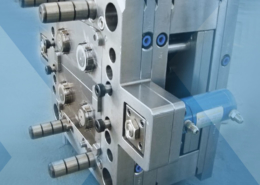
Exploring the Power of Rapid Injection: Revolutionizing Manufacturing
Author:gly Date: 2024-06-08
In the realm of manufacturing, innovation often dictates success. Among the various advancements, rapid injection has emerged as a transformative force, reshaping production processes and pushing the boundaries of efficiency. This article delves into the multifaceted aspects of rapid injection molding, shedding light on its significance, applications, challenges, and future prospects.
Understanding Rapid Injection
Rapid injection molding, also known as rapid tooling or rapid prototyping, is a manufacturing technique that accelerates the production of plastic parts by utilizing molds created through additive manufacturing technologies. Unlike traditional injection molding, which involves lengthy lead times and significant upfront costs for tooling, rapid injection offers swift turnaround times and cost-effective solutions, making it ideal for prototyping, low-volume production, and iterative design processes.
The Process
The process of rapid injection encompasses several key stages, including design, mold creation, injection molding, and post-processing. Initially, a digital model of the desired part is created using computer-aided design (CAD) software. This model is then translated into a physical mold through additive manufacturing techniques such as 3D printing or CNC machining. Once the mold is ready, it is inserted into an injection molding machine where molten plastic is injected under high pressure to replicate the part. Finally, the produced parts undergo finishing processes such as trimming, polishing, or painting to meet the desired specifications.
Advantages
Rapid injection offers numerous advantages over traditional manufacturing methods. Firstly, it significantly reduces lead times, allowing manufacturers to bring products to market faster and respond swiftly to changing customer demands. Secondly, it enables cost-effective production of small batches or customized parts, eliminating the need for expensive tooling and minimizing waste. Additionally, rapid injection facilitates rapid iteration and prototyping, empowering designers to refine their concepts quickly and efficiently.
Applications
The versatility of rapid injection molding renders it applicable across various industries, including automotive, aerospace, medical, and consumer goods. In the automotive sector, rapid injection is utilized for prototyping components such as dashboards, bumpers, and interior trims, enabling manufacturers to test designs and functionalities before mass production. Similarly, in the medical field, rapid injection is employed to fabricate custom medical devices and implants with precise geometries, ensuring optimal fit and performance for patients.
Challenges and Limitations
Despite its numerous benefits, rapid injection molding is not without challenges. One of the primary limitations is material selection. While traditional injection molding supports a wide range of materials, including engineering-grade thermoplastics, rapid injection is often restricted to certain plastics suitable for additive manufacturing processes. This limitation can impact the mechanical properties, surface finish, and durability of the final parts. Furthermore, the scalability of rapid injection for high-volume production remains a concern, as the additive manufacturing methods used for mold creation may not be cost-effective or efficient for large quantities.
Material Properties
The choice of materials for rapid injection molding plays a crucial role in determining the performance and suitability of the final parts. While thermoplastics such as ABS, polypropylene, and polycarbonate are commonly used due to their compatibility with additive manufacturing processes, their mechanical properties and heat resistance may not meet the requirements of certain applications. Thus, engineers and designers must carefully evaluate material options and their respective trade-offs in terms of strength, flexibility, and chemical resistance.
Surface Finish
Another challenge associated with rapid injection molding is achieving desired surface finishes. Unlike traditional injection molding, which produces smooth and uniform surfaces, additive manufacturing techniques may result in layer lines, surface irregularities, or porosity, affecting the aesthetics and functionality of the parts. To mitigate this issue, post-processing techniques such as sanding, polishing, or chemical smoothing can be employed, albeit at additional time and cost.
Scalability
While rapid injection molding excels in prototyping and low-volume production, its scalability for mass production remains a subject of debate. Additive manufacturing processes, although rapid and cost-effective for small batches, may not offer the same economies of scale as traditional injection molding for large quantities. Moreover, the durability and longevity of molds created through additive manufacturing technologies may pose challenges for prolonged use in high-volume manufacturing environments.
Future Perspectives and Opportunities
Despite the existing challenges, the future of rapid injection molding appears promising, driven by ongoing advancements in additive manufacturing technologies, materials science, and process optimization. As additive manufacturing techniques evolve and become more sophisticated, the range of materials suitable for rapid injection is expected to expand, addressing current limitations and enhancing the performance of fabricated parts. Furthermore, innovations in mold design and manufacturing processes may improve the scalability and efficiency of rapid injection, enabling its widespread adoption across industries.
Advanced Materials
The development of new materials tailored for rapid injection molding holds immense potential for enhancing the performance and versatility of manufactured parts. Researchers are exploring novel polymers, composites, and bio-based materials with improved mechanical properties, thermal stability, and biocompatibility, opening doors to new applications in areas such as healthcare, electronics, and sustainable manufacturing.
Digital Twinning
The integration of digital twin technologies into rapid injection molding processes offers opportunities for real-time monitoring, optimization, and predictive maintenance. By creating virtual replicas of physical molds and production systems, manufacturers can simulate and analyze various operating conditions, identify potential defects or inefficiencies, and optimize process parameters for enhanced productivity and quality control.
Sustainable Manufacturing
As sustainability becomes increasingly important in the manufacturing industry, rapid injection molding presents opportunities for reducing waste, energy consumption, and environmental impact. By enabling on-demand production, localized manufacturing, and lightweighting of components, rapid injection contributes to a more sustainable and eco-friendly approach to product development and supply chain management.
Conclusion
In conclusion, rapid injection molding stands at the forefront of manufacturing innovation, offering a swift, cost-effective, and versatile solution for producing plastic parts. While challenges such as material limitations, surface finish, and scalability persist, ongoing research and technological advancements promise to overcome these barriers and unlock new opportunities for rapid injection across industries. By embracing the potential of rapid injection molding and fostering collaboration between academia, industry, and policymakers, we can pave the way for a more efficient, sustainable, and agile manufacturing ecosystem.
GETTING A QUOTE WITH LK-MOULD IS FREE AND SIMPLE.
FIND MORE OF OUR SERVICES:
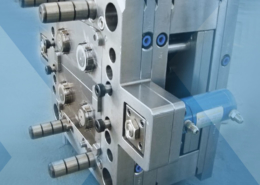
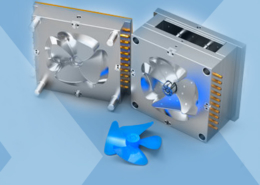
Plastic Molding

Rapid Prototyping
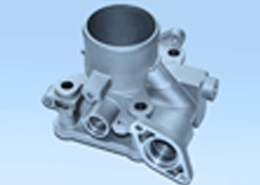
Pressure Die Casting
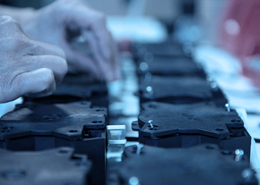
Parts Assembly
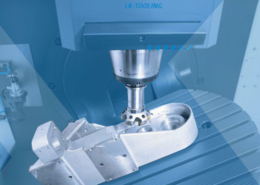