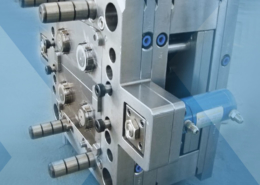
Where and How to Vent Injection Molds: Part 3 - best plastic for injection moldi
Author:gly Date: 2024-09-30
Continental said it consistently invests in the digitalization and automation of its global manufacturing operations at its 20 tire plants in 16 countries worldwide. The company said the focus lies on research and development of technologies, alternative materials, environmentally friendly production as well continuous improvements of the overall efficiency of logistics processes. By 2050 at the latest, the tire manufacturer said it aims to achieve 100% climate neutrality along its entire value chain.
The FIM process begins with high-precision, tight-tolerance, dissolvable tools printed by means of digital light processing. The tools can be used in injection molding machines with injection pressures up 2500 bar and maximum melt temperatures of 842°F (450°C), and are compatible with composites, thermoplastics, thermoplastic elastomers, silicones, ceramics, and metals. Rather than ejecting the component from the tool, as is customary in injection molding, the tool itself dissolves to release the molded part. The demolding takes between 12 and 48 hours.
Continental has acquired the mold manufacturing specialist EMT s.r.o. based in Púchov, Slovakia. All shares of Continental’s long-standing supplier were transferred to Continental effective April 2. The tire manufacturer had entered into a respective agreement with EMT’s shareholders, Dynamic Design (Romania) being the majority shareholder. All 107 employees, who have specialist knowledge in mold manufacturing, have been taken on by Continental, the company said. Further details of the agreement were not disclosed. Related Articles - VIP Tires & Service celebrates employee achievements at 2024 conference - The Group announces leadership changes - TIA to host Right to Repair Summit EMT is a manufacturer of special tire molds, especially for commercial vehicle and specialty tires. According to Continental, the company specializes in the milling of molds made of steel. With the acquisition of EMT, Continental said it completes its internal portfolio for mold making technologies. From now on, the tire manufacturer can independently produce tire molds for all applications if required. A first major step in this direction was the takeover of German mold manufacturer A-Z Formen in 2015 and Czech mold specialist VFC in 1993. Both companies specialize in producing molds for passenger car tires. “With the acquisition of EMT, we can act completely independently in mold making if required. Having expertise for all mold applications in house is a strategic advantage, given the economic uncertainties worldwide,” Dr. Bernhard Trilken, head of production and logistics at Continental’s Tires group sector, said. Continental said molds are used in tire construction as part of the vulcanization of tires. In this production step, raw rubber is converted into a flexible and elastic rubber. With the help of molds, a tire gets its desired stability and shape. “We are excited about the technological reinforcement that the EMT team brings to the table. As a long-standing partner, the relationship with Continental is already close,” said Julia Sadrina, who is responsible for production of tire molds and machinery worldwide for Continental’s tire business. Continental said it consistently invests in the digitalization and automation of its global manufacturing operations at its 20 tire plants in 16 countries worldwide. The company said the focus lies on research and development of technologies, alternative materials, environmentally friendly production as well continuous improvements of the overall efficiency of logistics processes. By 2050 at the latest, the tire manufacturer said it aims to achieve 100% climate neutrality along its entire value chain.
TPMS developer Hamaton said its new app-based retrofit TPMS kit, BLE Retro-Pro, will make its inaugural appearance at this year's Specialty Equipment Market Association (SEMA) show. According to the company, BLE Retro-Pro works with trailers and RVs, along with non-TPMS-enabled passenger vehicles and light trucks.
The so-called Scale-Up Platform promoted by the partnership reportedly enables development of 3D-printed injection mold tooling at 15% of the cost, 12% of the time, and with 75% fewer CO2 emissions compared with the use of conventional steel tools.
In her nomination, RNR said Mary Van Ochten is described as a dedicated teacher who welcomes her students to a fun environment.
Addifab has customers in industries ranging from medical and automotive to consumer electronics — in 2020, the company ran more than 300 client projects, according to Carsten Jarfelt, US Chief Commercial Officer. FIM is compatible with an extensive range of polymers, including biocompatible resins for medical and FDA-regulated projects. A 2019 study conducted by the Technological Institute in Denmark demonstrated that material from the FIM molds did not transfer to the product during the injection molding process and, thereby, did not compromise biocompatibility.
The Freeform Injection Molding process slashes the manufacture of injection mold tooling from weeks or months to a few hours.
Based on 3D printing technology, the FIM process allows users to additively manufacture complex injection mold tooling in hours instead of weeks or months. The tools are compatible with most thermoplastic materials, including reinforced high-performance feedstocks. The tooling can be dissolved, which allows the molding of complex components that would otherwise be difficult — or even impossible — to mold with conventional metal tooling, said Addifab.
The center will cover 753,000 square feet in the Dallas-Fort Worth Metropolitan area and operations are scheduled to begin in 2026.
“With the acquisition of EMT, we can act completely independently in mold making if required. Having expertise for all mold applications in house is a strategic advantage, given the economic uncertainties worldwide,” Dr. Bernhard Trilken, head of production and logistics at Continental’s Tires group sector, said.
Additionally, Hamaton said it will present phone-programmable NFC, BLE and aftermarket universal TPMS sensors, along with "feature-rich and cost-effective" TPMS diagnostic tools, and an extensive range of valves, workshop tools, and TPMS consumables.
Denmark’s Addifab, the developer of Freeform Injection Molding (FIM) technology that allows plastics processors to additively manufacture complex injection mold tooling in a matter of hours, announced today a partnership with Nexa3D, a maker of ultrafast 3D printers for industrial applications based in Ventura, CA. Through the collaboration, Nexa3D will supply its NXE 400 system — including the industrial 3D printer as well as wash and cure units — to FIM users. Addifab, which has its US office in Palo Alto, CA, will supply its proprietary tooling resins and post-processing equipment through the partnership. The agreement will broaden capabilities for industrial injection molding with ultrafast, large-format 3D printing, said the companies in today’s news release.
Editor in chief of PlasticsToday since 2015, Norbert Sparrow has more than 30 years of editorial experience in business-to-business media. He studied journalism at the Centre Universitaire d'Etudes du Journalisme in Strasbourg, France, where he earned a master's degree.
Continental said molds are used in tire construction as part of the vulcanization of tires. In this production step, raw rubber is converted into a flexible and elastic rubber. With the help of molds, a tire gets its desired stability and shape.
EMT is a manufacturer of special tire molds, especially for commercial vehicle and specialty tires. According to Continental, the company specializes in the milling of molds made of steel. With the acquisition of EMT, Continental said it completes its internal portfolio for mold making technologies. From now on, the tire manufacturer can independently produce tire molds for all applications if required. A first major step in this direction was the takeover of German mold manufacturer A-Z Formen in 2015 and Czech mold specialist VFC in 1993. Both companies specialize in producing molds for passenger car tires.
Nexa3D CEO Avi Reichental first encountered FIM at the RAPID + TCT conference in 2019, and saw the potential to reimagine additive tooling, he said in a prepared statement. “As both Addifab and Nexa3D have since productized and industrialized our respective processes, it became obvious that together we can achieve much more by digitizing injection molding at convincing scale sustainably. I can’t wait to see the far-reaching impact of our collaboration,” said Reichental.
“We are excited about the technological reinforcement that the EMT team brings to the table. As a long-standing partner, the relationship with Continental is already close,” said Julia Sadrina, who is responsible for production of tire molds and machinery worldwide for Continental’s tire business. Continental said it consistently invests in the digitalization and automation of its global manufacturing operations at its 20 tire plants in 16 countries worldwide. The company said the focus lies on research and development of technologies, alternative materials, environmentally friendly production as well continuous improvements of the overall efficiency of logistics processes. By 2050 at the latest, the tire manufacturer said it aims to achieve 100% climate neutrality along its entire value chain.
“Injection molding is a complex process, and tool building is the most complex part of the process,” said Lasse Staal, co-founding CEO of Addifab. “With Freeform Injection Molding, we provide injection molders with a fully transparent set of tools — no pun intended — that will allow them to fast-track tool designs and validations while raising the bar on tool innovation. Now we can take these capabilities to the next level by partnering with Nexa3D to broaden access and super power performance.”
The partners will come full circle when they showcase their joint solution at the RAPID + TCT show in Detroit on May 17 to 19, 2022. The companies are also setting up joint Silicon Valley demo facilities in Palo Alto.
GETTING A QUOTE WITH LK-MOULD IS FREE AND SIMPLE.
FIND MORE OF OUR SERVICES:
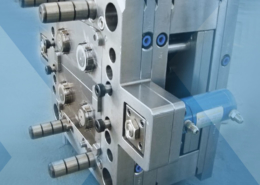
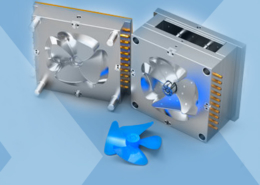
Plastic Molding

Rapid Prototyping
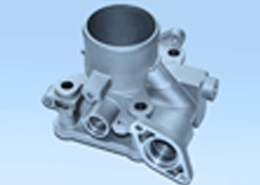
Pressure Die Casting
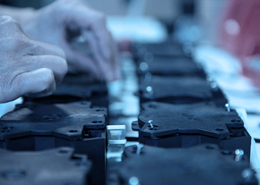
Parts Assembly
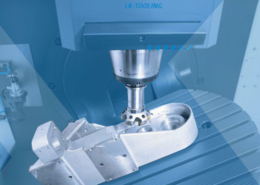