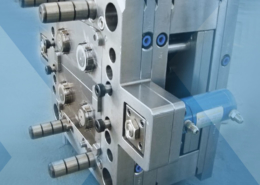
Unveiling the Next Generation of Injection Molding Machines: Faster,
Author:gly Date: 2024-09-30
Discover how artifical intelligence is revolutionizing plastics processing. Hear from industry experts on the future impact of AI on your operations and envision a fully interconnected plant.
Plastics Technology covers technical and business Information for Plastics Processors in Injection Molding, Extrusion, Blow Molding, Plastic Additives, Compounding, Plastic Materials, and Resin Pricing. About Us
The tailgate consists of several components. The outer frame and inner part made of Borealis Fibremod GB416LF are glued together to meet design and load requirements. Painted exterior parts are glued to the tailgate structure, as well. As a loadbearing part, the tailgate must be extremely robust to withstand static and dynamic loads. Part of the tailgate also lies in the vehicle’s interior, meaning it must comply with emission, fogging, and odor requirements. Finally, to achieve overall weight reduction for the new Multivan — it weighs around 200 kg less than its immediate predecessor — the tailgate itself must also be lighter. Using Fibremod GB416LF enabled Magna to meet these challenges head on.
Join Engel in exploring the future of battery molding technology. Discover advancements in thermoplastic composites for battery housings, innovative automation solutions and the latest in large-tonnage equipment designed for e-mobility — all with a focus on cost-efficient solutions. Agenda: Learn about cutting-edge thermoplastic composites for durable, sustainable and cost-efficient battery housings Explore advanced automation concepts for efficient and scalable production See the latest large-tonnage equipment and technology innovations for e-mobility solutions
Study shows the plastic compounding process is being used to boost electrical properties and UV resistance while custom compounding is increasingly being used to achieve high-performance in plastic-based goods.
Collaboration between materials supplier Borealis and Tier I Magna yielded the all-plastic tailgate, one of many firsts in the VW Multivan.
Join this webinar to explore the transformative benefits of retrofitting your existing injection molding machines (IMMs). Engel will guide you through upgrading your equipment to enhance monitoring, control and adaptability — all while integrating digital technologies. You'll learn about the latest trends in IMM retrofitting (including Euromap interfaces and plasticizing retrofits) and discover how to future-proof your machines for a competitive edge. With insights from industry experts, it'll walk you through the decision-making process, ensuring you make informed choices that drive your business forward. Agenda: Maximize the value of your current IMMs through strategic retrofitting Learn how to integrate digital technologies to enhance monitoring and control Explore the benefits of Euromap interfaces and plasticizing retrofits Understand how retrofitting can help meet new product demands and improve adaptability Discover how Engel can support your retrofitting needs, from free consultations to execution
In a time where sustainability is no longer just a buzzword, the food and beverage packaging industry is required to be at the forefront of this innovation. By adopting circular packaging processes and solutions, producers can meet regulatory requirements while also satisfying consumer demand and enhancing brand reputation. Join Husky to learn more about the broader implications of the circular economy — as well as how leading brands are leveraging this opportunity to reduce costs, increase design flexibility and boost product differentiation. Agenda: The cost and operational benefits of embracing circularity Key materials in circular packaging — including rPET and emerging bioplastics How to design a circular food and beverage package Strategies for selecting sustainable closures to future-proof packaging solutions Optimization and streamlining of production processes for enhanced efficiency How Husky Technologies can enable your sustainable success
This month’s resin pricing report includes PT’s quarterly check-in on select engineering resins, including nylon 6 and 66.
Additive technology creates air pockets in film during orientation, cutting down on the amount of resin needed while boosting opacity, mechanical properties and recyclability.
In business, it has become a platitude to call on employees to “take ownership” of their jobs; but PTA has taken that principal literally. In 2012, when Ray Seeley was seeking to wind down his role with the company, he balked at selling the company. “All the sales options could have made him a lot of money,” Dorans says, “but he knew at the end of the day that PTA would not have remained what PTA has always been, and he really cares about the employees.”
While prices moved up for three of the five commodity resins, there was potential for a flat trajectory for the rest of the third quarter.
Founded in 1953 in Connecticut, custom injection molder and moldmaker PTA Plastics now operates in Oxford, Conn. and Longmont, Colo. (pictured).
A collaboration between show organizer PLASTICS, recycler CPR and size reduction experts WEIMA and Conair recovered and recycled all production scrap at NPE2024.
The Plastics Industry Association (PLASTICS) has released final figures for NPE2024: The Plastics Show (May 6-10; Orlando) that officially make it the largest ever NPE in several key metrics.
Across all process types, sustainability was a big theme at NPE2024. But there was plenty to see in automation and artificial intelligence as well.
Molding operations are split between two rooms. The first, adjacent to the tool room, is filled by two rows of presses, while the other features a mix of presses and an assembly/secondary-operations area. Many value-added operations are mobile and can be wheeled into position adjacent to the press during molding runs. PTA has 34 injection machines companywide, with 18 in Longmont ranging up to 1375 tons. Most of the presses in Colorado are newer Toshiba’s, with an older Newbury and a Battenfeld (its largest machine) mixed in. Subtracting those two, the average press age comes in at just under 8 years.
One way PTA has remained ahead of that curve has been to find, defend and grow a niche in the market. That has meant a greater emphasis on medical clients and dedication to inhouse mold building, design-for-manufacture know-how, and value-added services.
Layout of he Longmont building, constructed in 1984, is not conducive to central drying, so PTA uses mobile dryers there. Recent additions include four new Matsui dryers. Dorans notes that PTA relies on a low-volume/high-mix business, which requires some agility, as the number of setups per month can range from 550 to 600.
While prices moved up for three of the five commodity resins, there was potential for a flat trajectory for the rest of the third quarter.
Robert Berg, director of information technology, says that since its inception, Job Book has been improved with direct feedback from the operators. Eventually, the company wants to tie in other equipment in the cell, including dryers. To make this, and other initiatives possible, PTA is currently in the midst of a building-wide IT overhaul, replacing older wire infrastructure with new fiber-optic cables.
Occupying more than 10,000 ft2, PTA’s toolroom in Longmont runs 24 hr a day with two shifts. Between the two facilities, PTA has 18 tool makers and produces up to 500 molds annually. Dorans estimates that 95% of the jobs it’s molding are run in tools made in house. Some mold components are outsourced, but the most important parts of the tool are cut by PTA. “Anything that touches plastics, we keep in-house,” Dorans says. Even for a component like a mold base, many of which PTA purchases from DME, Dorans notes that it is customized to the company’s specs.
PTA Plastics is in the midst of reconfiguring its warehouse, which includes extensive tool inventory, which it regularly manages to prune obsolete molds.
Value-added work has become a key and growing business for PTA, with Dorans noting, “It is very rare for us to mold a part and ship it without doing anything to it.” It is also rare for the company, which generates 70% of its business from medical, to take on simpler jobs. In the assembly area, Dorans picks up a housing with TPE overmolding and multiple screw inserts in different sides and along various planes. “This is a typical PTA part,” Dorans says, adding, “We don’t get poker chips.”
Successfully starting or restarting an injection molding machine is less about ticking boxes on a rote checklist and more about individually assessing each processing scenario and its unique variables.
technotrans says climate protection, energy efficiency and customization will be key discussion topics at PTXPO as it displays its protemp flow 6 ultrasonic eco and the teco cs 90t 9.1 TCUs.
“Our share value continues to grow year after year,” Dorans says, “and the employees are all given shares—they don’t buy them—so it’s an added benefit. It really makes you part of the team, and at the end of the day, your actions can actually improve the share value, and you can see those numbers continue to grow every year.” Since the inception of the ESOP, PTA reports that its stock performance has beaten the S&P every year, displaying the competitive strength of ESOP companies.
Formnext Chicago is an industrial additive manufacturing expo taking place April 8-10, 2025 at McCormick Place in Chicago, Illinois. Formnext Chicago is the second in a series of Formnext events in the U.S. being produced by Mesago Messe Frankfurt, AMT – The Association For Manufacturing Technology, and Gardner Business Media (our publisher).
In the early 2000s, as many molding shops de-emphasized their tool rooms and customers sought low-cost offshore molds, PTA did the opposite and invested in mold building in Connecticut and Colorado. “We were very aggressive towards growing the tooling business when many others were running away, pulling everything offshore,” Dorans says. “We just tried to understand what we needed to do.” Dorans admits that PTA wasn’t trying to compete with offshore moldmakers on cost, but it hoped to make a big-picture financial and long-term service case to its customers. “If your customer is looking at the total landed costs,” Dorans says, “at times, it still makes sense to do the work domestically, and you have control over that.”
Rich Dorans, who became president of PTA Plastics in March 2019, has been with the company since 1984 and was among those who chose to make the move in 1999 from Des Plaines, Ill. to Longmont, Colo.
Core Technology Molding turned to Mold-Masters E-Multi auxiliary injection unit to help it win a job and dramatically change its process.
The aim of this presentation is to guide you through the factors and the numbers that will help you determine if a robot is a smart investment for your application. Agenda: Why are you considering automation? What problems are you trying to solve? How and why automation can help Crunch the numbers and determine the ROI
Thousands of people visit our Supplier Guide every day to source equipment and materials. Get in front of them with a free company profile.
Plastics Technology’s Tech Days is back! Every Tuesday in October, a series of five online presentations will be given by industry supplier around the following topics: Injection Molding — New Technologies, Efficiencies Film Extrusion — New Technologies, Efficiencies Upstream/Downstream Operations Injection Molding — Sustainability Extrusion — Compounding Coming out of NPE2024, PT identified a variety of topics, technologies and trends that are driving and shaping the evolution of plastic products manufacturing — from recycling/recyclability and energy optimization to AI-based process control and automation implementation. PT Tech Days is designed to provide a robust, curated, accessible platform through which plastics professionals can explore these trends, have direct access to subject-matter experts and develop strategies for applying solutions in their operations.
Founded in 1953 in Bridgeport, Conn., custom injection molder and moldmaker PTA Plastics currently operates out of facilities in Oxford, Conn. and Longmont, Colo. But back in 1999, workers at a third site in Des Plaines, Ill. faced a decision. The Illinois plant would be closing, and while PTA would offer jobs to its workers at the two remaining sites, they would still have to decide whether to pick up and move to the East Coast or Rocky Mountains or stay put and find a new job.
Across the show, sustainability ruled in new materials technology, from polyolefins and engineering resins to biobased materials.
True to the adjective in its name, Dynamic Group has been characterized by constant change, activity and progress over its nearly five decades as a medical molder and moldmaker.
Dorans estimates that the company has 700 active tools in Longmont, with probably 1200 company wide. A strict preventive-maintenance schedule keeps these molds running, according to Brian Zutman, general manager. He notes that the ERP system will not allow a job to start up if the PM hasn’t been completed. The system works—PTA has tools from 1967 that are still running. Longevity is a particular benefit for medical tools—Dorans compares a good medical tool to an annuity, paying dividends for years after an initial investment. The downside, especially when you make upwards of 500 tools/year, is that mold inventory can build up. To avoid this, PTA performs a monthly review of the tool inventory, sending tools back to customers as they go out of service.
In this collection of content, we provide expert advice on welding from some of the leading authorities in the field, with tips on such matters as controls, as well as insights on how to solve common problems in welding.
In this three-part collection, veteran molder and moldmaker Jim Fattori brings to bear his 40+ years of on-the-job experience and provides molders his “from the trenches” perspective on on the why, where and how of venting injection molds. Take the trial-and-error out of the molding venting process.
Resin drying is a crucial, but often-misunderstood area. This collection includes details on why and what you need to dry, how to specify a dryer, and best practices.
Join KraussMaffei for an insightful webinar designed for industry professionals, engineers and anyone interested in the manufacturing processes of PVC pipes. This session will provide a comprehensive understanding of the technology behind the production of high-quality PVC pipes: from raw material preparation to final product testing. Agenda: Introduction to PVC extrusion: overview of the basic principles of PVC pipe extrusion — including the process of melting and shaping PVC resin into pipe forms Equipment and machinery: detailed explanation of the key equipment involved — such as extruders, dies and cooling systems — and their roles in the extrusion process Process parameters: insight into the critical process parameters like temperature, pressure and cooling rates that influence the quality and consistency of the final PVC pipes Energy efficiency: examination of ways to save material and energy use when extruding PVC pipe products
A long-glass fiber-reinforced polypropylene (PP) compound from Borealis is a core component of an all-plastic tailgate tagged to the new Volkswagen Multivan. Molded of Fibremod PP compound, the tailgate is said to be the largest ever all-thermoplastic tailgate.
When, how, what and why to automate — leading robotics suppliers and forward-thinking moldmakers will share their insights on automating manufacturing at collocated event.
Seeley’s solution was to create an Employee Stock Ownership Plan (ESOP), whereby he sold his stock to the company, creating a trust that holds the stock on the employees’ behalf with the share value determined by the success of the company—which, of course, is ultimately driven by its workers.
The revolutionary tailgate of the new VW Multivan demonstrates how customer-centric innovation and collaboration can produce high-performance parts that lower the overall carbon footprint of vehicles, said Borealis. The Fibremod portfolio of lighter-weight polypropylene (PP) compounds is giving Tier I suppliers and OEMs the freedom to design and manufacture more sustainable and lightweight solutions for leading automotive brands and their increasingly electric fleets, the company added.
PTA Plastics’ quality-control department creates a variety of testing fixtures and programs for CMM equipment, shipping both with parts to its customers.
Exhibitors and presenters at the plastics show emphasized 3D printing as a complement and aid to more traditional production processes.
Mike Sepe has authored more than 25 ANTEC papers and more than 250 articles illustrating the importance of this interdisciplanary approach. In this collection, we present some of his best work during the years he has been contributing for Plastics Technology Magazine.
“We take a look at where we are today, what the disruptors are going to be out in the future, and really how can we be a disruptor rather than getting disrupted,” Dorans says. “I don’t want to be ‘Amazoned’ or ‘Uberized’—we’re just trying to stay ahead of the curve from the technology standpoint.”
Despite price increase nominations going into second quarter, it appeared there was potential for generally flat pricing with the exception of a major downward correction for PP.
The toolroom, like the rest of the plant, is paperless, pulling CAD and CAM data from Cimatron software and feeding work progress into PTA’s ERP system supplied by InFor Syteline. The tool room is bookended by a Makino SNC 64 making electrodes from graphite for EDM on one side and a 5-axis Monoblock 65 Deckel Maho cutting steel on the other, with a variety of metalworking equipment in between. Dorans says PTA makes “purpose-built tooling”. That is, molds fabricated in a manner and from materials that are commensurate with what their ultimate job will be—satisfying the task to come while not being overengineered.
In a bid to go paperless, PTA Plastics created a digital “Job Book” replacing the three-ring binders that follow molds around at most shops with a digital program on a press-side laptop.
Learn about sustainable scrap reprocessing—this resource offers a deep dive into everything from granulator types and options, to service tips, videos and technical articles.
August 29-30 in Minneapolis all things injection molding and moldmaking will be happening at the Hyatt Regency — check out who’s speaking on what topics today.
Baystar's Borstar technology is helping customers deliver better, more reliable production methods to greenhouse agriculture.
The burden of managing those setups is eased by the company’s PTA Job Book software, created in-house about 13 years ago to help remove paper from the shop floor. At many other molding shops, a three-ring binder follows a job around, containing key specs and parameters for a part and mold. PTA’s Job Book makes this all-digital, allowing process and setup technicians to pull up everything from process parameters to water-line drawings on a press-side laptop. Step-by-step setup and assembly instructions are laid out with pictures and captions; and the system, which ties into the plant’s ERP software, provides real-time scrap data.
Sustainability continues to dominate new additives technology, but upping performance is also evident. Most of the new additives have been targeted to commodity resins and particularly polyolefins.
PP fiber-reinforced compounds have a proven track record when it comes to lightweighting for interior, exterior, and under-the-bonnet automotive parts. The proprietary Fibremod long-glass-fiber-reinforced PP (PP-LGF) technology offers fiber impregnation, flexibility in the use of various PP matrices, and the production of grades in customized colors. Fibremod compounds are described as cost-effective alternatives to conventional metals and engineering plastics–based solutions, as they are highly suitable for injection molding processes. Moreover, Fibremod LGF compounds boast flowability for smooth processing and low warpage.
While the melting process does not provide perfect mixing, this study shows that mixing is indeed initiated during melting.
In addition to straight injection molding, the company can do structural foam and gas assist. As PT visited, a Bauer compressor for gas assist was being wheeled into place next to one of the Toshiba machines. Keeping with its efforts to stay on technology’s cutting edge, PTA added gas assist when it was just getting started. Dorans notes that gas assist allows customers to break some design rules while also offering cosmetic and dimensional-stability benefits.
Processors with sustainability goals or mandates have a number of ways to reach their goals. Biopolymers are among them.
Mixed in among thought leaders from leading suppliers to injection molders and mold makers at the 2023 Molding and MoldMaking conferences will be molders and toolmakers themselves.
Mold maintenance is critical, and with this collection of content we’ve bundled some of the very best advice we’ve published on repairing, maintaining, evaluating and even hanging molds on injection molding machines.
PTA’s share value started at $3.95 in 2012, and came in at $12.90 in 2018. In October, PTA celebrates Employee Ownership Month, along with hundreds of ESOP companies around the country. Among other festivities, PTA will hold a raffle with prizes for workers who can make the closest guess at 2019’s share price. On a shelf in his office, Dorans has a row of mugs and cups commemorating the share price for each year, with steady increases all along. A new mug will soon be on Dorans’ shelf, but he says he can’t yet tell what number will be on it.
Join Wittmann for an engaging webinar on the transformative impact of manufacturing execution systems (MES) in the plastic injection molding industry. Discover how MES enhances production efficiency, quality control and real-time monitoring while also reducing downtime. It will explore the integration of MES with existing systems, emphasizing compliance and traceability for automotive and medical sectors. Learn about the latest advancements in IoT and AI technologies and how they drive innovation and continuous improvement in MES. Agenda: Overview of MES benefits What is MES? Definition, role and brief history Historical perspective and evolution Longevity and analytics Connectivity: importance, standards and integration Advantages of MES: efficiency, real-time data, traceability and cost savings Emerging technologies: IoT and AI in MES
Approaching its seventh decade in business, PTA Plastics has shifted its location and remade its customer base since its founding in 1953, but many things have not changed in the intervening years, including an emphasis on people and leading-edge technologies.
Gifted with extraordinary technical know how and an authoritative yet plain English writing style, in this collection of articles Fattori offers his insights on a variety of molding-related topics that are bound to make your days on the production floor go a little bit better.
The move had split the company, literally, but could have done so figuratively as well. In the end, all but one employee found a new PTA home, and Colorado received a healthy influx of Illinoians. Plastics Technology visited PTA’s facility in Longmont, which is 30 minutes northwest of Denver, the day after a narrow loss by the Chicago Bears, and more than a few of those transplants lamented the state of their long-distance “home” team with Rich Dorans, PTA’s president and PT’s tour guide.
Fibremod GB416LF was specifically tailored for use in tailgate carriers and visible structural parts. As a high-flow, 40%-fiber-reinforced material, it fulfils stringent emission and mechanical performance requirements. Using Fibremod GB416LF also can eliminate the need for additional surface finishing steps such as painting.
Plastics processors are finding applications for 3D printing around the plant and across the supply chain. Here are 8 examples to look for at NPE2024.
Second quarter started with price hikes in PE and the four volume engineering resins, but relatively stable pricing was largely expected by the quarter’s end.
“We just stay on top of the shows,” Dorans says. “Whether it’s IMTS (the International Manufacturing Technology Show) on the tooling side, or NPE and K on the plastics side.” Technology has long been a focus for the company and that didn’t change when Dorans took over. In fact, the concentration might have sharpened. The company is in the midst of a strategic planning initiative—PTA 2030-Envision the Future—that emphasizes where the industry and the market are headed and what the company would have to look like to continue to thrive. Making that determination is a cross-sectional team of 10 employees.
Ultradent's entry of its Umbrella cheek retractor took home the awards for Technical Sophistication and Achievement in Economics and Efficiency at PTXPO.
Introduced by Zeiger and Spark Industries at the PTXPO, the nozzle is designed for maximum heat transfer and uniformity with a continuous taper for self cleaning.
Dorans, an Illinois native who started with PTA in 1984, faced the stay-or-go decision 20 years ago. He made the move, and in March 2019, was named PTA’s president, taking over for Ray Seeley, who stepped aside after 40 years leading the company. When PT visited, Dorans—who had spent the previous week at an industry conference—was prepping to head to the K Show in Germany. A taxing schedule, but one that serves a core tenet.
In this collection of articles, two of the industry’s foremost authorities on screw design — Jim Frankand and Mark Spalding — offer their sage advice on screw design...what works, what doesn’t, and what to look for when things start going wrong.
Krones adds PET preform injection molding to its bottle blowing and filling capabilities, as well as cap molding and expansion into medical, food and other markets.
Say “manufacturing automation” and thoughts immediately go to the shop floor and specialized production equipment, robotics and material handling systems. But there is another realm of possible automation — the front office.
After successfully introducing a combined conference for moldmakers and injection molders in 2022, Plastics Technology and MoldMaking Technology are once again joining forces for a tooling/molding two-for-one.
Take a deep dive into all of the various aspects of part quoting to ensure you’ve got all the bases—as in costs—covered before preparing your customer’s quote for services.
In this collection, which is part one of a series representing some of John’s finest work, we present you with five articles that we think you will refer to time and again as you look to solve problems, cut cycle times and improve the quality of the parts you mold.
Multiple speakers at Molding 2023 will address the ways simulation can impact material substitution decisions, process profitability and simplification of mold design.
The company has taken on a 5000-ft2 offsite storage facility, which opens up some space in its warehouse. New racks were recently installed in the warehouse, and eventually most of the assembly and decoration work will be moved into that space, freeing up room for more injection machines. The wall currently occupied by secondary operations is already plumbed for another three presses, which could range up to 180 tons in clamp force.
While the major correction in PP prices was finally underway, generally stable pricing was anticipated for the other four commodity resins.
Always seeking to stay on the leading edge of technology, one of PTA’s most recent additions to its toolroom is a 5-axis Monoblock 65 Deckel Maho CNC milling machine.
This Knowledge Center provides an overview of the considerations needed to understand the purchase, operation, and maintenance of a process cooling system.
Because PTA can involve itself upfront in the design process—Dorans calls its capabilities here a “known strength”—it can put a project on the path toward a well-designed tool and a robust molding process while it’s still a 3D model. “We do not design parts, but we can help our customers design a part that’s manufacturable and cost-effective,” Dorans explains. “In some cases, it could be just eliminating a detail, which will save them money; or from a quality standpoint, refining a design we could all be much more successful with.”
GETTING A QUOTE WITH LK-MOULD IS FREE AND SIMPLE.
FIND MORE OF OUR SERVICES:
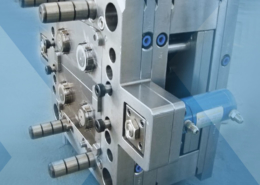
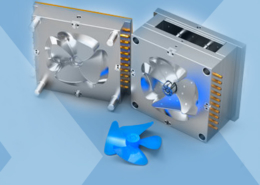
Plastic Molding

Rapid Prototyping
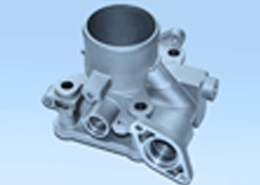
Pressure Die Casting
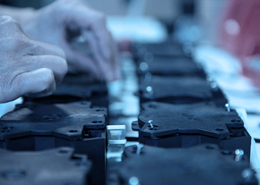
Parts Assembly
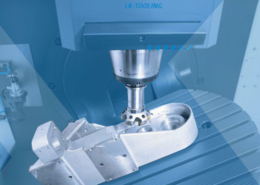