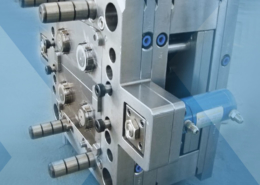
Exploring Thermolator Injection Molding: Revolutionizing Manufacturing Processes
Author:gly Date: 2024-06-08
Introduction
Thermolator injection molding stands at the forefront of modern manufacturing, offering innovative solutions to streamline production processes across various industries. This article delves into the intricacies of thermolator injection molding, shedding light on its significance, functionality, and implications for the manufacturing landscape.
Understanding Thermolator Injection Molding
Thermolator injection molding is a sophisticated manufacturing technique that involves the precise control of temperature during the injection molding process. By maintaining optimal temperature conditions, thermolators ensure the uniformity and quality of molded products, significantly enhancing efficiency and reducing production costs.
Historical Background
The evolution of thermolator injection molding can be traced back to the mid-20th century, with advancements in materials science and engineering driving its development. Initially utilized in the production of plastic components, thermolator injection molding has since expanded its applications to encompass a diverse range of industries, including automotive, electronics, and medical devices.
Operational Mechanism
At its core, thermolator injection molding relies on the principle of heating and cooling materials to facilitate the shaping of molds. Through a series of precise temperature controls and hydraulic mechanisms, molten materials are injected into molds, where they solidify to form finished products. This intricate process demands meticulous attention to detail and advanced technological infrastructure to achieve optimal results.
Advantages of Thermolator Injection Molding
Enhanced Precision
One of the primary benefits of thermolator injection molding is its ability to produce intricate and precise components with minimal margin for error. By maintaining consistent temperature profiles throughout the molding process, manufacturers can achieve unparalleled levels of accuracy and repeatability, ensuring uniformity across production batches.
Improved Efficiency
Compared to traditional molding techniques, thermolator injection molding offers significantly faster cycle times, allowing for higher throughput and increased productivity. The precise control of temperature parameters minimizes downtime associated with cooling and reheating, enabling continuous operation and swift turnaround times.
Cost-Effectiveness
Despite the initial investment required for implementing thermolator injection molding systems, the long-term cost savings are substantial. By optimizing material usage, reducing scrap rates, and enhancing production efficiency, manufacturers can achieve significant economies of scale, ultimately driving down per-unit costs and enhancing profitability.
Challenges and Considerations
Technological Complexity
While thermolator injection molding offers numerous benefits, its implementation presents inherent challenges, particularly regarding technological complexity. The integration of temperature control systems, hydraulic actuators, and precision molds necessitates sophisticated engineering expertise and substantial capital investment.
Quality Assurance
Maintaining consistent quality standards is paramount in thermolator injection molding, given the criticality of temperature control in the molding process. Deviations from optimal temperature ranges can result in defects and imperfections, compromising product quality and reliability. Implementing robust quality assurance protocols is essential to mitigate such risks and ensure compliance with industry standards.
Environmental Impact
Despite its efficiency and precision, thermolator injection molding raises environmental concerns related to energy consumption and material waste. The energy-intensive nature of heating and cooling processes contributes to carbon emissions and resource depletion, highlighting the need for sustainable manufacturing practices and renewable energy sources.
Future Perspectives and Conclusion
As manufacturing technologies continue to evolve, the role of thermolator injection molding is poised to expand further, driving innovation and efficiency across diverse industries. By embracing advancements in materials science, automation, and sustainability, manufacturers can harness the full potential of thermolator injection molding to unlock new opportunities and address emerging challenges.
In conclusion, thermolator injection molding represents a paradigm shift in modern manufacturing, offering unparalleled precision, efficiency, and cost-effectiveness. By understanding its principles, advantages, and challenges, manufacturers can leverage this transformative technology to achieve sustainable growth and competitive advantage in an ever-evolving global market.
GETTING A QUOTE WITH LK-MOULD IS FREE AND SIMPLE.
FIND MORE OF OUR SERVICES:
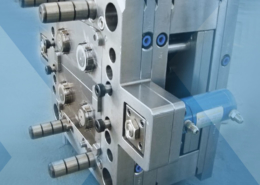
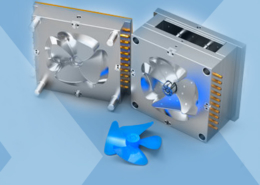
Plastic Molding

Rapid Prototyping
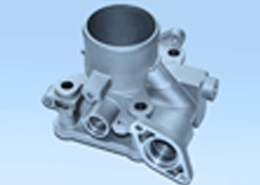
Pressure Die Casting
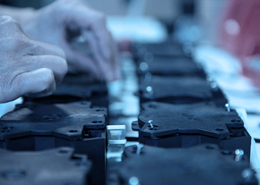
Parts Assembly
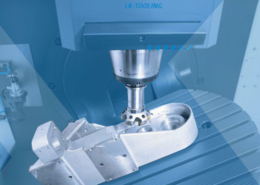