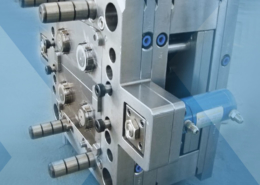
Short Shot Molding: Optimizing Injection Molding Processes
Author:gly Date: 2024-06-08
Short shot molding stands as a pivotal technique within the realm of injection molding, offering a multitude of advantages in terms of efficiency, cost-effectiveness, and quality control. This article delves into the intricacies of short shot molding, providing readers with a comprehensive understanding of its principles, applications, and implications for modern manufacturing practices.
Unveiling the Concept of Short Shot Molding
Short shot molding, also known as undersized shot molding or incomplete filling molding, involves injecting a predetermined amount of molten material into a mold cavity that is insufficient to completely fill the cavity. This deliberate limitation of material volume serves various purposes, including the creation of specific part geometries, optimization of material usage, and mitigation of defects such as sink marks and warpage. Short shot molding represents a strategic approach to achieving precise control over part dimensions, surface finish, and mechanical properties.
Historical Evolution
The evolution of short shot molding can be traced back to the early days of injection molding, where practitioners sought innovative solutions to address challenges such as part shrinkage, warpage, and dimensional instability. Over time, advancements in mold design, material science, and process optimization have contributed to the refinement and widespread adoption of short shot molding techniques across diverse industries. Today, short shot molding stands as a cornerstone of modern manufacturing, enabling manufacturers to achieve unparalleled levels of precision and efficiency in part production.
Key Principles and Mechanisms
Short shot molding relies on a combination of key principles and mechanisms to achieve desired outcomes. By carefully controlling the injection speed, pressure, and duration, molders can regulate the flow of molten material into the cavity, ensuring that only a predetermined portion is injected before the mold closes. This controlled filling process minimizes the risk of overpacking, flash formation, and other common defects associated with conventional injection molding. Furthermore, the strategic placement of gates, vents, and cooling channels facilitates uniform material distribution and rapid solidification, enhancing part quality and dimensional stability.
Applications and Advantages
Short shot molding finds widespread applications across various industries, ranging from automotive and aerospace to electronics and medical devices. One common application is the production of thin-walled parts with intricate geometries, where precise control over material distribution is critical to achieving optimal performance. Additionally, short shot molding is employed in the manufacturing of components with varying wall thicknesses, complex features, and tight tolerances. The ability to tailor material usage to specific requirements results in significant cost savings, reduced cycle times, and enhanced part quality.
Case Studies and Success Stories
Numerous case studies and success stories underscore the transformative impact of short shot molding on manufacturing operations. For instance, in the automotive industry, the adoption of short shot molding has enabled manufacturers to produce lightweight components with superior strength-to-weight ratios, contributing to fuel efficiency and emissions reduction. Similarly, in the electronics sector, short shot molding has facilitated the miniaturization of electronic devices and the integration of advanced features, driving innovation and market differentiation. These real-world examples highlight the versatility and effectiveness of short shot molding in meeting the evolving demands of modern production environments.
Future Perspectives and Innovations
Looking ahead, the future of short shot molding is ripe with possibilities for innovation and advancement. Continued research into material science, mold design, and process optimization promises to unlock new opportunities for enhancing the efficiency, reliability, and sustainability of short shot molding techniques. Furthermore, the integration of digitalization, automation, and additive manufacturing technologies will enable manufacturers to further streamline production processes, accelerate time-to-market, and expand the horizons of part design and functionality.
Conclusion
In conclusion, short shot molding represents a paradigm shift in injection molding, offering unprecedented levels of control, precision, and efficiency in part production. By leveraging strategic material usage and precise process control, manufacturers can achieve superior part quality, minimize waste, and optimize production costs. As we navigate the dynamic landscape of modern manufacturing, the adoption of short shot molding techniques holds the key to unlocking new opportunities for innovation, competitiveness, and sustainability. By embracing this transformative approach, manufacturers can stay ahead of the curve and meet the challenges of tomorrow's marketplace with confidence and ingenuity.
GETTING A QUOTE WITH LK-MOULD IS FREE AND SIMPLE.
FIND MORE OF OUR SERVICES:
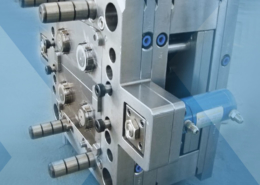
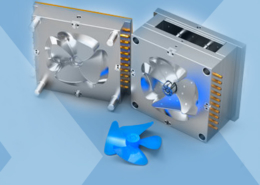
Plastic Molding

Rapid Prototyping
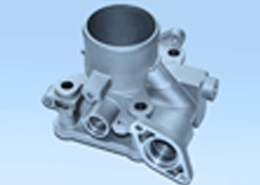
Pressure Die Casting
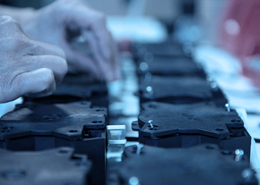
Parts Assembly
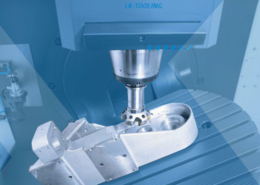