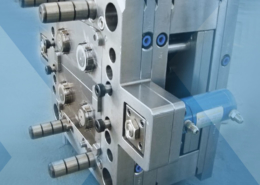
Toyota first to adopt plasma-coated polycarbonate rear quarter window - polycarb
Author:gly Date: 2024-09-30
Until she retired in September 2021, Clare Goldsberry reported on the plastics industry for more than 30 years. In addition to the 10,000+ articles she has written, by her own estimation, she is the author of several books, including The Business of Injection Molding: How to succeed as a custom molder and Purchasing Injection Molds: A buyers guide. Goldsberry is a member of the Plastics Pioneers Association. She reflected on her long career in "Time to Say Good-Bye."
Rotomolding has emerged as a highly effective and versatile alternative to traditional injection molding. Its unique process offers numerous advantages, including design flexibility, cost-effectiveness, seamless construction, suitability for large parts, and versatility in material selection. As manufacturing continues to evolve, rotomolding stands at the forefront, paving the way for innovative solutions and redefining the possibilities of plastic product production.
Rotational molding, often referred to as rotomolding, is a manufacturing technique that creates hollow plastic products by rotating a mold along two perpendicular axes. In contrast to injection molding, where molten plastic is forcefully injected into a closed mold under high pressure, rotomolding leverages the forces of gravity and centrifugal motion. This distinctive approach enables the production of expansive, intricate, and flawlessly constructed components characterized by consistent wall thickness.
The rotomolding process typically consists of four primary stages: loading, heating, cooling, and unloading. To initiate the process, a precise amount of plastic resin is loaded into the mold, which is then heated as it rotates in an oven. The heat causes the resin to melt and coat the interior of the mold, forming the desired shape. Subsequently, the mold is cooled, solidifying the plastic, and the finished product is unloaded.
Rotomolding supports a wide range of plastic materials, including polyethylene, polypropylene, and PVC, providing manufacturers with flexibility in choosing the most suitable material for their specific application. This adaptability extends the potential applications of rotomolded products across various industries.
Dynapack Asia operates over 30 manufacturing sites across Southeast Asia and China and intends to collaborate with its customers to increase the use of recycled materials and products, strengthening the region’s recycling ecosystem and achieving a circular economy. The company specializes in extrusion blow molding and injection molding for the manufacture of bottles, jars, caps and closures as well as precision molded parts for the personal and baby care, food and beverage, home cleaning, lubricant, pharmaceuticals, automotive and other industries.
In the dynamic world of manufacturing, innovation constantly pushes the boundaries of traditional methods. One such groundbreaking technique that has gained widespread recognition is rotomolding, a process revolutionizing the production of hollow plastic products. This blog post will delve into what rotomolding is and explore why it stands out as a formidable alternative to the more conventional injection molding.
Coca-Cola Amatil Indonesia (Amatil) has entered into a Heads of Agreement with long-term packaging partner Dynapack Asia to build what it calls the most sophisticated state-of-the-art bottle-to-bottle grade PET recycling facility in Indonesia.
“It is a significant step toward Amatil becoming self-sustaining in the plastic materials we use, ensuring a closed loop for plastic beverage packaging in Indonesia as a whole,” he added.
One of the standout features of rotomolding is its ability to produce seamless and stress-free products. The absence of joints or weld lines enhances the durability of the final product, making it ideal for applications where structural integrity is paramount. This seamless construction also contributes to a more aesthetically pleasing appearance.
Compared to injection molding, rotomolding requires simpler and less expensive molds. This is particularly advantageous for small to medium production runs, as the initial tooling costs are significantly lower. Additionally, the ability to mold multiple parts simultaneously can further expedite the production process, making rotomolding an economically viable option.
Rotomolding’s suitability for manufacturing large, single-piece products is a major advantage over injection molding. From industrial tanks and containers to playground equipment and automotive components, rotomolding excels in producing sizable items without sacrificing quality or efficiency.
President Director of Coca-Cola Amatil Indonesia, Kadir Gunduz, said the two companies have established a joint project team to leverage each company’s expertise in respective parts of the production and recycling process. “This joint venture represents a real environmental step-change in our move toward a more sustainable approach to plastic and a circular economy by bringing low-quality PET waste back to virgin-quality, food-grade PET, which also echoes the Coca-Cola Company’s ‘World Without Waste’ vision,” said Gunduz.
President Director of Dynapack Asia, Tirtadjaja Hamball, commented: “To support our environmental responsibility, we have signed a global commitment with the Ellen McArthur Foundation to use at least 25% of recycled resin material in our packaging products by 2025. This recycled PET resin facility is another step closer to achieving our commitment.”
The use of recycled plastic could reduce the amount of new plastic resin the company uses by an estimated 25,000 tonnes each year by 2022. This aligns with a commitment through the National Plastic Action Partnership to support Indonesia’s National Action Plan in achieving a 70% reduction in the nation’s marine plastic debris by 2025.
Amatil and Dynapack will work together through a proof of concept phase, which is intended to consider a potential plant’s economic feasibility, size, scale, and location; end-to-end requirements; and potential integration into each company’s value chains.
Rotomolding provides exceptional design flexibility, enabling the crafting of intricate and sophisticated shapes that might pose challenges or be unattainable through alternative molding techniques. The rotational nature of the process guarantees consistent thickness across the product, eradicating vulnerabilities and elevating structural strength.
GETTING A QUOTE WITH LK-MOULD IS FREE AND SIMPLE.
FIND MORE OF OUR SERVICES:
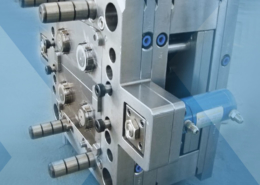
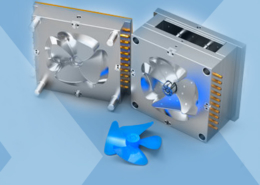
Plastic Molding

Rapid Prototyping
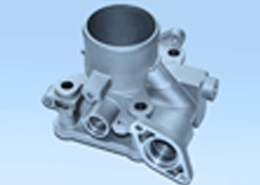
Pressure Die Casting
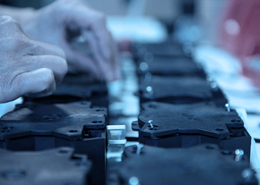
Parts Assembly
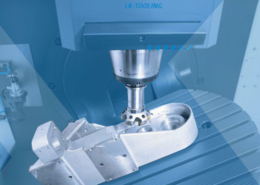