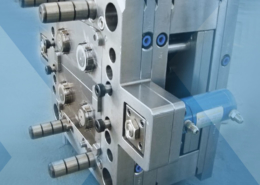
What drives the success of an industry: chance or strategy? Lessons from
Author:gly Date: 2024-09-30
Another area of debate in the injection moulding world is robot integration. The UK seriously lags behind other developed countries for its number of robot installations. That’s not just for the world of injection moulding, but in the UK manufacturing sphere more widely. In fact, the International Federation of Robotics (IFR) reports that the UK has just 101 robots per 10,000 employees — rookie numbers compared to competitors in the US, China and Germany.
Projecting a double-digit increase in sales, Plastic Molding Technology has invested close to $1 million in new injection molding and auxiliary equipment this year.
PMT has taken delivery of 10 new Maruka USA Toyo injection molding machines so far this year, including three 55-ton, four 110-ton, and two 200-ton presses. PMT also invested in its first injection molding machine under 40 tons, with a new Toyo 20-ton horizontal machine. The new investments will support key customers in the telecommunications, medical device, and electrical industries.
That proverbial rising tide that lifts all boats? Contract manufacturer Plastic Molding Technology (PMT) is riding that wave. The company announced today that it has invested close to $1 million in new equipment this year to support new contract awards that will require additional capacity.
The flagship all-electric range from TM Robotics is the SXIII all-electric series from Shibaura Machine. Shibaura Machine is the new name for Toshiba Machine — the Japanese manufacturer of industrial robots and injection mould machines. The SXIII range boasts faster injection speeds, enhanced sustainability and a streamlined design when compared to its hydraulic predecessors. What’s more, despite the perception of higher costs for all-electric machines, this range can improve cost efficiency by lowering the cost-per-part.
PMT also procured auxiliary equipment for the new presses, including several HY Robotics 3-axis robots and sprue pickers, Novatec dryers with central conveying systems, and conveyors with part separation. Two new Gorbel overhead crane systems will provide safe mold transport and set-up in the company’s white room space and on the plant floor.
Nigel Smith, managing director of TM Robotics, the international distribution partner of Shibaura Machine and the UK and Ireland distributor of its injection mould machines, explores the changing landscape of plastic's injection moulding sector and argues the case for investment in new technologies, both for better operational efficiency and improved sustainability.
PMT now has a total of 72 injection molding machines in its 60,000-square-foot manufacturing facility, and operates 24/7 in its strategic border location in El Paso, TX.
Due to this lack of uptake, the UK industry is missing some of the potential benefits of industrial robots, including improved productivity, efficiency and throughput. As a primary distributor of Shibaura Machine robots in the UK, the TM Robotics team has spotted opportunities for the injection moulding sector to reap the rewards of robotic automation.
There are over 5,800 companies operating in the UK plastics industry, contributing £25 billion to our economy each year. As a key player in Britain’s manufacturing sector, injection mould shops must embrace technological advancements in injection moulding machinery and accompanying automation for improved profit, productivity and sustainability.
The injection moulding process is responsible for up to 90 per cent of the Global Warming Potential (GWP) in the entire mould lifecycle. Recognising this, TM Robotics has championed investment in all-electric injection mould machines to replace older, more energy-intensive models.
Injection moulding applications have long played a key part in the UK’s manufacturing industry, producing everything from medical components, automotive parts, food containers, packaging items and much more. Traditionally, our manufacturers have relied on hydraulic-powered injection moulding machines in their operations. However, the industry is now at a crossroads, faced with the imperative to embrace technological advancements for sustainability and cost-effectiveness.
The most obvious application for robots in mould machine shops is for the loading and unloading of injection mould machines. However, many end users currently have relatively low robotic ability, having traditionally chosen Cartesian X-Y gantry style robots to unload injection moulding machines.
This was demonstrated by TM Robotics’ customer Lotan, a manufacturer of plastic containers based in Leicestershire, UK. Lotan’s production facility exclusively uses all-electric injection mould machines from Shibaura Machine. The SXIII provides significantly faster injection speeds than traditional moulding equipment, providing 35% faster cycle times than conventional hydraulic servo IMMs.
One notable observation is the prevalence of hydraulic legacy equipment that is still being used by UK manufacturers. The TM Robotics’ injection moulding servicing department has witnessed this first-hand and regularly visits manufacturing sites to service and maintain Shibaura Machine’s own hydraulic injection mould machines — some of which have been in action for up to three decades. On one hand, it is a testament to the resilience of these machines, but the industry must consider the environmental downsides of this ageing equipment.
“Several of our customers are experiencing record growth within their respective industries to support infrastructure in the USA,” said PMT CEO and owner Charles A. Sholtis in a prepared statement. For its part, PMT is projecting a double-digit increase in sales this year. It’s putting that extra money to good use by investing in new injection molding machines and auxiliary equipment that will, in turn, support booming customer demand.
GETTING A QUOTE WITH LK-MOULD IS FREE AND SIMPLE.
FIND MORE OF OUR SERVICES:
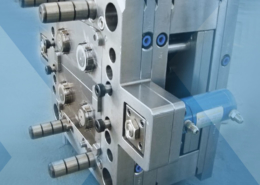
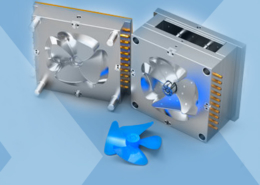
Plastic Molding

Rapid Prototyping
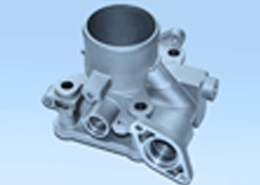
Pressure Die Casting
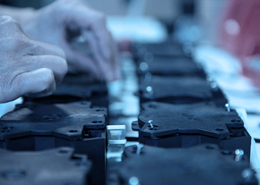
Parts Assembly
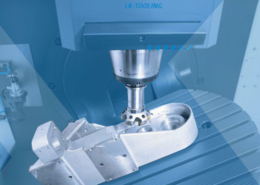