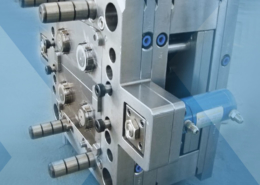
What drives the success of an industry: chance or strategy? Lessons from
Author:gly Date: 2024-09-30
Given the prevalence of injection molding, knowledge about this process could give these students a clear advantage in a wide variety of design careers. But the most satisfying outcome of this class, for both students and instructors, is probably the hard-won success can be shared directly with classmates, friends and family.
Two UK contract moulders – Merriott Plastics and Talisman – have just combined to create a multi-site, multi-competence business.
Andrew Lawrence remarked that the company is excited to be bringing together the wealth of expertise and knowledge that exists within its businesses, thus creating a formidable team.
In the design classes that students take before Making Multiples, they are free to make just about anything they want, exploring many media and a wide range of techniques. Making Multiples focuses on a single medium and technique while urging students to give their projects the utmost forethought in order to experience what it’s like to mass-produce an object they created from start to finish.
Indeed, Merriott Talisman customers in primary group markets such as automotive, electrical, defence and air and fluid movement can now look forward to the many benefits that will flow from the new business which is expected to turnover in excess of £15m sales this year.
Huynh’s own work tested the line between parts that could be copied a few times and those that could be duplicated in the dozens. His original plan was to make a fountain pen, decorated with intricate ribs. After designing the fragile and delicate mold components this piece would require, he realized making many wasn’t feasible. He changed course, instead creating a screwdriver with a design inspired by his original project.
“Having the chance to make more than one of something gives students experience that might be useful to them in their career but also is really incredible to create one of something – one mold – and then get to share your design with all of your friends,” Kohn said. “I think that’s a very empowering experience for students because they realize that they can make something that can be out in the world as a real object.”
The newly expanded company will provide customers - particularly in the Midlands, South West and South East - with improved and local product development, manufacture, logistics and technical support.
Changing times, however, require a dynamic response to business that builds on tradition: Shaun Champion Talisman Plastics managing director notes that ‘growth at Talisman in the last 5 years has seen us doubling our turnover and making major investments in people and equipment. This merger enables that rate of growth to continue – providing ‘win-win’ for us - but also great things for our customers, current and future.’
“In the real world, I’m not going to be designing my own mold and I’m not going to be cutting my own mold. But I am going to be designing my own parts, and if I don’t know what constraints there are around it, I’m not going to end up designing a very good part,” Stavisky said.
We want to provide announcements, events, leadership messages and resources that are relevant to you. Your selection is stored in a browser cookie which you can remove at any time using “Clear all personalization” below.
The new grouping will be led by Shaun Champion of Talisman and Andrew Lawrence, Merriott Plastics. Lawrence said: "We are truly delighted to announce this historic merger; bringing both these industry names together in the service of our customers and for UK manufacturing - while also honouring the legacy tradition that has brought us together."
In an advanced design and manufacturing course, students learn that the ubiquitous plastic objects made by injection molding are deceptively hard to make.
That legacy tradition is considerable: Talisman (known as LGG Charlesworth until 2018) is more than one hundred years old while Merriott Mouldings began production in the village of Merriott, Somerset in 1938 and ICM in Rochester, Kent in 1947. Each company is a member of the British Plastics Federation and has contributed greatly to the growth and culture of UK Plastics plc.
In each case, students sketched prototypes, printed them with a 3-D printer, machined the aluminum molds and injected the molds with molten plastic of their chosen flexibility and color to create final products.
Champion added: "Throughout the new company our key focus will always be about doing the right thing for our customers. Andrew and I therefore encourage all to call up, get in touch and put this commitment to the test. We are also exhibiting at Plastics Live 2024, Coventry Arena, June 12-13, 2024 so please make a date to visit our stand then."
Plastic objects made by injection molding are abundant and, for many of us, a constant presence in our everyday lives. Your phone case, toothbrush and the keys on your computer are all probably the result of mass production, which involves injecting molten plastic into molds.
Once students in ME325 have completed the design and manufacture of their molds, each individual part might take only 30 seconds to mold. This speed of production belies the challenges and amount of the time that went into designing the part and creating the tooling.
Each student devises a product that is interesting or useful enough to benefit from being highly reproducible. The results in winter quarter were diverse: an insulin vial protector, a screwdriver with interchangeable magnetic heads, a portable spring that makes it easier to use chopsticks, a necklace organizer and a shoe tag that a person can slide onto laces to add some flair to footwear.
“In other classes at the Product Realization Lab, you only make one part and you could polish it for hours,” said Brian Huynh, a master’s student in mechanical engineering. “But in the real world you’re going to be making hundreds of thousands or millions. So there’s debugging that goes with making your mold, and then there’s the injection-molding process, which makes you realize, I have to make it look good enough – just good enough – where, if I make a hundred of them, most of them look great.”
“Having the chance to actually try it, to go beyond the theory and make something, is really critical to understanding what it takes to manufacture these parts,” said Marlo Kohn, lecturer in mechanical engineering and instructor for the course.
Those products are ubiquitous, but deceptively hard to make, students learn in the engineering class ME325: Making Multiples: Scaled Manufacturing Tooling. In it, students design and make molds for their own mass-produced parts.
“When my first parts came out, I said, ‘Man, this looks so simple!’ But so much work and thought went into the mold and it was quite complicated to make,” said Katya Stavisky, a master’s student in mechanical engineering who made the shoelace tags last quarter. “Now, looking around at things, like the tools we use, I think, ‘Wow, the tooling for this must have been really difficult.’”
The joint technical moulding capacity from both companies provides machinery capability from 25 to 1,100 tonnes, including injection, compression and composite moulding services for products weighing from 5 grams to 10 kg.
While other classes tend to focus on the manufacturing process itself, this course is about designing to fit the manufacturing process, Huynh said. It’s a set of lessons fraught with complications that foster flexibility. The payoff, however, has more impact than the physical products suggest.
GETTING A QUOTE WITH LK-MOULD IS FREE AND SIMPLE.
FIND MORE OF OUR SERVICES:
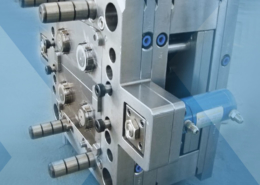
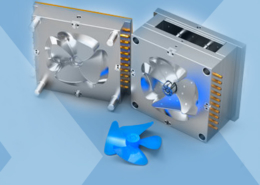
Plastic Molding

Rapid Prototyping
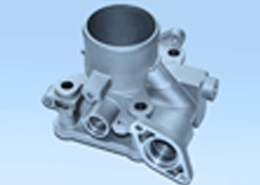
Pressure Die Casting
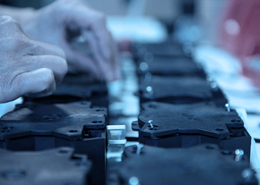
Parts Assembly
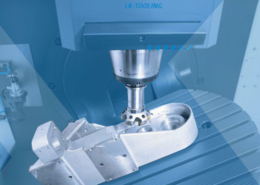