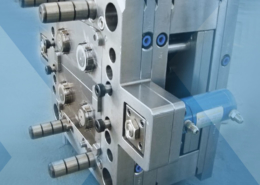
Top five key benefits of injection moulding in the medical industry - medical mi
Author:gly Date: 2024-09-30
For reliable performance, a slimline design and an unbeatable price, there is only one choice: the new ALLROUNDER 720 E GOLDEN ELECTRIC!
At NPE 2024, a high-temperature freeformer 750-3X will demonstrate how complex functional components can be printed reliably and reproducibly from certified original plastic pellets. For the processing of high-temperature material, the temperature of the build chamber can be raised to up to 200 degrees Celsius; plasticising takes place at a maximum of 450 degrees Celsius. The high-end machine has three discharge units and, from the outside, is indistinguishable from the freeformer 300-3X. However, at around 750 square centimetres, the part carrier is around 2.5 times larger. This allows larger functional components to be produced and small batches to be additively manufactured on an industrial scale. A compact melt pressure generator, which produces tiny droplets at a frequency of up to 400 hertz, is used for precise dosing and injection. The result is 3D-printed components that are comparable in quality to injection-moulded parts.
For reliable performance, a slimline design, and an unbeatable price, there is only one choice: the new ALLROUNDER 720 E GOLDEN ELECTRIC!
Lindsey has been an Associate Editor for Machine Design since 2012. She holds a Bachelor of Science in mechanical engineering from Cleveland State University. Prior to joining Penton, she worked in product design, packaging, development and strategy, and manufacturing. She covers the materials market and other areas of interest for design engineers such as 3D printing and methods to operate efficiently.
No matter the material — the printed mold, core, or tooling must withstand higher heat than the injected, dipped, poured, sprayed, or hand-layed material. If the print will be exposed to high temperatures, one recommendation is PPSF/PPSU. If the print needs to be certified for flame, smoke, and toxicity, then Ultem would be the material of choice. If the process will apply pressure on the print, polycarbonate acrylonitrile-butadiene-styrene (PC-ABS) can be used because it has the highest impact resistance. And, ABS-M30i or PC-ISO is suitable for processes that need to use material that is ISO-10993 certified. All of these materials work with fused-deposition-modeling (FDM) printing machines.
ARBURG's extensive expertise in plastics processing also includes a broad portfolio of products for additive manufacturing from sister company ARBURGadditive. At NPE 2024, a high-temperature version of the freeformer 750-3X will showcase the 3D printing of high-quality functional components made from Ultem 9085 – a material that is frequently used in the aerospace industry. There will also be a large number of sample components on display, for example for medical technology, electronics and in multi-material combinations.
The arburgXworld customer portal gives you access to a wide range of digital apps and features that make your daily work easier.
After converting the model into an STL file, upload the file to the software that works with the printer. Choose the resolution, material, and machine that will print the mold. Different systems allow more or fewer adjustments to the build specifications, but the program does most of the work at that point. Set the printer up with the material and (in some machines) the tip to be used. Check for any calibration and cleaning needed, and then start printing. Remove the mold and clean off support material — polish the mold as needed. Plastic molds fit the same as machined molds, so they can be directly inserted into most process machines. But depending on the tool and part, you might need to create a metal box around the plastic to hold it together.fri
The GESTICA control system is optimised for additive manufacturing in terms of process stability, component quality and build time. Based on the slicing data, the system calculates exactly how much material is required to build each individual layer. Variable dosing behaviour helps to reduce the residence time. The result is high-quality components with significantly reduced costs and material usage. A reproducible and reliable additive manufacturing process is also an essential requirement for the use of additively manufactured functional components in safety-relevant areas. For patient-specific implants and ventilation ducts in aeroplanes, for example, it is imperative that the production parameters for each individual component can be fully documented and traced. To do this, ARBURG offers its customisable "ProcessLog" customer portal app, which displays and documents a wide range of process and build job data in a clear graphical format. This significantly reduces rejects and error rates.
“There’s no doubt — printing individual and identical prototypes and end-use parts isn’t the right choice for large-quantity jobs and jobs that needed to be done yesterday,” says Gannon.
Printed molds, tooling, and cores may require different materials. And, material choice will continue to vary by the process and application. For instance, an injection mold will need high-heat and chemical-resistant material. Ultem of polyphenolsulfone (PPSF/PPSU) satisfies those specifications.
The freeformer can be used to realise sophisticated designs and complex geometries. Many sample components will be on show at NPE 2024, including products for the aerospace industry. The industrial machine, which is suitable for clean rooms, can also be used in medical technology, for example to produce resorbable implants, breast prostheses and medical devices and aids. Customised multi-material applications such as shoe insoles made of flexible TPE and a hard zone made of PP are also on display. The APF process is also ideal for sophisticated AM parts made from semi-crystalline PP.
Cores used to make molds can also be printed. For instance, a printed part can act as the core to make silicone molds. Cores are traditionally machined from plastic, wood, or metal depending on the tolerance needed and the surrounding temperature. Even though printed cores may require sanding to get a smooth finish, costs are lower than a core requiring several machining processes.
Machined tooling contributes to the majority of production costs for many small-run jobs. 3D printing can reduce the cost of plastic cores, molds, and tooling, but there are several considerations to examine before choosing this route. Patrick Gannon, engineering manager at Rapid Prototype + Manufacturing LLC, Avon Lake, Ohio, offers a few tips on how and when to 3D print plastic molds and tooling.
Printed plastic molds can be used in injection, extrusion, and blow-molding processes. Printed tooling can be used in vacuum-forming, thermoforming, and drape-forming processes. In thermoforming applications, for example, printed tooling can make blister packaging for consumer products. Tooling for packaging development may require multiple cavities and, with each cavity, there might be thousands of vent holes. Printing cuts the time and cost spent to drill or CNC those holes.
Tolerance must be taken into account when designing a mold. This means opening up gaps and realizing that you will never get extremely tight tolerances. If extreme tolerances are needed, a printed mold will not be acceptable right off the printer — even after postmachining.
3D printed mold design is similar to metal molds. Mounting holes can be modeled in the same pattern as a metal mold. And, if overmolding or dual material injecting is desired, the design mimics metal molds. However, printed design changes when heat transfer is an issue. Plastic molds transfer heat poorly so to help move heat, add several holes to the mold to help cool injected parts quicker. Another method is to insert copper or other heat-transfer materials into the holes.
Most 3D printers use a soluble structural material. This material can be removed with a solvent or chipped away. Cores printed from soluble material can be used in lost-wax casting applications. Soluble material can also be used as the master for open-molding processes such as spray or hand lay-up. For open-molding processes, print a soluble master slightly smaller than the desired part and layer the master with materials like fiberglass and resins. After the materials are cured, the soluble material can be removed.
“What we do know is that 3D printing plastic molds adds value because most machining operations can be eliminated. It’s not uncommon for a machined tool to cost $45,000 and take six to eight weeks to complete. The same mold, 3D printed, will cost about $2,000 and is made in a matter of hours to one week. Printed plastic molds are great for jobs producing 500 parts or less, and for jobs that use complex tooling. But remember, as with any 3D printing project, the best approach is to expect less-than-perfect results. And, if you have to make multiple versions of the tool, you begin to lose the benefits.”
Benefit from our expertise and lower the costs for your injection moulding production by optimising your energy requirement.
GETTING A QUOTE WITH LK-MOULD IS FREE AND SIMPLE.
FIND MORE OF OUR SERVICES:
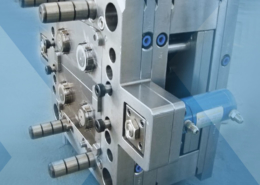
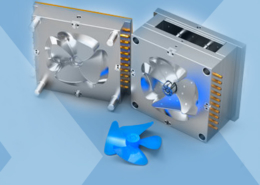
Plastic Molding

Rapid Prototyping
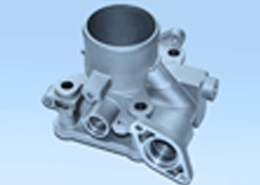
Pressure Die Casting
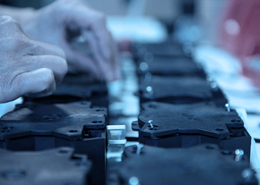
Parts Assembly
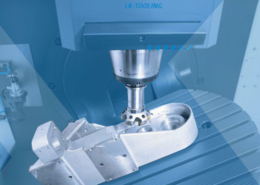