polyurethane processing. The multi-component injection moulding procedure is the foundation of this process. After injection moulding of the thermoplastic mould base body, the body is flow-coated with polyurethane (PUR) or polyurea (PUA) as the surface material in a second cycle.
Techniplas has used the ColorForm process for several years – although the manufacturer refers to it as “ColorFuse” technology. There are four ColorForm systems in Treuen and one in Rüti, Switzerland. An in-house technical center in Treuen also uses two further systems.
“Our customers, major OEMs from the automotive industry, place the highest demands on quality. There must be no defects larger than 0.2mm on the entire transparent component. With the MXW 1000 in combination with the RimStar Flex for PUR metering, we fully meet these requirements,” added Toni Luckner, process developer at Techniplas in Treuen.
Natech offers design, engineering, injection molding, assembly, filling and sealing, and packaging services. FDA registered, Natech is certified to ISO 9001 and ISO 13485 and has an ISO Class 8 cleanroom on site.
The RimStar Flex ColorForm reaction process machine, which was designed specifically for this process, and the mixing head, feed the surface material (PUR/PUA) directly into the cavity. “RimStar systems take up very little space and meter even small amounts precisely and at a high cycle frequency,” said Philipp Strasser, global application owner, RPM and automotive at KraussMaffei.
A new system has recently been put into operation, for which Techniplas used an existing MXW 1000 injection moulding machine from KraussMaffei as the basis. Techniplas had the MXW retrofitted at its manufacturer's main factory in Munich's Allach neighborhood.
The Nissei presses run bigger and smaller molds than the machines they replaced. With multiple machines running bigger molds, production schedules are more flexible and clients don’t have to wait because a machine isn’t available to run their product.
"ColorForm technology offers great potential for a lower CO₂ footprint in the production of components with a noble, multifunctional surface," said Michael Fuchs, global application owner surface and lightweight at KraussMaffei. By consolidating the process down into one step, the user saves time and resource on intermediate storage, painting, and reworking of components. By using a transparent polyurethane surface treatment, Techniplas can also achieve ‘depth effects’ on the final component. The company uses the MXW 1000 ColorForm system at its Treuen, Saxony site.
A contract development and manufacturing firm offering end-to-end services for clients in the medical device and diagnostics markets, Natech Plastics announced that it has installed three new injection molding machines this quarter at its Ronkonkoma, NY, headquarters. The machines will service customers in the medical, pharmaceutical, and consumer goods industries.
The new presses give engineers and operators more opportunities to efficiently run data-driven scientific molding for a reliable and repeatable process with little to no variation, said Natech. Scientific molding optimizes the tool design and validates the part’s end use, it added.
GETTING A QUOTE WITH LK-MOULD IS FREE AND SIMPLE.
FIND MORE OF OUR SERVICES:
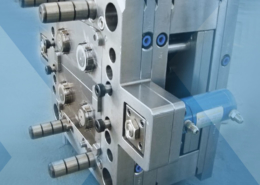
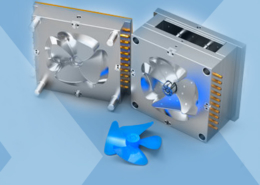
Plastic Molding

Rapid Prototyping
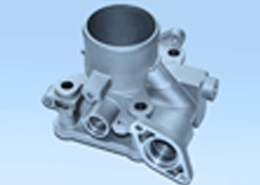
Pressure Die Casting
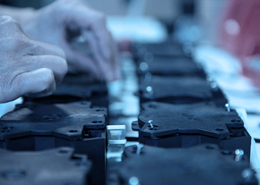
Parts Assembly
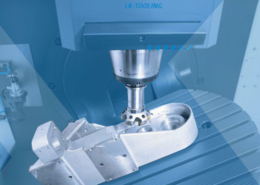