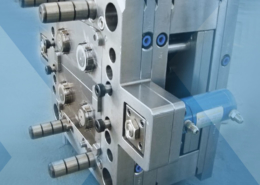
VRC Engineered Solutions to close Classic Molding - plastic injection molding se
Author:gly Date: 2024-09-30
Special shipping and ground transportation arrangements were needed to move the machine from Austria to the United States and even within Austria. The platens were transported to and from the St. Valentin manufacturing facility along the Danube River on barges. “Each machine was fully assembled and tested prior to shipping and then disassembled to be shipped to the United States,” said Jim Moran, business development manager at Engel North America.
German chemicals company Evonik and Swiss plastics processor Samaplast have collaborated in the development of an osteo-conductive PEEK-based material compatible with injection molding. Spinal implant prototypes have been molded to illustrate the processing properties of the new high-performance polymer, VESTAKEEP Fusion.
Getting the 8,000-ton machines from Austria to the Infiltrator Water Technologies plant in Kentucky was a logistical challenge.
The duo injection molding machines each have two 85,000 cm³ injection units, which allow for injecting a total shot weight of 270 lb (122 kg). Despite the clamping force and shot size, the machines have a relatively small footprint — 96 ft. (29.3 meters) long and 37 ft. (6.4 meters) wide — enabled by Engel’s two-platen design.
Engel was recently awarded a gold sustainability rating by EcoVadis, which relies on data from more than 90,000 evaluated companies and global supply chains to rank companies.
To demonstrate the medical potential of the technology, Evonik and Samaplast have produced prototypes of intervertebral implants, known as cages or spacers, which are used to fill the disc space in the spine following its removal due to disc degeneration. "We have produced a cage that contains all the details, such as serrations, threads, and apertures, that are relevant for spinal implants," explained Okle.
Two injection molding machines with a clamping force of 8,000 tons each have now been delivered by Austrian injection molding machine maker Engel to the Infiltrator Water Technologies (IWT) plant in Winchester, KY. IWT took delivery of the first Engel duo 130000/130000H/8200 combi US machine, the largest machine ever built at Engel’s St. Valentin facility in Austria, in February of last year. A second machine, a replica of the first, arrived at the facility this month. IWT, a subsidiary of Advanced Drainage Systems (ADS), produces water management products.
Thanks to the design freedom afforded by injection molding, VESTAKEEP Fusion–based cages can be tailored to patient-specific anatomies and different surgical techniques. The cage models show the design diversity in the interlocks and in the cavities for ossification. In addition, the design facilitates instrument guidance during surgery and enables minimally invasive, patient-friendly surgical techniques.
At the IWT site in Winchester, new manufacturing facilities had to be built to house the large machines. As 29 truckloads of machine parts were arriving from Austria, the 59,000-square-foot building expansion went forward. A 150-ton overhead crane was installed to move molds in and out of the machine and was also used to help assemble the new press.
Engel said it received the purchase order in November 2020 and completed handover of the first machine in February 2022. The second machine, a replica of the first, was delivered this month.
"We tested VESTAKEEP Fusion on injection molding machines in the cleanroom and found that it was very easy to process," said Samaplast CEO Stefan Okle in a prepared statement. "Thanks to the excellent exchange with Evonik, we were able to produce a prototype within 10 days." Previously, tool development alone had taken eight to 10 weeks. With rapid prototyping, this process can be shortened considerably.
A collaboration between Evonik and Swiss plastics processor Samaplast results in an alternative to titanium, stainless steel, and cobalt-chromium implants.
With VESTAKEEP Fusion, Evonik is introducing a new product line of next-generation PEEK-based implant materials that accelerate bone fusion and convalescence. In vitro studies document a more than 30% increase in cell attachment and cell proliferation, according to Evonik. In preclinical tests, histological examination reveals a dense network of newly formed osteoblasts at the bone-implant interface. Bone histo-morphometry shows an approximately twofold increase in bone apposition. Moreover, pull-out tests demonstrate a more than twofold increase in implant fixation, said the company.
Until now, it has been virtually impossible to manufacture implants from polymer compounds with bioactive particles by injection molding, because a thin polymer layer usually forms on the surface, preventing the implant from growing in, explained Evonik in a press release. VESTAKEEP Fusion's specially configured microparticles and their homogeneous distribution, however, allow the formation of functional biphasic calcium phosphate (BCP) additives on the surface of injection-molded components. The additives allow bone cells to adhere to the implant more quickly and promote osteo-integration between the bone and implant.
"Implant manufacturers were missing a PEEK material that fuses with bone cells and, thus, accelerates healing," said Marc Knebel, Head of the Medical Systems Market Segment at Evonik. "We are closing this gap in the market with VESTAKEEP Fusion and offering an alternative to titanium, stainless steel, or cobalt-chromium implants."
“We have made significant investments in new equipment, and this will allow us to produce our products more effectively and efficiently,” said Bryan Coppes, vice president of engineering and R&D at Infiltrator. “It is the new capabilities and opportunities for continued product development that are truly exciting. This new equipment will allow us to continue to bring new and innovative products to market and meet and exceed our customers' needs.”
Engel said it is increasingly receiving requests for custom solutions in the extremely high clamping force range. Clamping forces of 10,000 tons and more are possible. Machines of this size can process individual shot weights of several hundred kilograms or pounds and achieve two-ton-per-hour material throughput.
Engel added in the news release that it shares a commitment to sustainability with ADS, which claims to recycle more plastic than any other company in North America.
Evonik is also developing a 3D-printable VESTAKEEP Fusion filament that can be processed via additive manufacturing using fused filament fabrication technology.
Initially offered in granule form and as semi-finished products, VESTAKEEP Fusion can be milled, compression molded, extruded, and injection molded, said Evonik. The compound was optimized for injection molding in close cooperation with Samaplast AG.
GETTING A QUOTE WITH LK-MOULD IS FREE AND SIMPLE.
FIND MORE OF OUR SERVICES:
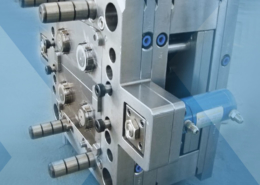
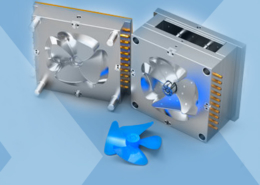
Plastic Molding

Rapid Prototyping
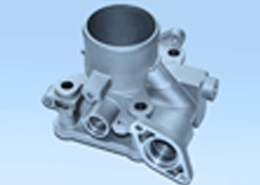
Pressure Die Casting
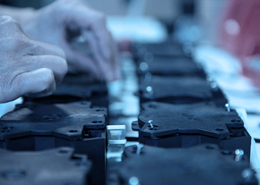
Parts Assembly
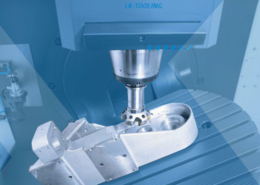