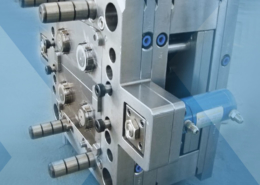
Exploring Soft Tooling Injection Molding: Revolutionizing Manufacturing Processe
Author:gly Date: 2024-06-08
Soft tooling injection molding, a cutting-edge technology in the realm of manufacturing, has garnered significant attention for its transformative capabilities. This article aims to delve into the intricacies of soft tooling injection molding, elucidating its principles, applications, advantages, and challenges.
Introduction: Unveiling the Marvels of Soft Tooling Injection Molding
Soft tooling injection molding represents a paradigm shift in the manufacturing landscape, offering a novel approach to producing intricate components with unparalleled precision and efficiency. Unlike traditional injection molding techniques that rely on rigid tooling, soft tooling leverages flexible molds crafted from materials such as silicone or urethane. This flexibility facilitates rapid prototyping, accelerates product development cycles, and enhances design freedom, making it a preferred choice across diverse industries.
The Science Behind Soft Tooling
Soft tooling injection molding operates on the fundamental principle of utilizing pliable molds to form intricate geometries with minimal tool wear. These molds, typically composed of silicone or similar elastomers, adapt to the contours of the injected material, ensuring uniformity and precision in the final product. By harnessing the elasticity of the mold material, manufacturers can achieve intricate details and intricate designs that were previously unattainable with traditional methods.
Applications Across Industries
The versatility of soft tooling injection molding transcends industry boundaries, finding applications in automotive, aerospace, consumer electronics, and medical device manufacturing, among others. In the automotive sector, soft tooling enables the production of lightweight, complex components with enhanced structural integrity, contributing to fuel efficiency and vehicle performance. Similarly, in the medical field, soft tooling facilitates the fabrication of patient-specific implants and medical devices with superior biocompatibility and accuracy, revolutionizing healthcare delivery.
Advantages Over Traditional Methods
Soft tooling injection molding offers a myriad of advantages over conventional manufacturing techniques, chief among them being reduced lead times, cost-effectiveness, and design flexibility. The rapid prototyping capabilities inherent in soft tooling expedite product development cycles, allowing manufacturers to bring innovations to market swiftly and stay ahead of competitors. Moreover, the ability to iterate designs seamlessly without incurring exorbitant tooling costs empowers designers to explore creative solutions and optimize product performance.
Challenges and Future Perspectives
Despite its myriad benefits, soft tooling injection molding presents certain challenges, including material compatibility, mold longevity, and dimensional stability. Addressing these challenges necessitates ongoing research and development efforts aimed at refining material formulations, enhancing mold durability, and optimizing process parameters. Looking ahead, advancements in material science, additive manufacturing, and process optimization hold the promise of overcoming current limitations, further expanding the scope and feasibility of soft tooling injection molding in various industries.
Conclusion: Pioneering the Future of Manufacturing
In conclusion, soft tooling injection molding heralds a new era in manufacturing, redefining the boundaries of what is possible in terms of design complexity, production efficiency, and product performance. As industries continue to embrace this transformative technology, collaboration among researchers, engineers, and manufacturers will be crucial in unlocking its full potential. By harnessing the power of soft tooling, we can propel innovation, drive economic growth, and pave the way for a more sustainable and resilient future.
Through this exploration of soft tooling injection molding, it becomes evident that its impact extends far beyond the realm of manufacturing, shaping the way we design, produce, and interact with products in the modern world. As we navigate the complexities of an ever-evolving global landscape, embracing innovative technologies such as soft tooling injection molding will be instrumental in fostering competitiveness, agility, and resilience in the manufacturing sector.
GETTING A QUOTE WITH LK-MOULD IS FREE AND SIMPLE.
FIND MORE OF OUR SERVICES:
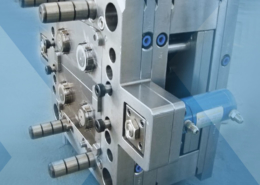
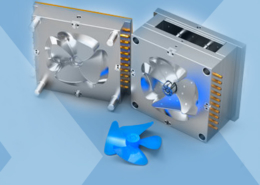
Plastic Molding

Rapid Prototyping
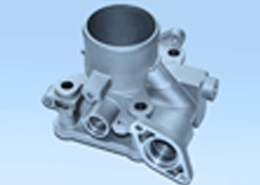
Pressure Die Casting
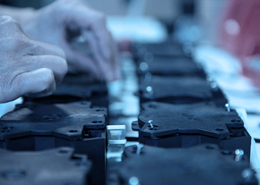
Parts Assembly
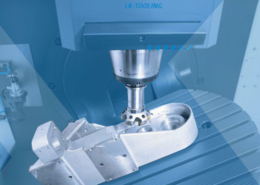