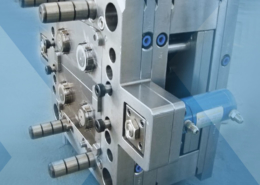
Venture Plastics welcomes director of new business development - plastic injecti
Author:gly Date: 2024-09-30
Novares is a global designer and manufacturer of complex components and systems for automotive OEMs. “In collaboration with Application Development Engineer Vincent Descombes and his team of experts from DuPont’s Center of Excellence for automotive electrification and assembly techniques, the engineers at our Powertrain China Skill Center were able to overcome technical challenges and provide a disruptive solution for EV battery cooling,” said Laurent Vanholme, Expert, Powertrain Components, at Novares. “We were able to master the difference in thermal expansion between the metal and plastic parts, and re-engineer the product to be processed with conventional welding.”
Editor in chief of PlasticsToday since 2015, Norbert Sparrow has more than 30 years of editorial experience in business-to-business media. He studied journalism at the Centre Universitaire d'Etudes du Journalisme in Strasbourg, France, where he earned a master's degree.
“Congratulations to Novares for this novel development, which comes at a critical time for demand growth of BEVs. Novares’ work will help OEMs offer consumers vehicles that drive farther, with batteries that last longer,” said Gabe Knee, Marketing Manager for Vehicle Electrification at DuPont Mobility & Materials. “Our plastic/metal bonding technology is a game changer for manufacturers of automotive components and will quickly find uses in other industries.”
The idea for LifeArk came into being when Wee visited a cousin who was a missionary in the Amazon. Wee was struck by how locals living along the river had to move whenever waters rose. “I decided, ‘Let me actually see if I can come up with housing that can float on the water,” Wee told LAist. Hence the name for the company. An encounter with Paul Cho, a co-founder of homeless services provider Illumina Foundation in California’s Orange County, led to applying the concept to first-world displacement.
The patented plastic/metal bonding technology enables the efficient production of a range of components for the automotive industry and other sectors. The technology was initially developed to support the replacement of metal EV battery cooling plates with hybrid designs that are more economical to produce and that better manage EV battery temperatures. Novares confirmed that its cooling plates meet industry requirements and enable cost reductions compared with all-metal alternatives.
Visitors to K 2022 can learn about the new bonding technology and the latest in sustainable and transformative materials from DuPont in hall 6, stand C43, from Oct. 19 to 26.
A pilot project in Los Angeles County uses roto-molded plastic modules to build permanent supportive housing for a fraction of the cost of municipal projects.
LifeArk molds 8-x-8 foot modules from a proprietary high-density polyethylene (HDPE) skin with an integrated high-density polyurethane core that snap together a little bit like Lego pieces to “build” housing units. The material contains 30% post-consumer recycled plastic. The pieces are roto-molded at a partner facility in Madera, CA, where 90% of the prefab housing is built. That has helped to slash construction costs.
DuPont’s bonding technology is also key. This technology — which can be integrated into the injection molding process — enables quick hot-plate welding of aluminum to injection-molded parts made of Zytel or Zytel HTN. Although the metal and the thermoplastics have different coefficients of thermal expansion, the bond between these disparate materials is strong enough to withstand extreme temperatures and aggressive chemicals.
Perhaps to preempt concerns from the zero-tolerance-for-plastics crowd, LifeArk notes the environmental benefits of using HDPE for the building blocks on its website. The material emits no harmful fumes into the environment and its production requires only a fraction of the energy required to produce steel from iron ore. The LifeArk modules can even be produced from 100% recycled HDPE, the company stresses, and is 100% recyclable. Housing made from the material has a 30-year lifespan with minimal maintenance, it adds.
The patented process enables rapid hot-plate welding of aluminum to injection-molded parts made of polyamide, allowing for different coefficients of thermal expansion.
Interestingly, the foam cores and a hull that replaces the land deck allow the modules to float. The LifeArk building system was designed to “create self-sustaining communities on water and land,” said the company on its website, and is a “rapidly deployable response that will mobilize economic development and regeneration for millions of displaced peoples around the world.”
LifeArk has started landing contracts up and down California’s central coast, reports LAist, but all eyes right now are on a pilot project in El Monte, a working class suburb of Los Angeles in the San Gabriel Valley. The company is using a $1 million innovation grant awarded by LA County to stitch together “dozens of modules to create three beige-gray, low-lying buildings that blend into a neighborhood that includes an ice cream supplier and faded stucco apartment complex,” writes LAist.
Key to the success of these hybrid cooling plates is DuPont Zytel HTN high-temperature nylon, which withstands the temperatures and aggressive chemicals in these applications and has flow properties that enable complex designs.
A lack of affordable housing is one of the causes of homelessness in major US urban centers. In Los Angeles County, where I live, more than 69,000 people are experiencing homelessness, according to the most recent survey of the L.A. Homeless Services Authority. Encampments riddle Los Angeles and surrounding communities and there is a wearied sense among residents that the problem has become intractable. An architect/entrepreneur by the name of Charles Wee begs to differ. His company LifeArk claims it can build permanent supportive housing at a cost of $190,000 per unit, reports nonprofit media outlet LAist. Compare that with the median per unit cost set forth by municipal officials of $470,000. What’s Wee's secret ingredient? You guessed it — plastic.
Tier 1 Novares and DuPont Mobility & Materials are co-developing a new hybrid plastic/metal cooling plate that will help OEMs extend the range and lifetime of their EV batteries. One key to this new project is the patented plastic/metal bonding technology developed at DuPont’s technology center in Meyrin, Switzerland.
GETTING A QUOTE WITH LK-MOULD IS FREE AND SIMPLE.
FIND MORE OF OUR SERVICES:
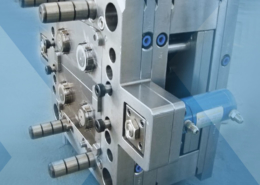
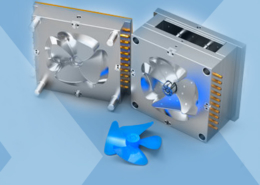
Plastic Molding

Rapid Prototyping
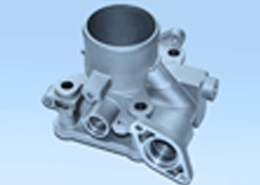
Pressure Die Casting
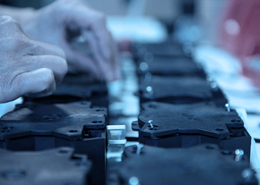
Parts Assembly
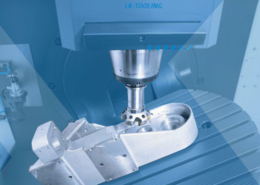