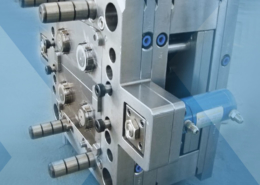
Two shot moulding, also known as dual-shot injection molding or multi-material i
Author:gly Date: 2024-06-08
Overview
Two shot moulding involves injecting two different materials into a single mold in two separate cycles. The first material is injected to form the base or substrate of the part, while the second material is injected to create specific features or details. This process eliminates the need for secondary operations like assembly or bonding, resulting in faster production times and reduced manufacturing costs.
Process Sequence
The process typically begins with the injection of the first material into the mold cavity, followed by a short cooling period. Then, the mold opens slightly to allow the second material to be injected into the same cavity, forming the desired features. Finally, the mold closes completely, and both materials are bonded together to create the final part.
Materials Compatibility
Two shot moulding offers versatility in material selection, allowing manufacturers to combine a wide range of thermoplastics with different properties. Common combinations include hard-soft, soft-soft, and rigid-flexible materials, enabling the production of parts with varying textures, colors, and mechanical properties.
Design Considerations
Designing for two shot moulding requires careful consideration of part geometry, material compatibility, and tooling design. Complex part designs with intricate features can be achieved, but proper gating, venting, and parting line placement are essential to ensure uniform material distribution and minimize defects.
Applications
Two shot moulding finds applications across diverse industries, including automotive, electronics, medical, consumer goods, and packaging.
Automotive Industry
In the automotive sector, two shot moulding is used to produce interior and exterior components such as instrument panels, door handles, and buttons. The ability to integrate multiple materials and colors in one part enhances aesthetics and functionality while reducing assembly costs.
Electronics
In electronics manufacturing, two shot moulding is employed to produce housings, keypads, and connectors with integrated seals and gaskets. This process ensures hermetic sealing, protection against moisture and dust, and improved durability in harsh operating environments.
Medical Devices
In the medical industry, two shot moulding is utilized to manufacture surgical instruments, drug delivery devices, and wearable sensors with biocompatible materials. The seamless integration of multiple materials facilitates the production of complex medical devices with superior performance and patient comfort.
Advantages and Challenges
Advantages
Cost Efficiency
: Eliminates the need for secondary operations, reducing labor and assembly costs.
Enhanced Product Quality
: Minimizes part defects, flash, and warpage, resulting in higher-quality components.
Design Freedom
: Enables the production of intricate designs and overmolded parts with improved aesthetics and functionality.
Challenges
Tooling Complexity
: Requires specialized tooling and equipment for precise material placement and bonding.
Material Compatibility
: Selection of compatible materials is crucial to ensure proper adhesion and mechanical properties.
Process Optimization
: Fine-tuning process parameters is necessary to achieve consistent part quality and cycle times.
Conclusion
Two shot moulding offers manufacturers a versatile and efficient solution for producing complex parts with multiple materials or colors. Despite its challenges, this advanced manufacturing process continues to drive innovation across various industries, enhancing product performance, aesthetics, and cost-effectiveness. As technology advances and materials science evolves, further research and development in two shot moulding hold the potential to unlock new opportunities and applications, shaping the future of manufacturing.
GETTING A QUOTE WITH LK-MOULD IS FREE AND SIMPLE.
FIND MORE OF OUR SERVICES:
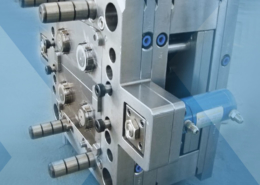
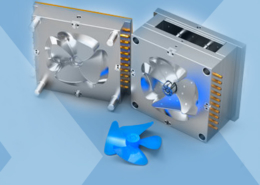
Plastic Molding

Rapid Prototyping
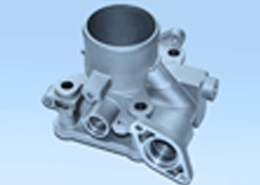
Pressure Die Casting
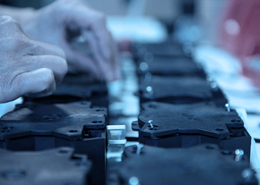
Parts Assembly
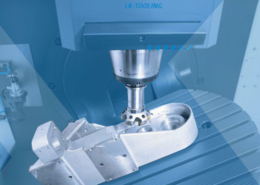