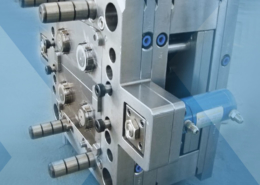
Tooling for Plastics Production - molds for plastic
Author:gly Date: 2024-09-30
Pentagon operates under ISO9001:2015 standards spanning both mould tool manufacture and plastic injection moulding and quality is vital throughout our manufacturing processes. The recent investment in to the Deltron CNC Coordinate Measuring Machine advances our quality process to the next level for mould tool manufacture. The compact machine brings high level measurement accuracy and repeatability directly to the shop floor allowing the technicians to check their own work at every stage and to produce extensive reports when required. Saving measurable amounts of time on the existing manual processes this state-of-the-art technology will predominantly be used for electrodes, cores, cavities, and other tooling components it will deliver greater accuracy for quality checking. The investment will support the reduction of tool manufacturing lead times and reduce the additional resources for reworking or remaking items.
We are also using materials with carbon or steel fillers that make them semi-conductive. This can be useful in environments where static electricity can be an issue, providing Antistatic & ESD protection, preventing electrostatic discharges. Some conductive plastics are also used in Electromagnetic Shielding, reducing EM interference.
The products that can be made from plastic waste are endless. Precious Plastic Monash put this guitar together. (Supplied: Precious Plastic Monash)
From humble beginnings, experimenting in his studio in the South Australian seaside town of Robe, the former corporate boss from Queensland is now being targeted by major companies around the country looking to repurpose their waste.
There are now 10 or so that he knows of in the country, including this Maragaret River start-up turning bottle lids into surfboard fins.
"In Australia we're pretty much picking out number one and number two type plastics and sometimes number five...all the other stuff is basically going to landfill," Mr Scott said. (ABC South East SA: Bec Whetham)
The Deltron features fully sealed recirculating bearings delivering four key benefits: no dirt ingress, no gearbox, no compressed air, and smooth fast operation. This helps deliver exceptional accuracy, simplicity, and reliability. The system will allow us to perform high accuracy measurement supported with bespoke generated reports, run automatic measurement programs, and allows offline programming. Having the ability to import DXF, STEP and IGES files will further aid the process and simplify the measuring of component parts.
"Instead of having to put their waste in their bins they can take it (to a hub) and kind of see a newly realised product there and then."
"That has really motivated us nationally to really think about the fact that we need to invest a bit more energy into our own recycled plastic manufacturing here," Mr Butler said.
"The machines that are coming out (now) have a great capacity so that means we're able to process more of the plastic that's getting dropped off," Mr Butler said.
Materials with glass filler offer benefits of improved strength, structural rigidity, and dimensional stability. Glass-filled nylons also have lower moisture absorption and are therefore less prone to taking in moisture compared to unfilled nylon, which can help ensure greater dimensional stability and reduce the risk of part failure in high-humidity environments. Material selection is largely based on the parameters surrounding the end use of the plastic component and the environment in which it will be used. The versatility of thermoplastic materials is advancing all the time which offers customers and their design engineers a wealth of options.
In line with the modern environment and the hard focus on sustainability within the polymer industry, the current crop of recycled materials that are available are much better than the products of a few years ago. Benefiting from much greater consistency allowing for a repeatable process in the moulding machine. This in turn increases our confidence in offering them as an alternative to traditional virgin polymers. This is particularly attractive to customers who want to be more environmentally sustainable or are simply looking for ways to reduce costs on high-volume parts. Although our approach to injection moulding remains consistent this advancement in recycled material options does enhance the polymer industries offerings.
Due to the chemical construction of some polymers and the additives, the tool designer may need to choose specific grades of tool steel for construction of the inserts to maximise the life of the tooling. Polymers such as PolyVinyl Chloride (PVC) release corrosive gasses during processing which can chloride steels with lower chrome content (non-stainless). While some materials require high hardness tool steels due to the abrasive properties or those of fillers that are added.
The results are then recorded and monitored; this enables the quality team to see if overtime any changes have occurred and maintains consistent accuracy of post moulding operations. The strict quality processes allow us to capture, report and rectify any quality concerns before they become an issue that may impact fulfilment of a customer order.
Mr Butler can imagine a future where Australians drop off their waste at local recycling hubs, from where it is transformed into products.
Depending on the chosen polymer and size of product the clamping force required to successfully mould the component can vary greatly, materials such as Low-Density Polyethylene require low force, while Polyether Sulphones and Polysulfones could require 13 times more clamping force. This will affect what press size is needed to mould the component in production.
The machine Mr Scott uses is inspired by the Precious Plastic project, the brainchild of Dutch industrial design student Dave Hakkens.
"If it goes ahead the idea is that they have all the pods they've made out of plastic collected, send them to me, I recycle and make them into a box, and they send them back out to customers or cafes to put their pods in," Mr Scott said.
Shrinkage affects the physical size of the mould form and is a key consideration when designing a mould tool. Even within the same range of polymers they can vary due to different factors one such factor being additives, or fillers. Fillers such as Talc and Glass fibre are common in materials and much like clamping force the shrinkage of materials can vary greatly so it is important to know not only the polymer that is to be moulded, but the specific material grade as well.
"As far as people developing these machines into something that works for their business…(it's) not something we've seen an awful lot, but we have seen a lot of people express interest in wanting to implement it."
Mr Hakkens started the open-source project in 2012 with the mission of giving people around the world the tools and resources to reduce plastic on a local scale.
"It empowers the community to use those machines and take it into their own community to act as a hub that different people can come to," Mr Butler said.
While Mr Scott built a bigger shed and hired an extra employee (his wife) last year to help keep up with business, there was only so much he could do with the technology available, he said.
Processing properties of the polymer dictate what temperature the tool needs to maintain during moulding. Some polymers require very cold tools, this is achieved by running chilled water through the tool and inserts, while others can require heating over 200°C, which is often achieved with hot oil or sometimes on smaller tools electrical heaters built in.
By working with experienced mould tool manufacturers such as us, sustainability in plastic injection moulding starts with mould tool design. Mould tool design is a complex area and by working with experienced and expert tool designers your tool can be designed with minimised waste in mind at every stage of the manufacturing process.
"If it takes so much time to produce a small product it doesn't really seem overly cost effective to use the machines for that," Mr Butler said.
Each mould for a Precious Plastic product takes a lot of time and effort to design and develop. Here is Brad Scott in the final stages of assembling a chopping board made with 5,500 old bread tags. (ABC South East SA: Bec Whetham)
Considering optimal cavitation, cooling, and ejection systems that best align with the product material specification will mitigate the generation of plastic waste in the moulding process. With the continuing advancements in recycled polymers and their improving compatibility with the plastic injection moulding process there is tangible ethical progress for the plastics sector. Here at Pentagon, we are excited to be taking this journey in the next chapter of plastics processing and its contribution to wider environmental and economic sustainability.
Brad Scott has had to be up front with companies about what he can realistically produce. (ABC South East SA: Bec Whetham)
While melting down plastic waste and recycling it into everyday items may seem like common sense, Mr Scott is one of few in the country actually doing it.
Mount Gambier's Whitty Engineering was approached by Brad Scott late last year. Aaron Hill and Hamish Hopgood have since helped Mr Scott design and build five different product moulds. (ABC South East SA: Bec Whetham)
Pentagon’s breadth of processing knowledge delivers multiple benefits to customers, sound material advice within the design stage coupled with optimal mould tool design that is aligned with specific material behaviours and properties. Our optimised injection moulding processes allow for manufacturing efficiencies that lead to repeatable quality products delivered with efficient lead times.
That he knew of, he said, he was the first to build a machine in Australia, and the first to make a business out of one.
"Currently we can't really say exactly where the plastic is coming from, so we can't make a new product and say that it's food safe," Mr Butler said.
"We're in that space now where the customer will come to us and say, here's a shape that I would like you to make. Can you make that out of bread tags?"
Processes beyond the mould are secondary operations to the injection moulding of the part, usually carried out for component features that are not compatible with the moulding process but are necessary to the finished product or to keep some of the initial cost out of the mould tool. This includes things such as drilling or insert fitting, milling, trimming and light assembly. Within the department quality checks take place every 1-2 hours whereby sample components that are being worked on are taken by the quality inspectors, checked, and measured using equipment such as co-ordinate measuring, callipers, micrometres, pin/thread gauges, and custom-built product specific jigs or gauges.
Project leader David Butler said until recently the machines could not take the volume of plastic required to establish a sustainable business.
"If you start with a very large batch of unsorted, uncleaned plastic, then most of your work would come in at the sorting and cleaning stage," Mr Butler said.
"We can actually start small-scale manufacturing, we can de-centralise a lot of our industries out of cities and make them into small country towns and provide small businesses for country towns, revive the whole place," Mr Scott said.
The original space Brad Scott worked out of when he started the business in 2018 was a third the size of his new workspace (pictured). (ABC South East SA: Bec Whetham)
Mr Scott said it was worth remembering he was one man in a shed operating home-modified machines made of donated kitchen ovens and car jacks.
We acknowledge Aboriginal and Torres Strait Islander peoples as the First Australians and Traditional Custodians of the lands where we live, learn, and work.
"Since then I've taken it to a different place, and that's really what (Precious Plastic) want you to do — they want you to get the general gist of your recycling and go whatever way you want," he said.
He said the next challenge and opportunity was creating food-safe products with the recycled plastics, finding ways to ensure the quality of the plastic.
Properties of thermoplastics are a key factor when designing an injection mould tool and the tool designer must take into consideration multiple factors that can vary greatly from polymer to polymer. The main ones to consider are camping force requirements, shrinkage, corrosive or abrasion properties, and mould temperature.
BP&R sat down with Gabby Day, communications manager at Pentagon Plastics, to discuss Pentagon's post-moulding procedures for adding features, maintaining quality control, and alignment with sustainability goals.
This service may include material from Agence France-Presse (AFP), APTN, Reuters, AAP, CNN and the BBC World Service which is copyright and cannot be reproduced.
Pentagon has been processing high engineering grades of thermoplastic materials for more than fifty years and the use of fillers greatly increases the choice of materials available to our customers and can provide advancements to the final function of the finished product.
Not all the plastic goes into a mould. This "waste" creation sits outside Mr Scott's shed. (ABC South East SA: Bec Whetham)
Another thing stopping businesses from jumping onboard could be the country's dependency on offshore recycling, Mr Butler said, although he added this was changing as Australia limited the amount of plastic waste it processed overseas.
At the same time Mr Scott was getting started in his shed, Monash University was establishing its Precious Plastic program.
GETTING A QUOTE WITH LK-MOULD IS FREE AND SIMPLE.
FIND MORE OF OUR SERVICES:
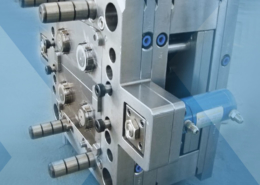
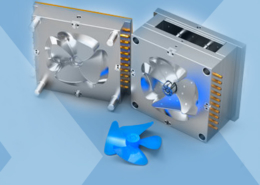
Plastic Molding

Rapid Prototyping
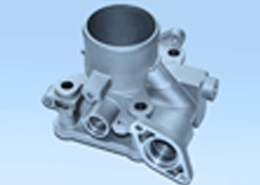
Pressure Die Casting
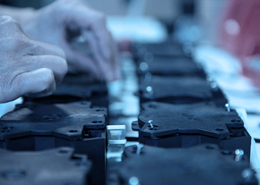
Parts Assembly
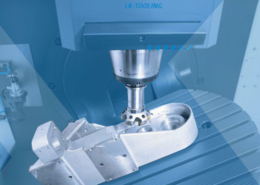