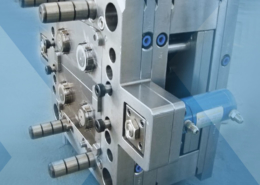
Where and How to Vent Injection Molds: Part 3 - plastic molding 1 inch
Author:gly Date: 2024-09-30
Harral says the experience has been a good one for him, “Recycling opens up a huge number of doors in the fields of engineering and art. Personally, I have found huge capabilities in using collected plastic and reconstituting it into an engineering medium, rather than simply putting it in a bin, only to maybe get recycled at a plant.”
“Our efforts are going toward using 100% of recycled plastic collected locally to make new products, tools, and art. This includes things such as cutting boards, keychains, bowls, plates, frisbees, tool handles and so much more,” says Harral.
Students get involved in the project from across campus. They may talk about the project in an AEST class, while others have done independent studies or honors theses or become involved through a club. Manusos says the SME club (Society of Manufacturing Engineers, is one of the most involved student organizations with the project.
“In addition to making durable items, students have the ethical implications for thinking about what they’re doing, what they’re making and how it will be used,” says Manusos. “And they use critical thinking to figure it out from start to finish – how the durable goods should be designed, produced, and put into the hands of others. What we do with the products when they are no longer useful and whether we can design products that can be recycled again are also important considerations.
The impetus behind the recycling project was to give the students an authentic experience in plastics recycling. “Often times we hear that plastic waste is not being handled properly and can end up in our local watershed. The Ocean Cleanup project is a non-profit organization that develops and scales technologies to rid the world’s oceans of plastic,” says Manusos. “The Ocean Cleanup and movements like “Precious Plastic” have many YouTube videos on how to reuse plastic in a meaningful way rather than throwing it away and having it land in the ocean. Precious Plastics also offers guidance, and schematics on building equipment for plastics recycling, opening a local recycling hub, and running an online store devoted to promoting the sale of plastic goods or equipment needed for these processes.”
Manusos applied for and received a $2,500 Positive Energy Fund grant from the University to purchase materials to build an extruder, an injection molder and to upgrade an existing plastics shredder. This will allow the department to scale up its capacity as the MU Sustainability Club scales up its collection.
Manusos hopes to grow the program by building additional equipment and working with the Sustainability Club on campus so they can take in plastic from across the campus, from offices, residence halls, the cafeteria, etc., and make it into something useful.
Fusible-core injection molding technology has been employed to mold a fuel housing for an aircraft using PEEK (polyetheretherketone) resin supplied by Victrex (West Conshohocken, PA). The solution reportedly delivers a 30% cost saving and up to 50% weight reduction versus existing metal designs.Processor Egmond Plastic was able to consolidate the number of parts using a carbon fiber reinforced grade of Victrex PEEK polymer. A separate bearing, for example, was eliminated since it is now integrated into the overall design of the housing.Fuel housing molded for CF-PEEK compound using fusible core process.Fuel housings for aerospace applications have very complex inner geometries which are not moldable using conventional injection molding technology. Egmond Plastic's fusible-core technology enables moldings of complex hollow housings, manifolds, and pipes. Richard Brandwijk, Managing Director at Egmond Plastic, explains: "Our technology, in combination with carbon fiber reinforced Victrex PEEK polymer, delivers numerous benefits. These include cost reduction, enhanced manufacturing speed, and weight reduction leading to improved fuel efficiency and reduced CO2 emissions. Along with part consolidation, this exceptional technology and material combination enables the design of very complex parts, beyond the capabilities of standard injection molding and metal processes."Utilizing a near net-shape manufacturing process for the fusible core allows for an 80% time saving versus machined parts. Further, secondary treatments for corrosion protection, such as anodizing, can be eliminated. Lead times can be reduced by 50%. These factors combine to deliver part cost savings of more than 30% versus metal equivalents."The global aerospace industry stands to gain enormously by persistently replacing metals in key applications, in which Egmond has demonstrated tremendous leadership," said Uwe Marburger, Aerospace Business Development Manager at Victrex. "Clearly, our PEEK knowledge and material solutions help enable the use of a technology that addresses some of the toughest challenges in complex aerospace part design and productions."Previously, the end-user had generally specified aluminum for the production of fuel containing parts, but a carbon fiber reinforced PEEK polymer demonstrated superior fatigue performance when compared to aluminum. It does this while meeting all the engineering requirements for this application, including stiffness, effective flame, smoke and toxicity (FST) performance, and resistance to aggressive chemicals, including notably, for this aerospace application, resistance to jet fuel and Skydrol hydraulic fluid. Parts can range in size all the way up to 30 cm x 30 cm x 40 cm (11.8 in x 11.8 in x 15.8 in), and typically the process is used for production runs of up to 2,000 parts.Egmond's unique fusible-core technology has already established a proven track record using Victrex PEEK in a fuel pump for the Eurofighter Typhoon, a jet fighter in use in several European countries. This pump has been in successful operational use for more than 20 years.
It takes a lot of coordination, smarts and a rather large shredder to take post-consumer plastic, like plastic water or soda bottles, and repurpose them into something more permanent. But that’s exactly what’s happening at Millersville University.
“These will be items made out of 100% recycled plastic,” says Manusos. “It’s from plastic from our campus that would have been tossed. It’s a great way to promote sustainability – making a durable item from something that people likely would have thrown away.”
This is impressive and meaningful work — much needed on campus and in all communities. Thank you for leading this effort!
Fusible-core injection molding technology has been employed to mold a fuel housing for an aircraft using PEEK (polyetheretherketone) resin supplied by Victrex (West Conshohocken, PA). The solution reportedly delivers a 30% cost saving and up to 50% weight reduction versus existing metal designs.Processor Egmond Plastic was able to consolidate the number of parts using a carbon fiber reinforced grade of Victrex PEEK polymer. A separate bearing, for example, was eliminated since it is now integrated into the overall design of the housing.
This is great news! I would love to see you make benches and tables from plastics on campus! This campus needs to recycle! All trash bins on campus should have a recylce bin next to it! Thank you for all you are doing!! Go Ville!!
Manusos says the students will get to decide what they will make from recycled plastic this semester. It could be Millersville keychains or maybe Millersville branded coasters. He says they hope to sell the products at the bookstore on campus. Another thing they’ve considered is selling shredded plastic by the pound.
“AEST is good at engineering, designing and fabricating things,” said Manusos, “so it made sense to build equipment to recycle plastic. A few years ago, our students built a plastic shredder using the Precious Plastics plans; the recent grant dollars were used, in part, to help upgrade that machine. These grant dollars were also used to support the construction of an extruder, which takes the chipped-up plastic and extrudes it into a long filament, similar to a weed whacker trimmer line. This project was largely the work of one of our students who was using the project for his Honors Thesis. This machine, when complete can be used to create the aw filament needed to feed our 3D printers, or the resulting filament can be chipped up and used in our injection molding machines.”
“Currently, our students bring in their own plastic waste to be sorted, cleaned, shredded and turned into something different,” explains Dominick Manusos, assistant professor in Applied Engineering, Safety & Technology. “We take the plastic waste, sort it by type and color, clean and wash it, shred it, put it through any number of machines and processes to make something useful.”
The recycling process will be presented to Millersville’s Council of Trustees at their Sept. 21 meeting. Millersville students Lauren Coca and Jackson Harral will present with Manusos at the meeting.
GETTING A QUOTE WITH LK-MOULD IS FREE AND SIMPLE.
FIND MORE OF OUR SERVICES:
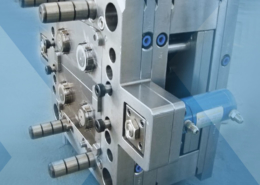
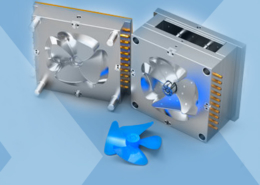
Plastic Molding

Rapid Prototyping
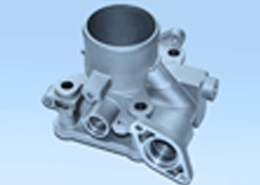
Pressure Die Casting
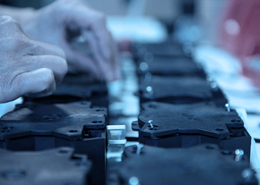
Parts Assembly
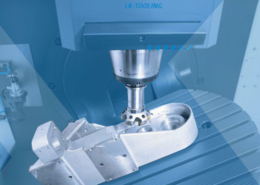