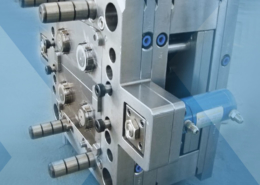
Top 10 Eco-friendly Substitutes for Plastic - top plastic injection molding comp
Author:gly Date: 2024-09-30
ENGEL says experimental methods such as filling studies are often not sufficient and analytical methods lead to better results. however, the problem often arises of establishing a smooth data exchange between software and production.
Technical director Guido Frohnhaus added: "To make attractive investment costs and a quick return on investment (ROI) possible, we rely on standardised equipment without compromising on quality and performance. Our new 'golden' electric machine combines high precision with a streamlined design at a particularly attractive price."
Time-consuming and error-prone manual input of data at the machine is no longer necessary. sim link fulfils this data exchange between simulation software and injection moulding machine without errors.
"The fact that we are holding the world premiere of the new electric machine at NPE2024 reflects the great importance of the American market for Arburg, our leading position in the USA and the expansion of our international business," said Gerhard Böhm, managing director sales and sftersales from the company's German headquarters in Lossburg.
ENGEL claims sim link makes problem-free data exchange between simulation and the injection moulding machine possible. This, in theory saves time consuming co-ordination loops between mould development and production.
The electric machine is not limited to a specific product and has short delivery times, which is particularly advantageous when it comes to urgent replacement purchases and capacity expansions. It is equipped with the Selogica ND control system as standard. If required, additional options and functions such as core pulls and heating and cooling circuits can be easily integrated and programmed. As a result, the new electric injection moulding machine produces a wide range of plastic parts flexibly, efficiently and reliably.
The individual machine dynamics are taken into account and the simulation can be carried out more realistically. The measured production data can be fed back into the simulation very easily. This improves the quality of the simulation.
The Allrounder 720 E Golden Electric features high-quality machine technology to ensure stable and reliable plastic parts production. This includes a toggle-type clamping unit and direct drives from the subsidiary AMK. With an electric mould height adjustment system, mould installation heights of up to 800 millimetres are possible. The drive components are optimised for a clamping force of 2,800 kN.
In an unprecedented move, for the first time a new machine from Arburg is celebrating its world premiere not in Germany, but on the international stage. The new Allrounder 720 E Golden Electric with a clamping force of 2,800 kN extends the product range of the electric series of the same name upwards and is the highlight at NPE 2024 in Orlando, Florida, USA. Streamlined in terms of installation area and price – this summarises its main advantages. The new injection moulding machine continues to stand out for its electric precision and process stability and offers high component quality with low investment costs and short delivery times.
Thanks to effective simulation of injection moulding, cost-intensive looping is reduced when optimising a new component. Where mould makers had to find the values manually for the initial sampling of the moulds, target values are now automatically transferred from the simulation to the injection moulding machine.
Arburg has optimised the design so that the new Allrounder 720 E Golden Electric, with a width of just 1,848 millimetres, has a significantly reduced installation area compared to other machines in its class. This has been achieved, for example, with a new safety door featuring recessed handles. At the same time, the stroke has been widened to 1,400 millimetres to gain better access to the ejector area.
Every injection moulder faces challenges in achieving its production targets. The most important factor in the development of new products is a short time to market. At the same time, the costs for the development and the optimisation of the moulds must be kept low.
Due to its smaller installation area, the new Allrounder fits into existing production grids and lines. Thanks to the new design, more machines can be set up in injection moulding production, resulting in an increased output per square metre.
ENGEL claims by using sim link, the number of repetitions could be significantly reduced. The quality of the simulation has also improved and become more accurate. Difficulties in the coordination could thus be successfully overcome.
Several experts are involved in the creation of a new product. sim link simplifies cooperation between simulation and production staff.
The proven high-quality Arburg plasticising with the "aXw Control ScrewPilot" ensures reproducible injection and excellent moulded part quality. Optimised mould venting with two-stage mould locking also plays a part in this. For convenient maintenance, the new electric Allrounder has the same easily accessible control cabinet concept as the new hybrid machines. Lubrication unit and optional pneumatics are located on the operating side. The parts chute in the machine base has been widened to 850 millimetres, making it easily accessible.
"Extending our portfolio of electric machines helps customers to meet current challenges such as increasing price pressure combined with rising costs for labour, energy and materials, shorter product life cycles and ever faster product changeovers."
At NPE2024, the Allrounder 720 E Golden Electric with a clamping force of 2,800 kN and a size 800 injection unit will be producing razor covers from PP. A 24-cavity mould from Hack will be used. The cycle time is around 8.5 seconds and the moulded part weighs 1.2 grams.
The Allrounder 720 E Golden Electric can be automated with all robotic systems from Arburg – from simple sprue pickers to Multilift linear robotic systems and six-axis robots. The exhibit is equipped with a Multlift V 30. The new 'golden' electric machine is interesting for almost every industry. It is particularly suitable for less complex products and cycle times of around 15 seconds or more. Typical areas of application include dimensionally stable housings for electromobility, thick-walled closures for household goods, precision components for medical technology and the construction, leisure and technical injection moulding sectors.
GETTING A QUOTE WITH LK-MOULD IS FREE AND SIMPLE.
FIND MORE OF OUR SERVICES:
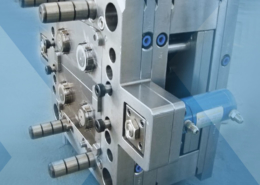
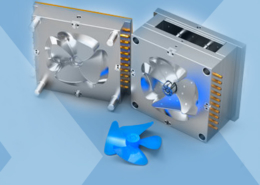
Plastic Molding

Rapid Prototyping
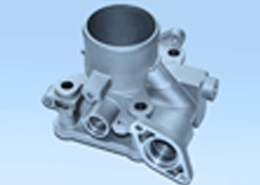
Pressure Die Casting
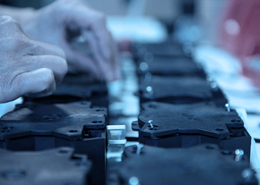
Parts Assembly
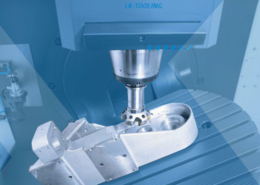