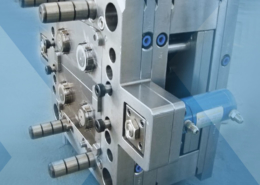
Top Shops Benchmarking Report: Molding at the Margin - plastic mold price
Author:gly Date: 2024-09-30
Presma has developed a new press expressly for coinjection molding. The new GTS200 Bic has two identical injection units, which can inject through the same nozzle simultaneously. It also has a rotary table. At the show, the unit produced a door handle with a foamed PP core and TPE skin.
After shrinking its machinery portfolio last year from 18 to three main product lines (with a fourth to be built as needed), DPG has rolled out a brand-new hydraulic line for general-purpose use. This “Pink” series is based on its Systec hydraulic line but is lower priced due to the fewer available options. It replaces the company’s former Extra series. Sizes range from 38.5 to 462 tons. Models larger than 500 tons will be developed this year.
In a time where sustainability is no longer just a buzzword, the food and beverage packaging industry is required to be at the forefront of this innovation. By adopting circular packaging processes and solutions, producers can meet regulatory requirements while also satisfying consumer demand and enhancing brand reputation. Join Husky to learn more about the broader implications of the circular economy — as well as how leading brands are leveraging this opportunity to reduce costs, increase design flexibility and boost product differentiation. Agenda: The cost and operational benefits of embracing circularity Key materials in circular packaging — including rPET and emerging bioplastics How to design a circular food and beverage package Strategies for selecting sustainable closures to future-proof packaging solutions Optimization and streamlining of production processes for enhanced efficiency How Husky Technologies can enable your sustainable success
KraussMaffei introduced a small two-platen line for general-purpose applications. The ClassiX line is based on KM’s CX series but with fewer options and about 15% lower price and faster shipping (around 20 days from order to delivery). It runs from 38 to 143 tons and comes with hydraulic or electric drive for the screw and ejector. A cantilevered clamp helps to free up floor space and allows access from three sides. A KM65-180CX press was teamed with the firm’s new LRX-S 50 top-mounted linear robot (33-lb payload capacity).
At the big “K” Show next month, top billing goes to new all-electric machines aimed at every segment of the market, from general-purpose to high-end.
Billion SAS of France (represented here by Oaktree Consulting), unveiled its first all-electric machines, the Select series from 75 to 150 tons. Each unit has at least six AC servo motors (nine with two injectors for multi-material molding, which is Billion’s specialty). This five-point toggle machine uses ballscrews for ejection and nozzle touch and planetary roller screws for injection and clamping, where higher force and precision are required. At the show, Billion demonstrated two-shot molding with its 110-ton Select Multi H150/260-100T, which made a garage-door opener from glass-filled PBT and TPE in 35 sec.
Multiple speakers at Molding 2023 will address the ways simulation can impact material substitution decisions, process profitability and simplification of mold design.
Demag Plastics Group (DPG) announced previously that it had revamped and expanded its all-electric IntElect series with its new NC5 control and high-torque water-cooled direct drive motors for all main movements. A 385-ton and 462-ton model will be added to the line, which currently ranges from 55 to 230 tons. Lower cost IntElect models made in China will debut this year, starting with a 110-tonner, and later adding models from 27 to 220 tons.
Husky demonstrated its In-Line Compounding (ILC) cell for long-glass mixing and molding, which mounts a Coperion twin-screw compounder on a plunger injection machine. Germany-based Brose is using it to mold door-module carriers converted from metal. French-based Faurecia is using the ILC to lightweight door-module carriers for Ford.
Chen Hsong’s new Supermaster TP two-platen series of large machines is targeting automotive applications. Seven sizes range from 2420 to 7150 tons, all with the new Ai-11 control. Clamp movements are said to be as fast as 750 mm/sec A patented tiebar hydraulic connection reportedly reduces stress concentrations and simplifies maintenance.
Automation is a must-have for molders of pipettes. Make sure your supplier provides assurances of throughput and output, manpower utilization, floor space consumption and payback period.
Husky unveiled a new HyPET high-performance package for PET preform molding that reportedly trims cycle times of high-cavitation tools by 15%. Refinements were made to the mold, robot, injection unit, clamp, and auxiliary equipment. At the show, a 96-cavity HyPET system molded 12.1-g, 500-ml water-bottle preforms in 5.5 sec, which compares with 6.5 to 7.0 sec with a standard package.
Ningbo Zhafir, which will be run as a stand-alone unit, will concentrate on electric machines. The new Venus series is said to be an optimization of Haitian’s HTD electric series and uses a number of European components. The double-toggle press is driven by five AC servo motors with belts and ballscrews. The control system from Sigmatek of Germany reportedly provides 0.25-millisec response time. The software also allows users to program for injection-compression molding. The machines come in a range from 44 to 451 tons and are assembled in Germany, although most of the machines will be shipped to Asia. Each press size offers a choice of four injection units with three screws apiece. Zhafir claims 70% energy savings vs. comparable hydraulic machines. Zhafir also is developing a tiebarless all-electric machine called Mercury with two-stage injection and models from 44 to 550 tons.
Despite price increase nominations going into second quarter, it appeared there was potential for generally flat pricing with the exception of a major downward correction for PP.
Learn about sustainable scrap reprocessing—this resource offers a deep dive into everything from granulator types and options, to service tips, videos and technical articles.
As reported in September, Netstal launched its smallest size PET-Line model to date, the PET-Line 2000 (220 tons), suitable for 24- to 48-cavity molds.
A 385-tonner produced thin-wall, MuCell-foamed PP containers with in-mold labeling in a 4+4 mold on a 5-sec cycle (110-g shot weight), while a 550-ton unit made closure spouts from LDPE in a 144-cavity mold in 3.75 sec (144-g shot).
Arburg has extended the size range of its Golden Edition series with three new models. The new 506-ton Allrounder 920 S Golden Edition has 920 x 920 mm tiebar spacing and shot capacity up to 2.8 lb. Arburg also added two vertical rotary-table models to the Golden Edition—the 88-ton Allrounder 1200 T 800 and 110-ton Allrounder 1200 T 1000.
A brand-new line of all-electric machines priced on par with comparable hydraulic presses and the first public demonstration of insert molding RFID chips into plastic parts will be two highlights of the Engel display at the mammoth K 2007 show in Dusseldorf, Germany, this October.
Engel demonstrated the new Exjection process that produces long thin parts by “intrusion molding,” a combination of injection and extrusion, involving gradual filling of a vertically moving mold cavity. The process was developed by IB Steiner Innovation Business and Hybrid Composite Products GmbH in Germany and has been licensed to both Engel and Arburg.
Octopus Energy Generation has also continued its commitment to Be.EV, with further funding allocated as part of the £110m cash injection announced in 2022. Octopus’ investment was made on behalf of the Sky fund (ORI SCSp) it manages, which has a majority stake in Be.EV.
Bemis Mfg. is using Ferromatik’s K-Tek press and a 6 x 4 cavity, four-face turning-cube mold from Foboha to produce a toilet-seat mounting bracket of PP and TPE with three living hinges. It replaces an eight-piece assembly.
Second quarter started with price hikes in PE and the four volume engineering resins, but relatively stable pricing was largely expected by the quarter’s end.
Tiny electric presses for micro-molding also made news. MCP Tooling Technologies launched its new 12/90 all-electric model, which has a clamp force of 9.9 tons and shot sizes from 1.6 g down to a few milligrams. It is designed as a clean-room machine and uses a reciprocating screw instead of a plunger.
Thousands of people visit our Supplier Guide every day to source equipment and materials. Get in front of them with a free company profile.
The Plastics Industry Association (PLASTICS) has released final figures for NPE2024: The Plastics Show (May 6-10; Orlando) that officially make it the largest ever NPE in several key metrics.
New machinery supplier Zhafir, part of China-based Ningbo Haitian, unveiled its German-built Venus line of all-electric machines from 44 to 451 tons.
Sandretto added a 495-ton model to its Nove HPF line of fast cycling hybrid presses for packaging. The largest model had been 396 tons. The line has electric screw drive, with all other motions driven hydraulically. In addition, Sandretto is building a plant in Shanghai and is developing a new Nove HP line that will combine European and Chinese machine concepts.
If you were looking for a new machine to mold micro- or mega-sized parts, multiple materials, long fibers, high-speed/high-cavitation packaging, exotic multi-material combinations with compounding on the machine, or just a cost-effective press for general-purpose use—K 2007 had it all.
In this collection of content, we provide expert advice on welding from some of the leading authorities in the field, with tips on such matters as controls, as well as insights on how to solve common problems in welding.
Billion of France rolled out its new Select all-electric line from 75 to 150 tons. Billion specializes in multi-barrel units, which have nine AC servos.
Formnext Chicago is an industrial additive manufacturing expo taking place April 8-10, 2025 at McCormick Place in Chicago, Illinois. Formnext Chicago is the second in a series of Formnext events in the U.S. being produced by Mesago Messe Frankfurt, AMT – The Association For Manufacturing Technology, and Gardner Business Media (our publisher).
This month’s resin pricing report includes PT’s quarterly check-in on select engineering resins, including nylon 6 and 66.
“It proves that investors, both domestic and international, are confident in the UK’s transition to EVs and its importance in transitioning to a net zero economy.”
Desma Tec, a subsidiary of Klockner Desma Schumaschinen, a German maker of urethane and rubber machines, rolled out the FormicaPlast micro-injection molder that can make small parts from thermoplastics or metal powders. Developed by the Kunststoffzentrum (KUZ) scientific institute in Leipzig, this servo-electric toggle system features a two-stage screw/plunger system for highly responsive molding and injection speeds up to 500 mm/sec. The 1.1-ton unit molds parts weighing less than 0.28 mg. The Desma-Tec line is sold here by Creative Mold.
The funds will also help Be.EV to cement its foothold in Manchester and the North West, where it’s already installed more than 600 charge points. These are accessible to all members of the public, with the 35,000 Be.EV members able to charge their EVs at discounted rates. The chargers are powered by renewable energy from Octopus Energy.
Discover how artifical intelligence is revolutionizing plastics processing. Hear from industry experts on the future impact of AI on your operations and envision a fully interconnected plant.
Arburg also merged its smaller Allrounder U line into its larger Allrounder S series and added a new size to create a more comprehensive hydraulic product line. The Allrounder S line now has 10 models from about 15 to 550 tons, including the brand-new 220-ton Allrounder 570 S. Selogica Direct touchscreen controls are available at no extra charge. The fully accumulator-driven presses come with optional electric screw drive.
As reported in September, Engel introduced its e-max line, the first all-electric machines that are price-competitive with comparable hydraulic machines.
Stork Plastics Machinery, a Dutch press maker with a new U.S. rep, rolled out its new S+ series of accumulator-assisted large machines. The successor to its S series comes in sizes from 110 to 1540 tons and features a new drive system and improved controls. A new Eco Mode function adapts the drive system to the process for energy savings, says Anthony Thompson, the U.S. rep. Users can select a fully hydraulic model or hybrid version with electric screw drive.
The majority of chargers supported by the new money will be ultra-rapid. There are currently only 5,336 locations in the UK that offer rapid and ultra-rapid charging.
One of automation’s key promises is repeatability: the same movement to the same location, time and time again. But to achieve that, all elements involved — robot, machine, EOAT, mold — must be in and stay in alignment.
Husky’ In-Line Compounding system fed continuous glass rovings to a Coperion twin-screw compounder (left). Long-glass PP mix was injected into a Quadloc Tandem press with two independent molds (far left below) producing Ford door-module carriers, handled by two six-axis Fanuc robots (far left above).
Processors with sustainability goals or mandates have a number of ways to reach their goals. Biopolymers are among them.
At the show, Husky ran a version of its ILC on an 1485-ton Quadloc Tandem press molding long-glass/PP door-module carriers in two standard molds arranged in a stack-type system. The 5.3-lb shot required a 50-sec cycle. Two Fanuc six-axis robots mounted on the tiebars demolded the parts.
Be.EV said the funding was a milestone in a nascent sector for debt and served as a strong vote of confidence from the banking industry that the public charging industry is a sound investment. The support from Germany’s KfW IPEX-Bank also gives strong endorsement of the UK from abroad.
It’s all about sustainability and the circular economy, and it will be on display in Orlando across all the major processes. But there will be plenty to see in automation, AI and machine learning as well.
While the melting process does not provide perfect mixing, this study shows that mixing is indeed initiated during melting.
Husky announced several enhancements to its Hylectric machines designed for production of closures. These include a new high-output screw drive and a new screw design that ensures melt quality and maintains control of melt temperature at high throughput rates. The system was demonstrated with Husky’s new Ultra 350 hot-runner valve gate for improved part quality, tight gate pitch, and throughputs up to 30 g/sec.
Take a deep dive into all of the various aspects of part quoting to ensure you’ve got all the bases—as in costs—covered before preparing your customer’s quote for services.
Chen Hsong rolled out its Jetmaster Ai electric/hydraulic hybrid series designed for fast cycles and energy savings. The line uses either Bosch Rexroth or Moog servo valves to control the accumulator-assisted hydraulic system, which is said to reduce energy use by 40% compared with a fixed-pump system. They also have a new controller that reportedly enables extremely high-precision movements. Machine response time is from 25 to 60 millisec, depending on type of system selected. Injection rates range from 300 mm/sec for high-speed models to 500 mm/sec for ultra-high-speed operation. The Ai line also uses a patented circular platen design that uniformly distributes stresses for minimal platen deflection. Three models range from 108 to 196 tons. Users can add the new iChen shop-floor networking system, which is now wireless instead of LAN based.
Asif Ghafoor, CEO of Be.EV, said: “This sizeable commitment from NatWest and KfW and the continued support from Octopus Energy Generation paves the way for future investments in the industry, which ultimately benefits the EV driving community and helps the Government’s zero-emission vehicles by 2035 mandate.
Sustainability continues to dominate new additives technology, but upping performance is also evident. Most of the new additives have been targeted to commodity resins and particularly polyolefins.
MCP also introduced its all-electric 12/90 VSA model for insert molding or overmolding. The tiebarless system uses a sliding or rotary table and is suitable for medical molding.
August 29-30 in Minneapolis all things injection molding and moldmaking will be happening at the Hyatt Regency — check out who’s speaking on what topics today.
As reported in September, DPG has speeded up the clamp on its hybrid El-Exis S series for 10% to 20% faster dry cycle and updated its controller to the new NC5 design with enhanced mold protection.
Exhibitors and presenters at the plastics show emphasized 3D printing as a complement and aid to more traditional production processes.
Ferromatik showed a complex multi-component application for the rotating “cube” tooling system from Foboha of Germany. The part was the hinge mounting bracket for the new Xcite toilet seat from Bemis Manufacturing Co., Sheboygan Falls, Wis., one of the largest producers of toilet seats in the world. Bemis specializes in multi-component molding, but this is its first cube system. It molds the brackets from PP and TPE with three living hinges, replacing eight formerly separate parts that required secondary assembly. The bracket is made on a 496-ton K-Tec hydraulic machine with a four-face, 6 x 4 cavity turning stack mold. The center stack turns 90° in 1.5 sec and produces six parts every 20 sec.
KraussMaffei’s SkinForm system used a 2530-ton two-platen MX machine with rotating center stack to mold this inner door panel with a PC/ABS substrate and overmolded RIM PUR in multiple colors. (A system similar to this was sold to Korean automotive supplier Il Kwang to develop applications for Hyundai Motors and Kia Motors.)
Core Technology Molding turned to Mold-Masters E-Multi auxiliary injection unit to help it win a job and dramatically change its process.
In this three-part collection, veteran molder and moldmaker Jim Fattori brings to bear his 40+ years of on-the-job experience and provides molders his “from the trenches” perspective on on the why, where and how of venting injection molds. Take the trial-and-error out of the molding venting process.
Natalie has worked as a fleet journalist for over 20 years, previously as assistant editor on the former Company Car magazine before joining Fleet World in 2006. Prior to this, she worked on a range of B2B titles, including Insurance Age and Insurance Day. Natalie edits all the Fleet World websites and newsletters, and loves to hear about any latest industry news - or gossip.
If you were looking for a new machine to mold micro- or mega-sized parts, multiple materials, long fibers, high-speed/high-cavitation packaging, exotic multi-material combinations with compounding on the machine, or just a cost-effective press for general-purpose use—K 2007 had it all. Eight suppliers of all-electric machines—two of them new entrants—showed off theirlatest models or designs. Five makers of hybrid-electrics rolled out new models, and nearly a dozen manufacturers introduced hydraulic machines of every type. Even hydraulic presses have been tweaked for energy savings and lower cost.
A collaboration between show organizer PLASTICS, recycler CPR and size reduction experts WEIMA and Conair recovered and recycled all production scrap at NPE2024.
Ferromatik Milacron showed the first model in its new Cap-Tec line specially built for cap and closure molding. Its Cap-Tec 300 (330 tons) produced thin-wall closures from a 72-cavity mold at rates projected to be 100,000/hr. Thicker caps for carbonated beverages can be molded at up to 80,000/hr. The line is based on the K-Tec press but is stripped of functions not required for this market in order to reduce cost and raise productivity. It has an electric screw drive and accumulator-assisted hydraulic clamp with a short-stroke design for molding small parts at high speed. Both 220- and 440-tonners are in development.
Negri Bossi’s new 1320-ton VH1200 Bi-Power two-platen unit is the smallest in the line, which ranges up to 6600 tons. A new 15-in. control screen is standard.
Andreas Ufer, member of the management board of KfW IPEX-Bank said: “We are glad to have won Be.EV as a new customer and thus help advance the e-mobility infrastructure in the UK. It is our mission to support the mobility transition with our financings in Europe and worldwide and drive the change towards decarbonisation in our societies.”
Boy rolled out its PC-based Procan Alpha control for its line of small two-platen machines. It replaces the 32-bit Procan CT control and features a 15-in. touchscreen, new freely configurable programming page, and a separate hardware module that handles processing of analog signals and frees the PC from all time-critical tasks, which speeds response. An Iterative Learning Controller program helps reduce start-up and set-up times and “learns” to control process deviations in the course of a run.
technotrans says climate protection, energy efficiency and customization will be key discussion topics at PTXPO as it displays its protemp flow 6 ultrasonic eco and the teco cs 90t 9.1 TCUs.
Join KraussMaffei for an insightful webinar designed for industry professionals, engineers and anyone interested in the manufacturing processes of PVC pipes. This session will provide a comprehensive understanding of the technology behind the production of high-quality PVC pipes: from raw material preparation to final product testing. Agenda: Introduction to PVC extrusion: overview of the basic principles of PVC pipe extrusion — including the process of melting and shaping PVC resin into pipe forms Equipment and machinery: detailed explanation of the key equipment involved — such as extruders, dies and cooling systems — and their roles in the extrusion process Process parameters: insight into the critical process parameters like temperature, pressure and cooling rates that influence the quality and consistency of the final PVC pipes Energy efficiency: examination of ways to save material and energy use when extruding PVC pipe products
Zhafir Plastics Machinery, a German subsidiary of China’s Haitian International Holdings, rolled out its first machines, the Venus all-electric line, designed for thin-wall technical parts in high-end automotive, medical, and telecommunications applications. Haitian International Holdings represents the injection molding business of Ningbo Haitian Group Co., said to be the world’s biggest supplier of injection presses (18,000 sold in 2006). U.S. molders may be acquainted with Haitian Plastics Machinery, which supplies six lines of general-purpose machines.
Introduced by Zeiger and Spark Industries at the PTXPO, the nozzle is designed for maximum heat transfer and uniformity with a continuous taper for self cleaning.
The deal between the national charge point operator, UK high street bank and German state bank will enable Be.EV to expand its charging network to more than 1,000 rapid and ultra-rapid charge points by the end of 2024.
Gifted with extraordinary technical know how and an authoritative yet plain English writing style, in this collection of articles Fattori offers his insights on a variety of molding-related topics that are bound to make your days on the production floor go a little bit better.
Join Wittmann for an engaging webinar on the transformative impact of manufacturing execution systems (MES) in the plastic injection molding industry. Discover how MES enhances production efficiency, quality control and real-time monitoring while also reducing downtime. It will explore the integration of MES with existing systems, emphasizing compliance and traceability for automotive and medical sectors. Learn about the latest advancements in IoT and AI technologies and how they drive innovation and continuous improvement in MES. Agenda: Overview of MES benefits What is MES? Definition, role and brief history Historical perspective and evolution Longevity and analytics Connectivity: importance, standards and integration Advantages of MES: efficiency, real-time data, traceability and cost savings Emerging technologies: IoT and AI in MES
Mixed in among thought leaders from leading suppliers to injection molders and mold makers at the 2023 Molding and MoldMaking conferences will be molders and toolmakers themselves.
The ‘DryerGenie’ marries drying technology and input moisture measurement with a goal to putting an end to drying based on time.
Engel has its own brand-new two-color, long-glass injection molding compounder developed with German twin-screw compounding specialist Leistritz Extrusiontechnik GmbH. A 1100-ton Engel Duo two-platen machine is integrated with a Leistritz ZSE Maxx corotating twin-screw extruder. Like the KraussMaffei system, Engel runs the extruder continuously and uses a “melt pot” accumulator for intermediate storage. The system is aimed mainly at automotive, as well as pallets and crates, and it can also process natural fibers.
As noted in our September show preview, Netstal brought out its Evos hybrid toggle concept that will replace its 10-year-old SynErgy hybrid toggle line in the 220- to 500-ton range. The Evos is hydraulic except for its servo-electric screw drive, but all axes of movement are under digital closed-loop control, including the secondary movements. A new clamp design keeps platen deflection the same as in the Synergy models but the moving mass is reduced 35%. This leads to a slightly faster dry-cycle time. Addition of two digitally controlled Moog valves improves response time to 16 millisec from almost 50 millisec on the Synergy.
Mold maintenance is critical, and with this collection of content we’ve bundled some of the very best advice we’ve published on repairing, maintaining, evaluating and even hanging molds on injection molding machines.
Pink machines come with DPG’s new NC5 control, an improved oil-management system, and a choice of three screw sizes for each model. Linear guidance of the moving platen and an ultrasonic stroke-measuring system for all movement axes provide precise operation. Servovalve technology reportedly ensures parallel movement of the ejector. The line also has DPG’s activeQ mold-protection software.
Successfully starting or restarting an injection molding machine is less about ticking boxes on a rote checklist and more about individually assessing each processing scenario and its unique variables.
Mike Sepe has authored more than 25 ANTEC papers and more than 250 articles illustrating the importance of this interdisciplanary approach. In this collection, we present some of his best work during the years he has been contributing for Plastics Technology Magazine.
Additive technology creates air pockets in film during orientation, cutting down on the amount of resin needed while boosting opacity, mechanical properties and recyclability.
Meanwhile, Arburg added an Allrounder 520 A model to its all-electric toggle line targeting small and micro-component molding. It comes with clamp forces of 143 or 165 tons, and has enlarged space between tiebars to handle bigger molds. It also uses Arburg’s new small size 70 injection unit with screw diam. of 18, 22, and 25 mm, providing shot sizes up to 40 g. The Allrounder A line now spans 55 to 220 tons.
While the major correction in PP prices was finally underway, generally stable pricing was anticipated for the other four commodity resins.
As reported previously, KraussMaffei demonstrated two novel approaches to multi-material overmolding. One was its SkinForm process, which involves injection molding auto parts with a rigid thermoplastic substrate (PC/ABS in this case) and RIM overmolding with a two-component thermoset urethane skin. The other demonstration also involved overmolding a thermoplastic (glass-filled nylon 66) with urethane—only this time, the soft component was a TPU into which was blended a liquid crosslinking agent to achieve the properties of vulcanized rubber. This was the first publicly demonstrated use of KM’s two-stage, twin-screw Injection Molding Compounder (IMC) for a purpose other than mixing long-glass fiber into thermoplastic composites.
Sandretto developed its new Mega NH line from 660 to 2200 tons with software features that allow for injection/compression molding. The E1 SEF-2000 software now also allows for wireless remote communication to call for assistance or to order spare parts right from the machine. The controller can also provide details on the machine’s energy consumption relative to its production rate.
Husky demonstrated its Hypac hybrid with direct-drive electric injection unit (introduced at NPE 2006) in a lightning-fast in-mold labeling system. A 300-ton unit molded four rectangular PP containers (250-g capacity) with Husky’s Ultra Packaging hot-runner valve gate and Muller IML mold and labeling system in 2.9 sec.
Plastics Technology covers technical and business Information for Plastics Processors in Injection Molding, Extrusion, Blow Molding, Plastic Additives, Compounding, Plastic Materials, and Resin Pricing. About Us
The aim of this presentation is to guide you through the factors and the numbers that will help you determine if a robot is a smart investment for your application. Agenda: Why are you considering automation? What problems are you trying to solve? How and why automation can help Crunch the numbers and determine the ROI
In this collection of articles, two of the industry’s foremost authorities on screw design — Jim Frankand and Mark Spalding — offer their sage advice on screw design...what works, what doesn’t, and what to look for when things start going wrong.
Battenfeld now offers its HM two-platen unit in sizes above 715 tons with new 880-, 1100-, and 1430-ton models built in Austria. Battenfeld also announced plans to expand its technical center in Meinerzhagen, Germany, with molding cells for gas and water injection and foam molding.
While prices moved up for three of the five commodity resins, there was potential for a flat trajectory for the rest of the third quarter.
After successfully introducing a combined conference for moldmakers and injection molders in 2022, Plastics Technology and MoldMaking Technology are once again joining forces for a tooling/molding two-for-one.
Ultradent's entry of its Umbrella cheek retractor took home the awards for Technical Sophistication and Achievement in Economics and Efficiency at PTXPO.
Plastics Technology’s Tech Days is back! Every Tuesday in October, a series of five online presentations will be given by industry supplier around the following topics: Injection Molding — New Technologies, Efficiencies Film Extrusion — New Technologies, Efficiencies Upstream/Downstream Operations Injection Molding — Sustainability Extrusion — Compounding Coming out of NPE2024, PT identified a variety of topics, technologies and trends that are driving and shaping the evolution of plastic products manufacturing — from recycling/recyclability and energy optimization to AI-based process control and automation implementation. PT Tech Days is designed to provide a robust, curated, accessible platform through which plastics professionals can explore these trends, have direct access to subject-matter experts and develop strategies for applying solutions in their operations.
Husky also launched Flex Mold, a low-cavitation preform mold that helps reduce mold conversion costs and mold-change times. Fewer components need to be replaced when changing from one preform type to another. The body of the cavities can be changed while the tapers and gate pad remain in the mold, eliminating the need to cool and then reheat the hot runner. Flex Mold is available with eight cavities for neck finishes up to 63 mm diam. or 16 cavities for necks up to 43 mm.
Resin drying is a crucial, but often-misunderstood area. This collection includes details on why and what you need to dry, how to specify a dryer, and best practices.
Fanuc of Japan, represented here by Milacron, exhibited its new Roboshot S-2000iB all-electric series with a new FDA-approved lubricant that substitutes for grease. It has become a prerequisite for use in medical and technical applications. Fanuc demonstrated an automated workcell with a 55-ton machine molding LCP connectors that were demolded by a Fanuc robot and inspected with its iR Vision system for good/bad part separation.
Join this webinar to explore the transformative benefits of retrofitting your existing injection molding machines (IMMs). Engel will guide you through upgrading your equipment to enhance monitoring, control and adaptability — all while integrating digital technologies. You'll learn about the latest trends in IMM retrofitting (including Euromap interfaces and plasticizing retrofits) and discover how to future-proof your machines for a competitive edge. With insights from industry experts, it'll walk you through the decision-making process, ensuring you make informed choices that drive your business forward. Agenda: Maximize the value of your current IMMs through strategic retrofitting Learn how to integrate digital technologies to enhance monitoring and control Explore the benefits of Euromap interfaces and plasticizing retrofits Understand how retrofitting can help meet new product demands and improve adaptability Discover how Engel can support your retrofitting needs, from free consultations to execution
Battenfeld broadened its EM line of electric machines with a new 330-tonner, which extends the line beyond 198 tons. Battenfeld demonstrated an EM 110/300 at the show, molding LSR baby-bottle nipples in six cavities on a 25-sec cycle.
Across all process types, sustainability was a big theme at NPE2024. But there was plenty to see in automation and artificial intelligence as well.
In our September K Show preview (see Learn More), we reported on new electric and hybrid presses from Arburg, DPG, Engel, Ferromatik Milacron, KraussMaffei, Netstal, and Negri Bossi. Lots more was unveiled at the show.
Chen Hsong unveiled its first 72-cavity Chen-Pet preform molding system. It previously made systems for up to 48 cavities. The new system is driven by a new 450-ton press with hydraulic accumulator, four Moog servo valves, and two 2-axis digital motion controllers for closed-loop speed and pressure control.
Haitian Plastics Machinery introduced its new hybrid electric machine, dubbed the Mars series. It encompasses 16 models from 66 to 660 tons that replace the former J5 line. They have new controls from Keba of Austria and an AC servo-driven gear-pump system that reportedly achieves 20% to 70% energy savings vs. conventional hydraulic machines.
In this collection, which is part one of a series representing some of John’s finest work, we present you with five articles that we think you will refer to time and again as you look to solve problems, cut cycle times and improve the quality of the parts you mold.
Be.EV, the Manchester-based national EV charging network, has secured £55m in debt financing from NatWest and KfW IPEX-Bank in a landmark debt raise for the industry.
Say “manufacturing automation” and thoughts immediately go to the shop floor and specialized production equipment, robotics and material handling systems. But there is another realm of possible automation — the front office.
Engel added a new 550-ton model to its dual-toggle Speed line for high-speed packaging. It also introduced the IL 3560 inline injection unit, which can be equipped with a barrier screw for high throughput with low material stress.
Join Engel in exploring the future of battery molding technology. Discover advancements in thermoplastic composites for battery housings, innovative automation solutions and the latest in large-tonnage equipment designed for e-mobility — all with a focus on cost-efficient solutions. Agenda: Learn about cutting-edge thermoplastic composites for durable, sustainable and cost-efficient battery housings Explore advanced automation concepts for efficient and scalable production See the latest large-tonnage equipment and technology innovations for e-mobility solutions
While prices moved up for three of the five commodity resins, there was potential for a flat trajectory for the rest of the third quarter.
Across the show, sustainability ruled in new materials technology, from polyolefins and engineering resins to biobased materials.
This Knowledge Center provides an overview of the considerations needed to understand the purchase, operation, and maintenance of a process cooling system.
When, how, what and why to automate — leading robotics suppliers and forward-thinking moldmakers will share their insights on automating manufacturing at collocated event.
GETTING A QUOTE WITH LK-MOULD IS FREE AND SIMPLE.
FIND MORE OF OUR SERVICES:
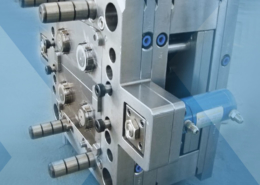
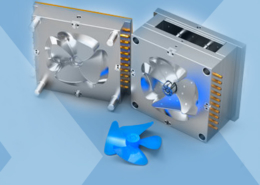
Plastic Molding

Rapid Prototyping
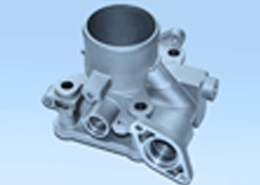
Pressure Die Casting
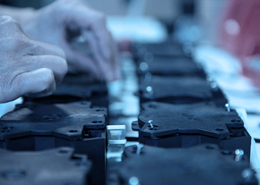
Parts Assembly
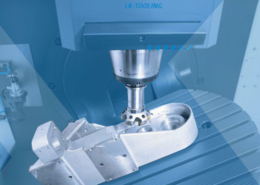