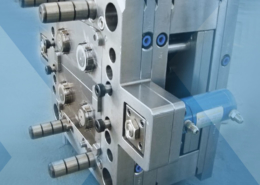
Warhammer molds cost Games Workshop over $8 million last year - plastic mold pri
Author:gly Date: 2024-09-30
Nexus also developed the ServoMix X20 LSR dosing system, which ensures air-free dosing, even in very small quantities, of the liquid silicone rubber. Networking via OPC UA and MES authentig by TIG ensures full process data monitoring and complete traceability down to the individual cavity level.
BASF SE’s Catamold® feedstock is synonymous with the high volume production of components by Metal Injection Moulding and the product’s launch, more than thirty years ago, was the catalyst for the industry’s global growth.
The process data of the dosing unit are available during production in the CC300 control system of the injection molding machine and can be used for even more precise process monitoring and continuous optimization. The dosing parameters are stored in the mold's part data record, making them immediately available at the machine control when the mold is set up again.
The following years of Powder Injection Moulding International magazine are available to download in PDF format, free of charge, from our archive.
It is the latter that has driven such dramatic growth in the global MIM industry over the last decade. For those who are just at the point of discovering this technology, Matt Bulger reveals the ten key rules for MIM success, as observed in his nearly three decades as a developer and manufacturer of MIM components.
Extensive MIM, CIM industry and sinter-based AM industry news, plus the following exclusive deep-dive articles and reports:
Developing a component for a new manufacturing process can be a daunting prospect. It is in any business’s nature to be cautious of change and to minimise risk; however, any successful business must also recognise when an opportunity is too good to ignore.
In this study, Martin Kearns and colleagues from Sandvik Osprey review the sintering behaviour of popular tool steels such as D2 and M2, and present fresh data on a range of other tool steels, some made via both prealloy and master alloy routes. Materials investigated include AISI8620 and tool steels H11, H13, S7 and high carbon, high speed steel, T15, all sintered in nitrogen.
Production of the 7-mm-diameter blades is fully automated in a 64-cavity mold with an Engel easix articulated robot and integrated vision control system.
Nexus designed the 64-cavity mould with a demolding device to enable the end-of-arm tooling to easily grip parts. To ensure precise fill control, the cold runners in the mold are equipped with electric needle shut-off systems. Nexus’ Timeshot technology controls the fill quantity as a function of injection time. Each cavity can be controlled individually, even in molds with up to 128 cavities.
MIM is a natural choice of fabrication method for complex parts in materials that are difficult to machine. Tool steels are one such class of material with significant potential applications growth, both for the MIM industry and for MIM-like Additive Manufacturing processes.
Earlier this summer PIM industry leaders from around the world came together in Lossburg, Germany, for Arburg GmbH + Co KG’s second International PIM conference.
Blade valves are used in a range of applications, from automotive to medical technology, and in all cases the injection molding process must meet strict consistency parameters. At K 2022, Engel and partner company Nexus Elastomer Systems will demo a fully automated production cell molding liquid silicone rubber (LSR) blade valves that achieves consistent quality in a cost-effective manner.
Reach a truly international audience that includes component manufacturers, end-users, industry suppliers, analysts, researchers and more.
Engel’s iQ weight control smart assistance system continuously analyzes the injection profile and readjusts quality-relevant process parameters in the same cycle whenever deviations occur.
The free-to-access PIM International magazine archive offers unparalleled insight into the world of MIM, CIM and sinter-based AM from a commercial and technological perspective through:
Discover suppliers of these and more in our advertisers’ index and buyer’s guide, available in the back of PIM International.
The 116-page September 2018 issue of Powder Injection Moulding International (Vol. 12 No. 3) features 60 pages of industry news, plus the following articles and technical reviews:
The easix articulated robot requires little headroom and connects the injection molding machine with camera-based quality control and the discharge station. Additional process units can be added retroactively, integrated upstream or downstream of the injection molding process.
This marks the first time that Engel is demonstrating a networked injection molding machine and LSR dosing unit via OPC UA in line with the Euromap 82.3 standard at a trade show.
Because of the tie-bar-less design, multi-cavity molds may be used on smaller injection molding machines than is customary, providing cost savings without affecting productivity per unit of area, according to Engel.
Incorporating tie-bar-less servo-hydraulic clamping and electric injection units, the e-victory model machine on display supports low-flash, rework-free processing of low-viscosity materials. The moving platen precisely follows the mold as the clamp force builds up, resulting in optimal platen parallelism, said Engel. Patented force dividers ensure that the clamping force is distributed evenly over the entire platen face. Even in large multi-cavity molds, the same clamping force is applied to cavities near the outer edge of the platen as those near the centre.
A number of the papers presented during the technical sessions at the POWDERMET2018 conference, organised by the Metal Powder Industries Federation (MPIF) and held in San Antonio, Texas, June 17-20, 2018, addressed issues related to achievable properties and the influence of feedstock characteristics on the processing of Powder Injection Moulded products.
Don't miss any new issue of PIM International, and stay up to date with the latest industry news. Sign up to our fortnightly newsletter.
At stand C58 in hall 15 an e-victory injection molding machine with smart digital assistance supported by Nexus’ mold and plasticizing technology will produce LSR blade valves measuring 7-mm in diameter. Production is fully automated in a 64-cavity mold with an Engel easix articulated robot and integrated vision control system.
Today, BASF has adapted this technology for metal Additive Manufacturing via Fused Filament Fabrication (FFF). This technology offers the company’s existing MIM customers a low-investment route into metal AM, whether for prototyping or the development of entirely new applications.
The event, which took place five years after the company’s inaugural PIM conference, had the goal of exploring the future of metal and ceramic injection moulding through two days of presentations by parts manufacturers, materials suppliers, equipment producers and researchers. Dr Georg Schlieper reports on the event for PIM International.
GETTING A QUOTE WITH LK-MOULD IS FREE AND SIMPLE.
FIND MORE OF OUR SERVICES:
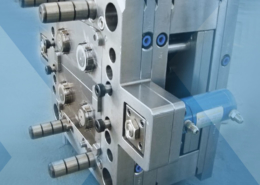
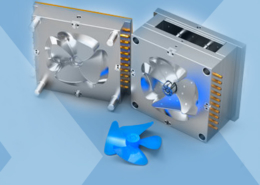
Plastic Molding

Rapid Prototyping
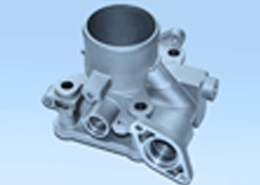
Pressure Die Casting
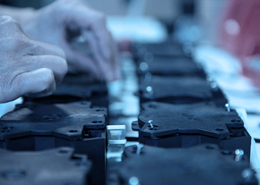
Parts Assembly
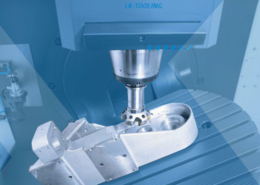