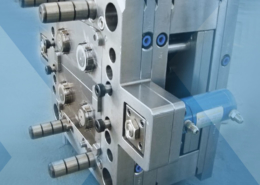
White & Case Advises Husky Injection Molding Systems on Successful
Author:gly Date: 2024-09-30
“The aim was to demonstrate to them the precision, creativeness, innovation and challenges that make up the product development process.
The 3D Design and Technology students at Stokesley School have been given a brief to design and make a set of working headphones that would appeal to a target market of eight to 12-year-olds.
Teacher Mike Stevens said: “This was a fantastic opportunity for the students to expand their knowledge by seeing first-hand how prototyping works in a real workplace environment.
“Giving students the opportunity to experience the world of work all adds to knowledge that will help them move on to next stage of their lives whether that’s higher education, training or employment.”
Icon Plastics manufactures and supplies complex plastic injection moulded parts and assemblies into the Automotive, Electronics and Defence industries.
“Therefore, when we heard that students from Stokesley School were learning about new product design as part of their course, we were only too happy to invite them in.
“As well as helping with their studies, we hope the visit may have encouraged some to consider a career in this business arena as it is important to inspire a future generation of workers.”
PMMA resin is acclaimed for its balance of properties that lens applications require, including UV resistance (non-yellowing), flexible colorability, chemical resistance, hardness, and scratch resistance. It is also recyclable via chemical depolymerization. PMMA is well positioned for emerging new vehicle designs, where industry has coined “light is the new chrome,” ensuring its role as a key to innovative lighting and more into the future.
The 2023 Automotive Innovation Awards recognized the material’s first use in the 1948 Cadillac Series 60, 61, and 62 models.
Precision plastic injection moulding firm Icon Plastics has opened its doors to a party of sixth formers to give them practical experience in prototyping components as part of their A-level studies.
They are being encouraged to make full use of a wide range of resources including 3D printing, laser machines, lamination, drape forming, vacuum forming and sublimation printing, in order to simulate a mass-produced product that has been injection moulded.
General Motors pioneered a revolution in automotive lighting by using PMMA on the 1948 Cadillac rear lamp lens, and other OEMs followed. From the perennial 1950’s "shark fins” to the modern “coast-to-coast” light bars, PMMA has played an integral role in the advancement of automotive lighting designs in both form and function. A variety of specialty PMMA grades designed for OEM-specific styles and applications are currently available, including non-transparent, high-gloss black versions (for paint replacement/exterior trim); various diffusive types (for LED edge/back lighting); and even infrared transparent variations designed for laser welding and radar/LiDAR covers.
• Pictured (above) is teacher Mike Stevens, left, and Icon Plastics operations director Phil Walker, centre, with students from Stokesley School.
As part of the task, they also have been advised to consider how all the parts are to be fabricated and assembled along with the internal speakers and cables. The end product will be tested and evaluated and its commercial viability identified.
Stephen has been with PlasticsToday and its preceding publications Modern Plastics and Injection Molding since 1992, throughout this time based in the Asia Pacific region, including stints in Japan, Australia, and his current location Singapore. His current beat focuses on automotive. Stephen is an avid folding bicycle rider, often taking his bike on overseas business trips, and is a proud dachshund owner.
The industry’s first acrylic rear lens, used on the 1948 General Motors Co. Cadillac Series 60, 61, and 62 models, has been named the 2023 Hall of Fame winner by the Automotive Division of the Society of Plastics Engineers (SPE). The acrylic, made possible with the invention of a polymer called polymethyl methacrylate (PMMA) by Dr. Otto Röhm in 1932, was a game changer, replacing ground glass and enabling a renaissance of new lighting designs for all OEMs.
If you have any questions or you’d like to get involved with our growing community of businesses doing great things in the Tees region, drop us a message in the form below and a member of our team will get back to you very soon.
To be considered for a Hall of Fame award, an automotive plastic or composite component must have been in continuous service in some form for at least 15 years and been broadly adopted in the automotive industry. This application certainly qualifies, as PMMA lenses are an industry standard known for glass-like optical properties at about half the weight of glass. PMMA offers numerous design and quality benefits, making it the premier material for lighting applications and more on all automotive vehicles and numerous other products.
Icon Plastics, which employs 43 people, has invested £1m in its premises at Durham Lane Industrial Estate, Stockton, since it moved there in 2014.
GETTING A QUOTE WITH LK-MOULD IS FREE AND SIMPLE.
FIND MORE OF OUR SERVICES:
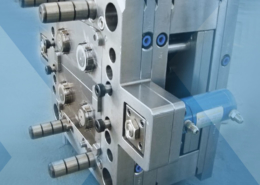
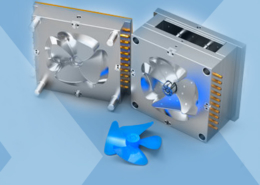
Plastic Molding

Rapid Prototyping
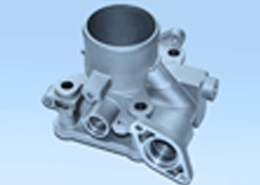
Pressure Die Casting
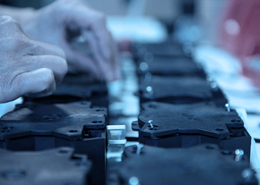
Parts Assembly
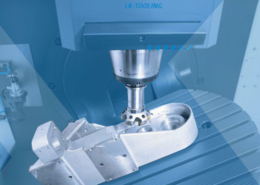