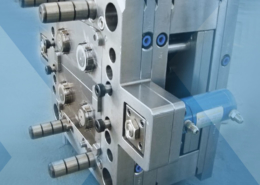
Unlock Extra Storage Space With These Under-Bed Boxes That Hide Clutter and
Author:gly Date: 2024-09-30
End-of-life car bumpers are converted into a raw material that is used in the production of new chassis vibration- and noise-attenuation components.
Ursula Nollenberger, Product Line Director for LSR Components at Trelleborg Sealing Solutions, says: "Our first application of this revolutionary technology is for a leading automotive tier-one supplier. The company was looking for a solution to visually differentiate geometrically identical parts that Trelleborg produces off a single tool for various vehicle platforms, without impacting the overall aesthetics of the finished product. This new process offered an ideal solution that was both practical and cost-effective."
Ultra-Poly, one of America's largest plastics recyclers, has announced a first-of-its-kind bumper recycling program, that involves the collection and reprocessing of damaged automotive bumpers into a new raw material for use in an auto component. Ultra-Poly collaborated with Tier 1 Autoneum North America to develop a product that uses the recycled bumper material as a rigid backing substrate for a fibrous layer, creating a composite used in vibration and noise attenuation in a chassis component. The material is listed in the International Material Data System (IMDS).
Jarno Burkhardt, General Manager of the Trelleborg Sealing Solutions European center of excellence for LSR component solutions in Stein am Rhein, Switzerland, comments: "The advantage of the two-colored LSR components to our customer, as well as to the OEM they supply, is that it gives, without adding significant extra cost, product traceability. The beauty of the novel tool design is that it will allow an unlimited number of color combinations from a single machine, in a single tool and in one single shot."
"This novel technology can be applied to any size and number of cavities per tool. Depending on part geometry and size as well as production capacity needed, we construct tools anywhere between 1 and 128 cavities with possibilities even beyond," adds Nollenberger.
"Expertise in tool design is fundamental to our core competences within Trelleborg Sealing Solutions," emphasizes Jarno. "Developing the two-color process required additional considerations during the design and construction of the tool to make sure the flow of the clear and the colored material portions must be kept strictly separated.
Leveraging a strong history in developing novel reverse logistics strategies, Ultra-Poly collects the used bumper covers directly from auto body shops, where they have been removed from vehicles and stripped of any usable connected components. The program offers a strong value to the shops, including;
The recycled material is now available to be sampled and used by any automotive manufacturer or supplier for other potential programs.
The resulting material offers strong value to converters and brand owners as well, including a consistent high-quality material with a balance of stiffness and toughness, and certified 100% post-consumer content.
The two-color injection molding process has been simplified through a development at Trelleborg Sealing Solutions (Stuttgart, Germany) that employs a single shot and a single tool to manufacture partially colored liquid silicone rubber (LSR) components. Utilizing an innovative and proprietary tool construction, the process has the capability to add color pigment to part of the transparent silicone material stream just prior to its injection into the tool cavity.
Autoneum North America Inc. Vice President of Product Development and Engineering, Dan Moler, added: “With the increasing challenge of OEMs to require more and more recycled content, this product delivers on that challenge, enabling us to become more sustainable as a company by reducing our carbon footprint and engineering a product from the ground up with end-of-life recycling in mind to ultimately reach the end goal of a circular economy. Everyone benefits — body shops, recyclers, automotive part manufacturers, OEMs and, most importantly, the environment.”
“This is a groundbreaking program that will help advance the automotive industry closer to achieving the standards of a circular economy,” said Kevin Cronin, vice president of sustainability and R&D at Ultra-Poly. “Sustainability is in the DNA of Ultra-Poly. Our commitment and expertise in improving the sustainability of the plastics industry is evident throughout our business model and we look forward to all that we can achieve with this innovative program.”
The two-color injection molding process has been simplified through a development at Trelleborg Sealing Solutions (Stuttgart, Germany) that employs a single shot and a single tool to manufacture partially colored liquid silicone rubber (LSR) components. Utilizing an innovative and proprietary tool construction, the process has the capability to add color pigment to part of the transparent silicone material stream just prior to its injection into the tool cavity.
Industry integrity – the used fascia are completely destroyed in the process and cannot be repaired and make their way back into the supply stream, which presents significant quality issues.
As a member of the Plastics Industry Association, the company was one of several that worked on the End-of-Life Vehicle (ELV) project, which sought to determine if the fascia material could be recovered for use in new fascia. Ultimately, this was deemed not viable, primarily because of surface finish issues. However, Ultra-Poly saw potential for the material in other polypropylene compounds as well as in non-appearance applications in the automotive and other industrial markets.
The process involves the two components of LSR raw material being mixed in a ratio of 1:1. On the way into the injection tool, this homogenous mass is then divided. Color is added via an additional mixing unit to one part of the volume stream and injected into the tool cavity via a proprietary valve design. Simultaneously, the colorless material is being injected via a second stream.
GETTING A QUOTE WITH LK-MOULD IS FREE AND SIMPLE.
FIND MORE OF OUR SERVICES:
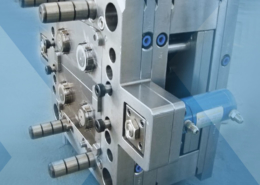
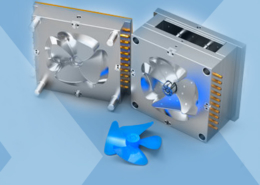
Plastic Molding

Rapid Prototyping
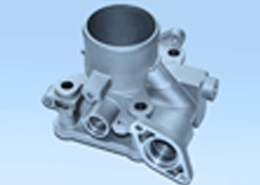
Pressure Die Casting
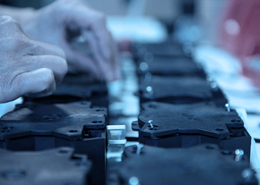
Parts Assembly
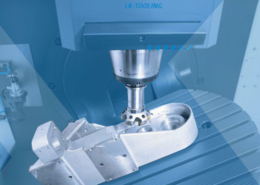