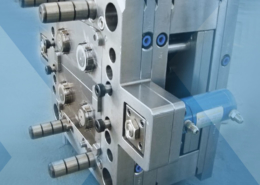
Unmanned Aerial System (UAS) Applies Injection Molded Chassis - peek injection m
Author:gly Date: 2024-09-30
Negri Bossi has sold a majority share of its business to Japanese injection moulding machinery manufacturer, Nissei Plastic Industrial Co., Ltd, for an undisclosed sum.
"This new partnership will elevate us to the status as one of the top ten suppliers worldwide for the supply of plastic injection moulding machines,” he added.
Nissei Plastic Industrial, which is engaged in the manufacture and sale of injection moulding machines, peripherical equipment, parts and dies, currently operates in three segments: Japan (active in purchase, manufacturing and sale of injection moulding machines and peripherical equipment), USA (engaged in the sale of products) and Asia (with China and Thailand affiliates focused on manufacturing and sales).
Fusible-core injection molding technology has been employed to mold a fuel housing for an aircraft using PEEK (polyetheretherketone) resin supplied by Victrex (West Conshohocken, PA). The solution reportedly delivers a 30% cost saving and up to 50% weight reduction versus existing metal designs.Processor Egmond Plastic was able to consolidate the number of parts using a carbon fiber reinforced grade of Victrex PEEK polymer. A separate bearing, for example, was eliminated since it is now integrated into the overall design of the housing.Fuel housing molded for CF-PEEK compound using fusible core process.Fuel housings for aerospace applications have very complex inner geometries which are not moldable using conventional injection molding technology. Egmond Plastic's fusible-core technology enables moldings of complex hollow housings, manifolds, and pipes. Richard Brandwijk, Managing Director at Egmond Plastic, explains: "Our technology, in combination with carbon fiber reinforced Victrex PEEK polymer, delivers numerous benefits. These include cost reduction, enhanced manufacturing speed, and weight reduction leading to improved fuel efficiency and reduced CO2 emissions. Along with part consolidation, this exceptional technology and material combination enables the design of very complex parts, beyond the capabilities of standard injection molding and metal processes."Utilizing a near net-shape manufacturing process for the fusible core allows for an 80% time saving versus machined parts. Further, secondary treatments for corrosion protection, such as anodizing, can be eliminated. Lead times can be reduced by 50%. These factors combine to deliver part cost savings of more than 30% versus metal equivalents."The global aerospace industry stands to gain enormously by persistently replacing metals in key applications, in which Egmond has demonstrated tremendous leadership," said Uwe Marburger, Aerospace Business Development Manager at Victrex. "Clearly, our PEEK knowledge and material solutions help enable the use of a technology that addresses some of the toughest challenges in complex aerospace part design and productions."Previously, the end-user had generally specified aluminum for the production of fuel containing parts, but a carbon fiber reinforced PEEK polymer demonstrated superior fatigue performance when compared to aluminum. It does this while meeting all the engineering requirements for this application, including stiffness, effective flame, smoke and toxicity (FST) performance, and resistance to aggressive chemicals, including notably, for this aerospace application, resistance to jet fuel and Skydrol hydraulic fluid. Parts can range in size all the way up to 30 cm x 30 cm x 40 cm (11.8 in x 11.8 in x 15.8 in), and typically the process is used for production runs of up to 2,000 parts.Egmond's unique fusible-core technology has already established a proven track record using Victrex PEEK in a fuel pump for the Eurofighter Typhoon, a jet fighter in use in several European countries. This pump has been in successful operational use for more than 20 years.
Nissei will also utilise the R&D and sales capabilities of Negri Bossi to expand its strengths in small and medium electric injection moulding machines.
Fusible-core injection molding technology has been employed to mold a fuel housing for an aircraft using PEEK (polyetheretherketone) resin supplied by Victrex (West Conshohocken, PA). The solution reportedly delivers a 30% cost saving and up to 50% weight reduction versus existing metal designs.Processor Egmond Plastic was able to consolidate the number of parts using a carbon fiber reinforced grade of Victrex PEEK polymer. A separate bearing, for example, was eliminated since it is now integrated into the overall design of the housing.
“We are, and will continue to, be Negri Bossi with our machines and our people as that is what our customers want,” Ward said in a statement. “The only difference now is that we have a strong industrial partner behind us who understands our market and whom can support us in order to better service our customer’s needs.”
The move comes as both companies look to combine their strengths in different regional markets, as well as combine machinery portfolios and technical knowledge.
“In terms of product they have a history of direct lock machines whilst we have always been known for our toggle machines. We are able to offer high tonnage machines were as they currently only go to 1300 ton whilst they are able to offer to market vertical machines.
By acquiring a stake in Negri Bossi, Nissei will be able to expand and strengthen its business footprint in the injection moulding machinery.
Negri Bossi, which has a particularly strong presence in Europe as well as the USA, Mexico and India, offers a range of high-performance injection moulding machines, amongst which are ultra-large injection moulding machines and moulding systems.
“Consolidated sales of the Nissei group will hit approximately 50 billion Japanese yen (€420 million). In addition to the integration of production, sales and service, we will be able to achieve further growth through global marketing with robot companies.”
The transaction is expected to close in January 2020 and will see Negri Bossi’s parent company, Kingsbury Corp, retain a minority stake in the company.
Mr Yoda, President and Representative Director of Nissei commented: “Negri Bossi is a well-established injection moulding machine manufacturer in Italy with more than 70 years of history, and this acquisition will enable respective business enhancement based on a reciprocally complementing relationship by geographical and product type perspective.
Ward added: “The strategic choice to purchase Negri Bossi was based on very strong potential synergies such as our strong geographical footprint in Europe and East coast of America compared to theirs of the Far east, Asia and west coast of America.
GETTING A QUOTE WITH LK-MOULD IS FREE AND SIMPLE.
FIND MORE OF OUR SERVICES:
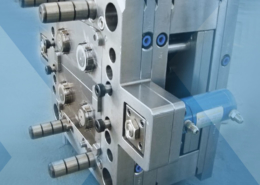
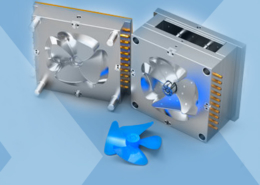
Plastic Molding

Rapid Prototyping
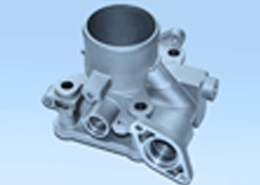
Pressure Die Casting
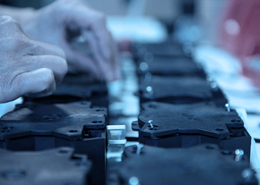
Parts Assembly
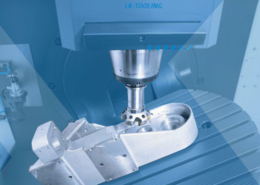