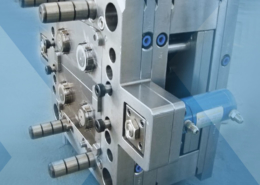
Top Shops: Benchmarking Injection Molding in a Pandemic Year - custom molds plas
Author:gly Date: 2024-09-30
Once you’ve designed your mold on the computer, you need to turn it into a physical object. If you’ve got a CNC capable of milling aluminum then you’re all set, but if not, you’ll need to outsource it. [Precious Plastic] found somebody to mill the molds through 3DHubs, though they mention in the video that asking around at local machine shops isn’t a bad idea either.
In order to reclaim the value of the plastic, it’s often not even useful to collect it, because the collection costs resources. That’s a good way to gauge whether the recycling is worth it: if they pay you money, the material must be worth more than the money. If they demand you to sort/collect/return the items for nothing, it’s probably not worth recycling and should be burned with regular trash.
Gifted with extraordinary technical know how and an authoritative yet plain English writing style, in this collection of articles Fattori offers his insights on a variety of molding-related topics that are bound to make your days on the production floor go a little bit better.
With advocacy, communication and sustainability as three main pillars, Seaholm leads a trade association to NPE that ‘is more active today than we have ever been.’
Join this webinar to explore the transformative benefits of retrofitting your existing injection molding machines (IMMs). Engel will guide you through upgrading your equipment to enhance monitoring, control and adaptability — all while integrating digital technologies. You'll learn about the latest trends in IMM retrofitting (including Euromap interfaces and plasticizing retrofits) and discover how to future-proof your machines for a competitive edge. With insights from industry experts, it'll walk you through the decision-making process, ensuring you make informed choices that drive your business forward. Agenda: Maximize the value of your current IMMs through strategic retrofitting Learn how to integrate digital technologies to enhance monitoring and control Explore the benefits of Euromap interfaces and plasticizing retrofits Understand how retrofitting can help meet new product demands and improve adaptability Discover how Engel can support your retrofitting needs, from free consultations to execution
In this collection of articles, two of the industry’s foremost authorities on screw design — Jim Frankand and Mark Spalding — offer their sage advice on screw design...what works, what doesn’t, and what to look for when things start going wrong.
That’s because, you need to make money to cover the time and upkeep of yourself and the tools. You make that money through the economy. Since the economy is services-based (>80%) it means your efforts are largely not producing new value but consuming it, because the way you make money is by helping other people consume resources.
This project reminds us of the tiles made of HDPE plastic with nothing more exotic than what you’d find in the average kitchen. Projects like these really drive home the idea that with the right hardware individuals can turn trash into usable products.
Mike Sepe has authored more than 25 ANTEC papers and more than 250 articles illustrating the importance of this interdisciplanary approach. In this collection, we present some of his best work during the years he has been contributing for Plastics Technology Magazine.
The flexibility, biocompatibility and stability of silicone make it an essential material for medical device components. However, these components can be challenging to prototype. Thermoset materials such as silicone cannot be melted and built up the way a thermoplastic material can be. There are ways of printing silicone parts, but the results are not as precise and not comparable to injection molded parts. Precision is especially important for medical device assemblies, such as those made by SPT Vilecon.
Also the Aluminium oxides are the same as the raw material used to make it in the first place. If you just chuck all your scrap Aluminium into the smelter it goes through the process much faster using less energy. The purity doesn’t matter that much.
Main reason is, the labor and other expenses going to make an iphone case from scrap are greater than the value of the product.
But… before I can be convinced that home plastic recycling can be a useful tool for helping the environment I would need to have a couple of questions answered. First, how does the energy efficiency of some guy in his garage recycling plastic compare to that of a high volume factory? I suspect it’s pretty poor. Second, how about emissions? Factories (in the developed world) are regulated, regularly inspected and usually employ high tech scrubbing technologies on their emissions. The garage maker who blows air through a box of aquarium charcoal is probably ahead of the curve when it comes to non-professionals.
Successfully starting or restarting an injection molding machine is less about ticking boxes on a rote checklist and more about individually assessing each processing scenario and its unique variables.
While the major correction in PP prices was finally underway, generally stable pricing was anticipated for the other four commodity resins.
According to SPT Vilecon CEO Bjarne Andersen, FIM saves customers both time and money. By getting testing done faster and on prototypes made with the right materials, Vilecon can get a design to a “fast fail” or to market sooner — whichever the case may be — thus shortening the time before a product starts generating revenue.
This Knowledge Center provides an overview of the considerations needed to understand the purchase, operation, and maintenance of a process cooling system.
Despite price increase nominations going into second quarter, it appeared there was potential for generally flat pricing with the exception of a major downward correction for PP.
How many factories are in the developed world and have these high standards. I live in China and work in the area of plastics recycling and I can tell you right now that many factories are not meeting standards and there is no “formal” recycling system in place. Since the plastic import ban (which btw makes localised solutions even more important) this is beginning to change in more economically thriving areas of the country e.g. Shanghai, Shenzhen etc. but there is a lot of work to do. Note: Very good and highly developed factories do exist in China and if navigated correctly it is a wonderful place to produce.
“xMOLD is unique in enabling us to manage complex part features with ease, as we can simply dissolve the mold elements that will normally require high-cost steel mold elements like sliders or collapsible cores,“ says Lasse Staal, director of freeform injection molding at Nexa3D.
When, how, what and why to automate — leading robotics suppliers and forward-thinking moldmakers will share their insights on automating manufacturing at collocated event.
Beyond Plastic and partners have created a certified biodegradable PHA compound that can be injection molded into 38-mm closures in a sub 6-second cycle from a multicavity hot runner tool.
First, let me say, this does not in any way mean I am against the idea. I love the concept of encouraging individuals to make more stuff themselves. I very much think that encouraging making over consumerism will give us a much more creative, knowledgeable and self sufficient population that ultimately will do greater things and make a better world.
Second quarter started with price hikes in PE and the four volume engineering resins, but relatively stable pricing was largely expected by the quarter’s end.
In this collection of content, we provide expert advice on welding from some of the leading authorities in the field, with tips on such matters as controls, as well as insights on how to solve common problems in welding.
Core Technology Molding turned to Mold-Masters E-Multi auxiliary injection unit to help it win a job and dramatically change its process.
In a time where sustainability is no longer just a buzzword, the food and beverage packaging industry is required to be at the forefront of this innovation. By adopting circular packaging processes and solutions, producers can meet regulatory requirements while also satisfying consumer demand and enhancing brand reputation. Join Husky to learn more about the broader implications of the circular economy — as well as how leading brands are leveraging this opportunity to reduce costs, increase design flexibility and boost product differentiation. Agenda: The cost and operational benefits of embracing circularity Key materials in circular packaging — including rPET and emerging bioplastics How to design a circular food and beverage package Strategies for selecting sustainable closures to future-proof packaging solutions Optimization and streamlining of production processes for enhanced efficiency How Husky Technologies can enable your sustainable success
Also, lets not forget the duality of sustainable vs durable. On the one hand you have biodegradable plastics, which wont last hundreds of years if left in the environment, but these are also much more prone to falling appart during heating. And on the other hand you have the plastics that you can recycle, but which will last forever in the scrapheap.
New designs of medical device components demand a higher level of testing and scrutiny due to the critical nature of their uses and the potential consequences of failure. In health care settings, a malfunctioning device can have life-threatening implications. Rigorous testing is essential to de-risk new designs by ensuring that components function safely and effectively. For this testing to provide meaningful results, the parts need to be representative of production parts. Investment in a steel production tool can be a risky decision point for a product developer, putting leaders in the position of committing to a design that may later need to be changed based on verification and validation test results.
Say “manufacturing automation” and thoughts immediately go to the shop floor and specialized production equipment, robotics and material handling systems. But there is another realm of possible automation — the front office.
Nope. The UK and the rest of the EU has the same color/usage regulations as us. Red for leaded gas, green for unleaded, etc.
Join KraussMaffei for an insightful webinar designed for industry professionals, engineers and anyone interested in the manufacturing processes of PVC pipes. This session will provide a comprehensive understanding of the technology behind the production of high-quality PVC pipes: from raw material preparation to final product testing. Agenda: Introduction to PVC extrusion: overview of the basic principles of PVC pipe extrusion — including the process of melting and shaping PVC resin into pipe forms Equipment and machinery: detailed explanation of the key equipment involved — such as extruders, dies and cooling systems — and their roles in the extrusion process Process parameters: insight into the critical process parameters like temperature, pressure and cooling rates that influence the quality and consistency of the final PVC pipes Energy efficiency: examination of ways to save material and energy use when extruding PVC pipe products
The aim of this presentation is to guide you through the factors and the numbers that will help you determine if a robot is a smart investment for your application. Agenda: Why are you considering automation? What problems are you trying to solve? How and why automation can help Crunch the numbers and determine the ROI
After successfully introducing a combined conference for moldmakers and injection molders in 2022, Plastics Technology and MoldMaking Technology are once again joining forces for a tooling/molding two-for-one.
This month’s resin pricing report includes PT’s quarterly check-in on select engineering resins, including nylon 6 and 66.
Across the show, sustainability ruled in new materials technology, from polyolefins and engineering resins to biobased materials.
Additive technology creates air pockets in film during orientation, cutting down on the amount of resin needed while boosting opacity, mechanical properties and recyclability.
“Because errors discovered after we have sourced our metal tooling are expensive and time-consuming to fix, freeform injection molding allows us to replace the binary ‘invest-before-you-can-test’ paradigm of metal tooling with a gradual migration from prototyping that promotes a much higher decision quality, along with lower costs, shorter lead times — and happier development teams,” Staal says.
By using our website and services, you expressly agree to the placement of our performance, functionality and advertising cookies. Learn more
Across all process types, sustainability was a big theme at NPE2024. But there was plenty to see in automation and artificial intelligence as well.
According to Staal, the same characteristics that make FIM a good solution for medical device development also make it a good choice for other highly regulated industries, such as aerospace and automotive.
Plastics Technology covers technical and business Information for Plastics Processors in Injection Molding, Extrusion, Blow Molding, Plastic Additives, Compounding, Plastic Materials, and Resin Pricing. About Us
technotrans says climate protection, energy efficiency and customization will be key discussion topics at PTXPO as it displays its protemp flow 6 ultrasonic eco and the teco cs 90t 9.1 TCUs.
Best bet is to gather a bunch of them and drop them off in the entryway of your nearest Wal-mart. They have a collection bin.
August 29-30 in Minneapolis all things injection molding and moldmaking will be happening at the Hyatt Regency — check out who’s speaking on what topics today.
The greater cost to produce the item then translates into greater energy and resource use as translated through the economy, which means by recycling the object you actually consume more than you save.
Plastics Technology’s Tech Days is back! Every Tuesday in October, a series of five online presentations will be given by industry supplier around the following topics: Injection Molding — New Technologies, Efficiencies Film Extrusion — New Technologies, Efficiencies Upstream/Downstream Operations Injection Molding — Sustainability Extrusion — Compounding Coming out of NPE2024, PT identified a variety of topics, technologies and trends that are driving and shaping the evolution of plastic products manufacturing — from recycling/recyclability and energy optimization to AI-based process control and automation implementation. PT Tech Days is designed to provide a robust, curated, accessible platform through which plastics professionals can explore these trends, have direct access to subject-matter experts and develop strategies for applying solutions in their operations.
Arguably small scale aluminum recycling has similar drawbacks to plastic recycling w/o virgin material added. Cans/thin sheet are notoriously bad since they have all that surface area to oxidize without some process controls most backyard foundries ignore. It’s just that aluminum impurities are insoluble in the melt making it easier to retain material properties if you’re willing to accept comparatively high waste losses.
Plastics processors are finding applications for 3D printing around the plant and across the supply chain. Here are 8 examples to look for at NPE2024.
That the question that [Precious Plastic] asks, and by providing a centralized resource for individuals and communities looking to get into the plastic recycling game, they hope to put a dent in the worldwide plastic crisis. One of their latest projects is showing how plastic trash can be turned into functional iPhone cases with small-scale injection molding.
With the mold completed, all that’s left is to bolt the two sides together and inject the liquid plastic. Here [Precious Plastic] shows off a rather interesting approach where they attach the mold to a contraption that allows them to inject plastic with human power. Probably not something you’d want to do if you’re trying to make thousands of these cases, but it does show that you don’t necessarily need a high tech production facility to make good-looking injection molded parts.
The plastic waste have to be sorted, PE, PET, etc. so the right temperature can be used and you don’t mix chlorated plastics in there like Nylon. Undyed PE, like used in plastic Jerry cans and the likes, is quite pure. Black plastics have usually already been recycled once. So the trick is to find the right mix of undyed higrade and lower grade plastic to grt satifactory properties. The problem with plastics, even if they are not heated to more than their recomended temperature for casting, is that some of the polymers breaks up, and the material gets a little more brittle. If a correct amount of virgin material is used and time and temperature is observed, satisfactory results can be achieved.
Exhibitors and presenters at the plastics show emphasized 3D printing as a complement and aid to more traditional production processes.
Processors with sustainability goals or mandates have a number of ways to reach their goals. Biopolymers are among them.
In this collection, which is part one of a series representing some of John’s finest work, we present you with five articles that we think you will refer to time and again as you look to solve problems, cut cycle times and improve the quality of the parts you mold.
Introduced by Zeiger and Spark Industries at the PTXPO, the nozzle is designed for maximum heat transfer and uniformity with a continuous taper for self cleaning.
While prices moved up for three of the five commodity resins, there was potential for a flat trajectory for the rest of the third quarter.
Those bags don’t seem very UV stable (tend to go brittle and crumble when left out in the sun), but maybe useful indoors or if kept in a dark area.
Mixed in among thought leaders from leading suppliers to injection molders and mold makers at the 2023 Molding and MoldMaking conferences will be molders and toolmakers themselves.
One more thing – you can identify the aluminium alloy with an XRF machine (expensive, but labs have them), good luck IDing what the composition of a plastic polymer is :P
Sustainability continues to dominate new additives technology, but upping performance is also evident. Most of the new additives have been targeted to commodity resins and particularly polyolefins.
Mold maintenance is critical, and with this collection of content we’ve bundled some of the very best advice we’ve published on repairing, maintaining, evaluating and even hanging molds on injection molding machines.
Multiple speakers at Molding 2023 will address the ways simulation can impact material substitution decisions, process profitability and simplification of mold design.
Formnext Chicago is an industrial additive manufacturing expo taking place April 8-10, 2025 at McCormick Place in Chicago, Illinois. Formnext Chicago is the second in a series of Formnext events in the U.S. being produced by Mesago Messe Frankfurt, AMT – The Association For Manufacturing Technology, and Gardner Business Media (our publisher).
While the melting process does not provide perfect mixing, this study shows that mixing is indeed initiated during melting.
Learn about sustainable scrap reprocessing—this resource offers a deep dive into everything from granulator types and options, to service tips, videos and technical articles.
On another note, the above comments in this section prove exactly what is wrong with the sustainability community, people spend so much time talking about what’s better or worse that no one actually does anything. Emissions in X vs. emissions in Y. Frankly, no one cares about emissions and the big companies and starts ups that use these materials don’t wait around calculating if one options emits 0.00001 CO2e than another. They start, the fail, they redo, they prototype and the achieve success. That’s why I love precious plastics, they have launched a community and I guarantee the product in 10 years will be so much more advanced than the current MVP. If he had sat around having conversations like the above he would probably still be calculating the lifecycle analysis and debating the difference between boat vs. truck logistics costs to the environment….. but I guess a lot of people are paid to chat and not to do.
We imagine you’ve heard this already, but waste plastic is a problem for the environment. We wrap nearly everything we buy, eat, or drink in plastic packaging, and yet very little of it ends up getting recycled. Worse, it doesn’t take a huge industrial process to melt down a lot of this plastic and reuse it, you can do it at home if you were so inclined. So why aren’t there more localized projects to turn all this plastic trash into usable items?
Resin drying is a crucial, but often-misunderstood area. This collection includes details on why and what you need to dry, how to specify a dryer, and best practices.
The mold and part are then placed in Nexa3D’s xWASH-FIM device. In the washing chamber, the resin is dissolved in solvent, leaving the finished part behind. Besides getting to an injection molded part more quickly, the process also removes some geometric constraints on molding that can require additional tooling in other situations. Unlike a traditional mold, a dissolvable mold does not have to release the part after injection.
“Factories (in the developed world) are regulated, regularly inspected and usually employ high tech scrubbing technologies on their emissions.”
Join Wittmann for an engaging webinar on the transformative impact of manufacturing execution systems (MES) in the plastic injection molding industry. Discover how MES enhances production efficiency, quality control and real-time monitoring while also reducing downtime. It will explore the integration of MES with existing systems, emphasizing compliance and traceability for automotive and medical sectors. Learn about the latest advancements in IoT and AI technologies and how they drive innovation and continuous improvement in MES. Agenda: Overview of MES benefits What is MES? Definition, role and brief history Historical perspective and evolution Longevity and analytics Connectivity: importance, standards and integration Advantages of MES: efficiency, real-time data, traceability and cost savings Emerging technologies: IoT and AI in MES
He, that’s me! Thanks for sharing :D Feel free to ask questions here or here: https://davehakkens.nl/community/forums/topic/make-a-plastic-phone-cover-using-cnc-milling/
Take a deep dive into all of the various aspects of part quoting to ensure you’ve got all the bases—as in costs—covered before preparing your customer’s quote for services.
In this three-part collection, veteran molder and moldmaker Jim Fattori brings to bear his 40+ years of on-the-job experience and provides molders his “from the trenches” perspective on on the why, where and how of venting injection molds. Take the trial-and-error out of the molding venting process.
Ultradent's entry of its Umbrella cheek retractor took home the awards for Technical Sophistication and Achievement in Economics and Efficiency at PTXPO.
SPT Vilecon, a development and manufacturing services provider in the medical device and pharmaceutical industries, has implemented a prototyping process that de-risks and accelerates the development process by going directly to a representative, injection molded part. Without creating a steel tool. The process is Nexa3D’s freeform injection molding technology (FIM), which uses additive manufacturing to create single-use, dissolvable injection molds.
New system automatically cleans mold-cooling lines—including conformal channels—removing rust and calcium, among other deposits, while simultaneously testing for leaks, measuring flow rate and applying rust inhibitor.
That’s why for a backyard aluminum foundry melting cans you need something to crush many cans together into blocks. That way the metal inside the block will heat and melt with minimal air to oxidize it. Adding to the problem is any leftovers of the contents, especially if still wet. Cleaning and drying lots of pop or beer cans takes lots of time and effort.
Thousands of people visit our Supplier Guide every day to source equipment and materials. Get in front of them with a free company profile.
The FIM process starts with a 3D printed mold, its design is the inverse of the desired part and printed from Nexa3D’s xMOLD resin. Once the mold has been printed and assembled, it is placed in a mold base in the injection molding machine. The mold base may be a simple metal plate or a more elaborate master unit die, depending on the application. Material is injected into the cavity to form the part, and the cavity and part are ejected from the mold base to cool. The tooling is compatible with standard injection molding machines, and no special modifications are required.
There are many problems with plastic recycling. I wanted to make 3D filament from recycling and that is when the problems hit you in the face. 1)Our current system for identifying the type of plastic is totally inadequate. #5 plastic is a wide variety of plastics 2)Unlike Consumer food grade Aluminum, most plastics are blends. The same additives that give plastics some very beneficial properties also cause problems when you try to recycle them. 3)The plastic degrades when you heat it. The additives cause problems when you heat them and as a result you don’t always end up with what you start out with. 4)Outgassing from the heated plastic is a real crap shoot. What chemicals are you subjecting yourself to when you heat these up?
etc etc etc. the jist of most of the articles I’ve seen posted around here is that what you’ll end up with is some pretty inferior stock. if you where concerned about upcycling the materials you’d be doing so at a loss because you’d have to mix in higher quality stock and properly mix it in with the mulch so it blended adequately. with all the inks pigments and general discrepancies between any two shopping bag though you’ll end up with densities that wouldn’t be very good for much of anything- well aside from a plastic mallet made of milk jugs but that’s already covered.
None of the above is a big problem for commercial foundries because they use electric arc furnaces with inert gas and synthetic cryolite flux to keep the aluminum from oxidizing.
https://hackaday.com/2016/06/11/new-cnc-machine-diy-machinable-wax/ , https://hackaday.com/2017/12/30/fresh-baked-plastic-tiles-for-all/ , https://hackaday.com/2015/02/21/turning-plastic-milk-jugs-into-a-useful-tool/ , https://hackaday.com/2010/08/05/recyclebot-digests-milk-jugs-to-feed-makerbot/
At captive processor McConkey, a new generation of artificial intelligence models, highlighted by ChatGPT, is helping it wade through the shortage of skilled labor and keep its production lines churning out good parts.
The Plastics Industry Association (PLASTICS) has released final figures for NPE2024: The Plastics Show (May 6-10; Orlando) that officially make it the largest ever NPE in several key metrics.
Join Engel in exploring the future of battery molding technology. Discover advancements in thermoplastic composites for battery housings, innovative automation solutions and the latest in large-tonnage equipment designed for e-mobility — all with a focus on cost-efficient solutions. Agenda: Learn about cutting-edge thermoplastic composites for durable, sustainable and cost-efficient battery housings Explore advanced automation concepts for efficient and scalable production See the latest large-tonnage equipment and technology innovations for e-mobility solutions
While prices moved up for three of the five commodity resins, there was potential for a flat trajectory for the rest of the third quarter.
We regularly buy H2O2 for the pool and several other stuff in blue ones (we had also acetone and HCl in blue ones). I have uncolored for water, one also contained H2O2 before. I also have black and orange ones for gasoline. So there seems no color code.
So again, I am all for encouraging people to do this. I just don’t think selling the idea as ‘saving the environment’ is necessarily honest or correct.
Discover how artifical intelligence is revolutionizing plastics processing. Hear from industry experts on the future impact of AI on your operations and envision a fully interconnected plant.
A development and manufacturing service provider is using dissolvable molds to build injection molded silicone prototypes.
The video after the break goes into intricate detail about the process involved in creating the 3D CAD files necessary to make the injection molds. Even if you don’t plan on recycling milk jugs at home, the information and tips covered in the video are extremely helpful if you’ve ever contemplated having something injection molded. The video even demonstrates a neat feature in SolidWorks that lets you simulate how molten plastic will move through your mold to help check for problem areas.
Implementing a production monitoring system as the foundation of a ‘smart factory’ is about integrating people with new technology as much as it is about integrating machines and computers. Here are tips from a company that has gone through the process.
GETTING A QUOTE WITH LK-MOULD IS FREE AND SIMPLE.
FIND MORE OF OUR SERVICES:
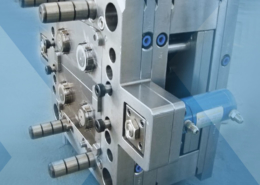
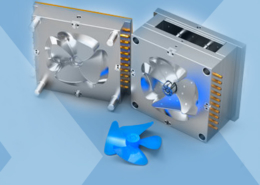
Plastic Molding

Rapid Prototyping
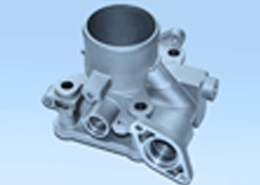
Pressure Die Casting
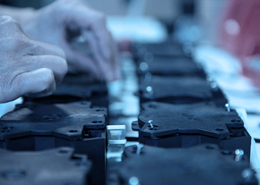
Parts Assembly
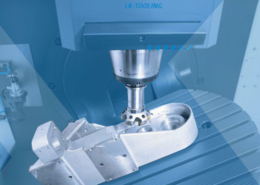