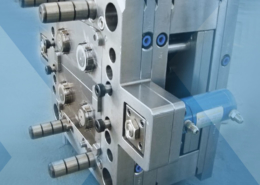
Why plastic waste is an ideal building material - soft plastic mould
Author:gly Date: 2024-09-30
where ηrel [–] is relative viscosity, t [s] is the flow time of the polymer solution and t0 [s] is the flow time of the pure solvent.
Bánhegyi, Gy. Editorial corner – a personal view. Reconsidering plastics recycling and bio-plastics. Express Polym. Lett. 15, 685–686 (2021).
Extensive MIM, CIM industry and sinter-based AM industry news, plus the following exclusive deep-dive articles and reports:
Due to their excellent properties, polyamides are widely used engineering polymers. They are semi-crystalline polymers12,13,14. In recent years, the demand for polyamides has reached 1 million tons, most of which has been used in the transport, electronics and construction industries2. The anionic ring-opening polymerization process allows the low viscosity monomer of polyamide 6, ε-caprolactam, to surround the fibers completely, without pores, and the final product to be formed as the last step in the polymerization process15,16,17,18,19,20. Moreover, in addition to the material and energy recovery typical with thermoplastic polymers, polyamide 6 also offers the possibility of chemical recycling, as it can be depolymerized to the starting monomer in a cost-effective way21.
A Zwick Z020 (Zwick, Ulm, Germany) tensile testing machine was used to test the standard Type 5A specimens (ISO 527–2) under uniaxial tensile loading at constant tensile speed. The machine recorded the tensile force as a function of length change. The dumbbell-shaped specimens were 75 mm long, 12.5 mm wide and 2 mm thick. Grip length was 50 mm and test speed was 5 mm/min. Tensile strength and tensile modulus were calculated.
MIM2023’s opening keynote was delivered by Diran Apelian, Distinguished Professor, Materials Science and Engineering, at the University of California, Irvine, USA. This opening keynote presentation was on an extremely thought-provoking topic entitled Megatrends in Near-Net-Shape Manufacturing. After his initial introduction, Apelian showed a slide stating ‘CHANGE: It is the Universal Constant’ which set the tone for the remainder of his presentation. The presentation was divided into four broad segments: digitisation/industry 4.2TM/data science; sustainability, including resource recovery and decarbonistion; process innovations; and talentism (not capitalism nor socialism).
This had the fastest debinding time with an average of 0.7 h/cm3. Heptane also had the fastest overall processing time for debinding and heated drying with a requirement of 0.8 h/cm3. Flammable liquid requires special equipment; not a significant toxicity hazard.
Another interesting set of solutions that were covered include hybrid processes that combine additive and subtractive technologies to produce the final product. Some of the companies that are using these hybrid technologies include 3DEO, Mantle and Tritone (MoldJet). The presentation also discussed some of the other sinter-based AM processes, such as screen printing, Cold Metal Fusion and Nanoparticle Jetting.
The aim of this research is to investigate the mechanical recyclability and reprocessability of polyamide 6 products produced by anionic ring-opening polymerization with the use of T-RTM, an innovative technology. As there have been no publications in this area so far, our further aim is to show how the properties of the raw material change during recycling. For this purpose, the products obtained by ring-opening polymerization were mechanically recycled, then injection-molded and their properties were compared to the original product and to a commercial injection molding polyamide 6.
Zhou, Q., Fang, J., Gao, H. & Loo, L. S. Substrate effects on the surface properties of nylon 6. Appl. Surf. Sci. 282, 115–120 (2013).
Another interesting presentation from Uniformity Labs (UL), California, USA, was given by Dr Joseph Schramm, entitled ‘Performance of Highly Uniform High Density Multimodal Stainless Steel Powders in Metal Injection Molding.’ This presentation highlighted the benefits of designed multimodal powders to attain higher solids loading in MIM feedstocks. The presentation highlighted the ability of UL powders to attain high relative densities, approaching that of the densest crystalline particle packings, while retaining their ability to flow without phase separation. Fig. 12 shows a schematic of the densest natural crystalline packing of binary spheres and the UL maximally random jammed packing, both using a powder size ratio of 5:1. It can be seen that the UL powder can attain a packing density that is almost the same as the densest natural crystalline packing.
The residual monomer content in each sample was determined by TGA based on the work of Samet Kurt et al.27. Minor changes in the initial stages of the TGA and DTG curves indicate the removal of absorbed water (up to about 80–100 °C) and residual monomer and oligomer (between about 100 °C and 240 °C) from the sample (Fig. 3). The significant weight loss of PA6 samples produced by T-RTM starts at ~ 260 °C, so we used the percentage weight at this temperature to determine conversion by compensating for the initial moisture content of the sample (~ 1.4%). The results indicate that the conversion efficiency of the sample was 96.8%. The reprocessed T-RTM test specimens had a similar degree of polymerization compared to the starting material (96.6%). The sample injection molded from polycondensation granules also showed similar conversion (97.7%, see Fig. 3), but the decomposition temperature of these samples starts around 350 °C. The sample produced by T-RTM had the lowest decomposition temperature. These different decomposition temperatures may be due to the different material structures of the samples and the absence of a stabilizer. The samples can be processed at a maximum melt temperature of 250 °C, above which significant degradation occurs.
Murray, J. J. et al. Effect of glass fibre sizing on the interfacial properties of composites produced using in-situ polymerised Polyamide-6 transfer moulding. Compos. B. Eng. 235, 109743 (2022).
For sustainable development, the key areas of focus need to be production waste, post-consumer waste and materials for clean energy. The area of processing innovations is also intimately tied with sustainability. Recycling and recovery of materials (especially rare earth materials used in batteries) is critical in process innovations.
HP’s Metal Jet has undergone significant refinement in the years since it was first unveiled in 2018. Now, by incorporating nearly the whole Bind...»
Several processing techniques based on the MEX process, developed by different companies, were discussed and some applications were highlighted. Various commercial solutions based on the principle of MEX, including those using feedstock in the form of a filament or rod (Desktop Metal, MarkForged) and pellet-based extrusion processes (Pollen and AIM 3D), as well as extrusion of gel-based and paste-based feedstocks, were touched upon.
Another major process that was covered was Vat Photopolymerisation (VPP), which is based on photopolymerisation of a metal or ceramic containing slurry using a digital light engine. Some of the processes that have evolved based on this technology by different companies include Lithoz, Incus, Holo, Trio Labs and Tethon 3D.
A major part of the presentation was based on Binder Jetting (BJT) technology, which has gained the best traction among all the sinter-based AM processes thanks to its promise of high-volume production capability at a low cost. The presentation pointed out that some of the technologies are complementary to MIM, supporting MIM companies in terms of quick tooling and even rapid prototyping of actual metal parts. However, it was pointed out that some processes, such as BJT, can also pose competition to MIM due to their ability to fabricate parts with high productivity and without the requirement of any tooling.
Maris, J. et al. Mechanical recycling: compatibilization of mixed thermoplastic wastes. Polym. Degrad. Stabil. 147, 245–266 (2017).
The relative viscosity of the polyamide 6 samples was determined with a PSL Rheotek RPV-1 automatic solution viscometer according to ASTM D4603. The solvent used was a mixture of phenol/1,1,2,2-tetrachloroethane (60%/40%) (Sigma-Aldrich, USA). The measurements were carried out at 30 °C on 0.5 dl/g polymer solutions. The relative viscosity of the samples was determined from the flow time of the solutions and the solvent through the capillary, with Eq. (2):
Halliwell, S. End of life options for composite waste. https://compositesuk.co.uk/system/files/documents/endoflifeoptions.pdf (2006).
Sheet-like specimens (510 mm × 290 mm × 2 mm) were produced with T-RTM and in-situ polymerization with equipment from KraussMaffei. The equipment consists of dosing units (DU) and a hydraulic press (Fig. 1). The DU is responsible for melting the raw material, storing it in an airtight container, transporting it to the mold carrier press and injecting it into the mold. The unit consists of two DUs, one (DU1) for the base and the other (DU2) for surface coating. The function of the press is to provide clamping force for the mold. The first step in the production process was to measure out the appropriate amount of raw materials—CL-92.5 m/m% (caprolactam), C10-4.5 m/m% (catalyst), C20P-3 m/m% (activator)—and feed them into the DU.
In the production of PA6 by anionic in-situ polymerization, attention should be paid to residual monomer content, as non-polymerizable monomers and oligomers can modify the properties of the final product as plasticizers. The maximum non-reacting monomer content in the product is 4–5%, above which it should be removed.
Recycling reduced molecular weight, which was thus close to the molecular weight of the IM grade material. This chain scission was also confirmed by ATR-FTIR. Tensile and flexural tests show that in-situ polymerization can produce products with higher strength than injection molding. Although the properties of recycled PA6 deteriorated compared to the starting material, its properties were almost the same as in the case of injection-molded PA6. The results of the Charpy impact test showed that the recycled samples exhibited higher impact strength due to the larger amorphous domains compared to the PA6 samples produced by T-RTM. Viscosity measurements demonstrated that processing at temperatures above 260 °C lead to the degradation of the material, which also cause a significant decrease in molecular weight and hence in viscosity. It was found that polyamide 6 products prepared from ε-caprolactam by anionic ring-opening polymerization with T-RTM technology can be easily recycled and reprocessed by injection molding without a processing aid. If melt temperature during reprocessing is kept below 250 °C, which is the beginning of the decomposition of anionically polymerized PA6, the properties of the resulting product are in good agreement with those of a conventional commercially available injection molding–grade PA6 material.
Fig. 8 shows the packing of different parts in a Desktop Metal BJT process. The picture on the top shows a single-layer stacking of three different parts (housing, valve body and brackets) in a build box, whereas the picture on the bottom shows the optimised packing of the same three parts for the complete build box.
However, the primary reason for incorporating AM was the tight timeline for project completion. PTI needed a rapid prototype technology that could manufacture production-representative parts that could then dovetail into large-volume MIM production. Binder Jetting of 316L was used to solve the issues. Various iterations of the button body and the button cap were fabricated to test: a) various retaining tab cross sections; b) sintered dimensional control; c) machined surface finish; and d) final assembly design. For example, Fig. 10 shows the results of button body tab flexing, which was possible due to the thin tab made from 316L. All the tests, including the flexing, were completed without hard tooling and the finished prototype parts were successfully delivered to the customer before any tool steel for a mould was cut.
By submitting a comment you agree to abide by our Terms and Community Guidelines. If you find something abusive or that does not comply with our terms or guidelines please flag it as inappropriate.
The crystalline fraction of the 5 mg samples was determined with a DSC Q2000 (TA Instruments, New Castle, USA) machine in a heat-cool-heat cycle, in nitrogen. The measuring range was 25 °C to 250 °C and the heating/cooling rate was 10 °C/min. The crystalline fraction was calculated with Eq. (1):
Bhadra, J., Al-Thani, N., Abdulkareem, A. Recycling of polymer-polymer composites in Micro and Nano Fibrillar Composites (MFCs and NFCs) from Polymer Blends (ed. Mishra, R.K., Thomas, S., Kalarikkal N.) 263–277 (Woodhead Publishing, Sawston, 2017).
Sample preparation (a) with the T-RTM unit (1, mold preparation for start; 2, mold closing and vacuuming; 3, mold filling; 4, polymerization; 5, mold opening and part removal) and the main parts of the T-RTM machine (b).
Qi, S. et al. New insight into the thermal-oxidative stability of polyamide 6: a comparison investigation on the effect of hindered amine and CuI/KI. Polym. Eng. Sci. 61, 348–361 (2021).
Humphry, J. et al. Isothermal differential scanning calorimetry analysis of the anionic polymerisation of polyamide-6: Separation by dual asymmetric gaussians. Mater. Today Commun. 25, 101473 (2020).
The semi-crystalline structure of PA6 consists of ordered crystalline molecular chains and disordered amorphous domains. While the former improves strength and stiffness, the latter provides toughness and elongation.
For the reference sample, Durethan B30S (Lanxess) polyamide 6 granules were used. This material, which is commonly used in injection molding, allows the production of products with good mechanical properties, such as high impact resistance. It has a melting point of 222 °C and a density of 1.14 g/cm3 at room temperature.
Although MIM2023 was organised as a hybrid event, including both online and in-person presentations, the in-person presentations significantly outnumbered the virtual ones. This was an extremely good sign for the industry, which is rebounding back to its pre-COVID days with attendance at the conference climbing to 138 and participation from 11 countries. International participation was still slightly weaker than expected, but is anticipated to bounce back next year.
The temperature- and shear-dependent viscosity of the polyamide samples were described by the Cross-WLF model between 240 and 280 °C (Fig. 12). The parameters of the model are presented in Table 1. The correlation (R2) between the model and the measured results was above 0.995 in all cases. The results show that the temperature dependence of the viscosity of the samples prepared by anionic polymerization and T-RTM is more significant than that of polycondensation PA. While the IM grade material becomes more stable with increasing melt temperature, the viscosity of T-RTM and T-RTM(re) materials shows a significant decrease. One of the reasons is that the difference between the decomposition temperatures of the samples is close to 100 °C. The TGA results showed that the T-RTM samples started to decompose at around 260 °C, with significant degradation occurring at higher temperatures. However, as the temperature increased, the viscosity of both the reprocessed and the T-RTM materials decreased more and more significantly. This may be because at higher temperatures; the chains started to break and degrade. At 280 °C, the viscosity of the polymerized materials is almost the same, about 20–30 Pas at low shear rates. Consequently, the maximum reprocessing temperature for these T-RTM samples is about 250 °C. Therefore, during the recycling of products produced by T-RTM, a stabilizer has to be added to ensure proper processability.
Open Access This article is licensed under a Creative Commons Attribution 4.0 International License, which permits use, sharing, adaptation, distribution and reproduction in any medium or format, as long as you give appropriate credit to the original author(s) and the source, provide a link to the Creative Commons licence, and indicate if changes were made. The images or other third party material in this article are included in the article's Creative Commons licence, unless indicated otherwise in a credit line to the material. If material is not included in the article's Creative Commons licence and your intended use is not permitted by statutory regulation or exceeds the permitted use, you will need to obtain permission directly from the copyright holder. To view a copy of this licence, visit http://creativecommons.org/licenses/by/4.0/.
Figure 11 shows the viscosity curves of specimens produced with different technologies at 240, 260 and 280 °C. At a test temperature of 240 °C, the viscosity curves of the samples produced with different technologies are different from each other. The samples produced by T-RTM had higher viscosity (about 400 Pas at a shear rate of 100 1/s), which indicate higher molecular weight—as the molecular weight of a given material increases, its viscosity also increases. As shown previously, the properties of the recycled T-RTM samples and the injection molding grade material are very similar, and their viscosity curves show good agreement as a function of shear rate at 240 °C (from 200 to 50 Pas between 100 and 10,000 1/s shear rate). The lower viscosity of the reused material compared to the original T-RTM product was due to the mechanical and thermal effects (grinding and melting) during reprocessing, which resulted in a reduction in molecular weight. The difference between the viscosity of the two materials at a shear rate of 100 1/s is 230 Pas. As shear rate increases, the viscosity of all three materials decreases, and the difference between them also tends to decrease.
One of the main ways to recycle polymers is mechanical recycling, whereby the thermoplastic polymer composite is shredded, melted and then injection molded or extruded. The process involves the use of a low-speed cutting or crushing machine to shred larger pieces into smaller pieces and is mostly used by manufacturers of glass fiber–reinforced composites. The resulting materials can be mixed with the original material and re-molded or extruded. The disadvantage of mechanical recycling is that the material degrades during melting and reprocessing, which reduces macromolecular length and molecular weight and this has a major impact on mechanical properties and processability. However, incorrect processing parameters (e.g. too high a temperature) cause more damage than repeated processing at the right temperature. In many cases, recycling is possible without a significant change in properties. Furthermore, due to advanced quality control, thermoplastic polymers can be injection molded or extruded ten times without noticeable molecular degradation if heat stabilizers are added21,22,23,24.
Su, K.-H., Lin, J.-H. & Lin, C.-C. Influence of reprocessing on the mechanical properties and structure of polyamide 6. J. Mater. Process. Tech. 192–193, 532–538 (2007).
Domingo, G. D. & Souza, A. M. C. Effect of reprocessing on the structure and properties. J. Appl. Polym. Sci. 139, 51869 (2022).
This is a story from what once looked like the edge of the metal Additive Manufacturing universe. A decade ago, the idea of a Metal Injection Moldi...»
Krawczak, P. Editorial corner – a personal view. Automotive plastics: what future is there for polymers in tomorrow’s electric and autonomous vehicles. Express Polym. Lett. 15, 288 (2021).
This work was done in collaboration with US MIM producer OptiMIM, based in Wilsonville, Oregon. UL 17-4 PH powders with a high tapped powder density (minimum –5.60 g/cm3; maximum –5.92 g/cm3) were converted into feedstock with loadings ranging from 71 to 77 vol.% (less than 4% binder by mass). The feedstocks were moulded into tensile bars and it was determined that all the loadings were mouldable without requiring any equipment modification.
Since the very first PM Titanium conference in Brisbane, Australia, in 2011, the PMTi series has been the essential meeting point where technical a...»
The short ‘commercial’ presentations by various companies were also informative and of great value to people who may not have been familiar with the different products they offered. Even though MPIF organised this event in a hybrid format, there were only a handful of virtual presentations but attendance was reasonable for these digital talks.
The structure and structural changes of polyamide 6 samples were analyzed by ATR-FTIR. Since the –CH2– content is relatively unchanged in polyamide 6, the spectra were normalized to these peaks30.
The design challenge faced by PTI was to consolidate the button assembly design and eliminate the polymer overmould. The designing and engineering of flexing retaining tabs and assembly threads in an all-MIM 316L button body design was challenging. Over and above that, the retaining tabs needed to be thin enough (~0.030”) to flex them by hand yet retain their shape without cracking.
Li, J., Liang, M., Gua, S. & Lin, Y. Studies on chain scission and extension of polyamide 6 melt in the presence of ultrasonic irradiation. Polym. Degrad. Stabil. 86, 323–329 (2004).
Ozmen, S. C., Ozkoc, G. & Serhatli, E. Thermal, mechanical and physical properties of chain extended recycled polyamide 6 via reactive extrusion: effect of chain extender types. Polym. Degrad. Stabil. 162, 76–84 (2019).
Cross-WLF model of the viscosity of the polyamide samples between 240 and 280 °C (a, T-RTM; b, T-RTM(re), c, IM grade samples).
It was stated that, “AI and robotics will transform tasks rather than make humans obsolete. The impact of AI and robotics depends on how we adopt them.” Machine Learning (ML), which is a branch of AI where one constructs computer algorithms to mimic tasks commonly performed by humans, is expected to play a critical role in the industrial transformation. This statement has reportedly been supported by Microsoft’s Bill Gates who has stated that “a breakthrough in ML would be worth ten Microsofts.” Deep learning, which is a subset of ML, is creating large disruptions and has the potential to keep driving the AI boom. A schematic of the timeline of AI, ML and deep learning is shown in Fig. 4.
With up to 8–9 million tons of waste generated by the automotive industry each year, these regulations will bring about a major change in this area, supporting new technological developments and eco-innovation. A regulation4 was also adopted requiring, among other things, that by 1 January 2015 at the latest, cars should be 95% recyclable by weight. In addition, stricter CO2 emission standards for vehicles have been introduced, requiring new passenger cars to have CO2 emissions below 95 g/km from 2020 and 75 g/km by 2030. These regulations were also intended to encourage the car industry to innovate technologically, promoting eco-innovation5,6. For these reasons, one of the main directions of this research is thermoplastic polymer composite technologies, which can be alternatives to metal components, due to their superior mechanical properties, lightweight and recyclability. Previously, the problem with continuous fiber–reinforced thermoplastic composite manufacturing technologies was that the high viscosity of the thermoplastic matrix material did not allow the sufficient impregnation of the reinforcing fibers, limiting the spread of the technology. The solution could be Thermoplastic Resin Transfer Molding (T-RTM), which is ideally suited for anionic ring-opening polymerization7,8,9. T-RTM has advantages over thermoset composite manufacturing technologies, such as recyclability, lower environmental impact, and the ability to create different layering patterns of reinforcing fabrics within a product for different loads. Furthermore, the short cycle time makes the technology suitable for mass production10. Thanks to the low temperatures and pressures used, large, thick and complex geometries can also be produced10,11.
First, the main bonds characterizing polyamides were determined. The peak at 3295 cm−1 is attributed to the hydrogen-bonded N–H stretching. Bands around 2924 and 2854 cm−1 are assigned to methylene (C–H) stretching or tension vibration. The peaks around 1634 and 1537 cm−1 correspond to amide I (C = O) and amide II (N–H and C–N combination), respectively31,32,33. As Fig. 6 shows, no new absorption peak appears on the spectra of the reprocessed T-RTM sample. Also, no significant changes can be observed in the main peaks of the spectra. Similarly Mondragon et al.31, a change was also observed at 1740 cm-1. This peak was five times higher after recycling. It can be associated with the stretching vibration of the carboxyl group (-COOH), probably formed due to the oxidation of peptide links of PAs during recycling. This may also prove the shortening of the chains assumed from the results of the solution viscosity measurement.
Worldwide Plastics Production Falls In 2020 Due To COVID-19: Report. https://www.republicworld.com/world-news/global-event-news/worldwide-plastics-production-falls-in-2020-due-to-covid-19-report.html (2021).
O.V.S.: Conceptualization, Investigation, Data curation, Writing—original draft preparation; A.S.: Conceptualization, Methodology, Investigation, Writing—review and editing, Supervision.
Prof Apelian acknowledged that talent is a scarce commodity and he quoted Klaus Schwab from the World Economic Forum, who stated that, “in the 4th Industrial Revolution, it is all about talentism; not capitalism nor socialism.” Development and utilisation of the talent pool will be the key to the success of the 4th Industrial Revolution. An illustration of the dream of Industry 4.2TM and the future of work and the worker is shown in Fig. 6.
The degradation, decomposition and monomer concentration of the samples were investigated by thermogravimetric analysis (TGA Q500, TA Instruments, New Castle, USA). The samples were heated to 400 °C in a nitrogen atmosphere at 10 °C/min. The B30S material was heated to 600 °C.
This had similar results to Tergo MCF. Non-flammable liquid can be used in open-top or vacuum equipment. The toxicity concerns with this include carcinogenicity, as a result the solvent is facing regulatory action and phase-out.
The free-to-access PIM International magazine archive offers unparalleled insight into the world of MIM, CIM and sinter-based AM from a commercial and technological perspective through:
It is of interest to note that the MIM conferences organised by MPIF have, over the past five years, seen a steady increase in the number of AM presentations. This trend has been driven primarily by the similarities in some of the sinter-based AM processes and Metal Injection Moulding as well as the ongoing discussions about whether these AM technologies are complementary or a threat to MIM. Recent years have also witnessed the proliferation of numerous sinter-based AM technologies.
The current scenario, where AM can be complementary to MIM, was very well covered in the presentation by Gaetano Mariella of PTI Tech Inc., New Jersey, USA. In his presentation entitled ‘Utilizing Metal Injection Molding and AM Binder Jetting in the Production of a 316L Industrial Part’, Gaetano detailed a case study that was initiated due to COVID-19. PTI was approached by a major elevator company to solve a problem with their current elevator button panels.
The bending tests were also carried out on a Zwick Z020 (Zwick, Ulm, Germany) universal tensile testing machine. Specimen size was 40 mm × 25 mm × 2 mm, support spacing was 32 mm and the loading rate was 5 mm/min. The test was performed up to the conventional deflection, which is equal to 1.5 times the specimen thickness (i.e. 3 mm in this case). From the evaluation limit, bending stress and the flexural modulus of elasticity were determined.
Contrastingly, a MIM-type of feedstock, where metal powder is mixed with organic binders to form a feedstock, is extruded through a nozzle to build a geometric shape that is subsequently subjected to debinding and a consolidation step to result in the final part. This multi-step process has similarities with the MIM process, except for the geometric shaping, which is accomplished by a build process, or printing, instead of moulding.
As can be imagined, these elevator button panels are high-touch areas by the public. Due to the COVID-19 pandemic, these button panels were subject to the widespread and increased use of chemical disinfectants to limit the spread of the virus. However, this increased use of various solvents and disinfectants was rapidly degrading the current legacy multi-part elevator button assemblies. Fig. 9 shows a picture of the current legacy overmoulded button assembly.
This offered the fastest overall processing time for debinding and ambient drying with a requirement of 3.3 h/cm3. This azeotrope also had the second fastest overall processing time for debinding with heated drying displaying an average rate of 1.4 h/cm3. Non-flammable liquid can be used in open-top or vacuum equipment; not a significant toxicity hazard.
Reach a truly international audience that includes component manufacturers, end-users, industry suppliers, analysts, researchers and more.
Department of Polymer Engineering, Faculty of Mechanical Engineering, Budapest University of Technology and Economics, Műegyetem rkp. 3, Budapest, 1111, Hungary
Oliveux, G., Dandy, L. O. & Leeke, G. A. Current status of recycling of fiber reinforced polymers: review of technologies, reuse and resulting properties. Prog. Mater. Sci. 72, 61–99 (2015).
For the preparation of the test samples, an ε-caprolactam/C10/C20P system was used, which can be applied for the production of PA6 by in-situ polymerization with short cycle times and anionic ring-opening below the melting point (130–170 °C). The starting material was AP- Nylon ε-caprolactam (L. Brüggemann GmbH & Co. KG, Germany), which has a melting point of 69 °C, a density of 0.6–0.7 g/cm3 and a viscosity in the liquid state similar to that of water (3–5 mPas). Due to its high moisture absorption capacity, it was stored under vacuum. Sodium caprolactam, with a density of 0.45–0.55 g/cm3 and a melting point of 62.2 °C, was used as initiator (Brüggolen C10, L. Brüggemann GmbH & Co. KG, Germany). Like ε-caprolactam, C10 is sensitive to moisture and easily deactivated in the presence of water, therefore it was stored under vacuum as well. Hexamethylene-1,6-dicarbamoyl caprolactam (Brüggolen C20P, L. Brüggemann GmbH & Co. KG, Germany) was used as activator. It has a density of 0.85 g/cm3 and a melting point of 70 °C.
During the DSC analysis, in the second heating cycle (Fig. 4), there is a smaller peak next to the main endothermic peak, due to reprocessing. This may be because two stable crystal structures (α and γ) can be distinguished in polyamide 6. The α structure has higher thermal and mechanical stability due to its more regular crystalline structure, because the chains are in a stretched state. It has a melting temperature of 222 °C, while the γ structure has a melting temperature of 215 °C. In the latter, the chains are twisted, which also changes the angle of the bonds between them, resulting in less stability29. Furthermore, as the number of recycling cycles increases, the average molecular weight decreases, but this secondary endothermic peak increases steadily; this way they show proportionality with each other.
Kim, H., Oh, K. & Seo, Y. Rheological and mechanical properties of a novel polyamide 6 synthesized by anionic polymerization of ε-caprolactam in a twin-screw extruder. Polymer 177, 196–201 (2019).
The DU has two tanks for melting CL + C10 and CL + C20P separately. The raw materials were melted in the DUs at 110 °C in an inert, nitrogen atmosphere, followed by vacuum deaeration and the provision of a nitrogen atmosphere. During operation, the melt circulates continuously in a closed system so that contact with air is avoided. Once the raw material is melted, it is conveyed through heated tubes to the forming die mounted on the press, where the material is fed in by means of a mixing head. The heated mixing head (110 °C) ensures that both components are fed separately into the mold (150 °C), and only come into contact with each other immediately after the mixing head, to avoid a premature start of the polymerization process. Proper mixing of the components from the two separate tanks is ensured by the right volumetric flow rate and the design of the mixing head. The hermetically sealed mold is under vacuum, which ensures the best possible filling. After the filling of the mold and the polymerization time (180 s), the finished specimen can be removed. This specimen (T-RTM) was used directly for testing.
Samples were conditioned in an exicator at 23 °C for 48 h at 50% relative humidity before testing. The samples for each test were prepared from 2 mm thick 80 × 80 mm injection molded and 510 × 290 × 2 mm T-RTM plates.
where ΔHm is the enthalpy of melting, ΔHcc is the enthalpy of cold crystallization, ΔHf is the melting enthalpy of a theoretically fully crystalline polymer (188 J/g for PA625) and φ is the mass fraction of the filler.
Grigore, M. E. Methods of recycling, properties and applications of recycled thermoplastic polymers. Recycling 2, 24 (2017).
Szakács, J. & Mészáros, L. Effect of fiber contents on fatigue behavior of injection molded polyamide 6 matrix composites. Period. Polytech. Mech. 61, 74–78 (2016).
Samples produced by T-RTM had higher strength than those re-injection-molded or injection-molded from polycondensation PA. While the former had a tensile strength of 69 MPa and a tensile modulus of elasticity of 3.3 GPa, the specimen injection molded from granules had a tensile strength of approximately 66 MPa and a tensile modulus of elasticity of 2.8 GPa (Fig. 7). The reason for this is the higher crystalline fraction of the specimens produced by T-RTM. The strength and stiffness of the re-molded PA6 specimens were only slightly inferior to those of the injection-molded specimens from polycondensation PA.
Gomez, C. et al. Resin transfer molding of high-fluidity polyamide-6 with modified glass-fabric preforms. Compos. Part A – Appl. S. 147, 106448 (2021).
The authors declare that they have no known competing financial interests or personal relationships that could have appeared to influence the work reported in this paper.
Semperger, O.V., Suplicz, A. The degradation during recycling of polyamide 6 produced by anionic ring-opening polymerization of ε-caprolactam. Sci Rep 13, 17130 (2023). https://doi.org/10.1038/s41598-023-44314-0
Achtnicht, M., von Graevenitz, K., Koesler, S., Löschel, A., Schoeman, B., Reanos, M. A. T. Including road transport in the EU-ETS - An alternative for the future?. https://www.econstor.eu/bitstream/10419/111452/1/826581412.pdf (2015).
The Charpy tests were performed on a Resil Impactor Junior (Ceast, Torino, Italy) tester. For the instrumented impact test, specimens of 80 mm × 10 mm × 2 mm were cut from each sample and a 2 mm deep notch was made on them. The test was performed with a 2 J hammer with a support distance of 62 mm. From the instrumented test results, impact strength and the ductility index (3) were determined.
Fig. 11 shows the AM button body and the button cap in both the as-sintered and machined conditions. The rapid prototyping using the BJT process was the key to the success of the project. Once the design and properties were achieved (that satisfied the customer), attention was focused on MIM for high-volume production of the actual components.
Laboratory experiments were carried out and five solvents were chosen. The solvent properties are outlined in Table 1 (Note: Tergo MCF is azeotrope 92 and Novec 73DE is azeotrope 85). A comparison of the amount of binder removed by different solvents is shown in Fig. 15. The time that it takes for the solvents to be removed at ambient temperature is also an important factor (Fig. 16). The overall debinding process efficiencies for different solvents are shown in Table 2. The presentation concluded with the following summary:
Murray, J. J., Robert, C., Gleich, K., McCarthy, E. D. & Bradaigh, C. M. Ó. Manufacturing of unidirectional stitched glass fabric reinforced polyamide 6 by thermoplastic resin transfer moulding. Mater. Design. 189, 108512 (2020).
Open access funding provided by Budapest University of Technology and Economics. This work was supported by the National Research, Development and Innovation Office, Hungary (OTKA FK138501). The research reported in this paper is part of project no. BME-NVA-02, implemented with the support provided by the Ministry of Innovation and Technology of Hungary from the National Research, Development and Innovation Fund, financed under the TKP2021 funding scheme. András Suplicz would like to thank the Hungarian Academy of Sciences for the János Bolyai Research Scholarship. The research was supported by the ÚNKP-20-5 New National Excellence Program of the Ministry for Innovation and Technology from the source of the National Research, Development and Innovation Fund. Prepared with the professional support of the Doctoral Student Scholarship Program of the co-operative doctoral program of the Ministry for Innovation and Technology from the source of the National Research, Development and Innovation Fund. Project no. RRF-2.3.1-21-2022-00009, titled National Laboratory for Renewable Energy has been implemented with the support provided by the Recovery and Resilience Facility of the European Union within the framework of Programme Széchenyi Plan Plus. Project no. TKP2021-NKTA-07 has been implemented with the support provided by the Ministry of Culture and Innovation from the National Research, Development and Innovation Fund, financed under the TKP2021 funding scheme.
Regulation (EC) No 443/2009 of the European Parliament and of the Council Official Journal of the European Union (2009).
Legault M. Infusible thermoplastics via in-situ polymerization. CompositesWorld.https://www.compositesworld.com/articles/infusible-thermoplastics-via-in-situ-polymerization (2014).
The presentation discussed the company’s lab scale machine that is currently on the market (Hammer Lab35) and mentioned their next production machine, known as Hammer Pro, which will have more than six times the build area compared to the lab version. This will enable the production of larger parts as well as parts in higher production volumes at a lower cost. Some of the details of the lab-size machine are shown in Table 3.
The change in the length of the molecular chains can be well characterized by the change in the viscosity of the polymer solutions. Figure 5 shows the relative viscosity of the PA6 samples. The specimen produced by T-RTM has the highest relative viscosity (2.3). In comparison, the recycled and IM grade samples have a relative viscosity more than 25% lower, 1.73 and 1.7, respectively. This indicates that mechanical recycling has significantly reduced the molecular weight of anionically polymerized PA6. In addition to molecular weight, crystalline fraction is also significantly reduced, which can lead to a deterioration of mechanical properties. Furthermore, the molecular weight and the crystalline fraction of the recycled and IM grade material are almost the same (Fig. 5), thus similar mechanical properties can be expected.
The drive for sustainability is directly connected to the growth in the world’s population, which jumped from 1.6 billion in 1900 to 6.1 billion in 2000 and 7.8 billion in 2020. This increase in population, along with the demands placed on the world’s material resources, has created the urgent need to focus on sustainability. The areas of materials and advanced manufacturing will have a direct impact on energy and climate change, food and water, housing (shelter), mobility (transportation, cyber mobility) and health.
Kovács, Zs., Pomázi, Á. & Toldy, A. The flame retardancy of polyamide 6-prepared by in situ polymerisation of ε-caprolactam-For T-RTM applications. Polym. Degrad. Stabil. 195, 10979 (2022).
The Cross-WLF model was used to model the effect of temperature and shear rate on viscosity. The model can be described as follow (4):
Due to the continuous development of the plastics industry, the annual production of plastics has been increasing for more than 50 years. In 2020, the volume of plastic products produced increased to 368 million tons, an increase of about 2.4% compared to 20181. At the same time, the amount of plastic waste has been steadily increasing as well, reaching 300 million tons per year in recent years, and its disposal is a global problem. To tackle this problem, countries have developed different strategies. The waste management policy of the European Union is one of the most advanced, with the reduction, reuse and recycling of waste in landfills as its main objective2,3.
Furthermore, the shift of the crystallization peak due to the reprocessing, i.e. the increase of the crystallization temperature from 163.13 to 185.48 °C28, can be seen in the cooling curves of the T-RTM product. In addition, there is a decrease in the width of the exothermic peak, all of which indicate an increase in the crystallization rate. Since the starting material was not changed, only reprocessed, it is likely that this is related to the reduction of the length of the molecular chains, their degradation. Samples prepared by T-RTM have longer molecular chains, which are therefore less mobile, so crystallization starts later and occurs more slowly than in the case of injection-molded samples, which are likely to have shorter chains.
The crystalline fraction of the samples was determined from the curves obtained by DSC (Fig. 4). Based on the first heating curves, the T-RTM samples had a higher crystalline fraction (43.4%) than the re-injection-molded and injection-molded samples. Based on the first heating curves, the injection-molded (IM grade) samples had a crystalline fraction of 32.39%, while the re-injected material (T-RTM (re)) had a crystalline fraction of 30.85%. The decrease in the crystalline fraction due to reprocessing may be caused by the different nature of the production technologies. The first heating curves show that the original T-RTM samples have a narrower crystal melting range than the injection-molded samples, which may be due to the narrower, more uniform distribution of the crystal lamella size (Fig. 4).
As the plastics industry continues to grow, the amount of plastic waste is also increasing. The European Union is controlling plastic waste through various regulations, focusing primarily on recyclability. A good alternative to traditional thermoset composites is thermoplastic polyamide 6 composites produced by Thermoplastic Resin Transfer Molding (T-RTM). Polyamide 6 has high strength and is produced by in-situ anionic ring-opening polymerization in T-RTM. Products made with this technology can replace traditional thermoset composites in many areas, which greatly increases recyclability. In this paper, the recyclability of the high molecular weight polyamide 6 matrix material of T-RTM composites is investigated. Products were mechanically recycled and then processed by injection molding. Thermal, mechanical and rheological properties of the samples were compared with the properties of the original product, as well as a general injection molding–grade PA6. Results show that the parts prepared with this innovative technology can be mechanically recycled and reprocessed by injection molding without a processing aid. After reprocessing, a significant reduction in properties is observed due to degradation, but the properties of the resulting product are in good agreement with those of a conventional commercially available injection molding grade PA6 material.
The tensile curves (Fig. 8) show that IM grade and recycled samples exhibited significant neck formation during tensile testing and only broke after more than 50% elongation. The nature of the two curves is similar, with identical behavior. The IM grade material has 50.3% (± 3.8%) elongation at break, and the recycled sample has 85.5% (± 9.19%). In comparison, the maximum elongation of the samples prepared by anionic polymerization is much lower: 10.8% (± 1.1%). This different character is also due to the different crystal fraction of polyamides.
where EFmax [kJ] is the energy absorbed up to the maximum force and Etotal [kJ] is the energy absorbed up to the first zero transition.
The initial time and cost savings were significant when using the Binder Jetting process for prototyping. In addition, the process dovetailed very well with the MIM production process. The result was a cost-effective all-stainless steel industrial button assembly impervious to solvent and disinfectant chemicals while maintaining the same design as the mating electrical panel assembly.
Fig. 13 shows a schematic comparing a non-uniform particle distribution in moulded parts (left) to a 75% dense loading where the particles are spread uniformly and maintain the same high density (right). Earlier investigations by UL showed the benefits of its multimodal, highly packed powder in Binder Jetting and whether these benefits could be translated to MIM.
where η [Pas] is the viscosity of the polymer melt, η0 [Pas] is the zero shear-rate viscosity, γ [1/s] is the shear rate, τ* [Pa] is the critical shear stress at the transition from the Newtonian plateau level to shear thinning, and n is the power law index. The temperature-dependent zero shear viscosity is given by the WLF equation (5):
One sinter-based AM process that has the potential to compete with MIM is Incus’s process based on Vat Photopolymerisation. A presentation of this process was given by Dr György Harakály of Incus, Austria, entitled Lithography-based Metal Manufacturing. His paper outlined the advantages of this process including the ability to produce complex green parts in a small- to medium-size range (1–200 g component mass), the highest resolution and surface aesthetics of metal AM processes, a wide range of materials with the possibility of processing non-flowable and non-weldable materials, a simple production process with easy preparation of printing jobs and quick exchange of materials, and safe working environment with no metal dust or high-power laser.
The Charpy impact strength of the T-RTM samples was 4.5 kJ/m2. The approximately 13% less crystalline fraction in the re-injection-molded sample resulted in an increase of about 6 kJ/m2 in impact work (Fig. 10). The ductility index (DI) of the samples was also calculated, which showed values close to 1 for all of them. DI values close to 1 indicate brittle fracture, while lower DI indicates tougher fracture. The injection-molded specimens had a higher average DI, i.e. they were more brittle than the specimens produced by T-RTM. However, we cannot show a significant difference between the measurement results due to the large standard deviations. In the case of the T-RTM samples, the brittle behavior is due to the notch and the high crystalline fraction. In the case of injection-molded samples, this can also be caused by the notch and shorter molecular chains.
The differences between single-step and multi-step processes, as outlined by ISO/ASTM 52900:2015, were discussed. It was pointed out that almost all the sinter-based AM processes were multi-step processes, where the parts are fabricated in two or more distinctly different operations. The first operation typically produces the basic geometry of the part and the subsequent step(s) results in the consolidation of the part to achieve the final properties (dependent on the desired material) of the part.
Don't miss any new issue of PIM International, and stay up to date with the latest industry news. Sign up to our fortnightly newsletter.
I would like to acknowledge the support received from MPIF staff (James Adams and Bill Edwards) and the authors for their help with the figures used in this report.
The objective of MIM2023 was to survey the advancements in the area of injection moulding of metals, ceramics and carbides and support the efforts of technology transfer across different areas of Metal Injection Moulding (MIM). It also looked to focus on new developments that contribute to the growth of MIM, and keep the community appraised and updated about other technologies, primarily sinter-based Additive Manufacturing, that could be complementary, but also pose a threat to MIM in some areas.
Thank you for visiting nature.com. You are using a browser version with limited support for CSS. To obtain the best experience, we recommend you use a more up to date browser (or turn off compatibility mode in Internet Explorer). In the meantime, to ensure continued support, we are displaying the site without styles and JavaScript.
Tohidi, S. D. et al. Development of polyamide 6 based single polymer composites reinforced by novel stitched plain fabrics. Mater. Today Commun. 24, 101068 (2020).
Kurt, S. et al. Determination of the residual monomer concentration of ε-caprolactam in polyamide-6 using thermogravimetric analysis coupled with Fourier transform infrared spectroscopy gas analysis. J. Appl. Polym. Sci. 138, 50730 (2021).
In addition to the main technical sessions, the wider event also featured the long-established one-day PIM tutorial, presented for many years by Prof Randall German and now by Matt Bulger, former president of the MPIF’s Metal Injection Molding Association (MIMA). MIMA standards committee, board of directors and members meetings also took place, as well as short commercial process and product innovation presentations and a tabletop exhibition.
Hopefully, future conferences will be able to do away with the hybrid format. Overall, it was heartening to see the enthusiasm and the excitement among the attendees as, hopefully, the world is looking at COVID-19 in the rear-view mirror.
Multi-cavity hard MIM tooling was designed and manufactured by PTI using novel gating techniques, as well as novel techniques that were developed to release and eject the complex component geometry. Custom sintering setters were developed to ensure the perpendicularity of extended thin retaining tabs while maintaining the flatness and concentricity of the button body.
Stiffness and strength were also greatly improved by the crystalline parts. The re-injection-molded specimens had the lowest crystalline fraction (30.85%) and ultimate flexural stress (35.8 MPa), while for the T-RTM specimens these values were 43% and 65 MPa, respectively. The in-situ polymerization products have higher stiffness than the injection-molded products. In addition to the highest flexural stress, the T-RTM samples also had the highest modulus of 1.88 GPa. Nevertheless, the T-RTM re-injection-molded specimen and polycondensation PA have similarly good mechanical properties (Fig. 9).
Die casting is a widely used process for the production of Metal Injection Molding-sized parts, but its application is typically for components wit...»
This presentation highlighted a case where a sinter-based AM process was successfully used as the perfect rapid prototyping method to establish the form, fit and function of the intended part, which was subsequently transitioned to high volume, near-net-shaped MIM components that were finally machined to yield the desired parts.
Song, L. et al. Dissolution window in in situ polymerization preparation of polyamide single-polymer composites. Polym. Eng. Sci. 61, 1662–1672 (2021).
where T [K] is the temperature, T* [K] is the glass transition temperature (320 K 25), and D1 [Pas], A1 [−] and A2 [K] are data-fitted coefficients 26.
An interesting area of process innovation is gigacasting in the automotive industry, leading to a simplification of vehicle structures. This innovation has the potential to reduce the number of automotive parts needed for a car body structure from 171 to two, and require 1600 fewer welds. To keep up with the demand for large casting sizes, the die cast machine size range has increased dramatically over time. Prof Apelian pointed out that LK, the global leader in hot chamber and cold chamber die casting machines, has increased the locking force of its hot chamber die cast machine cells from 2000 to 12,000 tonnes since 1970 (Fig. 5).
Mondragon, G. et al. Thermomechanical recycling of polyamide 6 from fishing nets waste. J. Appl. Polym. Sci. 137, 48442 (2020).
Semperger, O. V. & Suplicz, A. The effect of the parameters of T-RTM on the properties of polyamide 6 prepared by in-situ polymerization. Materials 13, 4–15 (2020).
Tohidi, S. D. et al. Mechano-morphological studies of polyamide 6 based single polymer laminate composites prepared by different reactive processing techniques. Polym. Test. 79, 106017 (2019).
Discover suppliers of these and more in our advertisers’ index and buyer’s guide, available in the back of PIM International.
A topic that often does not get the coverage that it deserves is that of the solvents used in debinding. This topic was covered in detail by David A Ferguson of MicroCare, LLC. His presentation entitled ‘Solvent Debinding Series: Update: Comparing Overall Efficiency of Various Solvent Mixtures’ discussed the current trends in solvent use and showed lab experiments of different solvents. During the presentation, David pointed out the issues with some of the popular solvents, as outlined below:
This review covers only a small section of the many interesting presentations that added tremendous value to the conference. It was difficult to pick and choose the papers to include in this report and many presentations that could not be covered for lack of space were also extremely insightful. The tabletop exhibition was mostly packed and the exchange of ideas and networking was ongoing.
Another important area that is tied to process innovations is the issue of conformal cooling in casting dies and injection moulding machines. This requires improved thermal management that allows shorter cycle times, improved mechanical properties, complicated geometry (thick and thin sections), uniform die/tool temperature, and better temperature control. AM is playing a key role in this area by allowing for increased tool complexity with fewer components and reduced lead times. Improvements in the performance of the tools are also dictated by new materials that can provide high thermal conductivity, high-temperature resistance and, thereby, result in extended tooling life.
The goal was to investigate the mechanical recyclability of polyamide 6 produced by in-situ polymerization, by T-RTM. We compared the thermal, mechanical and rheological properties of the starting and recycled polyamide 6 and polycondensation polyamide 6 (injection molding grade). Determining the residual monomer content proved to be very important, as its increase negatively affects mechanical properties. The results indicate that industrial PA6 has higher conversion—they have a lower residual monomer content. However, in-situ polymerization samples also have an acceptable monomer content of 2–2.5%. An increase in the crystalline fraction can result in increased strength and modulus and decreased impact strength. The tests showed that in-situ polymerized PA6 samples had a crystalline fraction more than 10% higher than PA6 samples injection molded from granules or pellets. The solution viscosity measurements showed that the anionically polymerized samples had the highest molecular weight, which can also have a significant effect on mechanical properties.
The presentation touched on the nine technologies that are reshaping production (Fig. 3). According to Prof Apelian, Industry 4.0 was going to consist of automation, connection, cloud computing, IOT, big data and system integration. Automation and Artificial Intelligence (AI) are expected to play a key role in the transformation to Industry 4.0. To emphasise that point, the presentation provided an interesting statistic on the change in stock values of these companies, compared to the Dow Jones Industrial Average, between 2 January 2020 to 4 January 2021. The compiled data showed that the Dow Jones had increased by 5%, but the majority of companies involved in automation and AI (ten different companies) had increased from 20 to 68% over the same period.
The presentation covered the broad technologies of Material Extrusion (MEX)-based processes, where the material is selectively dispensed through a nozzle or orifice. The material being extruded can become the final part itself, as in the case of pure polymer extrusion or hot extruding a metallic wire or polymer loaded with metal powder to form the final part.
The as-sintered surface roughness of the process is around 2.17 µm Ra, which can be reduced to 0.067 µm with surface treatment. A schematic of the overall Incus lithography-based metal manufacturing process steps is shown in Fig. 17 and the detailed printing step is shown in Fig. 18. The process is capable of high-volume production and better surface finish compared to most AM processes.
Fig. 14 shows the variation in the sintered densities of MIM bars with different feedstock loadings. It is interesting to note that the moulded bars achieve a very high sintered density as feedstock loading approaches the tapped density of the powder. This property then translates into lower shrinkage of the MIM bars at higher loadings, which is possible using the UL powder. Typically, lower shrinkage leads to lower distortion. Thus, UL powders of high tap densities can be beneficial to the MIM industry.
A Ceast SR 50 capillary rheometer (Ceast, Turin, Italy) was used to measure the melt viscosity of the materials. 2 capillaries of different lengths (5 and 20 mm) and the same diameter (1 mm) were inserted into the apparatus. The materials were measured at 3 different temperatures (240 °C, 260 °C and 280 °C) and at 7 different shear rates (100–10 000 1/s). The corrections necessary for evaluation (Bagley and Rabinowitch corrections) were automatically performed by the software of the instrument using the values measured with the two capillaries.
From the unreinforced polyamide 6 specimens produced by T-RTM, shredded 5 mm polyamide 6 pellets were produced with an Sb Plastics Machinery GRS202 shredder. From both the T-RTM shredded pellets (T-RTM (re)) and the Durethan B30S polycondensation polyamide 6 pellets (IM grade), 80 × 80×2 mm sheets were produced by injection molding in a two-cavity cold-runner mold at a melt temperature of 250 °C (Fig. 2). The samples were injection molded with an Arburg 270S 400–170 machine. The injection molded specimens were subjected to the same tests as the original T-RTM specimens.
A Bruker Tensor II, Attenuated Total Reflectance Infrared Spectroscopy apparatus (Bruker Optics Inc., USA) was used to analyze the chemical structure of polyamide 6 samples. Spectra were taken between 4000 and 400 cm-1; 16 scans were performed.
It was felt that there was a need for a presentation discussing several relevant sinter-based AM technologies. This was covered in a presentation by Dr Animesh Bose (yours truly), formerly with Desktop Metal and now with Optimus Alloys, entitled “Review of Some Sinter-Based Metal AM Technologies.” The presentation illustrated the similarities and the differences between the majority of sinter-based AM processes and MIM, as shown in Fig. 7.
GETTING A QUOTE WITH LK-MOULD IS FREE AND SIMPLE.
FIND MORE OF OUR SERVICES:
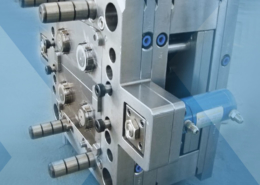
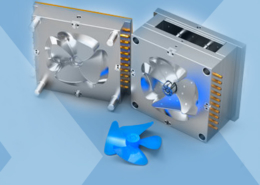
Plastic Molding

Rapid Prototyping
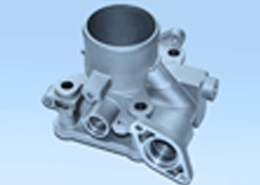
Pressure Die Casting
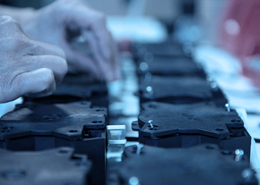
Parts Assembly
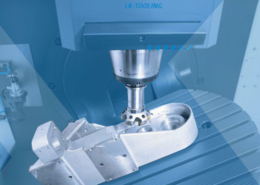