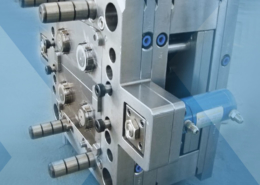
What’s Your Process Energy Fingerprint? - pvc moulding electrical
Author:gly Date: 2024-09-30
Hou, B. et al. A hybrid hint-based and fuzzy comprehensive evaluation method for optimal parting curve generation in injection mold design. Int. J. Adv. Manuf. Technol. 112, 2133–2148 (2021).
Xie, P. et al. Effect of gate size on the melt filling behavior and residual stress of injection molded parts. Mater. Des. 53, 366–372 (2014).
In a time where sustainability is no longer just a buzzword, the food and beverage packaging industry is required to be at the forefront of this innovation. By adopting circular packaging processes and solutions, producers can meet regulatory requirements while also satisfying consumer demand and enhancing brand reputation. Join Husky to learn more about the broader implications of the circular economy — as well as how leading brands are leveraging this opportunity to reduce costs, increase design flexibility and boost product differentiation. Agenda: The cost and operational benefits of embracing circularity Key materials in circular packaging — including rPET and emerging bioplastics How to design a circular food and beverage package Strategies for selecting sustainable closures to future-proof packaging solutions Optimization and streamlining of production processes for enhanced efficiency How Husky Technologies can enable your sustainable success
The grey correlation degree of a comprehensive evaluation of hydrogen storage cylinders is derived from formula (1) to formula (4). At this time, the four factors multi-objective evaluation index problem can be transformed into a single objective evaluation index problem. The results are shown in Table 8. The grey correlation data were processed by the range and mean analysis, and the results are shown in Table 9.
Through the analysis of the first direction residual stress process range, better process parameters combinations A4B2C1D3E4 can be obtained. When the melt temperature reaches 270 °C, the mold temperature reaches 80 °C, the holding pressure is 50 MPa, the holding time is 20 s, and the cooling time is 23 s. The optimum combination is not in the test times, the optimized molding process parameters are input into Moldflow software for analysis and verification. The final result is shown in Fig. 6. The residual stress in the first direction is 98.43 MPa.
The resulting vertical integration propelled by this mindset extends into some unexpected areas. To wit, the company’s original 245,000-square-foot facility in Ontario, California, includes a carpentry shop that designs, builds and installs all the office furniture for all of US Merchants’ facilities. Outside the shop, an “Arizona Project ‘22” poster hangs, marking its recent work to fully furnish the company’s newest outpost. US Merchants sent its own carpenters to the new facility where they took measurements for all its furnishings before coming back to California to build all the desks, shelving and more, and then return to Arizona to install it. When it’s not building furniture for the company, the carpentry shop also designs and constructs trade show booths for US Merchants, as well as store point-of-purchase displays.
Ultradent's entry of its Umbrella cheek retractor took home the awards for Technical Sophistication and Achievement in Economics and Efficiency at PTXPO.
The PS is the part that can be contacted when the moving mold and the fixed mold are closed, and the parting surface is where the plastic part is removed from the mold. The design of PS directly affects the product quality, mold structure and the difficulty of operation, and is one of the key factors for the success of mold design. When determining the parting surface, the location of the plastic part in the mold, the design of the cavity gating system, the structural manufacturability of the plastic part, the mold fabrication, venting and the operation process must be considered in conjunction with the design features of the hydrogen storage cylinder liner. After considering the above characteristics, the lining parting surface diagram was obtained, as shown in Fig. 131,32.
Li, C.-L. Design of flip-chip injection mold for chassis top cover based on CAE technology. Plastics 49(04), 50–54 (2020).
Say “manufacturing automation” and thoughts immediately go to the shop floor and specialized production equipment, robotics and material handling systems. But there is another realm of possible automation — the front office.
“I can give a customer a delivery date,” Green says, “and I know that I can meet that date. Why? Because we control the entire process. We do all that in-house and we control it, so I know that if I give somebody a promise, I’m going to be able to deliver because we do everything in-house.”
Analysis of warpage results: The warpage test data in Table 3 were analyzed by the range analysis method, and the analysis results are shown in Table 4.
In less than a decade in injection molding, US Merchants has acquired hundreds of machines spread across facilities in California, Texas, Virginia and Arizona, with even more growth coming.
Join KraussMaffei for an insightful webinar designed for industry professionals, engineers and anyone interested in the manufacturing processes of PVC pipes. This session will provide a comprehensive understanding of the technology behind the production of high-quality PVC pipes: from raw material preparation to final product testing. Agenda: Introduction to PVC extrusion: overview of the basic principles of PVC pipe extrusion — including the process of melting and shaping PVC resin into pipe forms Equipment and machinery: detailed explanation of the key equipment involved — such as extruders, dies and cooling systems — and their roles in the extrusion process Process parameters: insight into the critical process parameters like temperature, pressure and cooling rates that influence the quality and consistency of the final PVC pipes Energy efficiency: examination of ways to save material and energy use when extruding PVC pipe products
Now the owner of hundreds of injection molding machines, Jeff Green speaks frankly about his company’s molding knowledge when he acquired his first presses in 2014. “We didn’t know anything about injection molding,” Green says. “I knew as much about injection molding as you know about flying a 747 airplane.”
Across the show, sustainability ruled in new materials technology, from polyolefins and engineering resins to biobased materials.
Xu, Y. et al. Optimization of injection molding process parameters to improve the mechanical performance of polymer product against impact. Int. J. Adv. Manuf. Technol. 76(9–12), 2199–2208 (2017).
Dicheng, F. Design of injection mold for automotive cable connector based on CAD/CAE. Plast. Technol. 48(06), 102–108 (2020).
In the foreground, rows of shrink-wrapped pallets ready for delivery. In the background, US Merchants in-house thermoforming lines. Photo Credit: Plastics Technology
Formnext Chicago is an industrial additive manufacturing expo taking place April 8-10, 2025 at McCormick Place in Chicago, Illinois. Formnext Chicago is the second in a series of Formnext events in the U.S. being produced by Mesago Messe Frankfurt, AMT – The Association For Manufacturing Technology, and Gardner Business Media (our publisher).
Despite price increase nominations going into second quarter, it appeared there was potential for generally flat pricing with the exception of a major downward correction for PP.
Md Yusof, M. & Abu Mansor, M. S. Alternative method to determine parting direction automatically for generating core and cavity of two-plate mold using B-rep of visibility map. Int. J. Adv. Manuf. Technol. 96, 3109–3126 (2018).
Xianbing, C., Yifei, C. & Yuanji, S. Design and CAE optimization analysis of injection mold for set-top box pouring into the same mold and different cavity. Eng. Plast. Appl. 49(08), 87–92 (2021).
Another factor determining the quality of injection parts is process parameters; such as injection temperature, mold temperature and injection time, which they directly affect the production cost and quality. Unreasonable process parameters will lead to different defects in the final product, such as warping, shrinkage and residual stress, thereby reducing the mechanical properties of injection molded parts17,18,19,20. When manufacturing the cylinder liner, the process parameters will affect the quality properties, such as weld marks, under-injection and so on, increasing the waste rate.
August 29-30 in Minneapolis all things injection molding and moldmaking will be happening at the Hyatt Regency — check out who’s speaking on what topics today.
The influence of process parameters on the evaluation index was further optimized by grey correlation analysis and Taguchi algorithm based on SNR.
The hydrogen storage cylinder lining was taken as the research object. The injection model of the cylinder liner was developed employing 3D software, a two-cavity injection molding system was built, and Moldflow was utilized for analysis to determine the best combination of injection molding process parameters. The effects of injection process parameters (melt temperature, mold temperature, holding pressure, holding time and cooling time) on the evaluation index were analyzed by orthogonal experiment L16(45). The prediction data of IV hydrogen storage cylinder lining under different parameters were obtained by the range analysis method. The multi-objective optimization problem of injection molding process was transformed into a single-objective optimization problem by using the grey correlation analysis method. The optimal parameters such as melt temperature 270 °C, mold temperature 80 °C, packing pressure 55 MPa, packing time 20 s and cooling time 13 s were obtained. Taguchi method was adopted to obtain SNR (signal-to-noise ratio), while range and variance methods were used for analysis. The results showed that warpage was 0.4892 mm, the volume shrinkage was 12.31%, the residual stress in the first direction was 98.13 MPa, and the residual stress in the second direction was 108.1 MPa. The comprehensive index was simultaneously most impacted by the melt temperature.
Ozcelik, B., Kuram, E. & Topal, M. M. Investigation the effects of obstaclegeometries and injection molding parameters on weld line strength usingexperimental and finite element methods in plastic injection molding. Int. Commun. Heat Mass Transf. 39, 275–281 (2012).
Jeff Green, president and CEO of US Merchants, grew his business alongside the warehouse club stores that emerged in the ‘80s. Photo Credit: US Merchants
Liu, X. Design of complex side core-pulling injection mold for automotive headlight housing. Eng. Plast. Appl. 49(11), 99–103+108 (2021).
Almeida, F. D., Sousa, V. F. C., Silva, F. J. G., Campilho, R. D. S. G. & Ferreira, L. P. Development of a novel design strategy for moving mechanisms used in multi-material plastic injection molds. Appl. Sci. 11(24), 11805 (2021).
Orthogonal experimental optimization technology, an experimental method to study multiple factors and levels, employs different orthogonal arrays to minimize the number of experiments, thereby reducing the time and cost25. The purpose of the experimental study must be established before designing orthogonal experiments. The experimental measurement indicators are developed in accordance with the objectives of the experimental study to determine the influencing factors of the experiment.
Injection molding (IM) is a popular polymer processing technology for the manufacture of plastic products with complex shapes, high precision and low cost, resulting in products with high quality and good dimensional tolerances5,6. Mode design and process parameters can improve the quality of injection molded parts. One of the main tasks of mold design is gate design7. The gate is the first orifice where the material is injected into the cavity. It has been demonstrated that an appropriate gate size and runner aid in the quick injection of molten plastic into the cavity, enhance the product's mechanical characteristics and aesthetics, and lessen warping and residual stresses in injection-molded components8,9. Another factor in the design of the mold is the number of gates. Setting two gates on both sides of the product as opposed to only one on one side will enhance the turbulence of molten plastic. Another significant element influencing the quality of injection-molded products is the gate position in the mold design. Injection molded components can solidify faster and with fewer flaws if the gate is placed properly10,11,12,13.
According to the structure and process requirements of hydrogen storage cylinder liners, the cylinder liner forming mold was designed. The mold had two cavities, and the core was extracted using a hydraulic auxiliary method.
The cylinder liner mainly acts as a barrier to hydrogen. This simulation uses ammonium polyphosphate (PA6). The main performance indicators are shown in Table 1.
In this paper, the hydrogen storage cylinder liner structure needs to be molded by injection molding on the base of the metal head. Therefore, the core, cavity and ejection mechanisms of the hydrogen storage container liner injection model were designed, and the mold parts were established by 3D software. The mold design required not only the above mentioned parts but also the mold frame, gating system, cooling system, ejection mechanisms and exhaust system be supported. The three-plate mold frame and double cavity mold were used, and the latent gate was used in the gating system. Cooling channels were provided in the cavities and cores. The injection parts were ejected by a hydraulic ejector bar. A large amount of gas generated in the molding process will be carried away through the gap between the inserts. The final two-dimensional engineering diagram is shown in Fig. 3.
In this collection, which is part one of a series representing some of John’s finest work, we present you with five articles that we think you will refer to time and again as you look to solve problems, cut cycle times and improve the quality of the parts you mold.
k1, k2, k3 and k4 donate the average of the sum of each factor index at four levels, and the difference is R. Through the analysis of the warping process range, a better combination of process parameters A4B2C3D3E3 can be obtained. When the melt temperature reaches 270 °C, the mold temperature reaches 80 °C, the holding pressure is 55 MPa, the holding time is 20 s, and the cooling time is 18 s. The optimum combination was not in the test times, the optimized molding process parameters were entered into Moldflow software for analysis and verification. The final result is shown in Fig. 4, with a warping of 0.5185 mm.
Wang, G., Wang, G., & Yang, G. Study on automotive back door panel injection molding process simulation and process parameter optimization. Adv. Mater. Sci. Eng. https://doi.org/10.1155/2021/9996423 (2021).
The comparison of ANOVA and ANOVA shows that the degree of influence of each factor is consistent, but ANOVA can more intuitively see the influence of each factor on the index.
Pomerleau, J. & Sanschagrin, B. Injection molding shrinkage of PP: experimental progress. Polym. Eng. Sci. 46(9), 1275–1283 (2006).
Beginning in retail himself in 1979 with a tennis store in Beverly Hills dubbed with the pun-intended name — The Merchants of Tennis — Green grew into the wholesale business at a time in the early ‘80s when warehouse club chains were just getting started. One of Green’s patents is for the Pallet Program he devised as a means for those retailers to turn pallets of shrink-wrapped and boxed-up goods into ready-to-go, point-of-purchase displays with nothing more than a box cutter.
While the melting process does not provide perfect mixing, this study shows that mixing is indeed initiated during melting.
According to the injection molding results shown in Table 7, the influence order of the process parameters on the residual stress in the second direction is:holding time > mold temperature > melt temperature > holding pressure > cooling time.
Mold maintenance is critical, and with this collection of content we’ve bundled some of the very best advice we’ve published on repairing, maintaining, evaluating and even hanging molds on injection molding machines.
In this paper, the injection mold for IV-type hydrogen storage cylinder lining is designed. The injection molding process parameters were studied. The optimum combination of process parameters was selected after range analyses of each assessment index. To determine the level of each parameter's effect on the overall assessment index, two additional analytic techniques are used: grey correlation degree and Taguchi and SNR. On this basis, the injection molding process parameters are simulated and verified.
Over the years and owing in part to Green’s desire for maximum control, US Merchants vertically integrated everything from graphic and package design to thermoforming and thermoform die manufacturing to shipping and logistics with his own fleet of trucks. “Our business started to grow, and not just in packaging,” Green says, “but now we offer a nice menu of items that a manufacturer or retailer can select from, be it packaging or logistics or transportation or buying the product and reselling it, which a lot of manufacturers like. We’re really a turnkey solution for them.”
By submitting a comment you agree to abide by our Terms and Community Guidelines. If you find something abusive or that does not comply with our terms or guidelines please flag it as inappropriate.
Analysis of volume shrinkage results are shown in Table 3 and the analysis results are shown in Table 5, where the influence order of the process parameters on the volume shrinkage rate is: holding time > melt temperature > mold temperature > holding pressure > cooling time.
Sateesh, N., Reddy, S. D., Kumar, G. P. & Subbiah, R. Optimization of injection moulding process in manufacturing the top cap of water meter. Mater. Today Proc. 18, 4556–4565 (2019).
Resin drying is a crucial, but often-misunderstood area. This collection includes details on why and what you need to dry, how to specify a dryer, and best practices.
When, how, what and why to automate — leading robotics suppliers and forward-thinking moldmakers will share their insights on automating manufacturing at collocated event.
In terms of sustainability measures, monomaterial structures are already making good headway and will evolve even further.
Cylinder liner mold assembly drawing. 1. Floor 2. Push rod fixing plate 3. Push rod 4. Push rod 5. Dynamic die fixing plate 6. Dynamic die 7. Fixed template 8. Guide sleeve 9. Positioning ring 10. Gate sleeve 11. Screw 12. Fixed template floor 13. Type cavity inserts 14. Dynamic template 15. Push rod 16. Recoil pin 17. Spring 18. Floor rod.
According to Table 10, the average SNR and range of each process parameter are calculated, and the results are shown in Table 11.
Successfully starting or restarting an injection molding machine is less about ticking boxes on a rote checklist and more about individually assessing each processing scenario and its unique variables.
Working closely with Steve Gwon and his machinery distribution company E Solution Inc., Hirate and US Merchants soon switched over to LS Mtron injection molding machines. Eventually, Gwon and Hirate would help US Merchants not only source machines but molds, hot runner controllers, auxiliaries, robots, chillers, material handling systems, gantry cranes, mold tilters and more. Beyond sourcing, they also gave the rookie molder advice on everything from part design and employee recruiting to laying out and commissioning new plants.
“I don’t say I have the best standard in the world, but we live or die by what our standard is, so we don’t cut corners. That doesn’t mean we don’t make mistakes — we make mistakes like everybody else. We try to learn from our mistakes and not let them happen a second time, but we don’t make mistakes because we’re trying to cut corners to make a larger margin. If I give you a better price, it’s coming out of my margin, never out of the quality of the product.”
Back in 2014, one of those manufacturers requested something that wasn’t on the menu, asking US Merchants if it could make it a better 27-gallon storage container. “I do have engineers in my packaging and machine area that understand what injection molding is and they said to me, ‘Jeff, this product requires different equipment than what we currently have,’ and so I said, ‘Will you look into it and let me know what the cost is,’ and I went back the very next day to the customer and said, ‘If you give me a commitment…’ — because we don't do anything unless we have a firm commitment — and that customer gave me a commitment, sight unseen. I guaranteed that the product would be better than what they were currently selling. I went ahead and I bought some equipment, and that’s how I got into the injection molding business.”
Mean and range analyses were performed. The warpage, volume shrinkage, residual stress in the first direction and residual stress in the second direction of the cylinder were selected as the experimental evaluation indexes, and different molding process parameters such as melt temperature, mold temperature, packing pressure, packing time and cooling time were used as the experimental level factors. The results showed that the minimum warpage process combination was A4B2C2D3E3; the minimum volume shrinkage process combination was A1B2C3D3E4; the process combination with minimum residual stress in the first direction was A4B2C1D3E4; the process combination with minimum residual stress in the second direction was A3B2C2D3E2;
According to the injection molding results shown in Table 4, the influence order of various process parameters on warpage is: holding time > melt temperature > holding pressure > cooling time > mold temperature.
Xu, G. & Yang, Z. Multiobjective optimization of process parameters for plastic injection molding via soft computing and grey correlation analysis. Int. J. Adv. Manuf. Technol. 78(1–4), 525–536 (2015).
The purpose of ANOVA is to investigate which factors significantly affect performance characteristics. The ratio of deviation square sum and total deviation square sum for each factor in variance analysis reflects the influence of process parameters on test indexes. In this paper, \(\overline{{I_{{\text{j}}} }}\) is the average SNR of a certain experimental factor at a certain level, and the average signal-to-noise ratio of all levels of all experimental factors are taken.
All data generated or analyzed during this study are included in this published article and its supplementary information files.
Core Technology Molding turned to Mold-Masters E-Multi auxiliary injection unit to help it win a job and dramatically change its process.
Beyond Plastic and partners have created a certified biodegradable PHA compound that can be injection molded into 38-mm closures in a sub 6-second cycle from a multicavity hot runner tool.
Analysis of residual stresses in the second direction: Range analysis of residual stresses in the second direction in Table 3. The analysis results are shown in Table 7.
You need to pay attention to the inherent characteristics of biopolymers PHA/PLA materials when setting process parameters to realize better and more consistent outcomes.
Therefore, we chose the grey relation modeling equation to determine the grey relation coefficient. As shown in Eq. (1), the SNR of each single quality feature was normalized by grey correlation generation. The normalized value is between 0 and 1. Subsequently, the deviation sequence (2) was used to calculate the difference between the values of the reference sequence and pretreatment . After data preprocessing, grey correlation analysis (3) was used to process normalized data to calculate grey correlation coefficient, which represents the relationship between actual and ideal normalized analysis results. After calculating the grey correlation coefficient of all 16 iterations, the grey correlation degree (4) was calculated by averaging the grey correlation coefficient values corresponding to each evaluation index.
To minimize the comprehensive evaluation index value of cylinder liner plastic parts, this paper uses the SNR function of the small characteristic to calculate its SNR. The larger the SNR is, the smaller the target value is, and the better the quality performance is. SNR is calculated according to the following formula:
Second quarter started with price hikes in PE and the four volume engineering resins, but relatively stable pricing was largely expected by the quarter’s end.
Toe, C. Shrinkage behavior and optimization of injection molded parts studied by the Taguchi method. Polym. Eng. Sci. 41(5), 703–711 (2001).
For simultaneous analysis of four evaluation indicators, residual stress in the first direction and residual stress in the second direction, the range analysis of grey correlation analysis was carried out. The best combination of process parameters was discovered when the process parameters were set to A4B2C2D3E2 (when the melt temperature reaches 270 °C, the die temperature reaches 80 °C, the packing pressure is 55 MPa, the packing time is 20 s, and the cooling time is 13 s) The optimal warpage, volume shrinkage, residual stresses in the first direction and residual stresses in the second direction were 0.5041 mm, 12.4%, 97.88 MPa and 114.1 MPa, respectively.
This Knowledge Center provides an overview of the considerations needed to understand the purchase, operation, and maintenance of a process cooling system.
Li, K., Yan, S.-L., Pan, W.-F. & Zhao, G. Optimization of fiber-orientation distribution in fiber-reinforced composite injection molding by Taguchi, back propagation neural network, and genetic algorithm–particle swarm optimization. Adv. Mech. Eng. https://doi.org/10.1177/1687814017719221 (2017).
Sustainability continues to dominate new additives technology, but upping performance is also evident. Most of the new additives have been targeted to commodity resins and particularly polyolefins.
The components that make up an injection mold are referred to as the molding parts, and typically include the core, cavity, different molding rods, and molding inserts. Forming parts can be divided into installation parts and working parts. To produce plastic components, working parts come into close contact with the plastic parts33. In order to lower the cost of the die, it is advantageous to process and manufacture the structural design of die components in a way that is both convenient and easy to acquire qualified parts34.
“My personal belief is quality stands the test of time,” Green says, “and so we as a company don’t cut any corners. I believe that making the highest quality product in the industry, you have the longest staying power.” With its molded products, that ethos extends to the removal of any flash and, if need be, to avoid warp and produce a tote that closes cleanly and securely off the press, longer cycle times.
Additive technology creates air pockets in film during orientation, cutting down on the amount of resin needed while boosting opacity, mechanical properties and recyclability.
Zhao, P. et al. A Nondestructive online method for monitoring the injection molding process by collecting and analyzing machine running data. Int. J. Adv. Manuf. Technol. 72, 765–777 (2014).
“This is where companies like LS Mtron and E Solution have really made a difference,” Green says, “because these people are professionals and experts, and we’ve kind of put ourselves in their hands to help us and direct us in the right direction.”
Hydrogen is an important renewable and sustainable energy source with the advantages of zero pollution, a high energy conversion rate and an abundance of resources. The wide application of hydrogen energy requires solving the problems of hydrogen production, storage and transportation. Hydrogen storage technology is the key to hydrogen utilization1. Among them, a hydrogen storage cylinder is the most commonly used way of hydrogen storage, consisting of a lining and a composite winding layer. At present, the cylinders can be divided into type III aluminum liner and type IV polymer liner2. High density polyethylene (HDPE), polyamide (PA6), or PET(Polyethylene terephthalate) are the primary materials utilized to create type IV cylinder linings3. In general, injection molding is one of the methods of lining molding. The plastic molding technology, namely, the combination of metal head and resin lining molding, is used to produce lining through injection molding4.
Processors with sustainability goals or mandates have a number of ways to reach their goals. Biopolymers are among them.
Join Wittmann for an engaging webinar on the transformative impact of manufacturing execution systems (MES) in the plastic injection molding industry. Discover how MES enhances production efficiency, quality control and real-time monitoring while also reducing downtime. It will explore the integration of MES with existing systems, emphasizing compliance and traceability for automotive and medical sectors. Learn about the latest advancements in IoT and AI technologies and how they drive innovation and continuous improvement in MES. Agenda: Overview of MES benefits What is MES? Definition, role and brief history Historical perspective and evolution Longevity and analytics Connectivity: importance, standards and integration Advantages of MES: efficiency, real-time data, traceability and cost savings Emerging technologies: IoT and AI in MES
As US Merchants’ business has grown, so has its capabilities, driven by Green’s intense interest in maximum control over everything that can impact his business. “You could say I’m something of a very controlling individual,” Green says. “I always felt that we need to control our own destiny. When you have to farm things out to third parties, you’re only asking for issues with delivery and excuses why something can’t be done.”
A showroom displays just some of the totes, containers and shelving US Merchants produces at molding facilities across the U.S. Photo Credit: Plastics Technology
Parting surface of cylinder liner. 1. Positioning ring 2. Fixed template floor 3. Fixed template 4. Dynamic die 5 PS surface 6. guide post.
In this three-part collection, veteran molder and moldmaker Jim Fattori brings to bear his 40+ years of on-the-job experience and provides molders his “from the trenches” perspective on on the why, where and how of venting injection molds. Take the trial-and-error out of the molding venting process.
US Merchants’ Ontario, California, injection molding facility features 46 1,200-ton LS Mtron injection molding machines. Photo Credit: US Merchants
Open Access This article is licensed under a Creative Commons Attribution 4.0 International License, which permits use, sharing, adaptation, distribution and reproduction in any medium or format, as long as you give appropriate credit to the original author(s) and the source, provide a link to the Creative Commons licence, and indicate if changes were made. The images or other third party material in this article are included in the article's Creative Commons licence, unless indicated otherwise in a credit line to the material. If material is not included in the article's Creative Commons licence and your intended use is not permitted by statutory regulation or exceeds the permitted use, you will need to obtain permission directly from the copyright holder. To view a copy of this licence, visit http://creativecommons.org/licenses/by/4.0/.
Kramschuster, A. et al. Effect of processing conditions on shrinkage and warpage and morphology of injection moulded parts using microcellular injection moulding. Plast. Rubber Compos. 35(5), 198–209 (2006).
At this time, a set of re-optimized process parameters can be obtained. The optimized combination parameters are expressed as A4B2C2D3E2. When the melt temperature reaches 270 °C, the die temperature reaches 80 °C, the packing pressure is 55 MPa, the packing time is 20 s, and the cooling time is 13 s. The simulation results of the process parameters in Moldflow software are shown in Figs. 8, 9, 10 and 11. The warpage is 0.5041 mm, the volume shrinkage is 12.4%, the residual stress in the first direction is 97.88 MPa, and the residual stress in the second direction is 114.1 MPa.
According to the injection molding results shown in Table 6, the influence order of the process parameters on the residual stress in the first direction is: melt temperature > cooling time > mold temperature > holding pressure > holding time.
Chen, S.-C. et al. Effect of cavity surface coating on mold temperature variation and the quality of injection molded parts. Int. Commun. Heat Mass Transf. 36(10), 1030–1035 (2000).
Lizhen, I. et al. Optimization of molding process parameters of automobile gear lever based on orthogonal test. China Plast. 33(7), 50–56 (2019).
The percentage contribution of each factor to the SST sum of squares can be used to assess the importance of process parameter variations on the performance characteristics. In addition, the F value shown in Table 12 can also be used to determine which factors have significant effects on performance characteristics. Typically, changes in deterministic factors have a significant effect on performance characteristics when the F-values are large.
Song, Z. et al. Optimization and prediction of volume shrinkage and warpage of injection-molded thin-walled parts based on neural network. Int. J. Adv. Manuf. Technol. 109, 755–769 (2020).
True to the adjective in its name, Dynamic Group has been characterized by constant change, activity and progress over its nearly five decades as a medical molder and moldmaker.
In this collection of articles, two of the industry’s foremost authorities on screw design — Jim Frankand and Mark Spalding — offer their sage advice on screw design...what works, what doesn’t, and what to look for when things start going wrong.
Gifted with extraordinary technical know how and an authoritative yet plain English writing style, in this collection of articles Fattori offers his insights on a variety of molding-related topics that are bound to make your days on the production floor go a little bit better.
When Plastics Technology visited US Merchants’ original Ontario facility where those first seven injection molding machines are still molding totes, the packaging/logistics side of the operation was packing up everything from skateboards and boots to batteries and bags, with finished pallets marked for delivery to New Zealand, Japan, China and destinations beyond. Forklifts navigated a towering maze of shrink-wrapped pallets ready to be loaded onto trucks, including Green’s own. The full scope of the operations is a bit overwhelming, but it all makes sense to Green. “To an outside person,” Green says, “it looks very convoluted, but the truth of the matter is it’s like a jigsaw puzzle — everything fits into place.”
Exhibitors and presenters at the plastics show emphasized 3D printing as a complement and aid to more traditional production processes.
Thank you for visiting nature.com. You are using a browser version with limited support for CSS. To obtain the best experience, we recommend you use a more up to date browser (or turn off compatibility mode in Internet Explorer). In the meantime, to ensure continued support, we are displaying the site without styles and JavaScript.
In June 2023, US Merchants opened a facility in Glendale, Arizona, covering nearly 640,000 square feet, which will have 69 LS Mtron presses when fully commissioned, including 2,500-ton and all-electric machines. A second facility is coming to Houston, and the company will be opening its first international molding facilities in Montreal and the U.K. The molding operation we tour in Ontario, which was purchased in 2017, has 46 1,200-ton LS Mtron presses divided into three rows.
The reasonable setting of the feeding system affects the quality of the parts. Selecting the proper gate number and location may not only increase forming efficiency but also guarantee the quality of the components. Considering the shape of the lining structure and to ensure a smooth surface shape, after a comprehensive analysis, the end of the barrel section away from the metal head was chosen as the pouring position. Considering the parting surface and pouring position, the submerged gate pouring was selected. When the mold was opened, the gate can be automatically separated from the plastic part under the tension of the template. Figure 2 shows a mold with a two-cavity hydrogen storage cylinder lining structure and gate system, taking into account the injection molding machine's current structure and lining structure.
Through orthogonal experiments, the effects of molding parameters on volume shrinkage, warpage, first residual stress and second residual stress of cylinder liner were studied, and the optimal combination of molding parameters corresponding to four groups of evaluation indexes was obtained. The experimental results of four evaluation indexes under the combination of 16 groups of different process parameters are shown in Table 3.
The SNR and ANOVA were carried out. In order to minimize the comprehensive evaluation index value of the bottle liner, the SNR was analyzed. The optimum technological parameters were obtained as follows: A2B4C4E4E4. Under this technological parameter, the optimum warpage was 0.4892 mm, the volume shrinkage was 12.31%, the first direction residual stress was 98.13 MPa, and the second direction residual stress was 108.1 MPa. ANOVA was used to determine the significance of each factor in experimental research. After analysis, it was found that the melt temperature has the greatest influence on the comprehensive index, accounting for about 62.15%, followed by a pressure holding time and cooling time.
Hassan, H., Regnier, N. & Defaye, G. A 3D study on the effect of gate location on the cooling of polymer by injection molding. Int. J. Heat Fluid Flow 30, 1218–1229 (2009).
The aim of this presentation is to guide you through the factors and the numbers that will help you determine if a robot is a smart investment for your application. Agenda: Why are you considering automation? What problems are you trying to solve? How and why automation can help Crunch the numbers and determine the ROI
\(\xi_{{\text{i}}} (k)\) represents the gray relational coefficients, \(\Delta_{{0{\text{i}}}} (k)\) represents the sequence differences between corresponding positions in sequence \(x_{0} (k)\) and subsequence \(x_{{\text{i}}} (k)\), \(\xi\) represents the identification coefficient (generally, 0.5).
Across all process types, sustainability was a big theme at NPE2024. But there was plenty to see in automation and artificial intelligence as well.
The SNR of small characteristics is a monotonically decreasing function, and the larger the value, the better the SNR. Therefore, in the average analysis of hydrogen storage cylinder liners, the minimum value of the total SNR should be obtained at the maximum SNR. It can be seen from the table that the optimal process parameters corresponding to the total SNR range analysis are A2B4C4E4E4, that is, the corresponding process parameters are: melt temperature is 250 °C, mold temperature is 100 °C, holding pressure is 65 MPa, holding time is 25 s, cooling time is 23 s. The simulation results of the process parameters are shown in Figs. 12, 13, 14 and 15. The warpage is 0.4892 mm, the volume shrinkage is 12.31%, the residual stress in the first direction is 98.13 MPa, and the residual stress in the second direction is 108.1 MPa.
Take a deep dive into all of the various aspects of part quoting to ensure you’ve got all the bases—as in costs—covered before preparing your customer’s quote for services.
Thousands of people visit our Supplier Guide every day to source equipment and materials. Get in front of them with a free company profile.
Join this webinar to explore the transformative benefits of retrofitting your existing injection molding machines (IMMs). Engel will guide you through upgrading your equipment to enhance monitoring, control and adaptability — all while integrating digital technologies. You'll learn about the latest trends in IMM retrofitting (including Euromap interfaces and plasticizing retrofits) and discover how to future-proof your machines for a competitive edge. With insights from industry experts, it'll walk you through the decision-making process, ensuring you make informed choices that drive your business forward. Agenda: Maximize the value of your current IMMs through strategic retrofitting Learn how to integrate digital technologies to enhance monitoring and control Explore the benefits of Euromap interfaces and plasticizing retrofits Understand how retrofitting can help meet new product demands and improve adaptability Discover how Engel can support your retrofitting needs, from free consultations to execution
Hirscher, M. et al. Materials for hydrogen-based energy storage e past, recent progress and future outlook. J. Alloys Compd. 827, 153548 (2020).
Hentati, F. et al. Optimization of the injection molding process for the PC/ABS parts by integrating Taguchi approach and CAE simulation. Int. J. Adv. Manuf. Technol. 104, 4353–4363 (2019).
Kima, H. S., Sonb, J. S. & Imc, Y. T. Gate location design in injection molding of an automobile junction box with integral hinges. J. Mater. Process. Technol. 140, 110–115 (2003).
In this collection of content, we provide expert advice on welding from some of the leading authorities in the field, with tips on such matters as controls, as well as insights on how to solve common problems in welding.
Plastics Technology covers technical and business Information for Plastics Processors in Injection Molding, Extrusion, Blow Molding, Plastic Additives, Compounding, Plastic Materials, and Resin Pricing. About Us
technotrans says climate protection, energy efficiency and customization will be key discussion topics at PTXPO as it displays its protemp flow 6 ultrasonic eco and the teco cs 90t 9.1 TCUs.
Allegheny Performance Plastics specializes in molding parts from high-temperature resins for demanding applications as part of its mission to take on jobs ‘no one else does.’
By analyzing the residual stress process range in the second direction, a better combination of process parameters A3B2C2D3E2 can be obtained. When the melt temperature reaches 260 °C, the die temperature reaches 80 °C, the holding pressure is 50 MPa, the holding time is 20 s, and the cooling time is 13 s. The optimum combination is not in the test times, the optimized molding process parameters are input into Moldflow software for analysis and verification. The final result is shown in Fig. 7. The residual stress in the second direction is 136.8 MPa.
This month’s resin pricing report includes PT’s quarterly check-in on select engineering resins, including nylon 6 and 66.
US Merchants’ newest Glendale, Arizona, facility covers nearly 640,000 square feet and will have 69 LS Mtron presses when fully commissioned.
After comprehensively considering the quality requirements of hydrogen storage cylinder lining and actual production experience, five factors were selected, including melting temperature, mold temperature, holding pressure, holding time and cooling time, recorded as A, B, C, D and E, respectively. Based on the number of factors selected in the orthogonal test, four levels of each factor were selected uniformly by combining the recommended parameters and the actual injection molding experience. Table 2 shows the process parameters in the simulation. According to the principle of the orthogonal test, the orthogonal test table L16(45) was established. And the process parameters of 16 combinations in the table were analyzed by Moldflow software.
Li, K., Yan, S., Pan, W. & Zhao, G. Warpage optimization of fiber-reinforced composite injection molding by combining back propagation neural network and genetic algorithm. Int. J. Adv. Manuf. Technol. 90, 963–970. https://doi.org/10.1007/s00170-016-9409-3 (2017).
In a second-story conference room at US Merchant’s Beverly Hills, California, corporate headquarters, I’m seated across from Green at a glass-top table. I’ve just met the president and CEO of US Merchants, but his assessment of my aviation abilities is accurate. Nowadays, Green does know injection molding, and what he’s always known is retail, from sourcing, packaging and merchandising to shipping and logistics.
The above analysis showed that mean and range processing is an effective method to analyze and optimize single factors. However, these methods cannot be used simultaneously to optimize multiple objectives. In order to optimize the multi-objective data and carry out a comprehensive analysis to achieve the goal of this study, we introduced grey correlation analysis27.
Wu, H., Wang, Y., & Fang, M., Study on Injection molding process simulation and process parameter optimization of automobile instrument light guiding support. Adv. Mater. Sci. Eng. https://doi.org/10.1155/2021/9938094 (2021).
Introduced by Zeiger and Spark Industries at the PTXPO, the nozzle is designed for maximum heat transfer and uniformity with a continuous taper for self cleaning.
While prices moved up for three of the five commodity resins, there was potential for a flat trajectory for the rest of the third quarter.
Anovitz, L., Smith, B. Lifecycle Verification of Tank Liner Polymers; Oak Ridge National Lab. (ORNL): Oak Ridge, TN, USA, (2014). [CrossRef] storage vessel
Today, US Merchants operates seven facilities in California, with additional sites in Virginia, Texas, Canada and Arizona, as well as a planned expansion into the U.K. The company has standardized on LS Mtron injection molding machines, and it credits the Korean press maker and several other vendors with helping it transition from a molding newbie to an old plastics hand.
J.L and C.J.Z designed this study. J.L. did most of the laboratory analysis and wrote the first draft of the paper. S.H.M contributed to data interpretation and manuscript revision. F.L.J and S.Y.L participated in the experimental analysis and sample collection. J.G.L put forward constructive suggestions.
Ozcelik, B. Optimization of injection parameters for mechanical properties of specimens with weld line of polypropylene using Taguchi method. Int. Commun. Heat Mass Transf 38(8), 1067–1072 (2011).
Nowadays, many of those new requests make use of the company’s now extensive injection molding capabilities, including new sizes of totes and a line of molded plastic glassware. “If you ask me: have I ever made a drinking glass before — the answer would be no. Do I feel that the drinking glasses that we’re going to be coming out with are going to be exceptionally good and very well received? Absolutely.”
Mike Sepe has authored more than 25 ANTEC papers and more than 250 articles illustrating the importance of this interdisciplanary approach. In this collection, we present some of his best work during the years he has been contributing for Plastics Technology Magazine.
Learn about sustainable scrap reprocessing—this resource offers a deep dive into everything from granulator types and options, to service tips, videos and technical articles.
where \(\overline{{I_{{\text{j}}} }}\) —the average value of a certain experimental factor at a certain level ; \(\overline{Y}\)—Mean value of all test factors at all levels.
Lasn, K. & Echtermeyer, A. Safety approach for composite pressure vessels for roadtransport of hydrogen. Part 1 Acceptable probability of failure and hydrogend mass. Int. J. Hydrogen Energy 39(26), 1413e241 (2014).
\({\text{x}}_{{\text{i}}}^{*} (k)\) represents the gray relational values, max \({\text{x}}_{{\text{i}}}^{*} (k)\) and min \({\text{x}}_{{\text{i}}}^{*} (k)\) respectively represent the largest and the smallest values in the \({\text{x}}_{{\text{i}}}^{*} (k)\) sequence.
An important parameter considered in the design and manufacture of plastic parts is the parting surface (PS), which depends on the complexity of the parts and directly affects the design of the mold. One of the most time-consuming activities in mold design is to determine the parting surface14, which is mostly due to the fact that a variety of component geometry and pouring process-related elements must be taken into account when determining the parting surface. A reasonable parting surface helps simplify the mold structure and reduce costs15,16.
While the major correction in PP prices was finally underway, generally stable pricing was anticipated for the other four commodity resins.
“When you have to farm things out to third parties, you’re only asking for issues with delivery and excuses why something can’t be done.”
Mixed in among thought leaders from leading suppliers to injection molders and mold makers at the 2023 Molding and MoldMaking conferences will be molders and toolmakers themselves.
According to the injection molding results shown in Table 9, the influence degree of the process parameters on the grey correlation data is: holding time > mold temperature > cooling time > holding pressure > melt temperature.
Through the analysis of Table 5, a better process parameter group A1B2C3D3E4 can be obtained. When the melt temperature reaches 240 °C, the mold temperature reaches 80 °C, the holding pressure is 60 MPa, the holding time is 20 s, and the cooling time is 8 s. The optimum combination is not in the test times, the optimized molding process parameters are input into Moldflow software for analysis and verification. The final result is shown in Fig. 5. The volume shrinkage rate was 12.66%.
In order to visualize the influence of various factors on warpage deformation, a range analysis was introduced. The range is the difference between the maximum and minimum values of the average value of each parameter test result at different levels35. The larger the range value, the greater the impact of the coefficient on the index and the higher the impact on evaluation indicators.
Another guiding principle for Green and his wife, Marie, who is also his business partner since the tennis shop, is to use that reputation for attention to detail and quality to secure order commitments prior to taking on new jobs or new markets. “Our formula, my wife and mine, has not changed since we started our business with our little tennis store,” Green says. “We don’t really do anything unless we have a commitment. Typically, a customer of ours will come to us and say, ‘Can you make…?’”
Discover how artifical intelligence is revolutionizing plastics processing. Hear from industry experts on the future impact of AI on your operations and envision a fully interconnected plant.
The minimum characteristic warping value is set to Y1, and SNR is set to η1. The minimum volume shrinkage eigenvalue is set to Y2, the corresponding SNR value is η2, the minimum first residual stress is set to Y3, SNR is set to η3, the minimum second residual stress is set to Y4, and SNR is set to η4. The total SNR is as follows:
Join Engel in exploring the future of battery molding technology. Discover advancements in thermoplastic composites for battery housings, innovative automation solutions and the latest in large-tonnage equipment designed for e-mobility — all with a focus on cost-efficient solutions. Agenda: Learn about cutting-edge thermoplastic composites for durable, sustainable and cost-efficient battery housings Explore advanced automation concepts for efficient and scalable production See the latest large-tonnage equipment and technology innovations for e-mobility solutions
Analysis of residual stresses in the first direction is indicated in Table 3 and the analysis results are shown in Table 6.
At the end of the three rows of machines at the Ontario injection molding facility, some totes and other molded products are marked NCM (nonconforming materials) and will be scrapped. Khemlani notes NCM represents less than 1% of the company’s output, with the parts in question not meeting US Merchants rigid and rigorous standards, which are another core tenet of Green’s business philosophy.
“We don’t make mistakes because we’re trying to cut corners to make a larger margin. If I give you a better price, it’s coming out of my margin, never out of the quality of the product.”
Automation is a must-have for molders of pipettes. Make sure your supplier provides assurances of throughput and output, manpower utilization, floor space consumption and payback period.
After successfully introducing a combined conference for moldmakers and injection molders in 2022, Plastics Technology and MoldMaking Technology are once again joining forces for a tooling/molding two-for-one.
Li, J., Zhao, C., Jia, F. et al. Optimization of injection molding process parameters for the lining of IV hydrogen storage cylinder. Sci Rep 13, 665 (2023). https://doi.org/10.1038/s41598-023-27848-1
The Plastics Industry Association (PLASTICS) has released final figures for NPE2024: The Plastics Show (May 6-10; Orlando) that officially make it the largest ever NPE in several key metrics.
Different from the orthogonal experiments, Taguchi algorithm introduces the concept of SNR on the basis of orthogonal experiments. In Taguchi algorithm, the index of measuring test results is no longer a certain analysis data. Instead, the analysis is converted into an SNR28.
Plastics Technology’s Tech Days is back! Every Tuesday in October, a series of five online presentations will be given by industry supplier around the following topics: Injection Molding — New Technologies, Efficiencies Film Extrusion — New Technologies, Efficiencies Upstream/Downstream Operations Injection Molding — Sustainability Extrusion — Compounding Coming out of NPE2024, PT identified a variety of topics, technologies and trends that are driving and shaping the evolution of plastic products manufacturing — from recycling/recyclability and energy optimization to AI-based process control and automation implementation. PT Tech Days is designed to provide a robust, curated, accessible platform through which plastics professionals can explore these trends, have direct access to subject-matter experts and develop strategies for applying solutions in their operations.
Shen, Y.-K. et al. Analysis for optimal gate design of thin-walled injection molding. Int. Commun. Heat Mass Transf. 35, 728–734 (2008).
While prices moved up for three of the five commodity resins, there was potential for a flat trajectory for the rest of the third quarter.
This research is supported by the National Natural Science Foundation of China (Grant number 52075361), the Major Science and Technology Project of Shanxi Province (Grant number 20201102003) and the Key Research and Development Projects in Shanxi province (Grant number 201903D421030).
The analysis in Table 12 shows that melt temperature is the most important factor affecting the four analyzed parameters. Compared with the other four factors, the influence of melt temperature on the four factors is 62.15%, accounting for the leading role, while the influence of holding pressure on the four factors is 4.15% (Supplementary file). The effect of mold temperature, holding time and cooling time on the four factors are 6.40%, 12.82% and 12.48%, respectively. The order of four factors is melt temperature > holding time > cooling time > mold temperature > holding pressure.
In the hallway leading to the conference room, the walls are decorated with two of Green’s formidable collections: sports memorabilia and patents for his packaging and product display concepts that are now ubiquitous at retailers, including the warehouse club stores that he grew alongside starting in the 1980s.
Specifically, Green and US Merchants credit Shingo Hirate, president of equipment distributor Hirate America Inc., Anaheim, California, with helping the company understand what would be needed to get started in injection molding. Green and Larry Khemlani, US Merchants VP of Operations, met Hirate while walking a plastics trade show, and Hirate’s willingness to get into the nuts and bolts of starting a molding business from scratch won him a new and prodigious customer. US Merchants would order four full molding machine cells from Hirate shortly thereafter and then another three in quick succession.
Researchers have used a variety of optimization techniques in injection molding over the last few decades to lower various defect rates. Researchers used the experimental design (DOE) approach to perform a pilot thorough investigation of the injection molding process since warpage and shrinkage are two major injection molding defects. For warpage and shrinkage prediction, the neural network method is used to significantly reduce the defect rate21,22. The neural network has become a powerful and practical method for modeling highly complex nonlinear systems. In order to determine the optimum level of design parameters, a genetic algorithm is applied to the optimization of injection molding parameters of plastic parts23,24. Taguchi, another method for improving the quality of injection molded parts, is a robust parameter design technology, and shrinkage optimization plays a major role in determining the final size of injection molded parts. This method also determines the optimal level of each process parameter to reduce shrinkage and warpage in thin-walled products25,26. ANOVA (analysis of variance) and SNR (signal-to-noise ratio) are used for data analysis to determine the importance of factors, provide the initial optimal combination of process parameters, and obtain the contribution percentage of quantitative factors27,28. Grey correlation analysis is usually used in data processing of Taguchi orthogonal test to transform a multi-objective problem into a single-objective problem, which is beneficial for analyzing comprehensive data from tests29,30.
Multiple speakers at Molding 2023 will address the ways simulation can impact material substitution decisions, process profitability and simplification of mold design.
GETTING A QUOTE WITH LK-MOULD IS FREE AND SIMPLE.
FIND MORE OF OUR SERVICES:
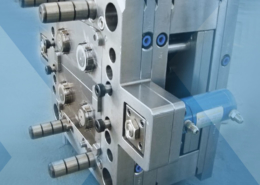
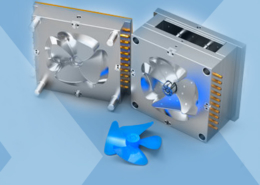
Plastic Molding

Rapid Prototyping
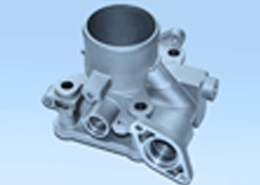
Pressure Die Casting
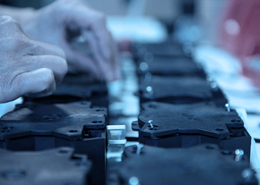
Parts Assembly
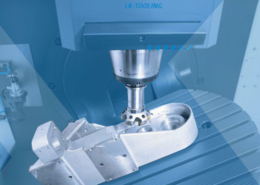