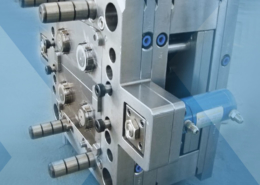
Unmanned Aerial System (UAS) Applies Injection Molded Chassis - ultem injection
Author:gly Date: 2024-09-30
Gifted with extraordinary technical know how and an authoritative yet plain English writing style, in this collection of articles Fattori offers his insights on a variety of molding-related topics that are bound to make your days on the production floor go a little bit better.
That also partly accounts for Omachron’s success in molding 100% regrind. For example, Conrad says his machines molded reground PVC plumbing fittings into new fittings that were 15% stronger than the originals, due to low molded-in stress. After five regrind cycles, the molded fittings still retained 10% higher strength than the virgin originals, owing to the low thermal stress of intrusion molding—without introducing any additional stabilizer additives.
The secret to all this is a process sometimes called “intrusion molding,” whereby the mold is filled by extrusion rather than by injection of a pre-plasticated shot of melt. According to Conrad, this method has the benefit of low pressure, low melt temperature, and very low molded-in stresses. Typical filling pressures are 100 to 300 psi, and final packing pressures run 600 to 900 psi. Conrad cites the example of molding ABS with typical process temperatures 5° to 15° C (9° to 27° F) lower than is recommended by the material supplier—“And we still get perfect parts.”
August 29-30 in Minneapolis all things injection molding and moldmaking will be happening at the Hyatt Regency — check out who’s speaking on what topics today.
Mike Sepe has authored more than 25 ANTEC papers and more than 250 articles illustrating the importance of this interdisciplanary approach. In this collection, we present some of his best work during the years he has been contributing for Plastics Technology Magazine.
If plastics processing can be compared for a moment to The Beatles, then rotational molding is George Harrison – the quiet one, often flying underneath the radar. But as with Harrison writing such classics as “Something” and “Here Comes the Sun”, rotational molding, also known as rotomolding, can surprise you sometimes. A case in point is Sherbrooke, Que.-based rotomolder Manunor, which has been making some noise of its own over the past several years by designing and manufacturing a series of innovative products, building a new 10,000-square-foot facility adjacent to its main 90,000-square-foot plant in Sherbrooke’s Gene H. Kruger Industrial Park, and investing in new machinery that includes a massive new rock n roll machine from equipment supplier STP Rotomachinery.
When, how, what and why to automate — leading robotics suppliers and forward-thinking moldmakers will share their insights on automating manufacturing at collocated event.
With the second generation of leadership now firmly in place as it marks 30 years in business, Manunor wants to keep growing. “We’re constantly meeting with companies that are making metal parts and working to convert them into plastics,” Marie-Michelle said. “We’re very diverse – anything that can be rotomolded, large or small, we can do it, and we want to build on that and keep expanding our product range.” The company also wants to draw more attention to rotomolding, period. “Rotomolding isn’t as well-known in the plastics space as it should be,” she said. “We want to help change that, and we bring local students in for tours as often as we can, to show them what our process is all about. We love rotomolding and we want more people to love it too.”
Additive technology creates air pockets in film during orientation, cutting down on the amount of resin needed while boosting opacity, mechanical properties and recyclability.
Implementing a production monitoring system as the foundation of a ‘smart factory’ is about integrating people with new technology as much as it is about integrating machines and computers. Here are tips from a company that has gone through the process.
Other advantages, she continued, include low-cost tooling in either aluminum or steel; consistent wall thickness; double-wall construction; high durability, since the parts are molded as one solid piece; high stability; and a great appearance, since rotomolding can accommodate surface finishes such as textures, logos, symbols, and lettering. And unlike competitive processes such as blow molding and thermoforming, rotomolding produces no pinch-off seams or weld lines, which gives a finished product without the use of secondary processes. “It’s the best method for making large, one-piece hollow parts and double-walled open containers such as tanks, kayaks, and coolers,” Marie-Michelle said.
Plastics Technology covers technical and business Information for Plastics Processors in Injection Molding, Extrusion, Blow Molding, Plastic Additives, Compounding, Plastic Materials, and Resin Pricing. About Us
Molds are made of aluminum, which reduces weight, cost, and time for machining. (The molds for the 4-ft planks mentioned above were built, and initial parts produced, only five days after receiving the order.) Some molds are ceramic-based with a flame-sprayed nickel coating for heat transfer and corrosion protection. Molds can be mounted on a pushcart for installation—“One person can do it safely,” Conrad asserts.
Ultradent's entry of its Umbrella cheek retractor took home the awards for Technical Sophistication and Achievement in Economics and Efficiency at PTXPO.
Introduced by Zeiger and Spark Industries at the PTXPO, the nozzle is designed for maximum heat transfer and uniformity with a continuous taper for self cleaning.
While the major correction in PP prices was finally underway, generally stable pricing was anticipated for the other four commodity resins.
While prices moved up for three of the five commodity resins, there was potential for a flat trajectory for the rest of the third quarter.
Thousands of people visit our Supplier Guide every day to source equipment and materials. Get in front of them with a free company profile.
Plastics Technology’s Tech Days is back! Every Tuesday in October, a series of five online presentations will be given by industry supplier around the following topics: Injection Molding — New Technologies, Efficiencies Film Extrusion — New Technologies, Efficiencies Upstream/Downstream Operations Injection Molding — Sustainability Extrusion — Compounding Coming out of NPE2024, PT identified a variety of topics, technologies and trends that are driving and shaping the evolution of plastic products manufacturing — from recycling/recyclability and energy optimization to AI-based process control and automation implementation. PT Tech Days is designed to provide a robust, curated, accessible platform through which plastics professionals can explore these trends, have direct access to subject-matter experts and develop strategies for applying solutions in their operations.
Join Wittmann for an engaging webinar on the transformative impact of manufacturing execution systems (MES) in the plastic injection molding industry. Discover how MES enhances production efficiency, quality control and real-time monitoring while also reducing downtime. It will explore the integration of MES with existing systems, emphasizing compliance and traceability for automotive and medical sectors. Learn about the latest advancements in IoT and AI technologies and how they drive innovation and continuous improvement in MES. Agenda: Overview of MES benefits What is MES? Definition, role and brief history Historical perspective and evolution Longevity and analytics Connectivity: importance, standards and integration Advantages of MES: efficiency, real-time data, traceability and cost savings Emerging technologies: IoT and AI in MES
Omachron’s commercial motto is “The Power of Small,” referring to empowering small businesses to tackle big projects with low capital investment, using small-footprint machines with lower power consumption. Such machines make possible “distributed manufacturing” close to customers for the machines’ output, even in rural areas.
Conrad notes that besides molding huge parts, his process also ensures accurate reproduction of part surface features down to micro scale—for example, capillary microstructures measuring only a ten-thousandth of an inch (0.001 mil).
In a time where sustainability is no longer just a buzzword, the food and beverage packaging industry is required to be at the forefront of this innovation. By adopting circular packaging processes and solutions, producers can meet regulatory requirements while also satisfying consumer demand and enhancing brand reputation. Join Husky to learn more about the broader implications of the circular economy — as well as how leading brands are leveraging this opportunity to reduce costs, increase design flexibility and boost product differentiation. Agenda: The cost and operational benefits of embracing circularity Key materials in circular packaging — including rPET and emerging bioplastics How to design a circular food and beverage package Strategies for selecting sustainable closures to future-proof packaging solutions Optimization and streamlining of production processes for enhanced efficiency How Husky Technologies can enable your sustainable success
Sustainability continues to dominate new additives technology, but upping performance is also evident. Most of the new additives have been targeted to commodity resins and particularly polyolefins.
There’s nothing small, however, about the capacity of these molding machines. Conrad says the first model on the market can mold parts weighing up to 70 lb and measuring 24 in. wide × 36 in. tall × 1 in. thick. Conrad likes to “spec” his machines conservatively. This month, he says, Omachron Plastics will mold PE parts up to 140 lb. The firm also has orders for parts measuring 12 × 12 × 6 in. And an accompanying photo shows molded HDPE 2 × 4 in. planks 4 ft long.
The machine with mold is about 3 × 7 ft—or about the footprint of a large office desk—and weighs around 2.5 tons without the mold. This is so compact that a molding operation can be established in a facility of 1000 to 2000 ft2, according to Conrad.
NPE2024: Absolute Haitian says Generation 5 of the servo-hydraulic Haitian and electric Zhafir machines lines emphasize efficiency, performance and intelligence.
Across the show, sustainability ruled in new materials technology, from polyolefins and engineering resins to biobased materials.
That said, not every plastic part is suitable to be rotomolded. “The part chooses the process, not the other way around – it depends on the function you want,” Marie-Michelle said. “Injection molding might be able to accommodate complex designs but it can’t create hollow products. And compared to blow molding, which does create hollow products, rotomolding offers denser walls and thicker corners, which some parts demand. So, if rigidity and strength are important – like for products that are meant to be used in rugged environments or places with high temperature – rotomolding might be the better choice.”
Mixed in among thought leaders from leading suppliers to injection molders and mold makers at the 2023 Molding and MoldMaking conferences will be molders and toolmakers themselves.
This month’s resin pricing report includes PT’s quarterly check-in on select engineering resins, including nylon 6 and 66.
technotrans says climate protection, energy efficiency and customization will be key discussion topics at PTXPO as it displays its protemp flow 6 ultrasonic eco and the teco cs 90t 9.1 TCUs.
After successfully introducing a combined conference for moldmakers and injection molders in 2022, Plastics Technology and MoldMaking Technology are once again joining forces for a tooling/molding two-for-one.
Discover how artifical intelligence is revolutionizing plastics processing. Hear from industry experts on the future impact of AI on your operations and envision a fully interconnected plant.
NPE2024: A slimmed-down version of Engel’s all-electric, e-mac injection molding machine is among eight displays, which also include LSR micromolding, quick mold changes and a cube mold.
The clamp and mold are typically much larger than the extruder. The machine is all-electric with a proprietary, ballscrew-driven clamp design. The clamp has 144 tons of closing force and 5 tons of opening force. “No individual part of the machine weighs more than 60 to 70 lb,” says Conrad. “And it’s totally modular, so parts are easy to replace.”
It can mold 70-lb parts 1 in. thick using 100% regrind, and it can reproduce micro surface detail. Add to that its small size, frugal energy consumption, and zero upfront cost.
Another benefit of the intrusion molding process is that it greatly reduces the equipment size needed to mold large parts. Three extruders are available for the plasticating section—1 in. diam., 18:1 L/D and 1.25 in., 24:1 or 36:1 L/D. With optimized screw designs and electric motors, they require only 2 to 5 hp to produce from 10-25 lb/hr for the smallest size up to 100-120 lb/hr.
In this collection of articles, two of the industry’s foremost authorities on screw design — Jim Frankand and Mark Spalding — offer their sage advice on screw design...what works, what doesn’t, and what to look for when things start going wrong.
This Knowledge Center provides an overview of the considerations needed to understand the purchase, operation, and maintenance of a process cooling system.
Join Engel in exploring the future of battery molding technology. Discover advancements in thermoplastic composites for battery housings, innovative automation solutions and the latest in large-tonnage equipment designed for e-mobility — all with a focus on cost-efficient solutions. Agenda: Learn about cutting-edge thermoplastic composites for durable, sustainable and cost-efficient battery housings Explore advanced automation concepts for efficient and scalable production See the latest large-tonnage equipment and technology innovations for e-mobility solutions
Manunor currently employs about 45 workers, has annual sales that exceed $10,000,000, and has a long list of North American customers, primarily in Quebec, Ontario, and the northeastern U.S. “We make more than 300 products in more than 20 sectors of activity, including kayaks, paddleboards, containers, tanks, indoor and outdoor toys and games, and parts for vehicles such as buses and ATVs,” Marie-Michelle said. “We do everything to make a finished part, from molding to assembling to packaging; and we’re very active in product and manufacturing process development, thanks to our team’s innovative spirit and expertise, which helps maintain a leading edge. The parts washer program that we developed in 2014, for example, is an in-house proprietary product that introduced an innovative solution to the market.”
Fast forward to today and the firm’s busy period continues basically uninterrupted save for a brief, unavoidable pause during the early days of the COVID-19 pandemic. Jacques St-Pierre has retired from Manunor – and he sold the assets of STP Equipment in 2005 to the Sacchi family, owners of Polivinil Spa, and they founded the new company of STP Rotomachinery – and Jacques’ daughter Marie-Michelle St-Pierre now serves as Manunor’s general director and CEO, having joined the firm in 2012. Unlike with some family-owned firms, however, her long-term involvement wasn’t a given. “I basically grew up at Manunor, working here on weekends and during summers while I was in high school, but I wasn’t sure about working here permanently,” Marie-Michelle said. “I studied mechanical engineering at Sherbrooke University and worked at co-op programs in a number of different businesses, big and small, in other sectors, because I wanted to see what opportunities were out there. So, when I finally decided to join Manunor after I graduated, I was fully committed.”
If that sounds like an attractive proposition, those are just a few of the benefits cited for a new line of low-pressure injection molding machines being launched by Omachron Technologies in Pontypool, Ont., a new name in plastics extrusion and molding machinery, headed by Wayne Conrad, who calls himself “chief scientist and also president.” Omachron recently came out with a line of small extruders (see last month’s Keeping Up section) that also serve as the plasticating section of its molding machines. After seven years in development, the first commercial models of those presses are being built now for a handful of initial customers. The company is expanding capacity to serve a broader molding audience by the end of the year.
Plastics processors are finding applications for 3D printing around the plant and across the supply chain. Here are 8 examples to look for at NPE2024.
Learn about sustainable scrap reprocessing—this resource offers a deep dive into everything from granulator types and options, to service tips, videos and technical articles.
Successfully starting or restarting an injection molding machine is less about ticking boxes on a rote checklist and more about individually assessing each processing scenario and its unique variables.
Multiple speakers at Molding 2023 will address the ways simulation can impact material substitution decisions, process profitability and simplification of mold design.
Omachron Technologies (omachrontechnologies.com) is the machine-building and moldmaking arm of Omachron Science, Conrad’s 30-year-old R&D company with 750 patents in fields as diverse as satellite communications, personal watercraft, and appliances (omachron.com). Another subsidiary is Omachron Plastics, which acts as a test bed for the company’s machinery, using it to produce the Plasti-Block line of machineable sheets, rods, tubes, blocks and custom shapes (plastiblocks.com).
Take a deep dive into all of the various aspects of part quoting to ensure you’ve got all the bases—as in costs—covered before preparing your customer’s quote for services.
Omachron’s machines are available for lease, not sale, so there is no upfront investment (except for molds and perhaps auxiliaries like water cooling). Typical monthly lease costs are $5000 to $6000 (USD).
For the uninitiated, rotomolding differs from other plastics processing methods like injection molding, thermoforming, and extrusion in that it works in layers. The virgin material and powdered colourant are poured into the mold; the mold is then closed tight, placed in an oven, and rotated at an even speed. In this way, the plastic is laid down in thin layers of even thickness, regardless of whether or not the mold features corners and curves. After the material is baked, the plastic is cooled inside the mold to ensure that it hardens evenly, and then extracted.
The company currently has seven rotomolding machines, all supplied by STP Rotomachinery. The newest machine, installed in August, is a rock n roll rotomolding machine with two sides and two completely independent arms, and is a total of 18 feet long with a 100-inch diameter. “It’s our longest rotomolding machine – and actually the longest currently being used anywhere in Quebec – and it fits between our largest rotomolder, which has a 120-inch diameter, and our smallest, which has an 80-inch diameter,” Marie-Michelle said. “We’ve always used STP machines – the company has a great reputation in the sector and it’s local as well, so parts and service are easy to obtain.”
On the other hand, these machines are not for fast-cycle molding. For large, thick parts, molding cycles can range from 10 min to 1 hr.
While prices moved up for three of the five commodity resins, there was potential for a flat trajectory for the rest of the third quarter.
Formnext Chicago is an industrial additive manufacturing expo taking place April 8-10, 2025 at McCormick Place in Chicago, Illinois. Formnext Chicago is the second in a series of Formnext events in the U.S. being produced by Mesago Messe Frankfurt, AMT – The Association For Manufacturing Technology, and Gardner Business Media (our publisher).
Across all process types, sustainability was a big theme at NPE2024. But there was plenty to see in automation and artificial intelligence as well.
Join KraussMaffei for an insightful webinar designed for industry professionals, engineers and anyone interested in the manufacturing processes of PVC pipes. This session will provide a comprehensive understanding of the technology behind the production of high-quality PVC pipes: from raw material preparation to final product testing. Agenda: Introduction to PVC extrusion: overview of the basic principles of PVC pipe extrusion — including the process of melting and shaping PVC resin into pipe forms Equipment and machinery: detailed explanation of the key equipment involved — such as extruders, dies and cooling systems — and their roles in the extrusion process Process parameters: insight into the critical process parameters like temperature, pressure and cooling rates that influence the quality and consistency of the final PVC pipes Energy efficiency: examination of ways to save material and energy use when extruding PVC pipe products
Coverage of single-use plastics can be both misleading and demoralizing. Here are 10 tips for changing the perception of the plastics industry at your company and in your community.
Exhibitors and presenters at the plastics show emphasized 3D printing as a complement and aid to more traditional production processes.
Join this webinar to explore the transformative benefits of retrofitting your existing injection molding machines (IMMs). Engel will guide you through upgrading your equipment to enhance monitoring, control and adaptability — all while integrating digital technologies. You'll learn about the latest trends in IMM retrofitting (including Euromap interfaces and plasticizing retrofits) and discover how to future-proof your machines for a competitive edge. With insights from industry experts, it'll walk you through the decision-making process, ensuring you make informed choices that drive your business forward. Agenda: Maximize the value of your current IMMs through strategic retrofitting Learn how to integrate digital technologies to enhance monitoring and control Explore the benefits of Euromap interfaces and plasticizing retrofits Understand how retrofitting can help meet new product demands and improve adaptability Discover how Engel can support your retrofitting needs, from free consultations to execution
Mold maintenance is critical, and with this collection of content we’ve bundled some of the very best advice we’ve published on repairing, maintaining, evaluating and even hanging molds on injection molding machines.
What if you could satisfy short- to medium-run injection molding needs with the capability of a 500-ton press, in a machine that uses one-tenth as much energy and can fit on a large office desk? What if you could do that with no capital investment for the machine? And what if that machine would allow you to mold 100% regrind into parts that are stronger than the virgin originals?
While the melting process does not provide perfect mixing, this study shows that mixing is indeed initiated during melting.
Resin drying is a crucial, but often-misunderstood area. This collection includes details on why and what you need to dry, how to specify a dryer, and best practices.
The Plastics Industry Association (PLASTICS) has released final figures for NPE2024: The Plastics Show (May 6-10; Orlando) that officially make it the largest ever NPE in several key metrics.
Say “manufacturing automation” and thoughts immediately go to the shop floor and specialized production equipment, robotics and material handling systems. But there is another realm of possible automation — the front office.
Rotomolding machines take up a lot of space, which cushioned the blow at Manunor slightly when the pandemic hit. “We didn’t have to shut any lines down or reconfigure our operations to create social distancing on the floor because our workers were already spread out,” Marie-Michelle said. “Like almost every other manufacturer in Quebec, we had to close for about five weeks in March-April 2020, at the very beginning of the pandemic, but after that we were able to carry on as usual.” And even during that forced lockdown, the company remained productive. “We worked with a customer to design an outdoor handwashing station that could be used safely during the pandemic,” Marie-Michelle said. “We designed the part, built the mold, and began rotomolding the product, all in six weeks. We’ve delivered about 3,000 units since then.”
Low power requirement also characterizes these machines, which can run on single-phase, 220V/80-89A power (or three-phase if desired).
Rotomolding also differs from other plastics processing methods as far as business strategy goes. “There really aren’t many rotomolding shops in Canada, or North America, so there’s enough room for everybody,” Marie-Michelle said. “Most of us belong to the Association of Rotational Molders, we all know each other, and we typically don’t compete against each other – we compete against manufacturers making products in other materials, such as metal, that are better suited to rotomolding. These are the new accounts that we want.” And even here, there’s a built-in limitation as to which new accounts to pursue, based on part dimensions and geography. “Rotomolded parts tend to be large and hollow, which makes them expensive to ship because you’re shipping a lot of air,” Marie-Michelle said. “So, it doesn’t make economic sense for us to pursue new business that’s too far away – in the southern U.S., for example, or western Canada. Rotomolders tend to stick to their own regions.”
Core Technology Molding turned to Mold-Masters E-Multi auxiliary injection unit to help it win a job and dramatically change its process.
Manunor was founded in 1993 by Jacques St-Pierre, who’s impact in the rotomolding world is considerable – he had previously founded Sherbrooke-based STP Equipment in 1988, which made independent-arm machines, fixed-arm machines, in-line shuttle machines, three- and four-sided sided shuttle machines, rocking ovens, lab machines, and a range of rotomolding accessories. Jacques St-Pierre was serving as Manunor’s CEO when Manunor entered a very busy period beginning in 2014, which is when it broke ground on its 10,000-square-foot expansion and also developed two new innovative products. The first was a parts washer to be used by machine shops and vehicle repair shops that was entirely designed and developed in Sherbrooke; with this equipment, oil and grease can be thoroughly cleaned without contaminants. The second was an innovative technology for rotomolding stand-up paddleboards for the Quebec-based manufacturer Pelican, and which began large-scale production in fall 2014.
In this collection, which is part one of a series representing some of John’s finest work, we present you with five articles that we think you will refer to time and again as you look to solve problems, cut cycle times and improve the quality of the parts you mold.
Any molder will tell you there’s a difference in working with electric vs. hydraulic drives. Servohydraulic is still hydraulic; a hybrid machine is something different. Imprecise use of terms causes needless confusion.
Omachron’s machines have molded LLDPE, HDPE, PP, rigid PVC, ABS, nylon, acetal, UHMW-PE, PEEK and PPS. Conrad says it’s possible to mold ABS, PVC and HDPE to very nearly the same dimensions in the same tool, regardless of the different materials’ shrinkage. That’s because his machines fill continuously during packing, through a heated inlet, so as to compensate for shrinkage during cooling in the mold.
Second quarter started with price hikes in PE and the four volume engineering resins, but relatively stable pricing was largely expected by the quarter’s end.
Despite price increase nominations going into second quarter, it appeared there was potential for generally flat pricing with the exception of a major downward correction for PP.
The aim of this presentation is to guide you through the factors and the numbers that will help you determine if a robot is a smart investment for your application. Agenda: Why are you considering automation? What problems are you trying to solve? How and why automation can help Crunch the numbers and determine the ROI
Marie-Michelle currently runs Manunor with her partner Mathieu Rouleau, who has been with Manunor as technical director since 2012. The couple became Manunor’s owners in 2017.
In this collection of content, we provide expert advice on welding from some of the leading authorities in the field, with tips on such matters as controls, as well as insights on how to solve common problems in welding.
Processors with sustainability goals or mandates have a number of ways to reach their goals. Biopolymers are among them.
In this three-part collection, veteran molder and moldmaker Jim Fattori brings to bear his 40+ years of on-the-job experience and provides molders his “from the trenches” perspective on on the why, where and how of venting injection molds. Take the trial-and-error out of the molding venting process.
Conrad says Omachron is building its first 10 commercial machines, which occupies its full production capacity right now. But next year it expects to expand to production of 50 to 100 machines.
GETTING A QUOTE WITH LK-MOULD IS FREE AND SIMPLE.
FIND MORE OF OUR SERVICES:
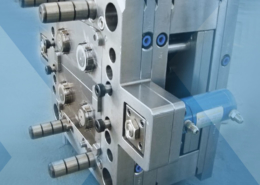
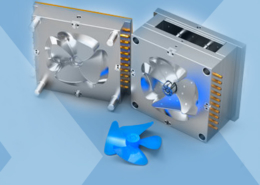
Plastic Molding

Rapid Prototyping
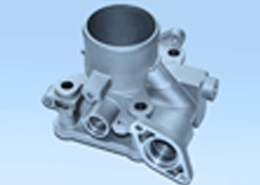
Pressure Die Casting
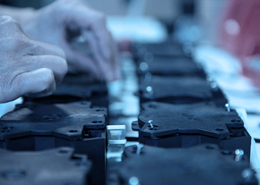
Parts Assembly
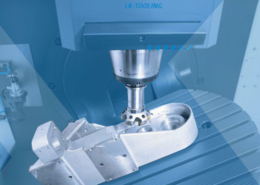