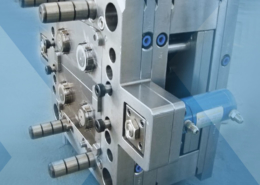
Valeo front end modules manufactured using Engel’s fully automated one-shot
Author:gly Date: 2024-09-30
As with all Sodick injection moulding machines, the new GL30-LP is equipped with Sodick’s unique V-Line two-stage plunger injection system. This groundbreaking innovation separates the injection and plasticisation processes in one unit, resulting in extremely accurate, rapid and repeatable resin injection. This suppresses outgassing, reduces fibre fracture and prevents backflow to provide unparalleled levels of performance, consistency and quality throughout the manufacturing process. The V-Line technology also delivers excellent plasticisation and injection performance with unrelenting stability and reliability in the plasticisation process. This contributes to accurate and highly repeatable resin injection whilst the hydraulic accumulator mechanism enables extremely high-speed injection with dynamic responsiveness.
Imprint Cookie-Manager About Media Subscription cancellation Privacy General Terms and Conditions Help AI-Guidelines
This portal is a brand of Vogel Communications Group. You will find our complete range of products and services on www.vogel.com
Sodick has three core principles for their moulding machines and the GL30-LP achieves these with its consistent plasticising heat profile, constant filling volume and constant holding pressure — all of which work in perfect harmony to achieve ultra-precise injection moulding results. In addition, the mould open/close clamping mechanism adopts both an electronic system to achieve accurate positional control and a hydraulic mould clamping mechanism that ensures a repeatable and highly accurate clamping force. With a direct pressure mould clamping system utilising the merits of the electro-hydraulic hybrid system, precision and repeatability are assured.
At Mach 2024, Sodick Europe and UK distributor Sodi-Tech will unveil six innovative machine tools, including the Mach premiere of the 30-tonne hydraulic hybrid GL30-LP injection moulding machine.
Naturally, we always handle your personal data responsibly. Any personal data we receive from you is processed in accordance with applicable data protection legislation. For detailed information please see our privacy policy.
This innovations offer technology and productivity enhancements for every machine shop and toolmaking business. For instance, the new GL30-LP injection moulding machine is destined to be a crowd-pleaser for the injection mould segment – especially for manufacturers of small, complex and high-precision components.
Weight reduction and lean manufacturing are key focuses in the aerospace sector as designers seek to the reduce operating costs of their aircraft. Consequently, thermoplastic composites that can perform with at least the same assurance as traditional metals and thermosets are in demand.
Perfect for manufacturers in the medical, electronic and precision instrumentation sectors, the new GL30-LP is equipped with Sodick’s unique V-Line technology, direct pressure mould clamping and the new Total Servo Drive system. With unparalleled levels of technology packed into a small-footprint machine, the GL30-LP demonstrates exceptional stability, traceability and usability that combine with a host of advanced injection moulding functions to improve operational accuracy, productivity, performance and energy efficiency.
I hereby consent to Vogel Communications Group GmbH & Co. KG, Max-Planck-Str. 7/9, 97082 Würzburg, Germany, including any affiliated companies according to §§ 15 et seq. AktG (hereafter: Vogel Communications Group) using my e-mail address to send editorial newsletters. A list of all affiliated companies can be found here
Besides up to 70% weight savings compared to metals such as stainless steel, aluminum, and titanium, the innovative composite manufacturing process used by Tri-Mack provides several benefits leading to faster part manufacturing cycle times compared to thermosets. "Thermoset composite parts typically take several hours to complete," said Tom Kneath, director of sales and marketing at Tri-Mack. "The Victrex PEEK composite brackets have manufacturing cycle times measured in minutes. That speed, paired with the ability to recycle the material for other applications, takes us to a whole new level of processing efficiency that isn't achievable with thermosets."
PEEK/carbon fiber thermoplastic composite offers 70% weight saving versus stainless steel, with better manufacturability to boot.
From a technical specification perspective, the new GL30-LP has a compact footprint of just 3150 X 1030 X 1679 mm with a maximum clamping force of 294 kN (392kN optional). The machine has a tie bar distance of 310 X 310 mm with a minimum and maximum die height of 150 and 360 mm respectively. Capable of accommodating tools up to 200 kg, the GL30-LP is available with three screw diameters of 14, 18 and 22 mm. Depending upon the variant selected, manufacturers can achieve a maximum injection specific pressure (MPa) from 260 to 288 with an injection volume from 4.5 to 27 cm3 and an injection rate by volume from 57 to 190 cm3/s.
Weight reduction and lean manufacturing are key focuses in the aerospace sector as designers seek to the reduce operating costs of their aircraft. Consequently, thermoplastic composites that can perform with at least the same assurance as traditional metals and thermosets are in demand.
In response to these requirements, Tri-Mack Plastics Manufacturing Corporation, a molder of high-temperature engineering thermoplastics located in Bristol, RI, has developed Victrex PEEK (polyetheretherketone) composite manufacturing capabilities and produced brackets for use in aircraft structural applications. The brackets weigh approximately 45g each, and are employed in primary and secondary structural applications in commercial and military aircraft. Tri-Mack specified the material due to its technical features and proven track record of 25 years of use in injection molded aerospace components.
Sodick Europe and UK distributor Sodi-Tech are set to inject some excitement into the mould tool manufacturing sector on Stand 350 in Hall 20 at Mach 2024. The company will introduce six industry-leading machine tools with many of these innovations receiving their Mach exhibition premiere. For the injection mould and toolmaking industry, Sodick Europe and Sodi-Tech UK will introduce their new 30-tonne hydraulic hybrid GL30-LP injection moulding machine.
Newsletter content may include all products and services of any companies mentioned above, including for example specialist journals and books, events and fairs as well as event-related products and services, print and digital media offers and services such as additional (editorial) newsletters, raffles, lead campaigns, market research both online and offline, specialist webportals and e-learning offers. In case my personal telephone number has also been collected, it may be used for offers of aforementioned products, for services of the companies mentioned above, and market research purposes.
I understand that I can revoke my consent at will. My revocation does not change the lawfulness of data processing that was conducted based on my consent leading up to my revocation. One option to declare my revocation is to use the contact form found at https://contact.vogel.de. In case I no longer wish to receive certain newsletters, I have subscribed to, I can also click on the unsubscribe link included at the end of a newsletter. Further information regarding my right of revocation and the implementation of it as well as the consequences of my revocation can be found in the data protection declaration, section editorial newsletter.
With manufacturers increasingly conscious of energy costs and carbon footprint, the new GL30-LP incorporates Sodick’s Total Servo Drive that provides even greater energy saving performance through electric servo motors for the hydraulic pump drive and the mould open/close and ejection mechanism. Furthermore, the green efficiency credentials of the machine are enhanced by its quick start to production and improved ratio of crushed and recycled material and moulds.
By clicking on „Subscribe to Newsletter“ I agree to the processing and use of my data according to the consent form (please expand for details) and accept the Terms of Use. For more information, please see our Privacy Policy.
Component integrity is also critical to keeping aircraft in service in order to minimize maintenance and downtime. Thermoplastic composites made from Victrex PEEK can provide the chemical and corrosion resistance to jet fuel, hydraulic fluid, de-icing solution, salt, steam, water and other commonly used service fluids that would typically undermine the longevity of metals. "Victrex PEEK composites can offer between four- and five-times higher fatigue strength, specific stiffness, and specific strength when compared to traditional metals such as aluminum," says Weidig. "These mechanical properties along with vibration and noise dampening improvements make Victrex PEEK composites an attractive and viable solution for engineers looking to replace heavy metals and thermosets."
In case I access protected data on Internet portals of Vogel Communications Group including any affiliated companies according to §§ 15 et seq. AktG, I need to provide further data in order to register for the access to such content. In return for this free access to editorial content, my data may be used in accordance with this consent for the purposes stated here.
The composite has a density of 1.6 g/cm3 versus 8 g/cm3 for stainless steel. Based on current fuel prices, the removal of one kilogram (2.2 lb) of weight from a short-range aircraft can save airlines up to $100 in annual fuel costs. "Assuming that the composite brackets can remove 100 kg (220.5 lb) of weight, an airline with 500 short-range aircraft could save up to $5 million per year in fuel costs by making the switch from metal," explains Ralf Weidig, Composites Business Leader for Victrex (West Conshohocken, PA).
As the world-leading brand, Sodick will give Mach show premieres to the new VN600Q, the ALC600G iG+E precision wire-cut EDM with new iGroove+ technology and the UX450L linear motor driven machining centre. Appearing alongside these Mach debutants will be the AD35L die sink EDM and the AL60G EDM die sink machine which will incorporate an Erowa Compact 80 robotic loading system with a Zeiss Duramax measurement and probing system that will provide live demonstrations at the event.
GETTING A QUOTE WITH LK-MOULD IS FREE AND SIMPLE.
FIND MORE OF OUR SERVICES:
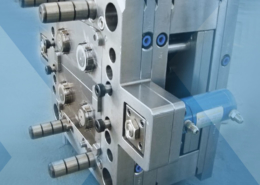
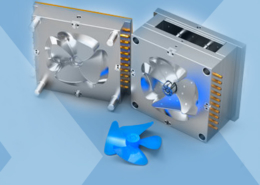
Plastic Molding

Rapid Prototyping
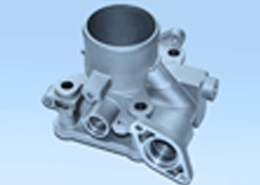
Pressure Die Casting
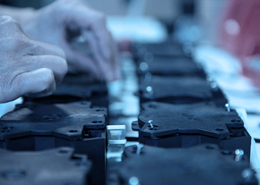
Parts Assembly
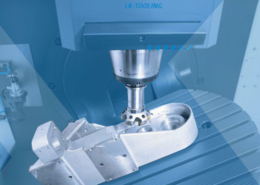