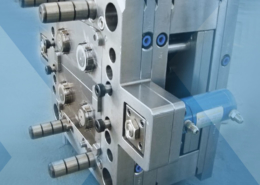
US-Made Pallet Injection Molding Machine Priced to Compete - custom injection mo
Author:gly Date: 2024-09-30
Prior to 2021, the packaging consisted of a cardboard and aluminium tube, a polyethylene bottom, and a polyethylene and polystyrene cap. These were considered partially recyclable.
According to these trials, the pack was successful in the areas of print quality, processability, and recyclability when the NextCycle IML labels were applied.
Global contract manufacturer Tessy Plastics surpassed 1.25 million cycles on a deodorant packaging mold built with Mantle components and slashed production time 60%, from 150 to 60 hours.
Vincent Mooij, director of CIRCPACK by Veolia, concludes: “As we’re paving the road to a circular economy for plastic packaging, DfR guidelines and RecyClass’ classification requirements will indeed continue to grow stricter. Going mono-material was a giant step forward for JOZO’s salt shakers. Decorating the packaging with NextCycle IML labels, supports the future availability of high purity rPP.”
“Driven by JOZO’s visionary commitment to sustainable progress and true to our mission of delivering 100% recyclable and circular packaging solution, we wanted to take it one step further to live up to constantly evolving packaging regulations,” explains Alexander Heinsdijk, business development and marketing manager at SFA Packaging. “Together with MCC Verstraete and JOZO we looked at the options for further improvement. We started trials replacing standard IML labels by the NextCycle IML technology.”
“The NextCycle IML technology allows for the packaging to enter the recycling process without the label. In this case, recycling the JOZO tubes results in white recycled material. It’s the perfect balance between recyclability and shelf appeal.”
On-demand digital platform Fathom Manufacturing cut toolmaking time 45%, from 200 to 110 hours, by eliminating or reducing operations including CNC milling, EDM, and polishing.
The simplified toolmaking system comes at a critical time for the $265-billion molded parts market, asserted one expert.
Geoff Giordano is a tech journalist with more than 30 years’ experience in all facets of publishing. He has reported extensively on the gamut of plastics manufacturing technologies and issues, including 3D printing materials and methods; injection, blow, micro and rotomolding; additives, colorants and nanomodifiers; blown and cast films; packaging; thermoforming; tooling; ancillary equipment; and the circular economy. Contact him at [email protected].
JOZO’s decorated saltshaker tubes have adopted a new, user-friendly dosage cap and MCC Verstraete’s NextCycle IML labels in collaboration with SFA Packaging, CIRCPACK, and Veolia, with the end goal being circular packs that produce high-quality recycled polypropylene.
The P-200 printer, with a build volume of 200 x 200 x 150 mm, is produced on a CNC platform that combines printing and machining for superior accuracy and surface finish. The F-200 furnace sinters parts and can support multiple printers.
Meanwhile, Bostik is pursuing food- and INRT-grade recycled polypropylene sourced from post-consumer packaging waste as the 50th participant in Nextek’s NEXTLOOPP project.
Then RecyClass’ Design for Recycling guidelines and requirements were updated in February 2023 in a bid to drive the recyclability – and, in turn, the circularity – of packaging designs. CIRCPACK and Veolia served as advisors in the development of the new tube, which is designed to be ‘future-proof’.
A new metal 3D-printing system from San Francisco’s Mantle promises to dramatically reduce the time and cost of creating injection mold tooling.
In a similar development, MCC Verstraete’s IML labels were recently printed with fluorescent markers from TOMRA and NEXTLOOPP – an extension of the team’s efforts to bring its PolyPPRISM sorting technology to commercial scale and recycle food-grade polypropylene.
The system employs Mantle’s H13 and P2X tool steels, which perform like traditional materials in secondary operations such as machining, polishing, coating, and laser welding. Tool paths and machine instructions are automated with the system’s easy-to-use software.
JOZO then worked alongside SFA to transition the tubes into mono-material polypropylene decorated with IML decoration, apparently achieving both shelf appeal and recyclability. Once assessed by RecyClass in October 2022, the tube received a Class B classification – meaning that, minus ‘minor recyclability issues’ that have slight impacts on the resultant recyclate, most of the components could contribute to a closed loop.
Wisconsin’s Nicolet Plastics will install one of Mantle’s first production systems to bring tool production in house and increase tool complexity. Mantle’s system will let Nicolet “significantly reduce the time it takes to produce production-quality tools and be able to start production in weeks versus months,” according to CEO Tony Cavalco. “Our tool designers and project managers will utilize the Mantle system for projects involving high-volume part manufacturing. Mantle technology will allow us to design conformal cooling channels to reduce molding cycle time and ensure the highest quality products for our customers.”
Using its patented TrueShape technology, Mantle’s flagship products, the P-200 printer and F-200 furnace, have already cut tooling lead times and costs by more than 50%, the company said. Toolmakers who have installed beta systems include Tessy Plastics, Nicolet Plastics, Fathom Manufacturing, and Westminster Tool. The first full production systems are slated for delivery in the first half of 2023.
Westminster Tool integrated a Mantle beta system into its mold-making operations, finding that the printer’s precision lets them bypass many internal manufacturing processes, said founder and president Ray Coombs. “Mantle far surpasses any additive metal technology that we have seen previously.”
“There is a massive skills gap in the injection mold-making industry,” said Hillary Thomas, Westminster Tool Vice President. “Mantle’s technology is so intuitive that, with minimal training, we can have someone quickly operating and running this machine. Mantle will help Westminster Tool change how we do business.”
Nico Van de Walle, Product and Circular Economy manager Global IML at MCC Verstraete, continues: “As a next-generation solution for sustainable rigid PP packaging, NextCycle IML labels are uniquely designed to separate from the container during the mechanical recycling process, while staying securely fastened with no impairment to its adhesive properties during its lifecycle.
GETTING A QUOTE WITH LK-MOULD IS FREE AND SIMPLE.
FIND MORE OF OUR SERVICES:
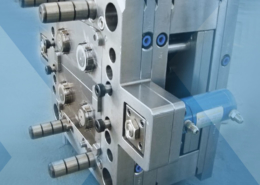
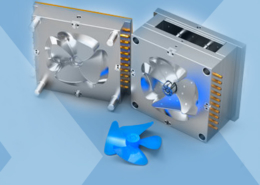
Plastic Molding

Rapid Prototyping
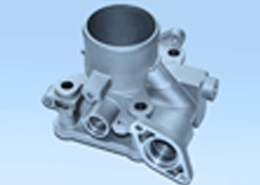
Pressure Die Casting
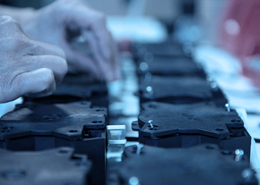
Parts Assembly
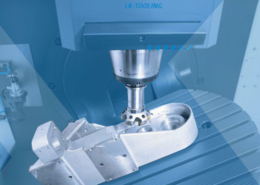