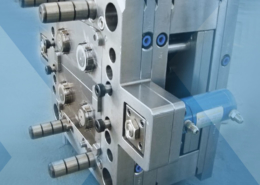
Top Shops: Benchmarking Injection Molding in a Pandemic Year - biggest injection
Author:gly Date: 2024-09-30
“We went in search of a company to commercialize that particular design,” said Luxme President Navam Jagan. “The experience has been excellent. They are a working partner. They worked with us, not only producing these parts for commercial use, but developing new product lines using UHMW-PE. We have gone into other areas using the application because there is such great demand.”
Global Polymer said that’s just what John Deere was looking for when it was re-designing skid plates for its combines. The skid plates, or skid shoes, help ease friction between the ground and the low-hanging parts of the combine’s header platform as it cuts through the field. The skid plates, originally an aftermarket part, were becoming standard equipment. A typical combine has as many as 50 of them installed.
The technology came in handy for customer Luxme International, which was in a rush to compete with copycats eager to cash in on Luxme’s innovative use of UHMW-PE parts in conveyor systems for food-handling applications. Using UHMW-PE parts to move the food eliminated exposed hardware—a requirement for food handling.
“Global Polymer could make our parts faster and better, using the same material,” said McCunn. “The molding process also allows us to add features.”
Until she retired in September 2021, Clare Goldsberry reported on the plastics industry for more than 30 years. In addition to the 10,000+ articles she has written, by her own estimation, she is the author of several books, including The Business of Injection Molding: How to succeed as a custom molder and Purchasing Injection Molds: A buyers guide. Goldsberry is a member of the Plastics Pioneers Association. She reflected on her long career in "Time to Say Good-Bye."
The material has a low coefficient of friction, which reduces the energy needed to operate machinery. Agricultural machinery manufacturers are finding that using UHMW-PE as opposed to steel in scraper applications improves fuel economy, reduces noise levels and increases wear resistance.
The shoes continue to hold up and evolve, said Global Polymer. John Deere has improved the design at least three times since the prototype. “We have increased the usage and improved the function,” said McCunn. “We’ve continued to improve the original design. Because the material does what we want it to do, we ask it to do more.”
"For low-volume production (approximately 10-100 parts), 3D-printed molds save time and money. They also enable a more agile manufacturing approach, allowing engineers and designers to easily modify molds and continue to iterate on their designs with low lead times and cost."
Global Polymer uses a unique compression molding process that it developed to embed steel and other metals within ultra-high-molecular-weight polyethylene.
John Deere also needed a company that could make them cost effectively, and approached Global Polymer to find a solution. Using its UHMW injection molding process, Global Polymer could produce the plates faster than the competition. Where others machined the parts out of single sheets of UHMW-PE, Global Polymer could mold them.
Gobal Polymer’s customer John Deere is also a convert to the benefits of UHMW-PE, which it uses in the production of heavy-duty agricultural equipment parts. “It’s a great material for sliding and wear applications,” said Greg McCunn, Materials Engineer, Plastics and Composites, at John Deere.
While it's free to download, there is a catch--you need to enter your e-mail address, and they openly state "We will also opt you into other relevant marketing communication," so you can presumably expect some spam.
Now that desktop 3D printing has become widespread, there's another production method crossing over into the DIY realm: Desktop injection molding. It's now possible "to create molds in-house to produce small, functional parts in production plastics," writes Formlabs.
It’s also proving to be cost effective, said Global Polymer. The company’s process results in what the industry calls net-shape molding, meaning that the parts come out nearly perfectly shaped, requiring little or no trimming. That saves on production time.
The metal is key in allowing the plastic to maintain its shape without deformation, and offers a very high level of corrosion resistance and weight reduction compared with a full metal part, said Barta.
For the mold material they used both clear and high-temperature resin. Obviously you need something that can withstand a higher temperature than the plastic that's going to be squirted into it.
The lightweight, weather-resistant plastic is a good fit for the rail industry, said Keith Parta, New Products Manager at Salco Products, which manufactures train parts that, until recently, had been made only of metal. “We’re trying to introduce materials into the rail industry that offer a higher level of performance than metal, carbon or stainless steel,” said Parta.
Producing plastic parts that are stronger than steel is the technical expertise of Global Polymer (Madison, SD), a compression molder that has earned a reputation for delivering innovative solutions for difficult manufacturing problems. Global Polymer uses a unique compression molding process that it developed to embed steel and other metals inside ultra-high-molecular-weight polyethylene (UHMW-PE).
It's worth noting that the LDPE didn't stick to the molds, i.e. they didn't require any release agents. They did, however, get a little flash. And they report that the cycle time was three minutes per shot.
With a stereolithography (SLA) 3D printer, you can produce molds that are smooth and strong enough--at least with a little help--to use for injection-molding small runs (10 to 100 parts, Formlabs reckons). What they've done in their testing is placed the molds--which have cavities, gates and sprues, they're the real deal--into aluminum frames, which prevent the mold from warping. You can work with standardized aluminum frames from injection molder manufacturers, or spend the bread to have something custom fabricated at a machine shop.
Salco went to Global Polymer when it wanted to create a new type of blind flange—essentially, a cap for the end of a pipe—for use on tank cars. The part would be required to withstand the elements, high pressure, corrosive chemicals and rough handling. Global Polymer built the cap with compression-molded UHMW-PE embedded with steel.
Founded in 1995, the company operates from a 75,000-square-foot facility with the capacity, tooling and expertise to fulfill national and international orders. More and more manufacturers are using the steel-strengthened parts that are nearly indestructible, according to the company, including John Deere, SAF-Holland, AGCO, Luxme and Salco Products.
Next they used a desktop (okay, benchtop) Galomb Model B-100 Injection Molder, which is relatively affordable at about four grand. They squirted low-density polyethylene into the mold--LDPE was specifically chosen for its low-melt temperature--and were successfully able to produce these parts:
RainIs this the White Paper you referred to?https://archive-media.formlabs.com/upload/injection-molding-from-3d-printed-molds.pdf
GETTING A QUOTE WITH LK-MOULD IS FREE AND SIMPLE.
FIND MORE OF OUR SERVICES:
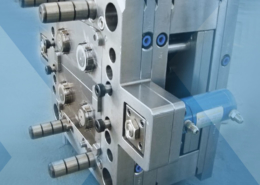
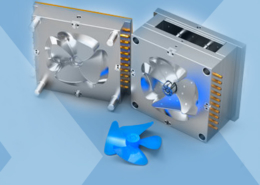
Plastic Molding

Rapid Prototyping
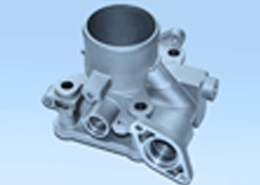
Pressure Die Casting
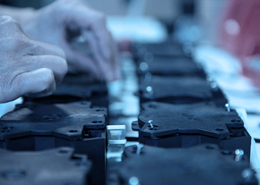
Parts Assembly
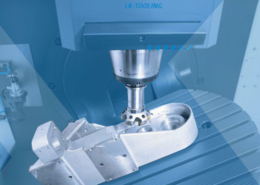