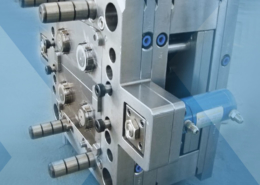
Ultrasonic cleaning technology extends injection mold life - injection molding m
Author:gly Date: 2024-09-30
During this webinar, the audience will be introduced to a variety of fiber composite technologies — as well as the machines and equipment — from short fibers to continuous fibers, from thermoset to thermoplastic, as well as the according process technology, including a special focus on long-fiber injection (LFI) and structural composite spray (SCS). Focus markets include automotive, aviation and AAM, transportation, and construction. This webinar will provide a detailed overview of according application examples. Agenda: Long fiber injection (LFI) Structural composite spray (SCS) Resin transfer molding (RTM), wet compression molding, etc. Pultrusion FiberForm
“Testing final products by enveloping the structure using a little more than critical design to loads is the current methodology, at least for high-performance bikes,” Stier says. Clarifying this statement, he explains that a bike is normally designed to handle loads 1.5 or two times greater than those expected. So if the part is loaded for mechanical testing at, say, 1.3 times the design load, and it does not break, “you have proven its structural integrity, which is worth more than analysis, which could always be flawed due to the nature of assumptions,” Stier offers.
Base Materials introduces a high-performance, toughened epoxy tooling board designed for thermoforming and vacuum forming processes, direct-to-part applications and more.
This technical demonstrator of HyperSizer Express frame geometry for an optimized hardtail mountain bike shows a layup of 0°/90°/±45° tape plies. The ply schedule is designed to meet typical requirements for performance bike frames, including ply-based strength criteria (Ref: Tsai-Hill, Tsai-Wu, Tsai-Hahn) as well as pedaling stiffness requirements (transverse bottom bracket deflection) for efficiency, and head tube stiffness requirements (transverse head tube deflection) for handling.
The first project is underway to recover carbon fiber used in an A330-200 aircraft, which will then be regenerated for other end uses by HRC.
Powered by an 85% air/15% pure polyimide aerogel, Blueshift’s novel material system protects structures during transient thermal events from -200°C to beyond 2400°C for rockets, battery boxes and more.
For its production Alfa all-road bike, Allied uses about 1m2 of 150-g/m2 Innegra prepreg weave in areas of the bike “that are at high risk of impact,” says Pickman. But the majority of the layup, he says, is 150-g/m2 standard-modulus UD prepreg (Mitsubishi Composite Materials Div., Irvine, CA, US). For its coming Alfa X, “we are using the 166-g/m2 TeXtreme/Innegra as the outermost ply for the entire bike, with the base layup as 110-g/m2 intermediate-modulus UD Mitsubishi fiber, both prepreg.”
All of this is very appealing to riders, says Dr. Scott W. Beckwith, president of BTG Composites Inc. (Taylorsville, UT, US) and the global technical director for the Society for the Advancement of Materials and Process Engineering (SAMPE, Diamond Bar, CA, US).
Steps bike designers and manufacturers must take to keep high-performance carbon fiber bikes safe, upright and on the road or trial.
HyperWorks is used by Argon18 “to reduce cost and time during the development of a bike frame,” says Legay (Fig. 1). “It allows us to develop optimized products that we could not get by test and trial-and-error only.”
A combination of Airtech’s 3D printing materials and Ascent’s production capabilities aim to support increased use of composite additive tooling in spaces like defense and aerospace.
Prepreg co-molding compound by IDI Composites International and A&P Technology enables new geometries and levels of strength and resiliency for automotive, mobility.
This collection details the basics, challenges, and future of thermoplastic composites technology, with particular emphasis on their use for commercial aerospace primary structures.
9T Labs used Additive Fusion Technology to iterate CFRTP designs, fully exploit continuous fiber printing and outperform stainless steel and black metal designs in failure load and weight.
Additive technology creates air pockets in film during orientation, cutting down on the amount of resin needed while boosting opacity, mechanical properties and recyclability.
The Marservis PROeco is a mass transportation marine vessel using Bcomp natural fiber for interior parts in place of standard materials.
The Plastics Industry Association (PLASTICS) has released final figures for NPE2024: The Plastics Show (May 6-10; Orlando) that officially make it the largest ever NPE in several key metrics.
The nearly infinite material design possibilities for a composite structure, however, make traditional design approaches — even those that involve standard computer aids — time-consuming and potentially subject to failure. But there are design solutions available today that offer software platforms that can simulate and optimize fiber architecture and ply shapes that will meet bicycle OEM specifications.
During this CW Tech Days event, sponsored by Composites One, experts will offer presentations to review and evaluate the composite materials, processes and applications that should and will be considered for use in the infrastructure and construction markets.
The composites industry plays a crucial role in developing lightweight and durable materials for a range of applications, including those critical to national defense. One key focus area is the development of advanced structural materials and manufacturing technologies that support next-generation space, missile and aircraft systems for the U.S. Department of Defense (DOD). ARC Technologies LLC (ARC), a division of Hexcel Corporation, based in Amesbury, Massachusetts, is a provider of advanced composites structures, specialty materials and other unique products that provide the U.S. Department of Defense with advanced capabilities to protect service members while in harm’s way. This team’s specialty is to understand a specific need from a program office, PEO, platform manufacturer or other offices within the DOD. With that understanding, the team can design a solution, develop a prototype for test and evaluation, perform extensive in-house testing — including electromagnetic, environmental and structural testing — and then partner with the customer through platform evaluation. The Hexcel Amesbury division has a team of engineers on staff, including mechanical, chemical, electrical and research and development specialists that can provide design, testing and manufacturing capabilities to service customer requirements from concept through production. This presentation will illustrate capabilities in advanced composites and other specialty materials structures, focusing on the Hexcel Amesbury team's niche in electromagnetic signature reduction and other unique capabilities.
Learn about sustainable scrap reprocessing—this resource offers a deep dive into everything from granulator types and options, to service tips, videos and technical articles.
HyperWorks’ design optimization solution, OptiStruct (Altair Engineering, Troy, MI, US), reduced the frame weight of Rolo Bikes’ (Linköping, Sweden) road bike from 829g to 792g (see next image).
In this collection of articles, two of the industry’s foremost authorities on screw design — Jim Frankand and Mark Spalding — offer their sage advice on screw design...what works, what doesn’t, and what to look for when things start going wrong.
Plastics Technology covers technical and business Information for Plastics Processors in Injection Molding, Extrusion, Blow Molding, Plastic Additives, Compounding, Plastic Materials, and Resin Pricing. About Us
The aim of this presentation is to guide you through the factors and the numbers that will help you determine if a robot is a smart investment for your application. Agenda: Why are you considering automation? What problems are you trying to solve? How and why automation can help Crunch the numbers and determine the ROI
Third is stiffness. “Stiffness is so important because it is a matter of energy,” Bressan says. “You react fast when you need to react, you push the bicycle and all the energy that you put into the bike becomes your speed. So the stiffness becomes a priority.” A bicycle with inadequate stiffness — for example, one made using low-modulus carbon fibers — can deform as the rider pumps on the pedals and pulls up on the handlebars to climb a hill or increase speed. When the bicycle deforms, some of the rider’s energy is lost. Bressan explains, “The material absorbs that energy and instead of having energy that pushes you, and you go faster, you lose part of that energy.”
Successfully starting or restarting an injection molding machine is less about ticking boxes on a rote checklist and more about individually assessing each processing scenario and its unique variables.
Despite price increase nominations going into second quarter, it appeared there was potential for generally flat pricing with the exception of a major downward correction for PP.
An on-demand mapping tool for anisotropic materials and polymer material fracture prediction model, i-Lupe, aims to help predict impact, crash behaviors.
American Bureau of Shipping (ABS) certifies use of jointly developed CFRP repair technique on FPSO and FSO industrial systems, addressing traditional steel restoration challenges.
The HyperWorks platform also was successfully used by composite bike design specialist Gridlayer LLC (Denver, CO, US) in the design of the Alfa all-road bike for Allied Cycle Works/HIA-Velo (Little Rock, AR, US) (Fig. 2) “A composite bicycle must ride great and provide adequate comfort for the rider while meeting safety standards. HyperWorks allows us to optimize and verify the laminate design long before material or tooling is cut,” says Gridlayer founder and owner Chris Meertens. “Once tooling is made, you are locked in.” (Fig. 3.)
CompPair and Composite Recycling introduce a roof scoop made of recycled fibers to an eco-efficient rally buggy, which channels airflow to the engine for optimal, sustainable performance.
This sidebar to CW’s August 2024 feature article reviews this technology for more efficient composites manufacturing and why it aligns with Koridion active core molding.
The second priority is weight, which Bressan points out depends on the fiber direction, or fiber architecture. “Every single tube on a bicycle works differently — some working more in torsion, others more in bending and still others working more in compression, for example,” he explains. Fiber architecture can be optimized for these loads. “This is the beauty of using composite materials compared to aluminum or titanium or metals in general, because the material itself is variable.”
technotrans says climate protection, energy efficiency and customization will be key discussion topics at PTXPO as it displays its protemp flow 6 ultrasonic eco and the teco cs 90t 9.1 TCUs.
Courses being offered include both injection molding training at LS Mtron’s Technical Center, and onsite injection molding training at LS Mtron customer locations. Peter Gardner, business director of LS Mtron USA, said his company is offering Orbital’s training as part of new machine sales, with all new LS Mtron machine sales in 2022 eligible to register for a free seat at one of the upcoming Wood Dale seminars. Those lectures include: Courses for Fundamentals of Scientific Injection Molding: Hands-on, Setup, Processing, & Troubleshooting (March 1-3, June 7-9, and December 12-14) and Thermoplastic Part Design, Part Defects & Scientific Injection Molding (September 13–14). Orbital recently moved its test molds to LS Mtron’s Technical Center.
While the major correction in PP prices was finally underway, generally stable pricing was anticipated for the other four commodity resins.
An overview of ASTM Standard Guide D8509, and its coupon-level mechanical testing of design properties for analyzing composite bolted joints.
The fourth and final consideration is safety. Optimization of material and manufacturing choices to best support specified critical load and performance targets is also the road to safer operation, Bressan says. And what defines optimum for a particular bike model depends to a significant degree on our first design factor, its intended purpose or use: A mountain bike cannot be designed perilously close to the breaking point like a Tour de France racing bike, to optimize stiffness and weight savings, when it must survive impacts on protruding stones as its rider pushes up and flies down steep winding trails. Instead, its strength and flexibility must be maximized to preserve both bike and rider. Similarly, that road bike now for sale in the bike shops, styled and painted to look for all the world like the racing bike that took the winner’s cup in last year’s Big Race, must be beefed up and can’t weigh as little as its namesake if it is to survive thousands of miles of sometimes rough pavement, when that similar-looking championship bike was expected to perform in but a single race series. Further, any structural defects, especially at removable part joints, reduce stiffness and strength in the regions of the defects and affect not only performance but rider safety. Steps must be taken to prevent such defects and provide for adequate manufactured part inspection.
In a time where sustainability is no longer just a buzzword, the food and beverage packaging industry is required to be at the forefront of this innovation. By adopting circular packaging processes and solutions, producers can meet regulatory requirements while also satisfying consumer demand and enhancing brand reputation. Join Husky to learn more about the broader implications of the circular economy — as well as how leading brands are leveraging this opportunity to reduce costs, increase design flexibility and boost product differentiation. Agenda: The cost and operational benefits of embracing circularity Key materials in circular packaging — including rPET and emerging bioplastics How to design a circular food and beverage package Strategies for selecting sustainable closures to future-proof packaging solutions Optimization and streamlining of production processes for enhanced efficiency How Husky Technologies can enable your sustainable success
The ITHEC 2024 will take place from the 9 to 10 October 2024 in Bremen, Germany. At the 7th International Conference, more than 300 participants from around the world will be presenting and discussing newest scientific results, meet leading international specialists, share their expertise and start business co-operations in the field of thermoplastic composite technologies. The international exhibition will feature 40+ exhibitors showcasing all steps of the supply-chain. Be it materials, machines, testing, processes, or solutions. By combining the exhibition and the conference ITHEC is further fostering the inter-connectivity between science and industry.
Reliable news and information on where and how fiber-reinforced composites are being applied — that’s just the start of what you get from our team here at CompositesWorld.
Because part failure at the speeds and road conditions experienced in today’s cycling domain can be catastrophic for both bike and rider, nondestructive testing (NDT) of individual components and even the final bicycle can help identify and reduce defects in the manufacturing process.
Foundational research discusses the current carbon fiber recycling landscape in Utah, and evaluates potential strategies and policies that could enhance this sustainable practice in the region.
Plastics Technology’s Tech Days is back! Every Tuesday in October, a series of five online presentations will be given by industry supplier around the following topics: Injection Molding — New Technologies, Efficiencies Film Extrusion — New Technologies, Efficiencies Upstream/Downstream Operations Injection Molding — Sustainability Extrusion — Compounding Coming out of NPE2024, PT identified a variety of topics, technologies and trends that are driving and shaping the evolution of plastic products manufacturing — from recycling/recyclability and energy optimization to AI-based process control and automation implementation. PT Tech Days is designed to provide a robust, curated, accessible platform through which plastics professionals can explore these trends, have direct access to subject-matter experts and develop strategies for applying solutions in their operations.
Aerospace manufacturer joins forces with composite materials company to achieve sustainable manufacturing practices that overcome traditional composite layup tooling.
Prepreg co-molding compound by IDI Composites International and A&P Technology enables new geometries and levels of strength and resiliency for automotive, mobility.
Across all process types, sustainability was a big theme at NPE2024. But there was plenty to see in automation and artificial intelligence as well.
Whether you’re exploring new applications or seeking to gain a foothold in emerging markets, Carbon Fiber 2024 is where you’ll discover the insights and connections needed to shape your business strategy. Register now.
Epoxies can be “toughened” via the addition of rubber compounds. Epoxy suppliers can provide them toughened in the formulation process. But bicycle designers and manufacturers are discovering ways to incorporate the mix of thermosets and thermoplastics into their design processes. For example, Jen Hanna, director of business development for Innegra Technologies (Greenville, SC, US), says Innegra high-modulus polypropylene (HMPP) UD and woven fiber has become a thermoplastic constituent of choice for some bicycle manufacturers. When mixing thermoplastics with thermoset matrices, however, cure cycles need to be carefully considered. “We recommend processing temps below 150°C [302°F]. Innegra works very well in a 250°F [121°C] prepreg.” She adds that that would present a challenge to the bike manufacturer on a quest for quicker cure cycles, which often means higher temperatures, noting that in that scenario, “Innegra would struggle to be a fit.” But a small sacrifice in production speed can be a good trade-off for the benefits that HMPP brings to bicycle performance. “The ductile nature and excellent flex-fatigue properties allow the material to withstand impacts, reduce vibrations and limit or stop fracture propagation in composite parts,” she points out, “creating a safer cycling product.”
This collection features detail the current state of the industry and recent success stories across aerospace, automotive and rail applications.
In this collection, which is part one of a series representing some of John’s finest work, we present you with five articles that we think you will refer to time and again as you look to solve problems, cut cycle times and improve the quality of the parts you mold.
Formnext Chicago is an industrial additive manufacturing expo taking place April 8-10, 2025 at McCormick Place in Chicago, Illinois. Formnext Chicago is the second in a series of Formnext events in the U.S. being produced by Mesago Messe Frankfurt, AMT – The Association For Manufacturing Technology, and Gardner Business Media (our publisher).
LS Mtron’s Technical Center in Wood Dale, Ill. will be home to injection molding training by Umberto Catignani of Orbital Plastics Consulting thanks to a new partnership. Photo Credit: LS Mtron
Low-melt polyaryletherketone (LMPAEK) unidirectional tapes provide outstanding thermal and fire protection, demonstrating their effectiveness through rigorous testing. These tapes are fire, smoke and toxicity compliant with FAR25.853 and meet OSU Heat Release Rate standards. The tapes were tested under ISO 2685/AC 20-135 Change 1, meeting the fireproof criteria. Additionally, they met UL 2596 requirements for battery thermal runaway tests. These tapes are crucial for high-temperature applications showcasing their resilience and safety in both aerospace and automotive applications. Part of a broader range that includes films and compounds, Victrex LMPAEK materials are valued for their excellent processability and weldability. They offer versatile solutions for complex needs beyond traditional structural parts, such as: thermal runaway and lightning strike protection, heat sinking, and intricate bracketry. Victrex LMPAEK materials facilitate automation and high-rate production while addressing performance and sustainability challenges. With reduced environmental impact, lower weight and cost-efficiency, they meet the evolving demands of the transportation industry and support innovative design solutions. Agenda: Introduction to LMPAEK ecosystem, highlighting unidirectional tapes Thermal and fire protection performance: applications and benefits Material forms and processability Sustainability and efficiency Conclusion and future innovations
Oxeon AB (Borås, Sweden) says its thin TeXtreme spread-tow carbon fiber tapes make it possible to replace a 4-ply UD layup (left) with one symmetrical fabric ply (right) containing the same number of plies but facilitating much easier drapability on curved surfaces and in tubular constructions.
Kennametal will cover the influence of different composite materials characteristics on drilling performance and how to optimize the process. Agenda: Who is Kennametal? Hole making challenges in composite materials Innovations for hole making applications Upcoming events and academic partnerships
That said, the International Organization for Standardization (ISO, Zurich, Switzerland) published its ISO 4210 standard for bicycles in 2014 and 2015 in nine sections. ISO 4210 was “developed in response to demand throughout the world, and the aim has been to ensure that bicycles manufactured in compliance with this International Standard will be as safe as is practically possible [editor’s italics]. The scope has been limited to safety considerations and has specifically avoided standardization of components,” according to ISO.
Here then, CW, with help from Dr. Beckwith, presents some accumulated wisdom from those who have taken seriously the unique challenges presented by the design and manufacture of composite bike components. The starting point, of course, is design.
Prepreg co-molding compound by IDI Composites International and A&P Technology enables new geometries and levels of strength and resiliency for automotive, mobility.
Exhibitors and presenters at the plastics show emphasized 3D printing as a complement and aid to more traditional production processes.
Take a deep dive into all of the various aspects of part quoting to ensure you’ve got all the bases—as in costs—covered before preparing your customer’s quote for services.
Sam Pickman, director of product/engineering for Allied Cycle Works/HIA-Velo, emphasizes the advantages of selectively adjusting the ratio and composition of carbon and thermoplastic fiber content in the layup to pinpoint the desired between performance/weight/cost balance for each bike model. “For a laminate that has its eye on price,” he notes, “we use a combination of standard-modulus UD [carbon fiber] prepreg in 150-g/m2 weight, a quasi-isotropic stack from Vectorply Corp. [Phenix City, AL, US], and Innegra in key locations to add damage tolerance and toughness.”
To build a super-lightweight layup that takes advantage of thermoplastic fatigue- and damage-tolerance benefits, Pickman uses an intermediate-modulus 100-g/m2 UD prepreg with a TeXtreme/Innegra hybrid material to add toughness.
The JEC Forum DACH is a business meetings event organised by JEC The JEC Forum DACH is organised on October 22 and 23, 2024 by JEC, in partnership with the AVK, gathering the composite materials community from the DACH Region (Germany, Austria and Switzerland).
Say “manufacturing automation” and thoughts immediately go to the shop floor and specialized production equipment, robotics and material handling systems. But there is another realm of possible automation — the front office.
Fig. 1a: Material placed precisely — and only — where needed The thickness of the composite frame for the Argon18 (Montreal, QC, Canada) Krypton endurance bike — it is as thin as 0.5 mm in some locations — was optimized using the Altair HyperMesh simulation software platform (see next image). Source | Argon18
This session is designed to demonstrate the benefits of ultra polymers for aerospace applications with real case examples of Syensqo's polymer portfolio. Agenda: Introduction to ultra polymers (PAEK, PEKK, PEEK, PAI) key features Application of ultra polymers in aerospace: concrete examples Benefits of ultra polymers: enhanced performance, durability and cost-efficiency
Advanced Engineering is the UK’s largest annual gathering of engineering and manufacturing professionals. The event will help you to source new suppliers, network, build connections and learn about the latest industry developments all in one place. Get involved and exhibit alongside 400+ exhibitors offering solutions and products across all industries and sectors to help improve your productivity and inspire creativity. With over 9,000+ of your peers due to attend and ready to network with and inspire you, this is the event you can’t afford to miss!
CompositesWorld's Carbon Fiber conference offers you cutting-edge information and access to industry experts in streamlining manufacturing costs, market outlooks and forecasting, and more. You will make invaluable contacts as you meet and network with the industry's most innovative and influential leaders at Carbon Fiber. __PRESENT
Continuous fiber-reinforced thermoplastic composite targets full circularity in aircraft interior applications, with FST, impact resistance and toughness features.
Thermoplastics may enable bike parts to better handle temperature swings in very hot or cold climates: “Innegra is stable on cryogenic levels down to -90°C [-130°F] and probably further,” Hanna notes. “We have tested to that degree and saw absolutely no change in mechanical properties. On the higher end, 165°F [74°C] is the melt temperature.” She quips, “I hope no one is cycling in that climate!”
Stephen Heinz, vice president of R&I for Syensqo delivered an inspirational keynote at SAMPE 2024, highlighting the significant role of composite materials in emerging technologies and encouraging broader collaboration within the manufacturing community.
Cevotec, a tank manufacturer, Roth Composite Machinery and Cikoni, have undertaken a comprehensive project to explore and demonstrate the impact of dome reinforcements using FPP technology for composite tanks.
The first major design factor is the purpose of the bike: Different uses impose different design imperatives. Pierre Legay, structural and CFD analyst for bike manufacturer Argon18 (Montreal, QC, Canada) explains, for example, that “low weight and high pedaling stiffness are required for race bikes, aerodynamics will be more critical for triathlon bikes, and good comfort will be required for endurance road bikes.”
Initial demonstration in furniture shows properties two to nine times higher than plywood, OOA molding for uniquely shaped components.
Second-ever PTXPO will feature a robust education program on flexible film, with more technical programming in the works.
Multiple speakers at Molding 2023 will address the ways simulation can impact material substitution decisions, process profitability and simplification of mold design.
One result of the simulation process was that hundreds of prepreg patches give the bike a stiff bottom bracket to improve pedaling efficiency, but a compliant seatpost to improve comfort. (Graphic color key: dark red areas thicker, dark blue thinner, as low as 0.5mm in some locations).
How the predictive tool “CZone” is applied to simulate the axial crushing response of composites, providing valuable insights into their use for motorsport applications.
HyperWorks’ design optimization solution, OptiStruct (Altair Engineering, Troy, MI, US), reduced the frame weight of Rolo Bikes’ (Linköping, Sweden) road bike from 829g to 792g. Final weight after additional tweaks by Rolo’s manufacturing team in OptiStruct is just 710g (also see short.compositesworld.com/RoloBikeFR). The graphic shows the ply direction for layup of tubes around the gear hub.
Resources exist, and are also readily available. “ASTM, in particular the D30 Composite Materials Committee, has decades of test methods at their disposal for determining (a) composite material design allowables, (b) state of actual cure, and (c) verification of fiber-resin void contents,” Beckwith points out. “Yet the majority of bicycle manufacturing companies never seem to use them in their design processes.”
Sustainability continues to dominate new additives technology, but upping performance is also evident. Most of the new additives have been targeted to commodity resins and particularly polyolefins.
After successfully introducing a combined conference for moldmakers and injection molders in 2022, Plastics Technology and MoldMaking Technology are once again joining forces for a tooling/molding two-for-one.
Stier says, “So far, the unchallenged frontrunner for composite high-performance bikes is unidirectional (UD) carbon fiber combined with epoxy thermosets in their various combinations.” But Stier and others point out that this combination, by itself, makes a fairly brittle composite. And that, left unmitigated, can be a safety risk. That brittleness, however, can be offset by adding thermoplastics in some form to the composite. “Their higher strain energy release rate (or toughness) might reduce the conservatism demanded from the rather brittle carbon epoxies and, thus, yield more safety due to increased fatigue- and damage-tolerance,” he suggests.
The composites industry is increasingly recognizing the imperative of sustainability in its operations. As demand for lightweight and durable materials rises across various sectors, such as automotive, aerospace, and construction, there is a growing awareness of the environmental impact associated with traditional composite manufacturing processes.
Resin drying is a crucial, but often-misunderstood area. This collection includes details on why and what you need to dry, how to specify a dryer, and best practices.
Processors with sustainability goals or mandates have a number of ways to reach their goals. Biopolymers are among them.
Given the market’s growth projections, composite bicycles will certainly proliferate anywhere riders value high performance. Admired for their benefits in high-performance bikes, composites also must command careful attention from those who design and manufacture them. In time, standards and regulations will find their proper place, but this industry can’t wait. Tools for design, testing and post-production evaluation of bikes that can keep their riders satisfied and safer are available, but bicycle builders must put them to use and support ongoing development of best practices.
Beckwith, who also serves as an expert witness in forensic investigations involving composite failures in road-bike structures, observes, “I have not seen a stress analysis, or set of material strength allowables or an applied safety factor for any of roughly 50 carbon fiber high-performance bike failures.” That needs to change, he insists: “Manufacturing, structural analysis, quality control, testing and inspection are all important considerations in controlling a very labor-intensive molding and composites manufacturing process.”
CW’s editors are tracking the latest trends and developments in tooling, from the basics to new developments. This collection, presented by Composites One, features four recent CW stories that detail a range of tooling technologies, processes and materials.
TeXtreme is used by bike manufacturer Masi Bikes (Vista, CA, US) for its new frames and forks, reducing fabric weight by 100 g/m2 while improving stiffness. “The goal wasn’t to just make the frame lighter, we also wanted to make it a bit smoother without giving up any drivetrain stiffness. The material is so thin, we could work with several plies to get the same thickness or less, resulting in significant improvements,” says Masi’s product manager James Winchester.
Over the last 8 months, Archer Aviation has completed a total of 402 test flights with its composites-intensive aircraft, adding to key milestones.
While prices moved up for three of the five commodity resins, there was potential for a flat trajectory for the rest of the third quarter.
Join this webinar to explore the transformative benefits of retrofitting your existing injection molding machines (IMMs). Engel will guide you through upgrading your equipment to enhance monitoring, control and adaptability — all while integrating digital technologies. You'll learn about the latest trends in IMM retrofitting (including Euromap interfaces and plasticizing retrofits) and discover how to future-proof your machines for a competitive edge. With insights from industry experts, it'll walk you through the decision-making process, ensuring you make informed choices that drive your business forward. Agenda: Maximize the value of your current IMMs through strategic retrofitting Learn how to integrate digital technologies to enhance monitoring and control Explore the benefits of Euromap interfaces and plasticizing retrofits Understand how retrofitting can help meet new product demands and improve adaptability Discover how Engel can support your retrofitting needs, from free consultations to execution
In this collection of content, we provide expert advice on welding from some of the leading authorities in the field, with tips on such matters as controls, as well as insights on how to solve common problems in welding.
Recoat temperature, part orientation and bead geometry are some key design variables to consider for a successful and reliable large-format additive manufacturing (LFAM) process.
In these sessions, experts will discuss the emerging hydrogen economy and the opportunities for composites in this lucrative space.
Second quarter started with price hikes in PE and the four volume engineering resins, but relatively stable pricing was largely expected by the quarter’s end.
Beckwith, however, questions this method’s reliability, noting that in most cases, there is an absence of detailed structural analyses. Loading the part for mechanical testing can induce internal manufacturing voids and delaminations that may approach critical fracture levels, he points out. Further, “Static loads do not account for braking loads, which induce high frictional heat and induced loads on wheels and forks. And long-term service fatigue definitely needs to be considered, as well as vibration loads imposed over time on any composite components.”
Join KraussMaffei for an insightful webinar designed for industry professionals, engineers and anyone interested in the manufacturing processes of PVC pipes. This session will provide a comprehensive understanding of the technology behind the production of high-quality PVC pipes: from raw material preparation to final product testing. Agenda: Introduction to PVC extrusion: overview of the basic principles of PVC pipe extrusion — including the process of melting and shaping PVC resin into pipe forms Equipment and machinery: detailed explanation of the key equipment involved — such as extruders, dies and cooling systems — and their roles in the extrusion process Process parameters: insight into the critical process parameters like temperature, pressure and cooling rates that influence the quality and consistency of the final PVC pipes Energy efficiency: examination of ways to save material and energy use when extruding PVC pipe products
Fabio Bressan, manager composite materials and virtual engineering for Solvay Composite Materials (Alpharetta, GA, US), affirms that, contending, “The best way is not to build a physical prototype but to build a computer prototype” that simulates the actual product. “Simulation is a special environment where you can increase the complexity of your imagination or the way you want to invent a new design.” He sees simulation as a bridge between materials and manufacturing — important because a composite material design is only as good as its manufacturability.
LS Mtron Injection Molding Machines USA (Peachtree Corners, Ga.), the U.S. subsidiary of the Korean machine supplier, has announced a partnership with Orbital Plastics Consulting (Atlanta) to provide scientific injection molding training. The hands-on courses will be taught by Umberto Catignani, president of Orbital Plastics Consulting, and take place at LS Mtron’s Technical Center in Wood Dale, Ill.
Gifted with extraordinary technical know how and an authoritative yet plain English writing style, in this collection of articles Fattori offers his insights on a variety of molding-related topics that are bound to make your days on the production floor go a little bit better.
This Knowledge Center provides an overview of the considerations needed to understand the purchase, operation, and maintenance of a process cooling system.
Thousands of people visit our Supplier Guide every day to source equipment and materials. Get in front of them with a free company profile.
Closed mold processes have many advantages over open molding. In this knowledge center, learn the basics and vital tools needed to produce parts accurately.
However, HIA-Velo’s Pickman warns that NDT isn’t enough. “You can learn some things from NDT, but to really learn through development, we test to failure, then cut the parts up to inspect the molding quality.”
In the Automated Composites Knowledge Center, CGTech brings you vital information about all things automated composites.
Arris presents mechanical testing results of an Arris-designed natural fiber thermoplastic composite in comparison to similarly produced glass and carbon fiber-based materials.
Mold maintenance is critical, and with this collection of content we’ve bundled some of the very best advice we’ve published on repairing, maintaining, evaluating and even hanging molds on injection molding machines.
Performing regular maintenance of the layup tool for successful sealing and release is required to reduce the risk of part adherence.
Six U.S. companies have proven their recycling technologies for composites and rare earth elements, and will be supported for relevant scale demonstration and validation.
Bike gear manufacturer PRO (Eindhoven, The Netherlands) makes its PRO Vibe handlebars with the same material. Weighing 220g, PRO Vibe carbon fiber composite handlebars are now the lightest in the PRO line up, and Innegra fibers “strengthen the bar’s most vulnerable areas without compromising its weight, so your handlebar is ready to ride in the harshest conditions,” Pro states.
The geometry of the bike, mostly dictated by function and style, and the scale of the series (produced units), are also design factors that “dominate the balance between the emphasis on ease (and cost) of manufacturing and structural performance,” Stier says. “An enormous amount of data, techniques and constraints all contribute in a major way to restrict and define the design problem, which is the reason why composites optimization software can play a crucial part in design solutions.”
Formnext Chicago is an industrial additive manufacturing expo taking place April 8-10, 2025 at McCormick Place in Chicago, Illinois. Formnext Chicago is the second in a series of Formnext events in the U.S. being produced by Mesago Messe Frankfurt, AMT – The Association For Manufacturing Technology, and Gardner Business Media (our publisher).
Jetcam’s latest white paper explores the critical aspects of nesting in composites manufacturing, and strategies to balance material efficiency and kitting speed.
From AFP hydrofoils to more efficient aircraft parts, Avel uses digital design, multiprocess production and a rule-breaking approach for complex 4D composites.
Bressan identifies four equally important goals for every commercial design. First is cost. Bressan, whose background includes Formula One and America’s Cup composite racecar and yacht designs, emphasizes that the first design goal is to consider the cost not only of the material itself, but “everything you design, the complexity you bring.”
Beckwith notes further that no legally binding structural safety standards yet exist that address common rider load and environmental conditions (braking, impact loads, fatigue, vibration, material aging or degradation, material abrasion and wear) for high-performance composite bikes. Further, the existing ASTM D-30 test methods are not yet recognized by ASTM’s F-08 Bicycle Committee.
Additionally, stitch-bonded non-crimp fabrics (NCFs) provide manufacturers and asset owners even more ways to gain a competitive advantage with products built specifically for the environments and loading conditions in which they will be utilized. Join Vectorply Corporation and Creative Composites Group (CCG) for this in-depth webinar detailing the process of engineering NCFs to build composite parts that will stand the test of time. Unlike steel, concrete and wood, composite NCFs can be optimized utilizing various fiber types, architectures and substrates to achieve the specific goals of their application efficiently. High corrosion resistance, strength and stiffness, and longevity can all be accomplished with custom-designed laminates for these heavily abused applications. Vectorply Vice President of Engineering Trevor Gundberg and Creative Composites Group Chief Sales Officer Dustin Troutman will share their industry-leading expertise on the process of laminate design and part production. Attendees can expect to learn when to use composite NCFs in their production process and the wide range of fiber-reinforced plastic (FRP) composites that Creative Composites Group produces for the industrial and infrastructure markets. Whether you want to learn more about utilizing NCFs in your production process or why CCG’s extensive product line may be the choice for your project, this webinar is the place learn the process and how to take the next steps. Agenda: Distinct advantages of non-crimp fabrics versus alternative materials How to design laminates for specific processes such as pultrusion and infusion Real-world success spotlights of NCFs in industrial applications
Explore the cutting-edge composites industry, as experts delve into the materials, tooling, and manufacturing hurdles of meeting the demands of the promising advanced air mobility (AAM) market. Join us at CW Tech Days to unlock the future of efficient composites fabrication operations.
While prices moved up for three of the five commodity resins, there was potential for a flat trajectory for the rest of the third quarter.
In this three-part collection, veteran molder and moldmaker Jim Fattori brings to bear his 40+ years of on-the-job experience and provides molders his “from the trenches” perspective on on the why, where and how of venting injection molds. Take the trial-and-error out of the molding venting process.
CompositesWorld’s Tech Days: Design, Simulation and Testing Technologies for Next-Gen Composite Structures is designed to provide a multi-perspective view of the state of the art in design, simulation, failure analysis, digital twins, virtual testing and virtual inspection.
Mixed in among thought leaders from leading suppliers to injection molders and mold makers at the 2023 Molding and MoldMaking conferences will be molders and toolmakers themselves.
TeXtreme spread-tow carbon fiber reinforcements from Oxeon AB (Borås, Sweden) also are being used to reduce weight and improve performance under load — especially to protect laminates from micro-cracking. Fredrik Ohlsson, product development director for Oxeon, explains: “By mixing and varying the layup sequence, by combining thicker materials (standard tow) and thinner materials (spread tow), it is possible to load a composite in its transverse direction to a much higher degree before cracks occur in the matrix between the filaments.” This is reportedly a great advantage in bicycles, where each push of the pedal induces a cyclic load path in multiple directions through the bike frame.
These design factors and solutions guide selection of the best materials for the bike’s purpose. Materials suppliers provide the tested property values of their products, which then can be entered into design software at the constituent, raw materials level. But it’s also necessary to determine the strength of the cured part, through coupon testing, which is the next design level after individual fiber/resin constituents.
Across the show, sustainability ruled in new materials technology, from polyolefins and engineering resins to biobased materials.
Innegra prepreg weave adds impact resistance in this standard UD prepreg layup for the Alfa all-road bike, built by Allied Cycle Works/HIA-Velo (Little Rock, AR, US).
New aircraft is expected to deliver wind turbine blades from 105 meters up to expand the reach of wind energy and achieve global climate goals.
EU project will develop bio-based, repairable and recyclable vitrimer composites and advanced sensors for highly reliable, sustainable wind blades.
Thermoplastics for Large Structures, experts explored the materials and processing technologies that are enabling the transition to large-part manufacturing.
Validation of 80-100% tensile strength and comparability to injection molding via Voxelfill extrusion process was achieved through plastic and fiber-filled test series.
Join Engel in exploring the future of battery molding technology. Discover advancements in thermoplastic composites for battery housings, innovative automation solutions and the latest in large-tonnage equipment designed for e-mobility — all with a focus on cost-efficient solutions. Agenda: Learn about cutting-edge thermoplastic composites for durable, sustainable and cost-efficient battery housings Explore advanced automation concepts for efficient and scalable production See the latest large-tonnage equipment and technology innovations for e-mobility solutions
“Sectioning [breaking] carbon fiber forks, which represent 82% of observed failures,” says Beckwith, “often clearly shows significant leading and trailing edge porosity, voids and delamination incurred during the molding process.”
The composites-intensive VTOL platform is next expected to undergo a series of test flights in various conditions to validate its performance, safety and reliability, leading up to eventual certification.
Thousands of people visit our Supplier Guide every day to source equipment and materials. Get in front of them with a free company profile.
Ultradent's entry of its Umbrella cheek retractor took home the awards for Technical Sophistication and Achievement in Economics and Efficiency at PTXPO.
How the predictive tool “CZone” is applied to simulate the axial crushing response of composites, providing valuable insights into their use for motorsport applications.
Join Wittmann for an engaging webinar on the transformative impact of manufacturing execution systems (MES) in the plastic injection molding industry. Discover how MES enhances production efficiency, quality control and real-time monitoring while also reducing downtime. It will explore the integration of MES with existing systems, emphasizing compliance and traceability for automotive and medical sectors. Learn about the latest advancements in IoT and AI technologies and how they drive innovation and continuous improvement in MES. Agenda: Overview of MES benefits What is MES? Definition, role and brief history Historical perspective and evolution Longevity and analytics Connectivity: importance, standards and integration Advantages of MES: efficiency, real-time data, traceability and cost savings Emerging technologies: IoT and AI in MES
Beckwith cites this type of corner cutting, done by bike manufacturers to decrease costs, as the type of major mistake that can lead to part failure and accidents on the road. “The majority of bike manufacturers assume that the materials of construction and the process is forgiving because, almost always, only the outside surfaces are visually observable upon removal from the processing mold, but this is a risky assumption.”
This month’s resin pricing report includes PT’s quarterly check-in on select engineering resins, including nylon 6 and 66.
While the melting process does not provide perfect mixing, this study shows that mixing is indeed initiated during melting.
Another design software choice for composite bicycles is Collier’s HyperSizer. Computer-aided engineering (CAE) software that couples with finite element analysis to analyze and optimize structures, HyperSizer is a NASA-spinoff software originally conceived for the aerospace industry. (Fig 4.)
After an accident, Bressan recommends C-scan tomography inspection of the part. Although he acknowledges that it is a very expensive procedure, he maintains, “Tomography allows you to check each layer and see what is happening between the materials.”
Program will focus on sustainable, next-gen wing solutions, including in wing design and manufacturing and advancements in carbon fiber-reinforced composite materials.
Making something out of (almost) nothing is an ‘eye opener’ for youngsters in their first exposure to plastics processing.
Oxeon spreads 12K (and greater) carbon tows, and reportedly can tailor biaxial or hybridized plies, or other UD or multi-directional fabric materials. The company works closely with its customers to help identify and optimize customer requirements. Ohlsson says the spread-tow fabrics also drape better than standard UD tapes around double curvatures or square shapes, yet still present the mechanical performance of cross-plied UDs. He adds, “We can tailor the fabric to change a four-ply UD layup into one fabric ply, possibly with different amounts of fiber in warp and weft, that gives exactly the requisite number of 0° and 90° fibers while still presenting a symmetrical layup.” (Fig. 5.)
When, how, what and why to automate — leading robotics suppliers and forward-thinking moldmakers will share their insights on automating manufacturing at collocated event.
Increasingly, prototype and production-ready smart devices featuring thermoplastic composite cases and other components provide lightweight, optimized sustainable alternatives to metal.
Among other simulation platforms, Bressan has used HyperMesh, a HyperWorks product from Altair Engineering (Troy, MI, US). Jeffrey Wollschlager, Altair’s senior director, composites technology, explains that Altair “took topology optimization technology that was originally developed for isotropic metals and adapted it to directional composite anisotropic materials.” Its multi-scale simulation features reach down to design levels of individual fiber and resin constituents, allowing the designer to “design-tune not only the structure but also the material,” as well as offer manufacturing simulation capability that enables the user to simulate draping individual plies onto the tooling, he says.
Celebrating National Composites Week 2024, CW looks at how composites are being used to provide the next generation of energy.
While the world continues to wait for new single-aisle program announcements from Airbus and Boeing, it’s clear composites will play a role in their fabrication. But in what ways, and what capacity?
Mike Sepe has authored more than 25 ANTEC papers and more than 250 articles illustrating the importance of this interdisciplanary approach. In this collection, we present some of his best work during the years he has been contributing for Plastics Technology Magazine.
Whether you’re exploring new applications or seeking to gain a foothold in emerging markets, Carbon Fiber 2024 is where you’ll discover the insights and connections needed to shape your business strategy. Register now.
Global market research firm Lucintel (Dallas, TX, US) predicts that the worldwide bicycle market will be worth US$59.9 billion by 2021, with CAGR of 2.4% from 2016 to 2021. Although bicycles with carbon fiber composites frames and other components will no doubt still account for a small percentage of that market’s upper end, it is clear that bicycle manufacturers are increasingly turning to carbon fiber composites for the advantages they offer. Compared to aluminum bikes, those made with carbon fiber are extremely lightweight, have greater strength and stiffness and damp vibration better due to the viscoelastic nature of resin matrices. Further, they are more responsive in terms of handling and feel, and, because they are molded, they can be made more aesthetically attractive, with striking texture choices.
Introduced by Zeiger and Spark Industries at the PTXPO, the nozzle is designed for maximum heat transfer and uniformity with a continuous taper for self cleaning.
Bressan agrees. “Honestly, with the first prototype, we just destroy the part. We cut the part in sections and see what we can see inside, to be sure the technology is working properly.” Even then, he adds, there are physical limitations. Even when the part is destroyed, one may not be able to verify everything.
“Its purpose defines the bike’s loads and functionality, defines environmental variables and structural performance and safety targets,” emphasizes Bertram Stier, research engineer, advanced composites, for Collier Research Corp. (Newport News, VA, US).
Explore the technologies, materials and strategies used by composites manufacturers working in the evolving space market.
Recoat temperature, part orientation and bead geometry are some key design variables to consider for a successful and reliable large-format additive manufacturing (LFAM) process.
ARRK Engineering and Mitsui Chemicals improved delamination prediction accuracy to help optimize absorbed energy/failure load for an overmolded TAFNEX CF/PP UD tape bumper beam.
The machine supplier and plastics consultancy will provide hands-on courses taught by Orbital’s Umberto Catignani that take place at LS Mtron’s Technical Center near Chicago.
Most defects in composite structures — in the present case, frames, front forks, handlebars and other bike components — are invisible until the part fails.
CompositesWorld is the source for reliable news and information on what’s happening in fiber-reinforced composites manufacturing. About Us
Core Technology Molding turned to Mold-Masters E-Multi auxiliary injection unit to help it win a job and dramatically change its process.
A report on the demand for hydrogen as an energy source and the role composites might play in the transport and storage of hydrogen.
CW Tech Days are virtual events dedicated to the topics impacting the composites industry today. Access past event recordings and register for upcoming Tech Days.
The composite tubes white paper explores some of the considerations for specifying composite tubes, such as mechanical properties, maintenance requirements and more.
Herone, Spiral RTC, Teijin Carbon Europe and Collins Aerospace Almere recycle A350 thermoplastic composite clips/cleats waste into rods for the all-thermoplastic composite Multifunctional Fuselage Demonstrator’s crown.
The DOMMINIO project combines AFP with 3D printed gyroid cores, embedded SHM sensors and smart materials for induction-driven disassembly of parts at end of life.
Knowing the fundamentals for reading drawings — including master ply tables, ply definition diagrams and more — lays a foundation for proper composite design evaluation.
There is a caveat, of course: Composite parts and structures cannot be designed or built in the same ways used to conceive and construct amorphous metallic parts. Composite materials are typically anisotropic. That is, their strength and other mechanical properties are directional rather than uniform — the load-carrying capacity of the composite is optimal in the direction(s) of fiber orientation. This, of course, provides a great advantage to the designer, but also is a source of aggravation in that the designer must select carefully from what has become a vast array of composite material possibilities to best meet a manufacturer’s specific bike performance requirements.
Discover how artifical intelligence is revolutionizing plastics processing. Hear from industry experts on the future impact of AI on your operations and envision a fully interconnected plant.
Commingling TeXtreme spread tow with Innegra’s HMPP fiber endows the part with higher elongation and ductility. “If you have a catastrophic failure of the composite part, it stays together because of the higher elongation fibers,” Ohlsson contends. “If there is a failure in a handlebar, the composite does not break completely but stays held together, minimizing the risk to hit your nose on the ground. Instead you could still maintain control of the bike until full stop.”
CompositesWorld’s CW Tech Days: Infrastructure event offers a series of expert presentations on composite materials, processes and applications that should and will be considered for use in the infrastructure and construction markets.
August 29-30 in Minneapolis all things injection molding and moldmaking will be happening at the Hyatt Regency — check out who’s speaking on what topics today.
Analyzing structural resonance of the aircraft under various loads becomes a critical step in obtaining flight certification.
GETTING A QUOTE WITH LK-MOULD IS FREE AND SIMPLE.
FIND MORE OF OUR SERVICES:
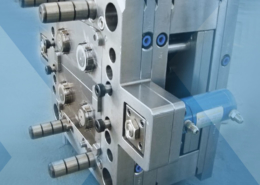
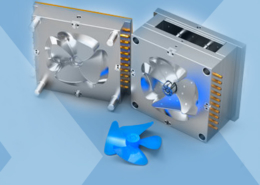
Plastic Molding

Rapid Prototyping
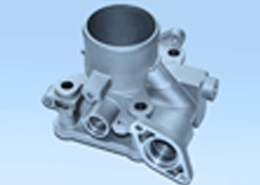
Pressure Die Casting
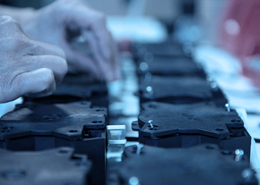
Parts Assembly
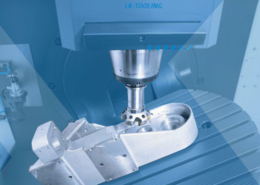