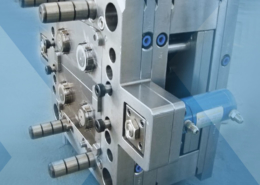
UK to see 4.5 billion pieces of BBQ plastic waste this summer - billion injectio
Author:gly Date: 2024-09-30
The combination of pharmaceutical and technological expertise makes Braunform an important partner for medical production. At Fakuma 2024, the mould maker will be presenting an injection mould that reflects the company’s know-how in an impressive way.
I understand that I can revoke my consent at will. My revocation does not change the lawfulness of data processing that was conducted based on my consent leading up to my revocation. One option to declare my revocation is to use the contact form found at https://contact.vogel.de. In case I no longer wish to receive certain newsletters, I have subscribed to, I can also click on the unsubscribe link included at the end of a newsletter. Further information regarding my right of revocation and the implementation of it as well as the consequences of my revocation can be found in the data protection declaration, section editorial newsletter.
Newsletter content may include all products and services of any companies mentioned above, including for example specialist journals and books, events and fairs as well as event-related products and services, print and digital media offers and services such as additional (editorial) newsletters, raffles, lead campaigns, market research both online and offline, specialist webportals and e-learning offers. In case my personal telephone number has also been collected, it may be used for offers of aforementioned products, for services of the companies mentioned above, and market research purposes.
I hereby consent to Vogel Communications Group GmbH & Co. KG, Max-Planck-Str. 7/9, 97082 Würzburg, Germany, including any affiliated companies according to §§ 15 et seq. AktG (hereafter: Vogel Communications Group) using my e-mail address to send editorial newsletters. A list of all affiliated companies can be found here
By clicking on „Subscribe to Newsletter“ I agree to the processing and use of my data according to the consent form (please expand for details) and accept the Terms of Use. For more information, please see our Privacy Policy.
The Braunform MED Mold is a concept for the safe use of injection moulds in cleanrooms, which is based on the company's more than 25 years of experience in medical technology and production in cleanrooms. It was specifically developed for medical and pharmaceutical applications and takes into account the challenges of the use of injection molds in cleanrooms. This standard defines in detail various mold specifications and their use according to ISO cleanroom classes. The team of specialists at Braunform fully integrated the MED Mold standard into the company in June 2010. With this know-how, the company offers its customers in the medical technology industry low wear and low particle injection moulds and — if required — safe and efficient production of plastic articles.
At Fakuma, Braunform will be presenting an 8-cavity injection mould that has been specifically designed for the production of insulin pen housings. The 8-cavity pilot mould made it possible to test and optimise the article and mould design and ultimately resulted in a 32-cavity production mould. Thanks to synchronised mechanical movements in combination with a horizontal article, direct injection with valve gate is possible. The injection mould is characterised by a high level of user-friendliness. Production is efficient and precise. The additional ejector stage controls the movement of two mini slides. A very space-saving and compact design is achieved as a result.
In case I access protected data on Internet portals of Vogel Communications Group including any affiliated companies according to §§ 15 et seq. AktG, I need to provide further data in order to register for the access to such content. In return for this free access to editorial content, my data may be used in accordance with this consent for the purposes stated here.
Naturally, we always handle your personal data responsibly. Any personal data we receive from you is processed in accordance with applicable data protection legislation. For detailed information please see our privacy policy.
This portal is a brand of Vogel Communications Group. You will find our complete range of products and services on www.vogel.com
Imprint Cookie-Manager About Media Subscription cancellation Privacy General Terms and Conditions Help AI-Guidelines
The technology and design of the mould are based on two core competences of Braunform: Lift&Strip² technology and the MED Mold standard, which is established in the company since 2010. The Lift&Strip² technology ensures that the movement initiated by the machine ejector lifts and strips the article at the same time. This innovative solution optimises the production process and increases production efficiency. This technology makes it easier to operate the stripping strip and reduces the cycle time. Thanks to a movable forced guidance system, the stripping strip moves synchronously with the mould opening. Previously, the mould was opened and the stripping strip was actuated with a separate drive. Now this drive is no longer required and two processes are combined into one.
GETTING A QUOTE WITH LK-MOULD IS FREE AND SIMPLE.
FIND MORE OF OUR SERVICES:
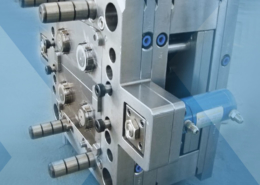
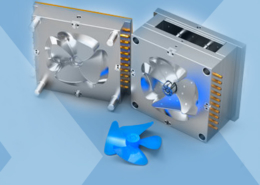
Plastic Molding

Rapid Prototyping
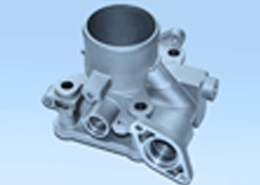
Pressure Die Casting
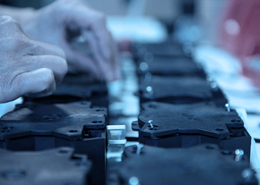
Parts Assembly
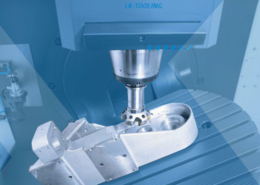