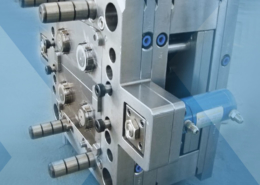
Tiny Homemade Injection Molder - aluminum mold for plastic injection
Author:gly Date: 2024-09-30
While prices moved up for three of the five commodity resins, there was potential for a flat trajectory for the rest of the third quarter.
While the melting process does not provide perfect mixing, this study shows that mixing is indeed initiated during melting.
In a time where sustainability is no longer just a buzzword, the food and beverage packaging industry is required to be at the forefront of this innovation. By adopting circular packaging processes and solutions, producers can meet regulatory requirements while also satisfying consumer demand and enhancing brand reputation. Join Husky to learn more about the broader implications of the circular economy — as well as how leading brands are leveraging this opportunity to reduce costs, increase design flexibility and boost product differentiation. Agenda: The cost and operational benefits of embracing circularity Key materials in circular packaging — including rPET and emerging bioplastics How to design a circular food and beverage package Strategies for selecting sustainable closures to future-proof packaging solutions Optimization and streamlining of production processes for enhanced efficiency How Husky Technologies can enable your sustainable success
Of course, these questions can be readily answered by performing tests on the “old” material and a newly minted lot. Molecular weight determinations can be a good place to begin, and as a follow-up, specimens can be molded from the two lots and the mechanical properties can be compared. But, based on the logic we have gone through above, it would be expected that the material that has been sitting on the warehouse shelf for two years will be perfectly serviceable.
Mixed in among thought leaders from leading suppliers to injection molders and mold makers at the 2023 Molding and MoldMaking conferences will be molders and toolmakers themselves.
This month’s resin pricing report includes PT’s quarterly check-in on select engineering resins, including nylon 6 and 66.
Introduced by Zeiger and Spark Industries at the PTXPO, the nozzle is designed for maximum heat transfer and uniformity with a continuous taper for self cleaning.
The Plastics Industry Association (PLASTICS) has released final figures for NPE2024: The Plastics Show (May 6-10; Orlando) that officially make it the largest ever NPE in several key metrics.
Coverage of single-use plastics can be both misleading and demoralizing. Here are 10 tips for changing the perception of the plastics industry at your company and in your community.
Processors with sustainability goals or mandates have a number of ways to reach their goals. Biopolymers are among them.
New competitors are also entering the OEM market. Large players such as Stratasys and 3D Systems are certifying an end-to-end process for producing medical parts with newly developed materials, using their own printing technology and offering printing services to customers such as hospitals, which formerly purchased from OEMs.
For the nylon 66, the continuous use temperature, as determined by ISO 2578, was given as 100-120oC (212-248oF). For the nylon 12, the published range was 90-120oC (194-248oF). The question then becomes, what time period is referred to by the term “continuous?” Often this refers to a period of 5,000 hours. But, in discussing this property with the material supplier, they offered that continuous in this case referred to 20,000 hours.
Plastics Technology’s Tech Days is back! Every Tuesday in October, a series of five online presentations will be given by industry supplier around the following topics: Injection Molding — New Technologies, Efficiencies Film Extrusion — New Technologies, Efficiencies Upstream/Downstream Operations Injection Molding — Sustainability Extrusion — Compounding Coming out of NPE2024, PT identified a variety of topics, technologies and trends that are driving and shaping the evolution of plastic products manufacturing — from recycling/recyclability and energy optimization to AI-based process control and automation implementation. PT Tech Days is designed to provide a robust, curated, accessible platform through which plastics professionals can explore these trends, have direct access to subject-matter experts and develop strategies for applying solutions in their operations.
While prices moved up for three of the five commodity resins, there was potential for a flat trajectory for the rest of the third quarter.
Across the show, sustainability ruled in new materials technology, from polyolefins and engineering resins to biobased materials.
Join this webinar to explore the transformative benefits of retrofitting your existing injection molding machines (IMMs). Engel will guide you through upgrading your equipment to enhance monitoring, control and adaptability — all while integrating digital technologies. You'll learn about the latest trends in IMM retrofitting (including Euromap interfaces and plasticizing retrofits) and discover how to future-proof your machines for a competitive edge. With insights from industry experts, it'll walk you through the decision-making process, ensuring you make informed choices that drive your business forward. Agenda: Maximize the value of your current IMMs through strategic retrofitting Learn how to integrate digital technologies to enhance monitoring and control Explore the benefits of Euromap interfaces and plasticizing retrofits Understand how retrofitting can help meet new product demands and improve adaptability Discover how Engel can support your retrofitting needs, from free consultations to execution
To give everyone the benefit of the doubt, we can select the low end of the published range — 100oC for the nylon 66 and 90oC for the nylon 12. Additional caution can be employed by assuming the warehouse temperature (in Nebraska) averaged 30oC (86oF) year-round. This assumption also makes the math simpler. Now, consider that for the nylon 12, a difference of 60oC (140oF) between 90oC and 30oC would slow down the rate of oxidation by a factor of 26 (64).
The AM landscape is diverse. In the plastics printing market, larger, integrated players cover the entire value chain from supplying materials to manufacturing printers to providing printing services. Several have added services by making targeted acquisitions. The larger players are also very active in creating new use cases in particular industries, driving sector-wide adoption and sale of equipment. In the metal printing market, by contrast, relatively small players focus more on certain parts of the value chain, such as in printing equipment or in printing services.
Gifted with extraordinary technical know how and an authoritative yet plain English writing style, in this collection of articles Fattori offers his insights on a variety of molding-related topics that are bound to make your days on the production floor go a little bit better.
Formnext Chicago is an industrial additive manufacturing expo taking place April 8-10, 2025 at McCormick Place in Chicago, Illinois. Formnext Chicago is the second in a series of Formnext events in the U.S. being produced by Mesago Messe Frankfurt, AMT – The Association For Manufacturing Technology, and Gardner Business Media (our publisher).
This 21-article compendium gives practical insights for manufacturing leaders looking to keep a step ahead of today’s disruptions.
Meanwhile, in addition to the traditional material, printing, and service businesses, fast-growing niche players are starting to arise. These companies ground their entire business models on AM, ideally combined with digital sales and service models. Align Technology, with its product Invisalign, provides an alternative to metal dental braces; there are similar examples from Sonova for in-ear hearing aids, Mykita with eyeglasses, and Shapeways with crowd design of consumer products.
Additive technology creates air pockets in film during orientation, cutting down on the amount of resin needed while boosting opacity, mechanical properties and recyclability.
Price relief is expected to continue through the fourth quarter for nine major commodity and engineering resins, driven by widespread supply/demand imbalances.
While the issue of shelf life appears to have no merit in this particular case, there are instances where it can be a concern. This is a combination of the material in question and some questionable practices in storing the materials. We will address these in our next segment.
In this collection of content, we provide expert advice on welding from some of the leading authorities in the field, with tips on such matters as controls, as well as insights on how to solve common problems in welding.
Multiplying this factor by the reference time of 20,000 hours would give an expected lifetime for the material at room temperature of 1,280,000 hours (a little over 146 years). Even if we dial back the acceleration factor to a level lower than anything we have ever observed, 1.5 for example (to account for what are called cage effects), we still end up with a projected room-temperature lifetime of 26 years. Because the lowest projected continuous use temperature for the nylon 66 is 10oC higher, all these projections would increase by 1.5 to two times, to yield a result of approximately 40-50 years.
There is a myth in our industry that nylon exposed to the air becomes “saturated” and will never dry. But saturation comes from immersion in water and results in moisture content levels of 8.5-9% in nylon 6 and 66. Studies have shown that nylon 66 exposed to typical ambient conditions absorbs approximately 2.2-2.5% moisture by weight of polymer and with some patience and time that moisture is removable. Nevertheless, it is true that once out of the original package, nylon can become more challenging to process.
Is a two-year-old hygroscopic resin kept in its original packaging still useful? Let’s try to answer that question and clear up some misconceptions.
Resin drying is a crucial, but often-misunderstood area. This collection includes details on why and what you need to dry, how to specify a dryer, and best practices.
ABOUT THE AUTHOR: Michael Sepe is an independent materials and processing consultant based in Sedona, Arizona, with clients throughout North America, Europe and Asia. He has more than 45 years of experience in the plastics industry and assists clients with material selection, designing for manufacturability, process optimization, troubleshooting and failure analysis. Contact: 928-203-0408 • mike@thematerialanalyst.com
Despite all of the optimism about AM, there are still major challenges to be overcome before the technology enjoys truly widespread adoption (Exhibit 3).
Company functions of today will also change when, for example, operators skilled for one production line will need to operate new AM production lines that produce a large variety of products. Traditional engineers will need to be trained in AM design. Marketing and sales, meanwhile, will need to learn how to market individualized products that can be produced anywhere in the world.
Join Wittmann for an engaging webinar on the transformative impact of manufacturing execution systems (MES) in the plastic injection molding industry. Discover how MES enhances production efficiency, quality control and real-time monitoring while also reducing downtime. It will explore the integration of MES with existing systems, emphasizing compliance and traceability for automotive and medical sectors. Learn about the latest advancements in IoT and AI technologies and how they drive innovation and continuous improvement in MES. Agenda: Overview of MES benefits What is MES? Definition, role and brief history Historical perspective and evolution Longevity and analytics Connectivity: importance, standards and integration Advantages of MES: efficiency, real-time data, traceability and cost savings Emerging technologies: IoT and AI in MES
Mike Sepe has authored more than 25 ANTEC papers and more than 250 articles illustrating the importance of this interdisciplanary approach. In this collection, we present some of his best work during the years he has been contributing for Plastics Technology Magazine.
The aim of this presentation is to guide you through the factors and the numbers that will help you determine if a robot is a smart investment for your application. Agenda: Why are you considering automation? What problems are you trying to solve? How and why automation can help Crunch the numbers and determine the ROI
Join Engel in exploring the future of battery molding technology. Discover advancements in thermoplastic composites for battery housings, innovative automation solutions and the latest in large-tonnage equipment designed for e-mobility — all with a focus on cost-efficient solutions. Agenda: Learn about cutting-edge thermoplastic composites for durable, sustainable and cost-efficient battery housings Explore advanced automation concepts for efficient and scalable production See the latest large-tonnage equipment and technology innovations for e-mobility solutions
Operating within guidelines from material suppliers can produce levels of polymer degradation. Get around it with better control over either the temperature of the melt or the barrel residence time.
In this three-part collection, veteran molder and moldmaker Jim Fattori brings to bear his 40+ years of on-the-job experience and provides molders his “from the trenches” perspective on on the why, where and how of venting injection molds. Take the trial-and-error out of the molding venting process.
In this collection, which is part one of a series representing some of John’s finest work, we present you with five articles that we think you will refer to time and again as you look to solve problems, cut cycle times and improve the quality of the parts you mold.
People tend to overestimate the short-term impact of technologies and significantly underestimate the long-term impact. Yet there is currently a lot of uncertainty about the long-term impact of AM on traditional value chains. Understandably, the issue is being raised by traditional players such as logistics companies that will be directly affected, and by governments that aim to prepare their manufacturing ecosystems and workforces for changes that may be coming soon.
With these changes in production capabilities will come equally dramatic shifts in company functions and their relative importance on the value chain. The ability to make completely customizable products will shift the traditional manufacturing mind-set of âWhat is feasible?â to one of âWhat is possible?â Design capabilities will therefore become an even more important strategic asset.
But moisture absorption and removal is a reversible process. Ostensibly, shelf-life concerns would pertain to nonreversible mechanisms. Among these would be loss of volatile constituents such as plasticizers. The principal concern, however, is oxidation. All polymers are susceptible to oxidation to some degree. This will depend upon the chemistry of the polymer and the level of stabilization provided against the mechanism. We understand that the rate of oxidation increases with rising temperature, and a useful rule of thumb that governs this relationship between time and temperature states that with every increase of 10oC the reaction rate doubles, thus reducing the expected life of the material by 50%.
Mold maintenance is critical, and with this collection of content we’ve bundled some of the very best advice we’ve published on repairing, maintaining, evaluating and even hanging molds on injection molding machines.
Baystar's Borstar technology is helping customers deliver better, more reliable production methods to greenhouse agriculture.
Learn about sustainable scrap reprocessing—this resource offers a deep dive into everything from granulator types and options, to service tips, videos and technical articles.
Despite price increase nominations going into second quarter, it appeared there was potential for generally flat pricing with the exception of a major downward correction for PP.
Several analyst reports expect that the direct market for AM will grow to at least $20 billion by 2020âa figure that represents just a fraction of the entire tooling market today.1 1.Nancy Eigel-Miller, Joe Jablonowski, and Steven Kline Jr., 2014 World machine-tool output and consumption survey, Gardner, February 27, 2014, gardnerweb.com. However, we believe that the overall economic impact created by AM could be much higher, reaching $100 billion to 250 billion by 2025, if adoption across industries continues at todayâs rate. Most of that potential will come from the aerospace and defense, automotive, medical, and consumer-goods industries.
Discover how artifical intelligence is revolutionizing plastics processing. Hear from industry experts on the future impact of AI on your operations and envision a fully interconnected plant.
So here is the question for material suppliers: If their own published data suggests that parts molded from these materials could last for a quarter to half a century at room temperature, what is it that makes the pellets from which we will produce these parts so fragile that their integrity would be called into question after 12 months? There is an obvious problem in logic here. A cynical person might conclude that this discussion about shelf life, at least in this case, is a disingenuous playing of a “get out of jail free” card.
This raises a common conversation in the industry regarding the longevity of raw materials if they are kept in storage for an extended period of time, and there are multiple factors that need to be considered. First, is the material in its original packaging and has that packaging been breached in any way? Has it been been punctured with a forklift, or have stacked gaylords collapsed into one another? This will introduce at least the possibility of contamination. In this case, the potential problems are more significant because these are nylons, which are very hygroscopic materials that can absorb significant amounts of moisture from the atmosphere over time.
This Knowledge Center provides an overview of the considerations needed to understand the purchase, operation, and maintenance of a process cooling system.
Successfully starting or restarting an injection molding machine is less about ticking boxes on a rote checklist and more about individually assessing each processing scenario and its unique variables.
Meanwhile, the number of materials that AM can handle is constantly expanding. A wide range of new plastics has been developed, along with processes and machines for printing with ceramics, glass, paper, wood, cement, graphene, and even living cells. Applications are now available in industries ranging from aerospace to automobiles, from consumer goods (including food) to health care (where artificial human tissue can be produced using AM) (Exhibit 1).
The customer was now expressing concern that the raw materials, which were still in their original packaging and had been stored in an indoor warehouse during this time, had expired and that their properties would have been compromised. An appeal to the material supplier brought only a statement saying they would stand behind the material if it was less than a year old.
Thousands of people visit our Supplier Guide every day to source equipment and materials. Get in front of them with a free company profile.
Core Technology Molding turned to Mold-Masters E-Multi auxiliary injection unit to help it win a job and dramatically change its process.
Is there a way to establish an expected shelf life for a material based on published data? In the case of these two materials sitting in my colleague’s warehouse, the answer was yes. The data sheets for both materials published something referred to as a continuous use temperature. This can be a rather loosely defined metric, but it does provide a point of reference for creating an expectation of longevity.
Universities are partnering with manufacturersâ research centers to create innovation centers for applied R&D, with examples including Advanced Remanufacturing and Technology Centre in Singapore and RWTH Aachen University/Fraunhofer Institute for Production Technology. Finally, a vibrant start-up scene has arisen as most patents on existing AM technologies have run out, leaving space for new (as well as established) players from various industries to enter at all points on the value chain. New design and service companies are being set up and new technologies developed, such as by BigRep and Carbon3D.
Additive manufacturing (AM)âthe process of making a product layer by layer instead of using traditional molding or subtractive methodsâhas become one of the most revolutionary technology applications in manufacturing. Often referred to as 3-D printing, the best-known forms of AM today depend on the material: SLS (selective laser sintering), SLA (stereolithography), and FDM (fused deposition modeling) in plastics, and DMLS (direct metal laser sintering) and LMD (laser metal deposition) in metals. Once employed purely for prototyping, AM is now increasingly used for spare parts, small series production, and tooling. For manufacturing with metals, the ability to use existing materials such as steel, aluminum, or superalloys such as Inconel has significantly eased the process of adopting AM.
Plastics Technology covers technical and business Information for Plastics Processors in Injection Molding, Extrusion, Blow Molding, Plastic Additives, Compounding, Plastic Materials, and Resin Pricing. About Us
Compared with traditional production methods, AM offers enormous benefits, including less hard tooling and assembly. In the long run, AM can completely change the way products are designed and built, as well as distributed, sold, and serviced (Exhibit 2).
While the major correction in PP prices was finally underway, generally stable pricing was anticipated for the other four commodity resins.
Multiple speakers at Molding 2023 will address the ways simulation can impact material substitution decisions, process profitability and simplification of mold design.
Second quarter started with price hikes in PE and the four volume engineering resins, but relatively stable pricing was largely expected by the quarter’s end.
We are also seeing an increasing availability of materials with properties comparable or even superior to those of existing ones. These materials include polymers such as nylon, PEEK, and ULTEM that are becoming more heat resistant and lending themselves to more applications, and metals and alloys within the standard range of available materials: industrial metals such as steel, aluminum, titanium, and Inconel; precious metals such as gold and silver; and new materials including amorphous, noncrystalline metals.
A few weeks ago, a longtime colleague emailed me with a question about the shelf life of two nylon materials. One was a 30% carbon fiber-reinforced nylon 66, while the other was a 20% glass fiber-reinforced nylon 12. My colleague’s company had inherited these materials along with the associated molds and their customer had no need for additional molded parts until two years after the jobs had been transferred.
Across all process types, sustainability was a big theme at NPE2024. But there was plenty to see in automation and artificial intelligence as well.
Exhibitors and presenters at the plastics show emphasized 3D printing as a complement and aid to more traditional production processes.
August 29-30 in Minneapolis all things injection molding and moldmaking will be happening at the Hyatt Regency — check out who’s speaking on what topics today.
Take a deep dive into all of the various aspects of part quoting to ensure you’ve got all the bases—as in costs—covered before preparing your customer’s quote for services.
This is an exponential relationship, so a rise of 20oC will increase the reaction rate by a factor of 4 (22), a 30oC increase quickens the process by a factor of 8 (23) and so on. We know from studies that the base acceleration rate per 10oC increase is not always exactly 2. It has been observed to be as low as 1.8 and as high as 2.5, but using the generic value of 2 enables a reasonable estimate of how a material will survive exposure to elevated temperatures.
How will the traditional way of serving markets change, and what are the implications for traditional plant setups and value chains? As far as production and distribution are concerned, a few things seem clear. Advantages from production in low-cost countries will likely diminish. New, customer-centric plants will emerge, allowing the finishing of products according to local demand and significantly reducing the need for long-distance transport of finished goods. We may also see new production-network modelsâfor example, production of half-finished products in low-cost countries, with finishing done close to customers to adjust for local taste, seasonality, and similar factors.
Manufacturers of AM machines, however, are addressing these limitations with significant results. Specialized AM service companies, along with engineering and consulting firms, are now bridging the design-skills gap. In addition, regional governments are funding AM-focused production clusters for applied R&D. Several analysts predict that next-generation machines will cut current AM production costs dramatically because of factors such as patent expiration and reduced postprocessing needs. Manufacturers will also benefit from increasing economies of scale and sourcing opportunities in low-cost countries.
Sustainability continues to dominate new additives technology, but upping performance is also evident. Most of the new additives have been targeted to commodity resins and particularly polyolefins.
Given the investments necessary for developing the next-generation machines, many of these smaller players are looking for capital. Consolidation in the market has therefore begun. Uncertainty about which manufacturers will survive will change the face of the industry, creating risk for manufacturers investing in equipment even as improving technology holds out the promise of surmounting current barriers to the adoption of AM.
AM machine manufacturers are working on better in-process control, advanced quality diagnostics, and data storage along the entire production process for certification purposes. Large AM manufacturers, including Materialise and Stratasys, suggest that AM can achieve material properties in both plastics and metals comparable to those from traditional production techniques.
Say “manufacturing automation” and thoughts immediately go to the shop floor and specialized production equipment, robotics and material handling systems. But there is another realm of possible automation — the front office.
Ultradent's entry of its Umbrella cheek retractor took home the awards for Technical Sophistication and Achievement in Economics and Efficiency at PTXPO.
Join KraussMaffei for an insightful webinar designed for industry professionals, engineers and anyone interested in the manufacturing processes of PVC pipes. This session will provide a comprehensive understanding of the technology behind the production of high-quality PVC pipes: from raw material preparation to final product testing. Agenda: Introduction to PVC extrusion: overview of the basic principles of PVC pipe extrusion — including the process of melting and shaping PVC resin into pipe forms Equipment and machinery: detailed explanation of the key equipment involved — such as extruders, dies and cooling systems — and their roles in the extrusion process Process parameters: insight into the critical process parameters like temperature, pressure and cooling rates that influence the quality and consistency of the final PVC pipes Energy efficiency: examination of ways to save material and energy use when extruding PVC pipe products
Adoption of AM has been highest in industries where its higher production costs are outweighed by the additional value AM can generate: improved product functionality, higher production efficiency, greater customization, shorter time to market (that is, improved service levels), and reduced obsolescence, particularly in asset-heavy industries. Engineering-intensive businesses such as aerospace, automotive, and medical can accelerate prototyping, allowing them to explore completely new design features or create fully individualized products at no extra cost. High-value/lower-volume businesses see faster, more flexible manufacturing processes, with fewer parts involved, less material wasted, reduced assembly time for complex components, and even materials with completely new properties created. And spare-parts-intensive businesses in fields such as maintenance, repair, and overhaul get freedom from obsolete parts, faster time to market, more local and on-demand production opportunities, and independence from traditional suppliers.
Meanwhile, various stakeholders are accelerating the overall market development for AM. Large OEMs are investing significantly in R&D and building internal centers of competence, while other large corporationsâsuch as HP, from the traditional printing businessâare entering the market. Major governments are setting up R&D funds, including the European Unionâs Horizon 2020 program, or are starting capability-building programs for their workforces, as in Korea.
In this collection of articles, two of the industry’s foremost authorities on screw design — Jim Frankand and Mark Spalding — offer their sage advice on screw design...what works, what doesn’t, and what to look for when things start going wrong.
We see little evidence of a race toward a single technology, sinceâbecause of factors including variations in cost, available materials, and surface finishâthe existing technologies serve different purposes. To explore the potential of AM, manufacturers therefore often need access to more than one technology, which they can get via specialized service providers that offer all the key ones. This picture may change, however, if new entrants dramatically increase performance by improving an existing technology or creating a completely new one.
technotrans says climate protection, energy efficiency and customization will be key discussion topics at PTXPO as it displays its protemp flow 6 ultrasonic eco and the teco cs 90t 9.1 TCUs.
When, how, what and why to automate — leading robotics suppliers and forward-thinking moldmakers will share their insights on automating manufacturing at collocated event.
After successfully introducing a combined conference for moldmakers and injection molders in 2022, Plastics Technology and MoldMaking Technology are once again joining forces for a tooling/molding two-for-one.
GETTING A QUOTE WITH LK-MOULD IS FREE AND SIMPLE.
FIND MORE OF OUR SERVICES:
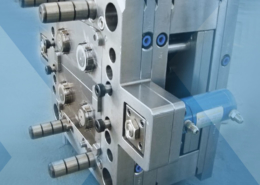
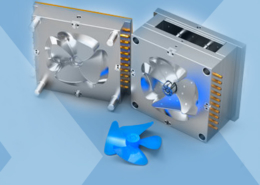
Plastic Molding

Rapid Prototyping
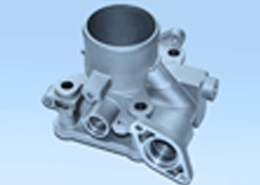
Pressure Die Casting
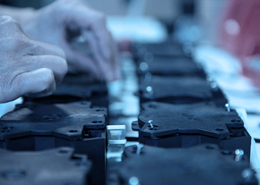
Parts Assembly
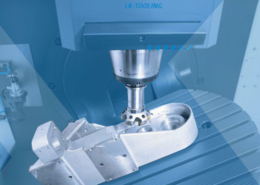