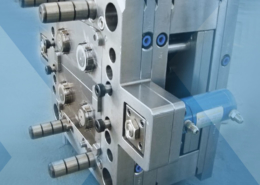
What Crocs are made of — and how they're changing - rubber plastic molding
Author:gly Date: 2024-09-30
“Shapeways’ readiness to embrace and invest in emerging technologies and processes, tailoring solutions to meet our customers’ unique needs and requirements, sets the company apart,” said John Tenbusch, Sales Director, Automotive Vertical for Shapeways. “This commitment sends a clear signal to our partners that we’re more than a supplier – we’re a true partner sharing in their vision for the production of quality, high-performance parts.”
Sabic PP-UMS foam resin is a new-generation, long-chain branched PP material with a melt strength greater than 65 cN to enable very low foam densities (20 to 200 kg/m3). It offers a broad processing window using various methods — foam extrusion, foam injection molding, foam blow molding, particle foaming, and foam blown and cast film. Sabic supports its materials with the resources of the Foam Innovation Center in the Netherlands. The center provides leading-edge technologies and a platform for collaboration with customers and organizations across the foam industry value chain.
Sabic PP-UMS foam resin’s processing versatility allows PP foams, subject to user testing, to be used in structural cores for sandwich panels in delivery vans, trucks, and recreational vehicles (RVs), and to provide structural and insulative properties in blow-molded air ducts. Examples of these applications, on display at the Sabic booth, illustrate the suitability of this foam resin for broad use in transportation components that can benefit from significant weight reduction and potential cost optimization.
While you’re here, why not subscribe to our Youtube channel? Featuring discussion, debriefs, video shorts, and webinar replays.
Besides weight savings and recyclability, this air duct offers additional functionality, including insulation properties that can save energy and help extend the range of electrical vehicles. This inherent insulative capability and smart design help manufacturers avoid the need to add insulation to the part. The results are additional savings on weight and cost (labor and material).
Sabic is spotlighting two diverse transportation applications that demonstrate the potential benefits of Sabic PP-UMS (Polypropylene – Ultra Melt Strength) foam resin at NPE2024 (Booth S19005). The material features high melt strength for high levels of foamability and enables the extrusion of PP foams with very low density, good impact resistance, and compliance with VDA 278 emission regulations.
Sabic is exhibiting two transportation applications at NPE that demonstrate the lightweighting, processing, and sustainability features of its PP-UMS foam resin.
Another advantage of the PP-UMS foam resin–based panel is its impact resistance. In addition, panels using the Sabic foam resin can be repaired easily if damaged and are durable because the foam resin does not react with water.
With a background in journalism, Ada has a keen interest in frontier technology and its application in the wider world. Ada reports on aspects of 3D printing ranging from aerospace and automotive to medical and dental.
The recently acquired contracts for Shapeways are in support of long-term production programs, which are anticipated to generate over $2.8 million in annual revenue for the next seven years. This move serves as evidence of Shapeways’ dedication and expertise in collaborating with Tier 1 manufacturers to facilitate high-volume production for original equipment manufacturers (OEMs), says the company.
Prototyping company Quickparts announced the introduction of a service that offered shipping as fast as same-day delivery. This achievement was made possible by leveraging novel manufacturing technologies, such as Nexa3D‘s high-speed resin 3D printers featuring Lubricant Sublayer Photo-curing (LSPc) technology. Quickparts also incorporated advanced injection molding technologies and CNC to enhance its service offerings. Ziad Abou, CEO of Quickparts said, “We are excited to bring our customers the speed and quality they need to meet today’s market demands.”
3D printing service provider Shapeways has announced the growth of its Enterprise Manufacturing Solutions division. It has been awarded contracts from two Tier 1 suppliers in the automotive and transportation industries, signaling substantial growth for the company.
“Our emphasis on relationship building and responsiveness to customer needs has been the key to our success in these projects,” said Aidan O’Sullivan, General Manager of Enterprise Solutions for Shapeways. “The trust we build with our customers, through measures like sending our experts to visit their sites, ensures alignment and open communication, driving productive partnerships.”
The PP foam produced with Sabic PP-UMS foam resin can function as a strong, insulative core material for sandwich panels in trucks, delivery vans, and RVs, replacing metal, wood, and competitive foams. Panels with PP foam cores produced from Sabic PP-UMS resin can reduce weight and help lower carbon dioxide emissions.
The second Tier 1 contract was awarded by a leading global automotive OEM. Under the terms of the contract, Shapeways will be responsible for manufacturing interior paneling and trim for a specific line of medium-duty trucks. The decision to award the contract was driven by several key factors, including the supplier’s demonstrated commitment to obtaining the required equipment and its capacity to meet the production requirements, and strict deadlines associated with the production of injection-molded parts.
Blow-molded PP foam produced with Sabic PP-UMS foam resin can be used in automotive air ducts to help reduce weight and simplify the mounting process in the vehicle. The foam resin creates a mono-material part for easy recycling in existing waste systems. An air duct, approximately 60 inches long (pictured at the top of this article), is in commercial use and can be viewed at the Sabic booth.
Stephen has been with PlasticsToday and its preceding publications Modern Plastics and Injection Molding since 1992, throughout this time based in the Asia Pacific region, including stints in Japan, Australia, and his current location Singapore. His current beat focuses on automotive. Stephen is an avid folding bicycle rider, often taking his bike on overseas business trips, and a proud dachshund owner.
To stay up to date with the latest 3D printing news, don’t forget to subscribe to the 3D Printing Industry newsletter or follow us on Twitter, or like our page on Facebook.
A sample composite PP sandwich panel from an RV floor, comprised of a glass fiber–reinforced PP face sheet and foam core, is on display at the Sabic booth.
“This distinctive foam resin with exceptional melt strength enables the extrusion of PP foam with very low density, which can help the transportation industry advance lightweighting goals by replacing heavier material combinations ranging from metal and wood to solid polymers,” said Amanda Roble, director, Advanced Consumer Solutions. “But Sabic PP-UMS foam resin does even more. Its purity and cleanliness address the most stringent automotive emission regulations, while its processing flexibility and blendability make it adaptable to many different applications. We look forward to working with the transportation value chain to develop new and innovative foam solutions.”
The first Tier 1 supplier contract was awarded by a major commercial trucking OEM to assume responsibility for producing injection-molded cab trim components. Regardless of possessing similar in-house capabilities, the OEM encountered capacity challenges, prompting it to select Shapeways to address its production needs.
Are you looking for a job in the additive manufacturing industry? Visit 3D Printing Jobs for a selection of roles in the industry.
San Francisco-based manufacturing bureau Fictiv incorporated 3D visualization into its injection molding Design for Manufacturability (DFM) system. Fictiv claimed that its Digital Manufacturing Ecosystem delivered high-quality parts at unprecedented speed. According to the company, this improved software enabled complete automation of injection molding workflows, allowing clients to expedite new product design and reduce manufacturing risks and delays. The enhanced system integrated digital manufacturability issue tracking, part version control, and communication tools. The utilization of 3D visualization also significantly sped up the process of requesting, assessing, and reacting to injection molding DFM input by engineering teams and approving parts for production.
Structural cores for sandwich panels in delivery vans, trucks, and recreational vehicles can be made from Sabic PP-UMS foam resin. Image courtesy of Sabic.
The Sabic foam resin is typically combined with other PP materials to produce the foam core. Adding a glass fiber–reinforced PP face sheet results in a mono-material part that is easier to recycle than a mix of material types. Furthermore, foam produced with Sabic PP-UMS foam resin can be thermally bonded to the PP face sheet, avoiding the need for adhesives.
GETTING A QUOTE WITH LK-MOULD IS FREE AND SIMPLE.
FIND MORE OF OUR SERVICES:
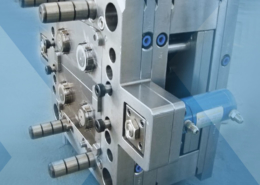
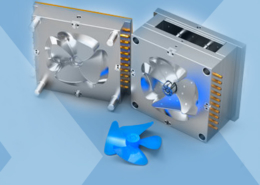
Plastic Molding

Rapid Prototyping
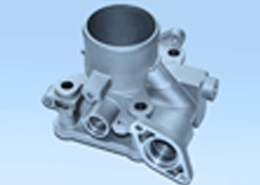
Pressure Die Casting
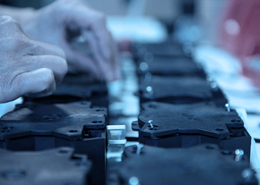
Parts Assembly
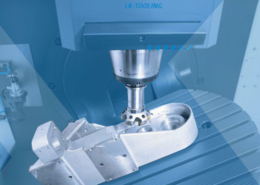