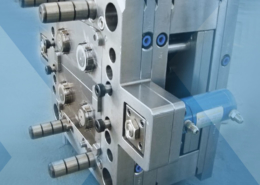
Why plastic waste is an ideal building material - one off plastic moulding
Author:gly Date: 2024-09-30
Lakeshore produces about four million caps annually and is adding equipment for cap lining. The company owns five injection molding machines (IMMs) from Absolute Haitian, ranging from 100 to 427 tons. Three of those IMMs are paired with top-entry robots from Absolute Robot. Lakeshore’s new manufacturing space can accommodate three more IMMs.
“The benefit to customers of our turnkey experience is risk mitigation,” Pontius said. “From CAD modeling to in-house fabrication and repair to prototyping and mass production, the development cycle is under one roof. If a mold has an issue, rather than having it taken out of the machine and shipped away for repair, we can diagnose the problem and repair it in a matter of hours, minimizing downtime and maximizing production schedules,” said Pontius.
Starting as a mold fabrication company in 2019, Lakeshore provides turnkey services from engineering through to assembly.
The proprietary technology developed by Polyplastics captures and evaluates the gases and identifies the mechanism by which pyrolysis gas forms during the injection molding process.
Lakeshore is helping many companies onshore molds or rebuild molds from a previous supplier that are difficult to remove. For these transitions, Lakeshore helps customers confirm mold and tooling compatibility with its facility, match material and color, review quality control requirements, and plan logistics.
Automation is critical to Lakeshore’s business. Removing high-end jewelry cases from a mold, for example, requires careful handling to maintain aesthetics, a task that is best performed by a robot. Molding polished parts of clear Tritan copolyester, which degrades quickly with any variation in cycle time, also requires automation. “The ARI top-entry robot is faster and more consistent at removing the part from the mold and prevents damage that could be introduced if a machine operator so much as bumps the mold when removing the part,” said Lakeshore CEO Kyle Pontius.
In a sign of robust injection molding demand, Utah’s Lakeshore Plastics expanded capacity of its Orem manufacturing facility by about 50% to 12,000 square feet.
Geoff Giordano is a tech journalist with more than 30 years’ experience in all facets of publishing. He has reported extensively on the gamut of plastics manufacturing technologies and issues, including 3D printing materials and methods; injection, blow, micro and rotomolding; additives, colorants and nanomodifiers; blown and cast films; packaging; thermoforming; tooling; ancillary equipment; and the circular economy. Contact him at [email protected].
The company’s proprietary technology captures and evaluates the gases formed during molding and identifies the mechanism by which pyrolysis gas forms during injection molding. It traps gases according to mold-based methods, and uses gas chromatography mass spectrometers (GC/MS) to qualitatively and quantitatively analyze their composition, identify the gases that are formed, and make fundamental improvements to the sources of their formation.
During the injection molding process, high temperatures and speeds along with the deterioration of plastic additives can release high volumes of decomposition gases. Mold deposits, gas burns, and short shots caused by pyrolysis gas can lead to quality problems. These may include undesirable effects on the dimensions and appearance of molded parts, resulting in high defect rates. Maintaining efficient production operations is important as manufacturers work to meet challenging applications such as automotive electrification and automation, said Polyplastics in its announcement.
Coming soon are specialized molds designed to produce custom plastic caps in various sizes and textures at a lower initial cost.
A new testing method that identifies gas formation during the injection molding process helps to reduce mold deposits, according to engineering thermoplastics supplier Polyplastics Co. Ltd. The Tokyo-based company’s Gas Investigation Method in Injection Molding (GIMIM) reportedly facilitates continuous molding and improves production efficiency.
For mold fabrication, the company added a CNC lathe and three electrical discharge machines (wire, sinker, and hole popper) to complement its CNC milling machine.
The system’s configuration is divided into the three stages of plasticization, metering, and injection, and each unit is fitted with traps to segregate the gases that form within each part of the process.
GIMIM makes it possible to measure high-molecular-weight substances that can cause mold deposits. Since this method directly analyzes gases that are formed inside the mold during filling, it yields results that are closest to real-world conditions, according to Polyplastics. In further research, Polyplastics plans to examine other problems caused by pyrolysis gas, such as short shots and gas burn defects as well as mold deposits.
“In the coming months, we're making available specialized molds to easily swap logos and textures on numerous cap sizes to produce a custom closure at a much lower initial cost,” Pontius said.
GETTING A QUOTE WITH LK-MOULD IS FREE AND SIMPLE.
FIND MORE OF OUR SERVICES:
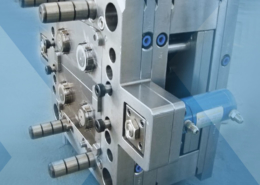
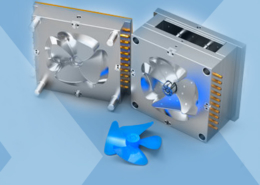
Plastic Molding

Rapid Prototyping
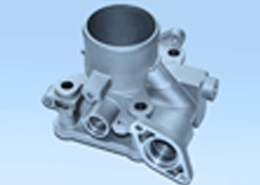
Pressure Die Casting
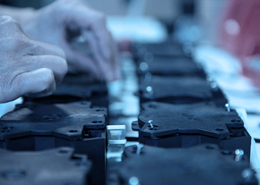
Parts Assembly
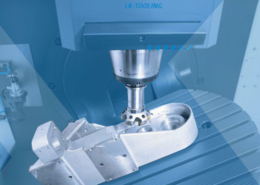