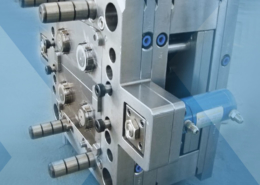
Where Dirty Dancing cast are now – from botched plastic surgery to lonely
Author:gly Date: 2024-09-30
Geoff Giordano is a tech journalist with more than 30 years’ experience in all facets of publishing. He has reported extensively on the gamut of plastics manufacturing technologies and issues, including 3D printing materials and methods; injection, blow, micro and rotomolding; additives, colorants and nanomodifiers; blown and cast films; packaging; thermoforming; tooling; ancillary equipment; and the circular economy. Contact him at [email protected].
HASCO is one of Europe’s leading form-service and mold making companies and currently holds the largest stock of standard mold parts in Scandinavia. They recently developed a Quick-Change Mold System which allows injection molding manufacturers to quickly and efficiently swap out their molds to reduce the time and expense of resetting their machinery. And thanks to 3D printed molds made on a high-tech Stratasys 3D printer they have made the process even cheaper, allowing for faster and less expensive prototyping, samples and affordable low-volume production runs.
Adidas has teased a new 3D-printed shoe, sending it to shoe photographer Tyler Mansour, also known as Arab Lincoln, who showcased it on his Instagram. Tyler introduced the shoes by...
Added Christopher Navratil, CTO of Alltrista's parent company: "We were determined to be the first manufacturer to run a system with 128 cavities in under two seconds. In Netstal, z-moulds, and Intravis, we have found the best system partners for this project. Each company is a leader in its field, and the combination is unbeatable. With our 128-cavity systems, we produce more efficiently than ever before, can deliver at any time, and inspire our customers. This has given us an enormous competitive advantage."
Stay up-to-date on all the latest news from the 3D printing industry and receive information and offers from third party vendors.
A 128-cavity mold will produce 26-mm water closures in a cycle time of 1.9 seconds in a live experience at Netstal’s booth at NPE 2024.
The mold, produced by Austria’s z-moulds, is as small and light as a 96-cavity mold and fits into the injection molding machine with a smaller column distance. Cycle time is reduced by the smaller design, which also requires moving less mass. Alltrista has cut the weight of its enclosures by 25%; with 3.1 billion closures produced annually, that means more than 2 million pounds less resin used – about the weight of 160 African Bush elephants, the company said.
“The speed of the process was incredible. Using our Objet500 Connex 3D Production System, we produced the parts of the cavity that shape the polymer – such as the inserts and slides – in just six hours compared to the 24 hours it previously took. Through the use of tried-and-tested standardized HASCO products and Stratasys state-of-the-art 3D printing, the project has proved that it is possible to implement this innovative rapid-technology application within the injection molding process. For the production of low-volume prototypes in the final product material, the ability to quickly change molds with a 3D printed cavity offers a rapid, low-cost alternative to conventional methods,” Paulmann confirms.
The injection molds are 3D printed using a Stratasys Objet500 Connex 3D printer, with the molds themselves being printed using their super-durable Digital ABS material. In addition to being one of the most advanced, multi-material 3D printers on the market, the Objet500 Connex is also a remarkably fast printer. By 3D printing molds rather than milling them from aluminum the time required for the mold production process can be dramatically reduced, allowing for quick and inexpensive adjustments to prototypes and molds. When the molds are combined with the K3500 Quick-Change Mold System, HASCO says that it sets a new low-cost benchmark for prototyping and low-volume injection molding.
Stay up-to-date on all the latest news from the 3D printing industry and receive information and offers from third party vendors.
“With time-to-market cycles shorter than ever and production quantities dropping, our customers are now looking for solutions that enable them to deliver prototypes quickly and cost-effectively. Compared with conventional metal or aluminum inserts, our new approach offers molders the flexibility to quickly produce and switch inserts, making them much more productive and profitable. Combining our longstanding heritage in mold making with Stratasys’ pioneering expertise in 3D printing injection molds, this best of both worlds technique is the future of prototype and low volume production,” said Dirk Paulmann, HASCO’s Executive VP of Sales & Business Development.
The global 3D printing market continued its upward trajectory in the second quarter of 2024, totaling $3.45 billion—a year-over-year increase of 8.4%. Despite a slight sequential decline from $3.47 billion...
In 3D Printing News Briefs today, four graduate students received $10,000 scholarships from ASTM International, and 3DPRINTUK announced the first commercial launch of the Stratasys SAF printer in the UK....
In the NPE demonstration, finished caps will travel through an Intravis vision-inspection system. The system executes 360-degree inspection of the closures to an accuracy of hundredths of a millimeter using nine high-resolution cameras.
Carbon and Keystone Industries just hit a milestone with the successful production of one million dental parts, highlighting the steady progress in 3D printing for dental manufacturing. In just 314,000...
"With the new CAP-Line concept, we are aligning our portfolio even more closely with our customers' applications,” he noted. “Closure manufacturers benefit from a customized system, while pre-configuration can speed up the consultation and quotation process so that delivery times for the machine are as short as possible."
Register to view and download proprietary industry data from AM Research and 3DPrint.com Questions? Contact info@3dprint.com
Overall, Netstal’s CAP-Line also fits in a smaller overall space — 538 square feet — and uses about 12% less electricity than competing machines running 96-cavity molds, Kogler said.
You can find out more about the K3500 Quick-Change Mold System on the HASCO website. And you can find out more about the Stratasys Objet500 Connex 3D printer here. Let us know your thoughts on the future role of 3D Printing within the injection molding space. Discuss in the HASCO forum thread on 3DPB.com.
Injection molding is probably the single most popular form of mass production on the planet. While the manufacturing process was invented in 1919 it wasn’t until World War II that it became widely used and since then we’ve been living in an injection molded world. It is very likely that every person on the planet has dozens if not hundreds of products manufactured with the process in their home. Initially only certain varieties of plastics could be injection molded and to this day thermoplastics remain the most popular application. But these days the process will work with virtually any material, including metal, flexible elastomers, glass and even food. Molds are typically made from steel or aluminum and created using subtractive manufacturing techniques like a CNC machine. But recently companies have begun experimenting with advanced 3D printing materials and processes in order to simplify the mold creation process.
HASCO stumbled on the process almost accidentally while producing a sealing plug using its industry-standard A8001 clamping fixture. Because of the geometry of the screw required it simply could not be produced using conventional injection molding processes. But because the Stratasys Objet500 Connex is capable of extremely fine detail on objects with complicated geometries, HASCO was able to redesign the screw mold at the correct size and wall thickness without any problems. The company 3D printed several new mold inserts to test and verify the integrity of the design. Once the 3D printed molds proved themselves to work as expected they happily moved on to the mass production phase.
"Alltrista is the first in the world to produce with 128 cavities and a cycle time of 1.9 seconds,” said Horst Kogler, head of Netstsal’s caps and closures business unit. “They produce more than 3.1 billion closures with two lines [annually]. More output per square meter of production area is currently not possible."
Netstal’s CAP-Line 4500 is identical to two production systems being used by Alltrista, a contract manufacturer based in Greer, SC. The line features an all-electric clamping unit with 4,500 kN of force and a dry cycle time of 1.4 seconds. An optimized barrier screw allows for a smaller injection unit with higher plasticizing performance and better homogenization, Netstal expained.
GETTING A QUOTE WITH LK-MOULD IS FREE AND SIMPLE.
FIND MORE OF OUR SERVICES:
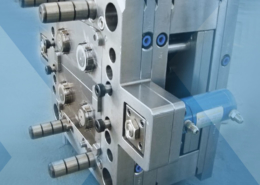
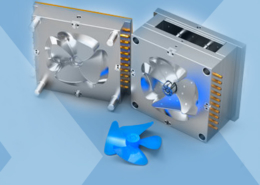
Plastic Molding

Rapid Prototyping
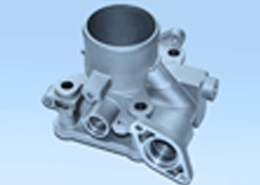
Pressure Die Casting
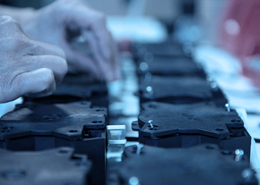
Parts Assembly
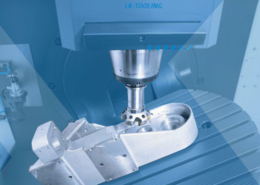