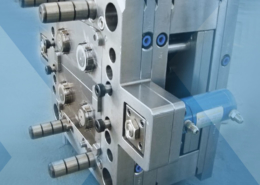
Twin-sheet thermoforming offers advantage over blow molding for 3D air ducts - o
Author:gly Date: 2024-09-30
An overview of ASTM Standard Guide D8509, and its coupon-level mechanical testing of design properties for analyzing composite bolted joints.
The number of NFC materials available has grown in recent years, but Texonic’s Juillard notes that one hurdle of NFC development continues to be limitations in processing compared to traditional fiber materials. Although natural fiber materials can be manufactured via a variety of processes, with common methods being prepreg layup/autoclave cure, compression molding and RTM, unique challenges remain.
Prepreg co-molding compound by IDI Composites International and A&P Technology enables new geometries and levels of strength and resiliency for automotive, mobility.
This session is designed to demonstrate the benefits of ultra polymers for aerospace applications with real case examples of Syensqo's polymer portfolio. Agenda: Introduction to ultra polymers (PAEK, PEKK, PEEK, PAI) key features Application of ultra polymers in aerospace: concrete examples Benefits of ultra polymers: enhanced performance, durability and cost-efficiency
One is that natural fibers absorb resin differently than other fiber types — “like sponges,” as Juillard describes. For this reason, he says a manufacturing process such as compression molding, RTM or other vacuum-assisted process that introduces pressure during consolidation is needed for optimum results. He adds, “If you try to do wet layup with no pressure, you won’t be able to control the resin-to-fiber ratio [with NFCs].”
Jeff Green, president and CEO of US Merchants, grew his business alongside the warehouse club stores that emerged in the ‘80s. Photo Credit: US Merchants
Filament winding with NFCs. Companies continue to expand the processing capabilities of NFCs from prepregs and infusion, such as Autonational's R&D work on filament winding with flax fiber/bio-based resin. Photo Credit: Autonational
Increasingly, prototype and production-ready smart devices featuring thermoplastic composite cases and other components provide lightweight, optimized sustainable alternatives to metal.
As WEAV3D worked in this area, it became clear that because thermoplastics are involved, the processing window was “very narrow,” Oberste explains. The melt temperature of the polypropylene commonly used in the company’s products is only 10 to 15°F lower than the top temperature the natural fibers can survive. The WEAV3D process is an adhesive-free technology that relies on heating the tape to the resin’s melt temperature in order to bond it to the material the lattice is being made to reinforce. Therefore, “the amount of heat and how fast [the tape] moves through the heating zone have to be very carefully controlled, so that you don’t have degradation of the fiber during processing.”
“We don’t make mistakes because we’re trying to cut corners to make a larger margin. If I give you a better price, it’s coming out of my margin, never out of the quality of the product.”
The Plastics Industry Association (PLASTICS) has released final figures for NPE2024: The Plastics Show (May 6-10; Orlando) that officially make it the largest ever NPE in several key metrics.
Discover how artifical intelligence is revolutionizing plastics processing. Hear from industry experts on the future impact of AI on your operations and envision a fully interconnected plant.
When Plastics Technology visited US Merchants’ original Ontario facility where those first seven injection molding machines are still molding totes, the packaging/logistics side of the operation was packing up everything from skateboards and boots to batteries and bags, with finished pallets marked for delivery to New Zealand, Japan, China and destinations beyond. Forklifts navigated a towering maze of shrink-wrapped pallets ready to be loaded onto trucks, including Green’s own. The full scope of the operations is a bit overwhelming, but it all makes sense to Green. “To an outside person,” Green says, “it looks very convoluted, but the truth of the matter is it’s like a jigsaw puzzle — everything fits into place.”
Across all process types, sustainability was a big theme at NPE2024. But there was plenty to see in automation and artificial intelligence as well.
The market for NFCs has come a long way in the past 10 years, but efforts continue to ready the natural fiber supply chain, materials and processes for more widespread adoption by manufacturers.
Several suppliers, including Bcomp and Terre de Lin’s manufacturing branch TDL Technique, are also working on natural fiber materials that are suited for use with thermoplastic resin systems. Carlson notes that as more thermoplastic-based NFCs are developed, recycling will likely become more viable, as thermoplastics can be heated, softened and reshaped via injection molding or extrusion.
Even further, NFCs in the mobility space may some day soon take to the skies, transitioning into aircraft interiors applications. Aeroflax, an aerospace-grade flax fiber/bio-based resin product developed by Lufthansa Technik (Hamburg, Germany) with Bcomp’s ampliTex and powerRibs flax fiber reinforcements, is said to be at technology readiness level (TRL) 5 or 6, with the potential to increase sustainability and reduce weight in aircraft ceiling panels, door frame linings and more.
After several initial prototypes of table legs and chairs done at Autonational’s R&D center, the commercial filament winding line was delivered to Vepa at the end of 2022.
CompPair and Composite Recycling introduce a roof scoop made of recycled fibers to an eco-efficient rally buggy, which channels airflow to the engine for optimal, sustainable performance.
In automotive interiors, a variety of companies are beginning to get involved — and some have been in the space for many years. For example, global automotive supplier Faurecia (Nanterre, France), part of the Forvia Group, has been working on automotive interiors for decades and announced a number of new technologies in 2022. The company aims to reduce the carbon footprint of its materials by 87% by 2030 across several of its divisions, with a focus on sustainable materials.
In these sessions, experts will discuss the emerging hydrogen economy and the opportunities for composites in this lucrative space.
One example related to materials is the EU’s 2022 European Green Deal which proposed several strategies that mandate EU-manufactured products ranging from construction materials to textiles be made from sustainable, recyclable or recycled materials.
Lingrove’s Luttwak adds that localizing the supply chain is of vital importance, particularly for materials suppliers that currently reside in areas where flax and hemp are not grown.
Carlson explains that for Bcomp’s flax fiber/epoxy parts, thermal energy recovery is currently the best option available. This involves incinerating the part at its EOL in a process that recovers and uses the heat from the incineration for another purpose, such as generating electricity or capturing the heat for use in houses.
Advanced Engineering is the UK’s largest annual gathering of engineering and manufacturing professionals. The event will help you to source new suppliers, network, build connections and learn about the latest industry developments all in one place. Get involved and exhibit alongside 400+ exhibitors offering solutions and products across all industries and sectors to help improve your productivity and inspire creativity. With over 9,000+ of your peers due to attend and ready to network with and inspire you, this is the event you can’t afford to miss!
For example, Autonational’s first commercial filament winding line specifically for NFCs was developed for furniture manufacturer Vepa (Hoogeveen, Netherlands). The winder was first used to build prototypes of filament-wound table legs and chairs from flax fiber and bio-based epoxy, with the first commercial line delivered at the end of 2022.
Join Wittmann for an engaging webinar on the transformative impact of manufacturing execution systems (MES) in the plastic injection molding industry. Discover how MES enhances production efficiency, quality control and real-time monitoring while also reducing downtime. It will explore the integration of MES with existing systems, emphasizing compliance and traceability for automotive and medical sectors. Learn about the latest advancements in IoT and AI technologies and how they drive innovation and continuous improvement in MES. Agenda: Overview of MES benefits What is MES? Definition, role and brief history Historical perspective and evolution Longevity and analytics Connectivity: importance, standards and integration Advantages of MES: efficiency, real-time data, traceability and cost savings Emerging technologies: IoT and AI in MES
Further, Hexcel’s Nature Range materials were first prototyped on Blizzard skis at the Tecnica Group Ski Excellence Center. “We expect that winter sports is going to grow into a key market for the Nature Range products, as it provides a challenging set of technical requirements, and successes there will really confirm that we’ve delivered a more sustainable prepreg solution that maintains the performance of our previous products,” notes Fischereder.
After a decade of proving its linerless, weight-saving composite tanks with NASA and more than 30 aerospace companies, this CryoSphere pioneer is scaling for growth in commercial space and sustainable transportation on Earth.
Across the show, sustainability ruled in new materials technology, from polyolefins and engineering resins to biobased materials.
Also making recent headlines is Lingrove’s ekoa product, enabling the color-changing, interactive doorspear component inside Hyundai’s Palisade concept vehicle. Similarly, in 2022, Cobra Advanced Composites (CAC, Chonburi, Thailand) launched a line of exterior and interior finish components made from flax fiber prepregs.
In a second-story conference room at US Merchant’s Beverly Hills, California, corporate headquarters, I’m seated across from Green at a glass-top table. I’ve just met the president and CEO of US Merchants, but his assessment of my aviation abilities is accurate. Nowadays, Green does know injection molding, and what he’s always known is retail, from sourcing, packaging and merchandising to shipping and logistics.
CW Tech Days are virtual events dedicated to the topics impacting the composites industry today. Access past event recordings and register for upcoming Tech Days.
Reliable news and information on where and how fiber-reinforced composites are being applied — that’s just the start of what you get from our team here at CompositesWorld.
Plastics Technology’s Tech Days is back! Every Tuesday in October, a series of five online presentations will be given by industry supplier around the following topics: Injection Molding — New Technologies, Efficiencies Film Extrusion — New Technologies, Efficiencies Upstream/Downstream Operations Injection Molding — Sustainability Extrusion — Compounding Coming out of NPE2024, PT identified a variety of topics, technologies and trends that are driving and shaping the evolution of plastic products manufacturing — from recycling/recyclability and energy optimization to AI-based process control and automation implementation. PT Tech Days is designed to provide a robust, curated, accessible platform through which plastics professionals can explore these trends, have direct access to subject-matter experts and develop strategies for applying solutions in their operations.
In this collection of content, we provide expert advice on welding from some of the leading authorities in the field, with tips on such matters as controls, as well as insights on how to solve common problems in welding.
How the predictive tool “CZone” is applied to simulate the axial crushing response of composites, providing valuable insights into their use for motorsport applications.
Additive technology creates air pockets in film during orientation, cutting down on the amount of resin needed while boosting opacity, mechanical properties and recyclability.
Oberste sees the prototyping work WEAV3D has done with lattice-reinforced NFC panels as the first step toward use of WEAV3D’s lattices for automotive applications. “The OEMs [we’ve worked with] are interested in the idea of whether [this technology] could strengthen the natural fiber panels to the point where other types of reinforcements in the assembly could be eliminated as well as the ribbing, such as brackets or stiffening plates, and therefore reducing weight and part count in the overall assembly.”
Allegheny Performance Plastics specializes in molding parts from high-temperature resins for demanding applications as part of its mission to take on jobs ‘no one else does.’
American Bureau of Shipping (ABS) certifies use of jointly developed CFRP repair technique on FPSO and FSO industrial systems, addressing traditional steel restoration challenges.
To this end, Malingrey says the Alliance has released an open-source, downloadable LCA for studying the environmental impact of flax fibers grown and scutched in western Europe. All fiber suppliers in the study were part of the Alliance’s European Flax certification and use the European Commission’s Product Environmental Footprint (PEF) approach. Malingrey notes that additional mapping and data collection projects are in progress.
Mike Sepe has authored more than 25 ANTEC papers and more than 250 articles illustrating the importance of this interdisciplanary approach. In this collection, we present some of his best work during the years he has been contributing for Plastics Technology Magazine.
While the major correction in PP prices was finally underway, generally stable pricing was anticipated for the other four commodity resins.
After several years of research, today the company’s core product is called Varian, a patented “composite thread” that weaves together flax fibers and plant-based PLA resin; it’s available in prepreg sheets or rolls. Made from materials sourced locally within France, Varian is customizable with choices of weave, finish and colors.
While prices moved up for three of the five commodity resins, there was potential for a flat trajectory for the rest of the third quarter.
Additionally, stitch-bonded non-crimp fabrics (NCFs) provide manufacturers and asset owners even more ways to gain a competitive advantage with products built specifically for the environments and loading conditions in which they will be utilized. Join Vectorply Corporation and Creative Composites Group (CCG) for this in-depth webinar detailing the process of engineering NCFs to build composite parts that will stand the test of time. Unlike steel, concrete and wood, composite NCFs can be optimized utilizing various fiber types, architectures and substrates to achieve the specific goals of their application efficiently. High corrosion resistance, strength and stiffness, and longevity can all be accomplished with custom-designed laminates for these heavily abused applications. Vectorply Vice President of Engineering Trevor Gundberg and Creative Composites Group Chief Sales Officer Dustin Troutman will share their industry-leading expertise on the process of laminate design and part production. Attendees can expect to learn when to use composite NCFs in their production process and the wide range of fiber-reinforced plastic (FRP) composites that Creative Composites Group produces for the industrial and infrastructure markets. Whether you want to learn more about utilizing NCFs in your production process or why CCG’s extensive product line may be the choice for your project, this webinar is the place learn the process and how to take the next steps. Agenda: Distinct advantages of non-crimp fabrics versus alternative materials How to design laminates for specific processes such as pultrusion and infusion Real-world success spotlights of NCFs in industrial applications
Ultradent's entry of its Umbrella cheek retractor took home the awards for Technical Sophistication and Achievement in Economics and Efficiency at PTXPO.
The first project is underway to recover carbon fiber used in an A330-200 aircraft, which will then be regenerated for other end uses by HRC.
Wood-fiber composite, 3D printed house. This R&D prototype, announced in fall 2022, experiments with locally sourced wood fiber as a reinforcing material for a 3D-printed house structure to solve housing shortage issues. Photo Credit: UMaine ASCC
Automotive interiors. From trunk panels to visual interior components like those pictured, the vibration damping properties of NFCs serve automotive interiors well while meeting automotive OEM goals for increased use of sustainable materials. The bottom image shows Lingrove’s ekoa materials in use on a color-changing visual doorspear on the Hyundai Palisade concept vehicle. Photo Credit: Lingrove
Other composites processes are also being adapted for use with NFCs, such as filament winding. For the past several years, the R&D branch of filament winding machinery supplier Autonational BV (IJlst, Netherlands) has been working on filament winding, prepreg processing and related machinery specifically geared toward the different mechanical requirements of manufacturing natural fiber composites with bio-based resins, explains Harry Fietje, sales manager at Autonational. This work started with collaboration with a team at the University of Amsterdam (Netherlands), which had created a plant-derived epoxy and were looking for an industry partner to test the material in a real process.
Prepreg co-molding compound by IDI Composites International and A&P Technology enables new geometries and levels of strength and resiliency for automotive, mobility.
Sustainability continues to dominate new additives technology, but upping performance is also evident. Most of the new additives have been targeted to commodity resins and particularly polyolefins.
Next step: NFCs in aircraft? Several companies and R&D products are working toward use of natural fibers with aerospace-grade resins for qualification in aircraft interiors. This concept image uses Culture iN’s Varian flax fiber-based composite material. Photo Credit: Culture iN
While the melting process does not provide perfect mixing, this study shows that mixing is indeed initiated during melting.
Ultimately, there is still much opportunity for growth in both technology and adoption of NFCs, but the past few years have solidified these as an option for sustainable manufacturing across a variety of end markets.
Recoat temperature, part orientation and bead geometry are some key design variables to consider for a successful and reliable large-format additive manufacturing (LFAM) process.
An on-demand mapping tool for anisotropic materials and polymer material fracture prediction model, i-Lupe, aims to help predict impact, crash behaviors.
This sidebar to CW’s August 2024 feature article reviews this technology for more efficient composites manufacturing and why it aligns with Koridion active core molding.
August 29-30 in Minneapolis all things injection molding and moldmaking will be happening at the Hyatt Regency — check out who’s speaking on what topics today.
In 2013, CW reported that biocomposites — both natural fibers and bio-based resins — were beginning to reach a level of commercialization and competitiveness with more traditional synthetic fiber products. At the time, cellulose fiber, which is processed from plant-derived pulp into uniform fibers, appeared to be the top contender in the natural fibers space. By CW’s 2016 feature on the same topic, improvements in performance and increased processing options had enabled flax fiber to rise as the natural fiber of choice for sporting goods applications and some automotive parts, with research in bamboo fibers showing promise.
When, how, what and why to automate — leading robotics suppliers and forward-thinking moldmakers will share their insights on automating manufacturing at collocated event.
Automation is a must-have for molders of pipettes. Make sure your supplier provides assurances of throughput and output, manpower utilization, floor space consumption and payback period.
Collins Aerospace draws on global team, decades of experience to demonstrate large, curved AFP and welded structures for the next generation of aircraft.
Along with solving these challenges, in the near term, suppliers aim to scale up their production capacity, expand their product ranges, and penetrate further into new markets and increasingly large-scale applications.
Formnext Chicago is an industrial additive manufacturing expo taking place April 8-10, 2025 at McCormick Place in Chicago, Illinois. Formnext Chicago is the second in a series of Formnext events in the U.S. being produced by Mesago Messe Frankfurt, AMT – The Association For Manufacturing Technology, and Gardner Business Media (our publisher).
Over the last 8 months, Archer Aviation has completed a total of 402 test flights with its composites-intensive aircraft, adding to key milestones.
In the hallway leading to the conference room, the walls are decorated with two of Green’s formidable collections: sports memorabilia and patents for his packaging and product display concepts that are now ubiquitous at retailers, including the warehouse club stores that he grew alongside starting in the 1980s.
The DOMMINIO project combines AFP with 3D printed gyroid cores, embedded SHM sensors and smart materials for induction-driven disassembly of parts at end of life.
Mixed in among thought leaders from leading suppliers to injection molders and mold makers at the 2023 Molding and MoldMaking conferences will be molders and toolmakers themselves.
Whether you’re exploring new applications or seeking to gain a foothold in emerging markets, Carbon Fiber 2024 is where you’ll discover the insights and connections needed to shape your business strategy. Register now.
Thousands of people visit our Supplier Guide every day to source equipment and materials. Get in front of them with a free company profile.
Still, progress is being made and the landscape has changed much over the past decade, especially in the area of flax fiber composites. According to Laurent Cazenave, communications officer at flax farming cooperative Terre de Lin (Saint-Pierre-le-Viger, France), “Ten years ago, flax was not widely used in industrial applications, [though] university studies highlighted the advantages of flax fiber, notably low density contributing to lightweight composite parts.”
The product was also developed to help solve compatibility challenges for compounders. Typically, “Natural fibers don’t mix well with petroleum-based plastics,” Henry explains, but, “Imperium focuses on solving the bonding, dust, flammability, moisture and bulk density problems that plastic compounders face when working with natural fibers.” Over the next two years, the company plans to scale up its current production to meet growing demand.
These materials are growing in appeal not just because they come from a renewable source, but because of technical advantages in composites like lightweighting and vibration and noise damping, as well as aesthetic appeal. Vibration and noise damping specifically are broadening the appeal of NFCs in applications like automotive interior components, explains Nicolas Juillard, VP of technology and development at materials supplier Texonic Inc. (Saint-Jean-sur-Richelieu, Quebec, Canada). Texonic, which is part of the Textile Monterey Group (Drummondville, Quebec, Canada), has been working on optimizing natural fibers for use in composites at the R&D level with various partners since 2012, launching its first flax fiber fabric line in 2017.
Performing regular maintenance of the layup tool for successful sealing and release is required to reduce the risk of part adherence.
Despite price increase nominations going into second quarter, it appeared there was potential for generally flat pricing with the exception of a major downward correction for PP.
Processors with sustainability goals or mandates have a number of ways to reach their goals. Biopolymers are among them.
In a time where sustainability is no longer just a buzzword, the food and beverage packaging industry is required to be at the forefront of this innovation. By adopting circular packaging processes and solutions, producers can meet regulatory requirements while also satisfying consumer demand and enhancing brand reputation. Join Husky to learn more about the broader implications of the circular economy — as well as how leading brands are leveraging this opportunity to reduce costs, increase design flexibility and boost product differentiation. Agenda: The cost and operational benefits of embracing circularity Key materials in circular packaging — including rPET and emerging bioplastics How to design a circular food and beverage package Strategies for selecting sustainable closures to future-proof packaging solutions Optimization and streamlining of production processes for enhanced efficiency How Husky Technologies can enable your sustainable success
Over the past few years, a lot of attention has been paid to the emergence of NFCs in automotive components. This has included body panels and hoods for a variety of supercars and race cars, as well as interior applications for commercial vehicles.
Today, US Merchants operates seven facilities in California, with additional sites in Virginia, Texas, Canada and Arizona, as well as a planned expansion into the U.K. The company has standardized on LS Mtron injection molding machines, and it credits the Korean press maker and several other vendors with helping it transition from a molding newbie to an old plastics hand.
This month’s resin pricing report includes PT’s quarterly check-in on select engineering resins, including nylon 6 and 66.
Within the recreational market, NFCs have also found a home on recreational and racing boats and yachts, starting with a number of prototypes. As one example, the CrossCall racing yacht, which won the Class40 World Championships in June 2022, was reported to be the first Class40 yacht to make significant use of flax fiber composites. Infused, hybrid flax/glass fabrics were used to manufacture the hull, cockpit and several other components of the boat.
During this webinar, the audience will be introduced to a variety of fiber composite technologies — as well as the machines and equipment — from short fibers to continuous fibers, from thermoset to thermoplastic, as well as the according process technology, including a special focus on long-fiber injection (LFI) and structural composite spray (SCS). Focus markets include automotive, aviation and AAM, transportation, and construction. This webinar will provide a detailed overview of according application examples. Agenda: Long fiber injection (LFI) Structural composite spray (SCS) Resin transfer molding (RTM), wet compression molding, etc. Pultrusion FiberForm
Second quarter started with price hikes in PE and the four volume engineering resins, but relatively stable pricing was largely expected by the quarter’s end.
Natural fibers, new markets. In recent years, the landscape for natural fiber materials — materials, processes and end markets — has expanded beyond niche applications and R&D labs into increasingly larger-scale commercial projects. A few examples pictured include Formula 1 and other motorsports applications (top left image), skis and other sporting goods (top right), furniture and other interior applications (bottom left) and automotive interiors (bottom right). Photo Credit, left clockwise: Super Formula, via Bcomp Ltd.; ZAG Skis / Juan Cruz, via Bcomp Ltd.; Autonational; Lingrove
According to Juillard, Texonic continues to be involved in R&D work to develop and optimize additional materials for use in NFCs — with a large focus on hemp fiber as well, which is also continuing to grow in supply and usage. As he explains it, one of the largest factors in choosing natural fiber materials is not necessarily the properties of one type of fiber over another, but localization of the supply. Currently, due in large part to climate, flax is produced most widely in Europe, while the market for hemp agriculture grows in North America.
Working closely with Steve Gwon and his machinery distribution company E Solution Inc., Hirate and US Merchants soon switched over to LS Mtron injection molding machines. Eventually, Gwon and Hirate would help US Merchants not only source machines but molds, hot runner controllers, auxiliaries, robots, chillers, material handling systems, gantry cranes, mold tilters and more. Beyond sourcing, they also gave the rookie molder advice on everything from part design and employee recruiting to laying out and commissioning new plants.
Oberste and WEAV3D are relatively new to working with NFCs. Originally, WEAV3D developed an automated weaving system that manufactures tunable thermoplastic composite lattices that can be used to reinforce a variety of materials, from concrete to automotive panels. The company began with carbon and glass fiber lattices, and has in recent years expanded its R&D work to include natural fiber lattices, which are used to reinforce NFC panels for the automotive market.
The composite tubes white paper explores some of the considerations for specifying composite tubes, such as mechanical properties, maintenance requirements and more.
In the foreground, rows of shrink-wrapped pallets ready for delivery. In the background, US Merchants in-house thermoforming lines. Photo Credit: Plastics Technology
Specifically, Green and US Merchants credit Shingo Hirate, president of equipment distributor Hirate America Inc., Anaheim, California, with helping the company understand what would be needed to get started in injection molding. Green and Larry Khemlani, US Merchants VP of Operations, met Hirate while walking a plastics trade show, and Hirate’s willingness to get into the nuts and bolts of starting a molding business from scratch won him a new and prodigious customer. US Merchants would order four full molding machine cells from Hirate shortly thereafter and then another three in quick succession.
Join KraussMaffei for an insightful webinar designed for industry professionals, engineers and anyone interested in the manufacturing processes of PVC pipes. This session will provide a comprehensive understanding of the technology behind the production of high-quality PVC pipes: from raw material preparation to final product testing. Agenda: Introduction to PVC extrusion: overview of the basic principles of PVC pipe extrusion — including the process of melting and shaping PVC resin into pipe forms Equipment and machinery: detailed explanation of the key equipment involved — such as extruders, dies and cooling systems — and their roles in the extrusion process Process parameters: insight into the critical process parameters like temperature, pressure and cooling rates that influence the quality and consistency of the final PVC pipes Energy efficiency: examination of ways to save material and energy use when extruding PVC pipe products
Explore the cutting-edge composites industry, as experts delve into the materials, tooling, and manufacturing hurdles of meeting the demands of the promising advanced air mobility (AAM) market. Join us at CW Tech Days to unlock the future of efficient composites fabrication operations.
Marine expansion. Some of the largest NFC parts manufactured to date have been for recreational and racing marine vessels, including infused decks and hulls. Hybrid fiberglass/natural fiber is also being used. Photo Credit: Baltic Yachts, via Bcomp Ltd.
Cevotec, a tank manufacturer, Roth Composite Machinery and Cikoni, have undertaken a comprehensive project to explore and demonstrate the impact of dome reinforcements using FPP technology for composite tanks.
Beyond high-performance marine and sports, the appealing sustainability aesthetic of natural fibers lends these materials to decorative interior items and furniture, as Lingrove and Culture iN have discovered with their product lines.
New aircraft is expected to deliver wind turbine blades from 105 meters up to expand the reach of wind energy and achieve global climate goals.
Successfully starting or restarting an injection molding machine is less about ticking boxes on a rote checklist and more about individually assessing each processing scenario and its unique variables.
How the predictive tool “CZone” is applied to simulate the axial crushing response of composites, providing valuable insights into their use for motorsport applications.
Fischereder adds, “Increased sustainability and enhanced health and safety are both areas where our input raw materials can have a major impact. As the bio-derived chemical raw materials industry has continued to develop, Hexcel has moved to partially replace petrochemical-based epoxy content with bio-derived alternatives. A key target for us was to make sure that the excellent resin characteristics remain unchanged in the new Nature Range products, maintaining high mechanical performance and consistent processing properties while giving customers a more sustainable material option.”
CompositesWorld's Carbon Fiber conference offers you cutting-edge information and access to industry experts in streamlining manufacturing costs, market outlooks and forecasting, and more. You will make invaluable contacts as you meet and network with the industry's most innovative and influential leaders at Carbon Fiber. __PRESENT
Analyzing structural resonance of the aircraft under various loads becomes a critical step in obtaining flight certification.
Wood-like composites. Lingrove’s ekoa materials are marketed as a flax fiber and plant-based resin alternative to wood for building and automotive interiors. Texonic, too, has developed a wood-like NFC for use in a variety of sporting goods, automotive, furniture applications and more. Photo Credit: Lingrove (top and middle) and Texonic (bottom)
Now the owner of hundreds of injection molding machines, Jeff Green speaks frankly about his company’s molding knowledge when he acquired his first presses in 2014. “We didn’t know anything about injection molding,” Green says. “I knew as much about injection molding as you know about flying a 747 airplane.”
Stephen Heinz, vice president of R&I for Syensqo delivered an inspirational keynote at SAMPE 2024, highlighting the significant role of composite materials in emerging technologies and encouraging broader collaboration within the manufacturing community.
CompositesWorld’s CW Tech Days: Infrastructure event offers a series of expert presentations on composite materials, processes and applications that should and will be considered for use in the infrastructure and construction markets.
US Merchants’ newest Glendale, Arizona, facility covers nearly 640,000 square feet and will have 69 LS Mtron presses when fully commissioned.
Prepreg co-molding compound by IDI Composites International and A&P Technology enables new geometries and levels of strength and resiliency for automotive, mobility.
Furthermore, beyond natural fiber fabrics and tapes, short natural fibers are being developed as additives for use in plastic parts. For example, in 2022, Heartland (Detroit, Mich., U.S.) launched Imperium, its first hemp fiber additive product line. According to Jesse Henry, CEO and founder, the company began as a bio-based plastics company, but pivoted to hemp fiber additives in 2020, aiming to support customers with cost-effective, carbon-negative additives for use in thermoplastics. Heartland sells Imperium in powder and masterbatch format for use in injection molding, compression molding, extrusion, thermoforming, and other types of plastic and rubber manufacturing.
“I don’t say I have the best standard in the world, but we live or die by what our standard is, so we don’t cut corners. That doesn’t mean we don’t make mistakes — we make mistakes like everybody else. We try to learn from our mistakes and not let them happen a second time, but we don’t make mistakes because we’re trying to cut corners to make a larger margin. If I give you a better price, it’s coming out of my margin, never out of the quality of the product.”
Herone, Spiral RTC, Teijin Carbon Europe and Collins Aerospace Almere recycle A350 thermoplastic composite clips/cleats waste into rods for the all-thermoplastic composite Multifunctional Fuselage Demonstrator’s crown.
A report on the demand for hydrogen as an energy source and the role composites might play in the transport and storage of hydrogen.
Beginning in retail himself in 1979 with a tennis store in Beverly Hills dubbed with the pun-intended name — The Merchants of Tennis — Green grew into the wholesale business at a time in the early ‘80s when warehouse club chains were just getting started. One of Green’s patents is for the Pallet Program he devised as a means for those retailers to turn pallets of shrink-wrapped and boxed-up goods into ready-to-go, point-of-purchase displays with nothing more than a box cutter.
Multiple speakers at Molding 2023 will address the ways simulation can impact material substitution decisions, process profitability and simplification of mold design.
One of the latest, most ambitious exterior construction applications to date was announced in November 2022 by the University of Maine Advanced Structures and Composites Center (UMaine ASCC, Orono, Maine, U.S.), which fabricated a 600-square-foot, 3D-printed prototype house made entirely from bio-based resins reinforced with a locally sourced, wood-based fiber. Called BioHome3D, the prototype was developed with funding from the U.S. Department of Energy (DOE) and in partnership with Oak Ridge National Laboratory (ORNL, Knoxville, Tenn., U.S.)
True to the adjective in its name, Dynamic Group has been characterized by constant change, activity and progress over its nearly five decades as a medical molder and moldmaker.
The composites industry plays a crucial role in developing lightweight and durable materials for a range of applications, including those critical to national defense. One key focus area is the development of advanced structural materials and manufacturing technologies that support next-generation space, missile and aircraft systems for the U.S. Department of Defense (DOD). ARC Technologies LLC (ARC), a division of Hexcel Corporation, based in Amesbury, Massachusetts, is a provider of advanced composites structures, specialty materials and other unique products that provide the U.S. Department of Defense with advanced capabilities to protect service members while in harm’s way. This team’s specialty is to understand a specific need from a program office, PEO, platform manufacturer or other offices within the DOD. With that understanding, the team can design a solution, develop a prototype for test and evaluation, perform extensive in-house testing — including electromagnetic, environmental and structural testing — and then partner with the customer through platform evaluation. The Hexcel Amesbury division has a team of engineers on staff, including mechanical, chemical, electrical and research and development specialists that can provide design, testing and manufacturing capabilities to service customer requirements from concept through production. This presentation will illustrate capabilities in advanced composites and other specialty materials structures, focusing on the Hexcel Amesbury team's niche in electromagnetic signature reduction and other unique capabilities.
Hannah Mason reports on sustainability in manufacturing across Gardner Business Media brands. She is also a Technical Editor reporting about composites manufacturing for CompositesWorld, a topic she has covered since 2018. She earned a Masters of Arts in professional writing from the University of Cincinnati and a B.A. in writing from West Liberty University.
Much of the work done in composites recycling focuses on recovering and reusing higher-performance, higher-cost carbon fiber, begging the questions: Are lower-cost, renewable NFCs worth recycling? Can they survive the same processes as carbon fiber, with high enough properties to reuse? These considerations are still being worked out. As Hexcel’s Fischereder notes, new applications for recycled NFCs are also an important part of the conversation. With a field as new as NFCs, both demand for recycled NFCs and supply are also still immature.
CompositesWorld is the source for reliable news and information on what’s happening in fiber-reinforced composites manufacturing. About Us
Learn about sustainable scrap reprocessing—this resource offers a deep dive into everything from granulator types and options, to service tips, videos and technical articles.
Gifted with extraordinary technical know how and an authoritative yet plain English writing style, in this collection of articles Fattori offers his insights on a variety of molding-related topics that are bound to make your days on the production floor go a little bit better.
Notably, in 2022 BMW Group’s investment arm iVentures acquired a stake in Bcomp, signaling a commitment to commercial uses of sustainable materials. In June 2022, BMW unveiled a new M4 GT4 racecar sporting Bcomp’s flax fiber materials in several body components. The company announced at the time that the switch to NFCs reduced greenhouse gas emissions for the vehicle production by up to 85% for those components, while improving vibration damping performance.
For example, longtime reinforcements and resins supplier Hexcel (Stamford, Conn., U.S.) launched an NFC-specific, HexPly Nature Range in 2022, which includes woven and stitched flax fiber reinforcements with HexPly M49, M79-LT and M79.1-LT epoxy resins containing partially bio-derived content. The partially bio-based resins can also be used with traditional fiberglass or carbon fiber reinforcements, as well, notes Achim Fischereder, industrial marketing director at Hexcel.
Initial demonstration in furniture shows properties two to nine times higher than plywood, OOA molding for uniquely shaped components.
“This is where companies like LS Mtron and E Solution have really made a difference,” Green says, “because these people are professionals and experts, and we’ve kind of put ourselves in their hands to help us and direct us in the right direction.”
Another challenge is sensitivity to temperature, especially as companies expand into new types of processing methods and resins. “At the same temperatures used to process carbon or glass fibers, natural fiber might start to char or decompose,” explains Christopher Oberste, president and chief engineer of composite lattice manufacturer WEAV3D Inc. (Norcross, Ga., U.S.).
The JEC Forum DACH is a business meetings event organised by JEC The JEC Forum DACH is organised on October 22 and 23, 2024 by JEC, in partnership with the AVK, gathering the composite materials community from the DACH Region (Germany, Austria and Switzerland).
A combination of Airtech’s 3D printing materials and Ascent’s production capabilities aim to support increased use of composite additive tooling in spaces like defense and aerospace.
In this three-part collection, veteran molder and moldmaker Jim Fattori brings to bear his 40+ years of on-the-job experience and provides molders his “from the trenches” perspective on on the why, where and how of venting injection molds. Take the trial-and-error out of the molding venting process.
Back in 2014, one of those manufacturers requested something that wasn’t on the menu, asking US Merchants if it could make it a better 27-gallon storage container. “I do have engineers in my packaging and machine area that understand what injection molding is and they said to me, ‘Jeff, this product requires different equipment than what we currently have,’ and so I said, ‘Will you look into it and let me know what the cost is,’ and I went back the very next day to the customer and said, ‘If you give me a commitment…’ — because we don't do anything unless we have a firm commitment — and that customer gave me a commitment, sight unseen. I guaranteed that the product would be better than what they were currently selling. I went ahead and I bought some equipment, and that’s how I got into the injection molding business.”
What types of commercial applications are being manufactured with NFCs today? Many of the initial commercial NFC applications were sporting goods and furniture pieces, and these continue to be two leading market areas for the materials, but as raw material supply, natural fiber fabrics and processing technologies evolve, NFCs are increasingly used for applications in even higher-volume or higher-performance markets like automotive and even aerospace.
“Our materials replace and augment commonly used plastic additives like fiberglass, talc and calcium carbonate. Our LCA [lifecycle assessment] gives brands and suppliers a predictable path to reduce the carbon footprint of the plastic they use everyday just by changing the additive and reducing the amount of plastic required to create the same product,” Henry says.
Take a deep dive into all of the various aspects of part quoting to ensure you’ve got all the bases—as in costs—covered before preparing your customer’s quote for services.
“Automotive is picking up, as the release date of large-scale serial production cars is getting close — these are projects that we have worked on together with OEMs for several years and that are now finally about to hit the consumer market,” Bcomp’s Carlson says.
CompositesWorld’s Tech Days: Design, Simulation and Testing Technologies for Next-Gen Composite Structures is designed to provide a multi-perspective view of the state of the art in design, simulation, failure analysis, digital twins, virtual testing and virtual inspection.
Starting with sporting goods. The vibration-damping properties of NFCs, plus their aesthetic appeal, contributed to the materials’ appearance early on in the market, particularly in sporting goods like skis. Photo Credit: ZAG Skis / Quentin Iglesis, via Bcomp Ltd.
Whether you’re exploring new applications or seeking to gain a foothold in emerging markets, Carbon Fiber 2024 is where you’ll discover the insights and connections needed to shape your business strategy. Register now.
Thousands of people visit our Supplier Guide every day to source equipment and materials. Get in front of them with a free company profile.
Adding strength and stiffness. WEAV3D’s lattices are shown to increase flexural strength and stiffness of an NFC panel. In the graph above, an unreinforced NFC panel (NFPP) gains stiffness and strength properties with the addition of different layers and material mixes of lattices (SSG is single-sided glass fiber lattice, SSC1 is a single-sided glass/carbon fiber lattice, DS1C is a double-sided mixed carbon/glass lattice with one carbon tape layer in each mix, DS2C is a double-sided mixed carbon/glass lattice with two carbon layers in each mix). Ultimately, lattice reinforcement increases performance to match a panel made from 50% long glass fiber reinforced polypropylene (50% LCF PP). Photo Credit: WEAV3D Inc.
The choice to adopt flax or hemp over synthetic or petroleum-based fibers is a step toward increased sustainability, but natural fibers alone are not enough to truly make a product sustainable. Today, many NFCs are made from traditional resins like epoxy.
Companies are also using NFCs in exterior applications in construction and infrastructure. The multinational design, engineering and architecture firm Arup (London, U.K.) won a JEC award in 2015 as part of the EU-funded BioBuild project, demonstrating a self-supporting facade system comprising 4 × 2.3-meter flax fabric/bio-resin panels. The NFC panels reportedly reduce the embodied energy in façade systems by up to 50% compared to conventional construction materials with no increase in cost. More recently, Exel Composites (Vantaa, Finland) produced 6 kilometers of flax/bioresin profiles for a “fauna passage” viaduct in the Netherlands and three flax fiber/bio-resin bridges will be completed by 2023 as part of the “Smart Circular Bridge” project. Luttwak notes these exterior architecture applications are an end goal of Lingrove’s. Autonational, too, has begun working on filament-wound NFC prototypes for outdoor structures like poles for road signs, with additional applications to come.
Foundational research discusses the current carbon fiber recycling landscape in Utah, and evaluates potential strategies and policies that could enhance this sustainable practice in the region.
“In the same way that other high-end industries use quality standards, the Alliance engages the flax and linen sector in the application of traceability and transparency procedures. This is one of the key strategic commitments to the composites sector,” she says.
The Marservis PROeco is a mass transportation marine vessel using Bcomp natural fiber for interior parts in place of standard materials.
Celebrating National Composites Week 2024, CW looks at how composites are being used to provide the next generation of energy.
Join Engel in exploring the future of battery molding technology. Discover advancements in thermoplastic composites for battery housings, innovative automation solutions and the latest in large-tonnage equipment designed for e-mobility — all with a focus on cost-efficient solutions. Agenda: Learn about cutting-edge thermoplastic composites for durable, sustainable and cost-efficient battery housings Explore advanced automation concepts for efficient and scalable production See the latest large-tonnage equipment and technology innovations for e-mobility solutions
Continuous fiber-reinforced thermoplastic composite targets full circularity in aircraft interior applications, with FST, impact resistance and toughness features.
The increased interest in sustainability — and, importantly, the increase in high-quality flax and hemp fiber — has also led several mainstay suppliers of more traditional composite reinforcements, like fiberglass or carbon fiber, to begin offering natural fiber products.
In less than a decade in injection molding, US Merchants has acquired hundreds of machines spread across facilities in California, Texas, Virginia and Arizona, with even more growth coming.
Jetcam’s latest white paper explores the critical aspects of nesting in composites manufacturing, and strategies to balance material efficiency and kitting speed.
Flax and hemp. A variety of plant-based fibers exist today, with the top two in the composites space being hemp and flax (pictured). The formats and processing capabilities of these materials continue to expand as more companies enter the arena of supplying NFC materials. Photo Credit: Bcomp Ltd.
Still, Malingrey says that demand for natural fibers has been “increasing strongly since 2020. Whereas a few years ago, natural fibers were more of an R&D exercise, now we see fully developed products entering the market.”
In the Automated Composites Knowledge Center, CGTech brings you vital information about all things automated composites.
Knowing the fundamentals for reading drawings — including master ply tables, ply definition diagrams and more — lays a foundation for proper composite design evaluation.
The composites industry is increasingly recognizing the imperative of sustainability in its operations. As demand for lightweight and durable materials rises across various sectors, such as automotive, aerospace, and construction, there is a growing awareness of the environmental impact associated with traditional composite manufacturing processes.
Renewable fibers. The sustainability appeal of natural fiber composites from plant-based sources (like flax, pictured) is to replace synthetic materials like carbon or fiberglass with natural, renewable alternatives. Companies continue to make NFCs more sustainable still by localizing supply chains, reducing carbon footprint for manufacture and using bio-based resins in addition to natural fibers. Photo Credit: Bcomp Ltd.
Despite the sustainability appeal of a plant-based, renewable alternative to carbon or glass fiber, commercial adoption of natural fibers in composites has been relatively slow, due to industry challenges such as limited supply, variable fiber quality, limited mechanical performance in finished parts, differences in manufacturability and, depending on the material, higher material costs compared to fiberglass.
In terms of sustainability measures, monomaterial structures are already making good headway and will evolve even further.
“When you have to farm things out to third parties, you’re only asking for issues with delivery and excuses why something can’t be done.”
“Technically, if you look at the literature, one type of [natural fiber] may have more resistance and one has higher modulus, but right now, talking about the differences isn’t the right approach, because none of them are totally optimized for use in composites,” Juillard says. “We have some good products now, but there’s still a lot of work to do. Choosing one over the other isn’t about processing or properties. It’s about supply chain, and which material you can get at which cost.”
The resulting vertical integration propelled by this mindset extends into some unexpected areas. To wit, the company’s original 245,000-square-foot facility in Ontario, California, includes a carpentry shop that designs, builds and installs all the office furniture for all of US Merchants’ facilities. Outside the shop, an “Arizona Project ‘22” poster hangs, marking its recent work to fully furnish the company’s newest outpost. US Merchants sent its own carpenters to the new facility where they took measurements for all its furnishings before coming back to California to build all the desks, shelving and more, and then return to Arizona to install it. When it’s not building furniture for the company, the carpentry shop also designs and constructs trade show booths for US Merchants, as well as store point-of-purchase displays.
From furniture to floors. Interior commercial applications of NFCs range from tables (top) and chairs (bottom) to ceiling and floor panels. Photo Credit: Autonational (top) and Lingrove (bottom)
Say “manufacturing automation” and thoughts immediately go to the shop floor and specialized production equipment, robotics and material handling systems. But there is another realm of possible automation — the front office.
Interior applications. Culture iN’s flax fiber and plant-based PLA Varian product were developed specifically for more sustainable, aesthetically pleasing interior applications, like the pictured light fixture. Photo Credit: Culture iN
Plastics Technology covers technical and business Information for Plastics Processors in Injection Molding, Extrusion, Blow Molding, Plastic Additives, Compounding, Plastic Materials, and Resin Pricing. About Us
Mold maintenance is critical, and with this collection of content we’ve bundled some of the very best advice we’ve published on repairing, maintaining, evaluating and even hanging molds on injection molding machines.
You need to pay attention to the inherent characteristics of biopolymers PHA/PLA materials when setting process parameters to realize better and more consistent outcomes.
Recoat temperature, part orientation and bead geometry are some key design variables to consider for a successful and reliable large-format additive manufacturing (LFAM) process.
During this CW Tech Days event, sponsored by Composites One, experts will offer presentations to review and evaluate the composite materials, processes and applications that should and will be considered for use in the infrastructure and construction markets.
Exhibitors and presenters at the plastics show emphasized 3D printing as a complement and aid to more traditional production processes.
Stemming from years of university and industry research, the first major use cases were sustainability-minded sporting goods manufacturers of products like tennis rackets and skis. Over time, various “players, projects and industrial successes have gradually given [NFCs] visibility and credibility,” Cazenave says.
Additional efforts are ongoing at the R&D level. For example, Fietje reports that Autonational and its partner Plantics are working on a pilot recycling system using steam to separate fibers and resins — specifically with the mechanical requirements of NFCs and bio-based resins in mind.
US Merchants’ Ontario, California, injection molding facility features 46 1,200-ton LS Mtron injection molding machines. Photo Credit: US Merchants
The ITHEC 2024 will take place from the 9 to 10 October 2024 in Bremen, Germany. At the 7th International Conference, more than 300 participants from around the world will be presenting and discussing newest scientific results, meet leading international specialists, share their expertise and start business co-operations in the field of thermoplastic composite technologies. The international exhibition will feature 40+ exhibitors showcasing all steps of the supply-chain. Be it materials, machines, testing, processes, or solutions. By combining the exhibition and the conference ITHEC is further fostering the inter-connectivity between science and industry.
Six U.S. companies have proven their recycling technologies for composites and rare earth elements, and will be supported for relevant scale demonstration and validation.
“My personal belief is quality stands the test of time,” Green says, “and so we as a company don’t cut any corners. I believe that making the highest quality product in the industry, you have the longest staying power.” With its molded products, that ethos extends to the removal of any flash and, if need be, to avoid warp and produce a tote that closes cleanly and securely off the press, longer cycle times.
One of Bcomp’s goals is to qualify its flax fiber materials for use in rail and interior aircraft applications, which means developing higher-performance products that can pass stringent fire tests. “Our goal is to help decarbonize mobility; our impact increases as we reach into even larger markets,” Carlson says.
The aim of this presentation is to guide you through the factors and the numbers that will help you determine if a robot is a smart investment for your application. Agenda: Why are you considering automation? What problems are you trying to solve? How and why automation can help Crunch the numbers and determine the ROI
The automotive interiors industry already mass-produces compression-molded NFC panels for use in trunk floors and sidewalls, made primarily from hemp or jute in the form of nonwoven mats or long fibers. Typically, Oberste says, these panels are reinforced with injection overmolded glass fiber-reinforced ribs to add strength and stiffness where needed, but these ribs add unwanted weight and geometry to the panels. With an OEM partner, WEAV3D began an effort to replace these ribs with layers of carbon, glass or natural fiber thermoplastic composite lattices produced via WEAV3D’s automated system.
The composites-intensive VTOL platform is next expected to undergo a series of test flights in various conditions to validate its performance, safety and reliability, leading up to eventual certification.
Aerospace manufacturer joins forces with composite materials company to achieve sustainable manufacturing practices that overcome traditional composite layup tooling.
Introduced by Zeiger and Spark Industries at the PTXPO, the nozzle is designed for maximum heat transfer and uniformity with a continuous taper for self cleaning.
Joe Luttwak, CEO at Lingrove, explains that architects, designers and executives in the interiors industry, for residences and commercial spaces, are increasingly “looking to decarbonize, and need high-performance products.” The company supplies prefabricated panels and surface veneers designed to provide the look of luxury wood. Applications of ekoa veneers include wall and ceiling panels and cabinetry/caseworks products, with flooring in development.
In this collection, which is part one of a series representing some of John’s finest work, we present you with five articles that we think you will refer to time and again as you look to solve problems, cut cycle times and improve the quality of the parts you mold.
Multiple suppliers are working on bio-based resins for use with natural fibers, including Hexcel. Fischereder says, “In the future, we believe that bio-derived epoxy content, in addition to equivalent mechanical performance, will not just be offered as an option. It will start to become the baseline and a must-have to proceed with material qualification.” For Hexcel, this means working on new, bio-derived versions of HexPly resin systems, which are currently undergoing certification by testing and certification services company TÜV (Cologne, Germany).
Terre de Lin’s Cazenave also notes that several of the company’s partners have begun successfully replacing fiberglass with flax fiber composites in a variety of recreational and racing boats. One notable and large example is the 9-meter-wide, 18-meter-long flax fiber composite deck for the We Explore proof of concept catamaran, developed by Outremer shipyard, VPLP Design and Kairos Environnement.
What about an NFC part’s EOL? In general, several recycling options for composites exist, at various levels of commercialization. For example: Mechanical recycling, involving the shredding of entire parts into small pieces that can be reused for injection molding or another purpose; pyrolysis or thermolysis, where heat is introduced to a part until the resin is burned off, leaving a reusable fiber behind; or solvolysis, which uses some type of chemical process to separate a resin from its original fibers.
A number of other companies have also entered this space, with the goal of making their specific end markets more sustainable. Lingrove (San Francisco, Calif., U.S.) launched its flax fiber and plant-based resin composite material, called ekoa, to replace wood in ukuleles and guitars in 2013, followed by sporting goods in 2014. It then worked to commercialize and industrialize ekoa for automotive interiors and the furnishings/interiors market.
Porcher Industries (Eclose-Badinières, France) and Saertex (Saerbeck, Germany) have also announced NFC offerings, with flax fiber/thermoplastic automotive-grade materials (Porcher) and flax fiber noncrimp fabrics (NCF) for marine and leisure applications (Saertex), each in partnership with flax supplier Terre de Lin. Terre de Lin, which claims to produce about 15% of the world’s flax supply, manages all stages of flax production for its 700-member farms, from seeds, to processing of the harvested flax, to manufacture of fibers specific for composites and other markets. Over the past decade, recognizing the value for its flax fibers within the composites industry, Terre de Lin has worked to offer flax fibers “adapted to the composites market,” Cazenave says, including controlled quality and development of a versatile range of rovings compatible with composites processes.
MTorres seeks to enable next-gen aircraft and open new markets for composites with low-cost, high-permeability tapes and versatile, high-speed production lines.
Formnext Chicago is an industrial additive manufacturing expo taking place April 8-10, 2025 at McCormick Place in Chicago, Illinois. Formnext Chicago is the second in a series of Formnext events in the U.S. being produced by Mesago Messe Frankfurt, AMT – The Association For Manufacturing Technology, and Gardner Business Media (our publisher).
Explore the technologies, materials and strategies used by composites manufacturers working in the evolving space market.
Backed by government funding, Autonational’s R&D team began working with the university team and the resulting spin-off company Plantics (Arnhem, Netherlands), which now sells its resins commercially. Adapting its filament winding machinery for natural fibers and bio-based resins required about a year and a half of trial and error, Fietje says, requiring many adjustments to the temperature and processing conditions.
While prices moved up for three of the five commodity resins, there was potential for a flat trajectory for the rest of the third quarter.
Arris presents mechanical testing results of an Arris-designed natural fiber thermoplastic composite in comparison to similarly produced glass and carbon fiber-based materials.
Closed mold processes have many advantages over open molding. In this knowledge center, learn the basics and vital tools needed to produce parts accurately.
Malingrey of the Alliance for European Flax-Linen & Hemp agrees, noting that scientifically driven datasets on both the environmental and technical advantages of flax and hemp fiber composites are needed to truly prove out their value in the market and allow for established guidelines on their use.
At the end of the three rows of machines at the Ontario injection molding facility, some totes and other molded products are marked NCM (nonconforming materials) and will be scrapped. Khemlani notes NCM represents less than 1% of the company’s output, with the parts in question not meeting US Merchants rigid and rigorous standards, which are another core tenet of Green’s business philosophy.
Efficient, high-quality, well-controlled composites manufacturing at volume is the mantra for this 3D weaving specialist.
As Fietje of Autonational notes, to be effective, the ideal supply chain would involve natural fibers with bio-based resins derived from plant sources, plus an end-of-life (EOL) solution that allows the part or its original components to be recycled for another use.
CW’s editors are tracking the latest trends and developments in tooling, from the basics to new developments. This collection, presented by Composites One, features four recent CW stories that detail a range of tooling technologies, processes and materials.
Another guiding principle for Green and his wife, Marie, who is also his business partner since the tennis shop, is to use that reputation for attention to detail and quality to secure order commitments prior to taking on new jobs or new markets. “Our formula, my wife and mine, has not changed since we started our business with our little tennis store,” Green says. “We don’t really do anything unless we have a commitment. Typically, a customer of ours will come to us and say, ‘Can you make…?’”
Base Materials introduces a high-performance, toughened epoxy tooling board designed for thermoforming and vacuum forming processes, direct-to-part applications and more.
This Knowledge Center provides an overview of the considerations needed to understand the purchase, operation, and maintenance of a process cooling system.
“I can give a customer a delivery date,” Green says, “and I know that I can meet that date. Why? Because we control the entire process. We do all that in-house and we control it, so I know that if I give somebody a promise, I’m going to be able to deliver because we do everything in-house.”
As CW reported in 2016, early commercial adopters of NFCs included ski and snowboard manufacturers adopting Bcomp flax fiber/epoxy materials, taking advantage of the lighter weight of flax fiber compared to fiberglass and the high vibration damping for a smoother ride. Today, Carlson reports that Bcomp still has a large share of business in sporting goods as well as motorsports applications. One recent example that CW reported on is an award-winning motorbike brake disc cover made in part with Bcomp’s flax fiber/epoxy.
In June 2023, US Merchants opened a facility in Glendale, Arizona, covering nearly 640,000 square feet, which will have 69 LS Mtron presses when fully commissioned, including 2,500-ton and all-electric machines. A second facility is coming to Houston, and the company will be opening its first international molding facilities in Montreal and the U.K. The molding operation we tour in Ontario, which was purchased in 2017, has 46 1,200-ton LS Mtron presses divided into three rows.
Validation of 80-100% tensile strength and comparability to injection molding via Voxelfill extrusion process was achieved through plastic and fiber-filled test series.
Join this webinar to explore the transformative benefits of retrofitting your existing injection molding machines (IMMs). Engel will guide you through upgrading your equipment to enhance monitoring, control and adaptability — all while integrating digital technologies. You'll learn about the latest trends in IMM retrofitting (including Euromap interfaces and plasticizing retrofits) and discover how to future-proof your machines for a competitive edge. With insights from industry experts, it'll walk you through the decision-making process, ensuring you make informed choices that drive your business forward. Agenda: Maximize the value of your current IMMs through strategic retrofitting Learn how to integrate digital technologies to enhance monitoring and control Explore the benefits of Euromap interfaces and plasticizing retrofits Understand how retrofitting can help meet new product demands and improve adaptability Discover how Engel can support your retrofitting needs, from free consultations to execution
This push for sustainability solutions, alongside supply chain and technical advancements in natural fiber materials, and processes to manufacture them into composites, are fueling R&D and commercial growth into new markets.
Over the years and owing in part to Green’s desire for maximum control, US Merchants vertically integrated everything from graphic and package design to thermoforming and thermoform die manufacturing to shipping and logistics with his own fleet of trucks. “Our business started to grow, and not just in packaging,” Green says, “but now we offer a nice menu of items that a manufacturer or retailer can select from, be it packaging or logistics or transportation or buying the product and reselling it, which a lot of manufacturers like. We’re really a turnkey solution for them.”
Resin drying is a crucial, but often-misunderstood area. This collection includes details on why and what you need to dry, how to specify a dryer, and best practices.
Powered by an 85% air/15% pure polyimide aerogel, Blueshift’s novel material system protects structures during transient thermal events from -200°C to beyond 2400°C for rockets, battery boxes and more.
So far, despite these challenges, WEAV3D has seen positive results, showing that even a single, 0.3- to 0.5-millimeter lattice layer adds enough bending stiffness that the OEM could not only eliminate the ribbing but also make the overall panel thinner. WEAV3D demonstrated that it could produce a lattice-reinforced composite panel with the same mechanical properties as the original rib-reinforced panel, at about a 25% reduction in part mass. For added stiffness, additional layers can be added, and the tapes can be made from carbon, glass or natural fiber tapes as needed. WEAV3D continues to work with Tier 1 suppliers and OEMs on prototype panels and tests, aiming toward serial production.
Natural fibers — derived from plant-based sources such as flax, hemp, jute or bamboo — have been used for thousands of years, but adoption of natural fiber-reinforced composites (NFC) as we currently define them has been much more recent, with commercial applications slowly emerging over the past decade.
Kennametal will cover the influence of different composite materials characteristics on drilling performance and how to optimize the process. Agenda: Who is Kennametal? Hole making challenges in composite materials Innovations for hole making applications Upcoming events and academic partnerships
According to WEAV3D’s Oberste, more sustainable, renewable and/or recyclable materials within automotive designs is no longer a niche idea, and companies are willing to pay a bit more to be able to claim a certain percentage of natural fiber or other sustainable materials within a vehicle. “There are several different approaches the industry is taking to ‘sustainable’ content — natural fibers is one option within that,” he says.
Bcomp’s Carlson says, “For suppliers of natural fiber reinforcements, the market is relatively immature and developing as we speak. There are so many factors that must come together: Combining expertise in natural fibers with the industrial knowledge to scale, the technical knowledge to develop a high-performance product and the commercial capacity to take it to the market, and convincing markets with high inertia to change and high entry barriers to try something new.”
Beyond Plastic and partners have created a certified biodegradable PHA compound that can be injection molded into 38-mm closures in a sub 6-second cycle from a multicavity hot runner tool.
What does today’s NFC market look like? The Alliance for European Flax-Linen & Hemp (Paris, France) tracks data on flax and hemp supply, demand and applications from its member suppliers across Europe. Chantal Malingrey, director of marketing and communication, says that flax fibers are the most used natural fibers in composites today, though composites are still the smallest end market for these fibers overall, compared to the much more established fashion and textile industries. “In broad terms, we typically say the breakdown is 60% for fashion textiles, 30% for furniture textiles and 10% for technical applications, which includes composites.”
The supply chain for flax and hemp themselves also continues to grow, but as with any agricultural product, it can be somewhat volatile. And though materials suppliers agree that the quality of the product has come a long way in recent years, measurement of that quality and standardization are still ongoing endeavors.
Core Technology Molding turned to Mold-Masters E-Multi auxiliary injection unit to help it win a job and dramatically change its process.
Over the past two or three years, sustainability has become increasingly important. Once a niche interest, sustainability focused on emissions reduction is now being driven by standards. Governments, regulatory organizations, OEMs and consumers are demanding materials and process solutions that favor decarbonization.
After successfully introducing a combined conference for moldmakers and injection molders in 2022, Plastics Technology and MoldMaking Technology are once again joining forces for a tooling/molding two-for-one.
Nowadays, many of those new requests make use of the company’s now extensive injection molding capabilities, including new sizes of totes and a line of molded plastic glassware. “If you ask me: have I ever made a drinking glass before — the answer would be no. Do I feel that the drinking glasses that we’re going to be coming out with are going to be exceptionally good and very well received? Absolutely.”
EU project will develop bio-based, repairable and recyclable vitrimer composites and advanced sensors for highly reliable, sustainable wind blades.
Automotive exteriors. Starting with motorsports and Formula 1, natural fibers continue to find a place in high-performance automotive exteriors and supercars. The bottom image shows the focus on flax fiber composites for the Porsche 718 Cayman GT4 Clubsport MR, featuring Bcomp ampliTex and powerRibs. Photo Credit: BMW M Motorsport, via Bcomp Ltd. (top image) and Dr. Ing. h. c. F. Porsche AG, via Bcomp Ltd. (bottom image)
Oberste notes that use of natural fiber tapes over the past year has been new for WEAV3D, involving a back-and-forth process with the tape supplier to optimize the materials and the processing. “The behavior of the tape is different, and it handles differently,” he explains. For example, natural fiber tapes are more prone to curling or twisting, but must consistently lie flat to go through the WEAV3D machine or other processes.
Also in the interiors space, Culture iN (Montaigu-Vendee, France) was founded in 2014 with the goal of producing sustainably sourced and processed textiles for furniture and luggage applications. Company founder David Ambs “wanted to change our living spaces” to be more focused on “sensorial appeal [and] respect for health and the environment,” explains Ronan Legrand, commercial director.
Low-melt polyaryletherketone (LMPAEK) unidirectional tapes provide outstanding thermal and fire protection, demonstrating their effectiveness through rigorous testing. These tapes are fire, smoke and toxicity compliant with FAR25.853 and meet OSU Heat Release Rate standards. The tapes were tested under ISO 2685/AC 20-135 Change 1, meeting the fireproof criteria. Additionally, they met UL 2596 requirements for battery thermal runaway tests. These tapes are crucial for high-temperature applications showcasing their resilience and safety in both aerospace and automotive applications. Part of a broader range that includes films and compounds, Victrex LMPAEK materials are valued for their excellent processability and weldability. They offer versatile solutions for complex needs beyond traditional structural parts, such as: thermal runaway and lightning strike protection, heat sinking, and intricate bracketry. Victrex LMPAEK materials facilitate automation and high-rate production while addressing performance and sustainability challenges. With reduced environmental impact, lower weight and cost-efficiency, they meet the evolving demands of the transportation industry and support innovative design solutions. Agenda: Introduction to LMPAEK ecosystem, highlighting unidirectional tapes Thermal and fire protection performance: applications and benefits Material forms and processability Sustainability and efficiency Conclusion and future innovations
Thermoplastics for Large Structures, experts explored the materials and processing technologies that are enabling the transition to large-part manufacturing.
Led by global and industry-wide sustainability goals, commercial interest in flax and hemp fiber-reinforced composites grows into higher-performance, higher-volume applications.
Today, numerous suppliers have natural fiber materials marketed for composites use. Bcomp Ltd. (Fribourg, Switzerland) launched its first two products in 2012. The company’s powerRibs reinforcement grids and ampliTex dry fabrics and prepregs come in a range of compatibility options, including thermoplastics or thermoset resins, and processes including resin transfer molding (RTM), vacuum infusion, autoclave cure or compression molding.
This collection features detail the current state of the industry and recent success stories across aerospace, automotive and rail applications.
Reinforcing NFCs with lattices. WEAV3D Inc. produces carbon, fiberglass or natural fiber lattice reinforcements for a variety of materials. The company has recently entered the NFC space with its hemp and jute-reinforced NFC panels for automotive trunks and other interior applications. Photo Credit: WEAV3D Inc.
In 2018, Teijin broke ground on a facility that is reportedly the largest capacity carbon fiber line currently in existence. The line has been fully functional for nearly two years and has plenty of room for expansion.
In this collection of articles, two of the industry’s foremost authorities on screw design — Jim Frankand and Mark Spalding — offer their sage advice on screw design...what works, what doesn’t, and what to look for when things start going wrong.
This collection details the basics, challenges, and future of thermoplastic composites technology, with particular emphasis on their use for commercial aerospace primary structures.
A showroom displays just some of the totes, containers and shelving US Merchants produces at molding facilities across the U.S. Photo Credit: Plastics Technology
technotrans says climate protection, energy efficiency and customization will be key discussion topics at PTXPO as it displays its protemp flow 6 ultrasonic eco and the teco cs 90t 9.1 TCUs.
Program will focus on sustainable, next-gen wing solutions, including in wing design and manufacturing and advancements in carbon fiber-reinforced composite materials.
Lingrove has worked to develop ekoa for automotive interiors for years, and is now targeting structural applications in the construction industry.
As US Merchants’ business has grown, so has its capabilities, driven by Green’s intense interest in maximum control over everything that can impact his business. “You could say I’m something of a very controlling individual,” Green says. “I always felt that we need to control our own destiny. When you have to farm things out to third parties, you’re only asking for issues with delivery and excuses why something can’t be done.”
This includes the company’s NAFILean products, a hemp fiber-based, injection-moldable material first launched in 2011 for components like instrument panels. The company also offers natural fiber-reinforced polypropylene (NFPP) products that can be compression molded and combined with other materials like recycled carbon fiber. New product lines and serial applications for NAFILean and NFPP are reported to be underway.
GETTING A QUOTE WITH LK-MOULD IS FREE AND SIMPLE.
FIND MORE OF OUR SERVICES:
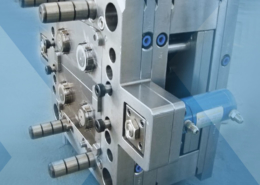
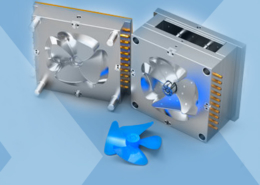
Plastic Molding

Rapid Prototyping
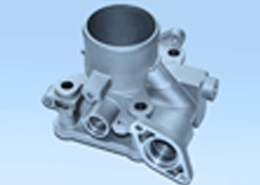
Pressure Die Casting
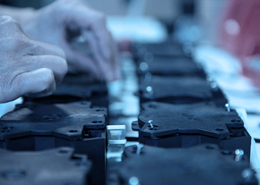
Parts Assembly
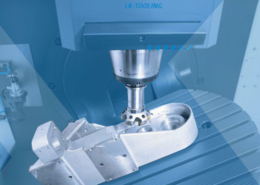