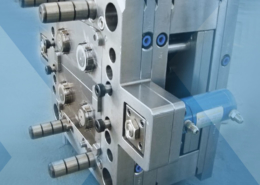
Toward Biodegradable and Recyclable Luminescent Polymers - biodegradable plastic
Author:gly Date: 2024-09-30
Long before Tesla/SolarCity announced its new solar-roof products last month, Dow launched its PowerHouse Solar Shingles in 2009, designed to integrate directly into the roof. By 2011, the company’s “groundbreaking” product was struggling to survive. This summer, with the product no longer viable and a pending merger with DuPont looming, Dow decided to stop making the PowerHouse entirely.
The online auction house Hilco Global announced the equipment, including plastic-injection molding machines, solar-cell welding systems, glass washers, sun simulators, laminators — among other equipment — had been sold. Neither the buyer or the financial terms of the sale were disclosed.
Proper training of installers and a global infrastructure of independent contractors is the key . We plan to support them with equity crowdfunding.
BIPV isn’t failing because of a lack of job sites – it’s failing because solar has not bridged the general labor gap due to subsidy-driven economics.
Liquid silicone injection moulding: This produces pliable, durable parts in high volume, and is used in fabricating tubes and respiratory masks requiring high levels of hygiene and chemical resistance.
Once the conventional PV sites are tapped out — if that ever happens — the value of solar-generating windows, walls and roads will increase. Until then, BIPV frequently amounts to paying a premium for less of a return. That math has already killed a long line of companies.
Your personal data will only be disclosed or otherwise transmitted to third parties for the purposes of spam filtering or if this is necessary for technical maintenance of the website. Any other transfer to third parties will not take place unless this is justified on the basis of applicable data protection regulations or if pv magazine is legally obliged to do so.
Dow announced on June 28, 2016, that it will cease manufacturing POWERHOUSE modules. As part of the transition to cease POWERHOUSE operations, we will no longer be providing design services for new projects. Dow will continue to support warranties issued on existing POWERHOUSE Systems.
we are a Lebanese company working in brick and construction materials and I saw your company portfolio and we are interesting in your product. so please we would like from you to contact us via email: chtoura@mcic.company we are waiting your replay as soon as possible.
The indelible imprint of injection moulding in medical manufacturing underscores its pivotal role in delivering efficient, high-quality, and cost-effective solutions to the industry. As the medical field continues to evolve, the synergy between injection moulding and emerging technologies like 3D printing is poised to drive innovation further, ensuring the continual enhancement of patient care and medical advancements.
In the realm of medical device manufacturing, the tussle between traditional injection moulding and modern 3D printing technologies continues. However, injection moulding has held its ground firmly, especially when high-volume production, cost-effectiveness, and precision are all paramount.
Products exist for flashing, taping, gluing and sealing skylights, windows, air condition hatches, and kinds of rectangles to our rooftops. What the solar industry lacks are general contractors who know how to properly flash and seal roofing systems. Instead, we have installers who know a little electrical and not alot of roofing whom target going after the low hanging fruit, driven by a subsidy business model that shortcuts traditional design-bid-build construction processes. If our past decade of “NABCEP”-driven subsidies had instead targeted roofing contractors with 10+ years roofing experience, and if our “green collar job” education grants had targeted architects/engineers instead of community college students, we’d have general contractors building true solar rooftops by now.
As Julian Spector at GTM Research wrote this summer when Dow originally announced it would no longer manufacture the PowerHouse shingles:
Gas-assisted injection moulding: In certain medical device applications, gas-assist moulding can provide solutions that conventional injection moulding can’t. The process consists of injecting a pressurised gas into the mould cavity after the initial plastic injection, expelling the molten plastic and forming hollow areas within the final product. It is suited to the manufacturing of complex parts without visual blemishes, for instance, tube- or rod-shaped parts which typically include handles and foot pedals, as well as large, cover-shaped structural parts e.g. side panels and covers for medical devices.
Luke Smoothy, founder and director, Get It Made, delves into why injection moulding still holds the sceptre in the medical industry and highlights the key benefits it brings.
Instead, our protectionist solar import tariffs stifle innovation, while shoveling subsidy dollars over to the utilities who attack distributed solar, while stoking a political climate which has put Rick Perry as the head of the DoE.
You may revoke this consent at any time with effect for the future, in which case your personal data will be deleted immediately. Otherwise, your data will be deleted if pv magazine has processed your request or the purpose of data storage is fulfilled.
Elon Musk is now betting Tesla/SolarCity’s future that he can buck the trend Dow’s PowerHouse solar shingles pioneered. As Dow’s solar shingles business gasps its last breath, the industry awaits to see if Musk’s intuition is correct.
Since the need for devices and components in the medical sector is always increasing, injection moulding stands out for its effectiveness and capacity to handle large-scale orders. The method is best suited for high-volume production, making it the preferred method for mass-producing medical components. That said, even though 3D printing is hailed for having cheaper initial costs in small-scale production, its cost advantage diminishes as production volume rises.
When your labor force is comprised of installers who know very little about roofing, how can the product be integrated into the roof?
With the final sale of its manufacturing equipment, the chemical giant’s dreams of leading a solar-roofing revolution have officially ended.
Five years after Dow Chemical promised to change the way people thought of solar shingles, it sold the last of its manufacturing equipment to an unknown buyer.
The timing of the final sale is ironic, given the hoopla surrounding Tesla’s solar-roofing products, which are expected to into mass production next summer. Roof-integrated solar has been a goal for at least the last seven years, and no one has been able to move the needle enough to make it the centerpiece of its business.
John, you know well about this product. Ocean View, Delaware I have a home that … desperately needs a new roof and I do not want to get the normal shingles if I can get a Solar Shingles that it is awesome to hear that exsist .. with the right co. to install it. Do you know any Co. in that area .. zip code 19970 and my cell is 703-624-0027
An expansive range of materials are available with injection moulding, making it easier to produce medical equipment that adheres to the strict biosafety and chemical stability criteria of the medical sector. Techniques such as thin wall moulding and gas-assisted injection moulding enable the production of both practical and aesthetically appealing parts.
This content is protected by copyright and may not be reused. If you want to cooperate with us and would like to reuse some of our content, please contact: editors@pv-magazine.com.
The cookie settings on this website are set to "allow cookies" to give you the best browsing experience possible. If you continue to use this website without changing your cookie settings or you click "Accept" below then you are consenting to this.
John, you make some excellent points. Our team is planning to support the proper installation of Aesthetics Solar Roofing (ASR).
Thin wall moulding: A specialised form of conventional injection moulding that focuses on the mass production of ultra-thin (less than 1mm) and light plastic parts to make material cost savings. This is used to create portable medical devices enabling clinicians and patients to transport and operate them more easily - such as wearable devices, micro surgical tools, and invasive equipment like catheter ablation tools and endoscopes.
pv magazine USA offers daily updates of the latest photovoltaics news. We also offer comprehensive global coverage of the most important solar markets worldwide. Select one or more editions for targeted, up to date information delivered straight to your inbox.
As a homeowner interested in an architecturally acceptable (shingles vs panel) solution to PV generation, I remain confused by “plummeting cost” in solar equipment production and my inability to find distributors and installers in the Midwest. There are plenty of panel installers emerging, but my house is a perfect south facing ranch in need of a new roof, and I don’t want to buy a new roof, then overlay a panel system. Any ideas and advice are welcome.
Perhaps intriguingly is the fact that 3D printing and injection moulding are not exclusive of one another. Injection moulding is frequently preceded by 3D printing, which assists with prototyping and even helps create moulds for the injection moulding process.
Well-suited for products with straightforward shapes, injection moulding delivers unrivalled precision and finish quality. For medical applications such as moving machine parts or implantable devices, the procedure gives a vital smoother finish.
GETTING A QUOTE WITH LK-MOULD IS FREE AND SIMPLE.
FIND MORE OF OUR SERVICES:
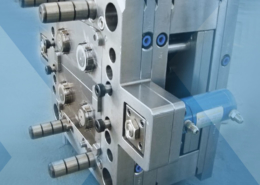
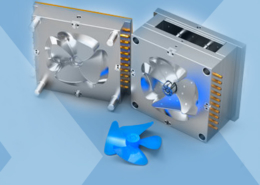
Plastic Molding

Rapid Prototyping
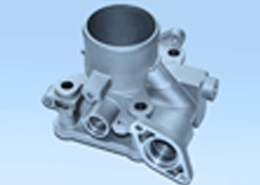
Pressure Die Casting
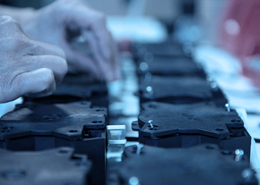
Parts Assembly
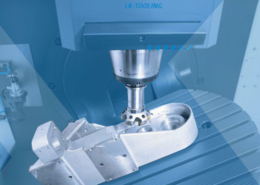