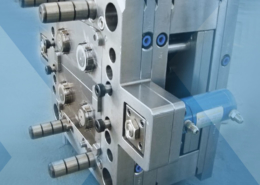
Troubleshooting Challenge: Injection Molding Machine Can’t Finish the Job - smal
Author:gly Date: 2024-09-30
Ridat has delivered a Model 4030MM Midmatic Vacuum Forming Machine and 406RCP Roller Cutting Press to the company, which is a provider of turnkey solutions for medical device companies.
Antolin, one of the largest international suppliers for automotive interiors and a leader in innovation and sustainability, is the commercial partner for the TECP award. “The use of WEAV3D reinforcements promises to reduce the weight of our NFPP components, which in turn reduces CO2 emissions and trims waste to improve the overall sustainability of these parts,” said Pablo Soto, materials specialist with Antolin’s Corporate Innovation Department. This supports Antolin’s sustainability commitments to reduce CO2 emissions by 75% and nonhazardous waste generation by 10% by 2028.
Ridat’s Model 4030MM Midmatic Vacuum Forming Machine is a reel-fed thermoformer with a forming area of 1000mm x 750mm. Its operation is fully automatic and this allows for uninterrupted production with minimum operator supervision. The material is indexed with a set of rollers powered by a stepper motor, and a centre pull guillotine powered by a pneumatic cylinder separates the sheets.
Ridat has more than 60 years of heritage in thermoforming equipment manufacturing and in supplying allied ancillaries, and it has more than 2500 installations in over 65 countries.
Ridat’s technology will help 3BY to further enhance its manufacturing capabilities and achieve greater production efficiency.
Germany’s Polyvlies, a supplier of nonwoven materials, is also participating in the project. The company’s Naroplast thermoplastic natural-fiber nonwoven textile-based composite targets automotive compression molding applications. “WEAV3D’s ability to tailor the tapes and woven patterns to the application provides an extremely flexible way to increase the strength and stiffness of the panels while improving design flexibility,” said Axel Hinrichs, CEO of Polyvlies USA. Polyvlies natural nonwoven composites have been used on a commercial basis by the likes of Mercedes Benz, Volkswagen, BMW, and Jaguar.
Ridat has demonstrated its ability to support the international medical devices market, through a new project for 3BY, which is headquartered in Northern Galilee, Israel.
Composite materials and processing innovator WEAV3D Inc. has been awarded a $200,000 Technology Enhancement for Commercial Partnerships (TECP) supplement to its 2021 National Science Foundation (NSF) Small Business Innovation Research (SBIR) Phase II grant. The new award focuses on the use of WEAV3D’s woven composite lattices to enhance the performance and sustainability of natural-fiber polypropylene (NFPP) composites for automotive applications.
This additional award follows a previous $1 million grant to fund the design, fabrication, and testing of a continuous composite forming line that uses ultrasonic welding to increase production throughput of WEAV3D’s patent-pending process. This next-generation system is being built according to automotive production speed and quality standards, with a target production capacity of 200,000 to 300,000 automotive door panel size parts per year and per machine.
The model also includes standard Ridat features such as a user-friendly micro-processor system that assists with fault finding and has zone control capabilities for accurate zone temperature control.
WEAV3D’s compression molding technology for natural fiber composites is a cost-competitive alternative to processes such as resin transfer molding and automated fiber placement.
“This grant will fund a detailed study of mechanical performance and manufacturability of lattice-reinforced NFPP panels, including the development and validation of finite element simulation tools,” said Chris Oberste, president of WEAV3D and principal investigator for this award. “Our technology enhances the performance of NFPP materials, enabling these sustainable materials to be optimized for a range of applications within the vehicle.”
Stephen has been with PlasticsToday and its preceding publications Modern Plastics and Injection Molding since 1992, throughout this time based in the Asia Pacific region, including stints in Japan, Australia, and his current location Singapore. His current beat focuses on automotive. Stephen is an avid folding bicycle rider, often taking his bike on overseas business trips, and is a proud dachshund owner.
The grant from the National Science Foundation (NSF) will fund a study of the performance and manufacturability of lattice-reinforced natural-fiber polypropylene (PP) panels for automotive applications.
GETTING A QUOTE WITH LK-MOULD IS FREE AND SIMPLE.
FIND MORE OF OUR SERVICES:
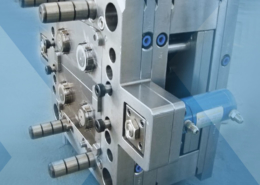
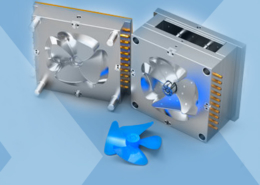
Plastic Molding

Rapid Prototyping
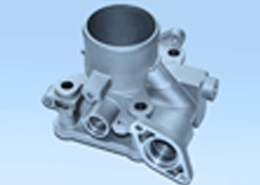
Pressure Die Casting
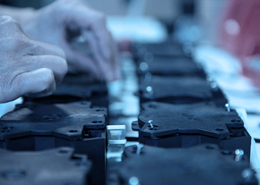
Parts Assembly
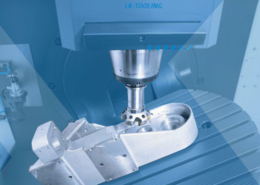