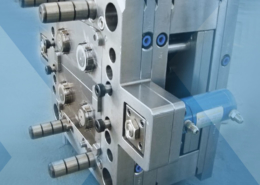
Tide Rock Acquires Plastic Molding Technology - prototype & plastic mold co
Author:gly Date: 2024-09-30
“The cost of replacing the original vinyl packaging made out of petroleum based plastic PP with a biodegradable alternative was more expensive, but we consider the biodegradable plastic market as an economy of scale,” Technology Strategy professional Young Min Lee told ABC News. “As more and more plastics are replaced with biodegradable plastic, the production cost will naturally go down.”
Until she retired in September 2021, Clare Goldsberry reported on the plastics industry for more than 30 years. In addition to the 10,000+ articles she has written, by her own estimation, she is the author of several books, including The Business of Injection Molding: How to succeed as a custom molder and Purchasing Injection Molds: A buyers guide. Goldsberry is a member of the Plastics Pioneers Association. She reflected on her long career in "Time to Say Good-Bye."
This next generation of plastic, PHA -- made from microorganism fermentation -- is currently manufactured by U.S. company Danimer, based in Bainbridge Georgia, and Japanese company, Kaneka.
The inevitable move from petroleum-based plastic to an eco-friendly substitute has been exacerbated by Europe’s sales ban of the 10 most commonly found plastic waste items at the bottom of the ocean such as straws, takeout containers and water bottles made of polystyrene.
After a certain period of fermentation, the materials go through a refinery process where PHA are dehydrated and aggregated before being made into long strands of liquid plastic, which later dries up into solid biodegradable plastic materials.
“Plastics made from crude oil are said to take over 500 years to completely decompose, while biodegradable plastics take decades at most,” SungYeon Hwang, Head of Bio-based Chemistry Research Center at the Korea Research Institute of Chemical Technology, told ABC News. “Biodegradable plastic does not pollute the sea even if it accidentally flows into the shore.”
The chosen strains go through a fermentation process during which the cells are grown in bioreactors and subsequently fed with sugar made from feedstock for better production of PHA.
"Creative is an ideal company for Big 3 Precision to partner with because of its outstanding extrusion blow molding capabilities, something that Big 3 Precision has not been supplying to its customers," said Clinton Hyde, Vice President of Sales & Engineering for Big 3 Precision. "Now, through this partnership our customers can also order extrusion blow molds from us and receive the expert engineering and manufacturing that Creative has been providing for 30 years."
The amount of commercial waste at this point is not enough to design a separate collecting system, experts say. PHA will only become an effective eco-friendly alternative for plastic when its manufacturing reaches an adequately sized economy of scale in the future.
Big 3 Precision (Centralia, IL) and Creative Blow Mold Tooling (Lee's Summit, MO) have announced the formation of a strategic partnership to create Centers of Excellence (CoE) for the design and manufacture of injection blow and injection stretch blow molds (IBM/ISBM), as well as the design and manufacture of extrusion blow molds.
Bioplastics like PHA are, theoretically, compostable if collected and buried separately but, for now, consumers are advised to throw them away together along with general waste.
SUWON, South Korea -- South Korean conglomerate CJ Cheiljedang is jumping into the global market to begin mass production of PHA biodegradable plastic, or polyhydroxyalkanoates.
The goal of the partnership and the CoE is to help existing customers with speed to market through increased product development and support. Big 3 and Creative also intend to use the CoE concept to help balance engineering and manufacturing capacity, increase efficiencies and further reduce lead times for customers. The partnership will allow customers to source tooling on complementary platforms through a known and trusted business partner. For some customers, access to the CoE will allow them to more quickly and efficiently expand their existing capabilities to other platforms.
“These selected strains are optimally grown in a controlled environment where we tightly regulate the shaking speed and temperature,” Researcher Park Yae-seul told ABC news.
“It will make a big step for a better environment if the plastic waste that has no choice but to go to general waste such as straws, agricultural mulching films and small containers, are replaced with biodegradable plastic like the PHA,” Hong Soo-yeol, chief researcher at Seoul-based Resource Recycle Consulting, told ABC News.
CJ Cheiljedang’s PHA has been certified biodegradable in industry use, household compost, soil and water by TUV Austria, an institution for biodegradability testing and certification.
Big 3 Precision (Centralia, IL) and Creative Blow Mold Tooling (Lee's Summit, MO) have announced the formation of a strategic partnership to create Centers of Excellence (CoE) for the design and manufacture of injection blow and injection stretch blow molds (IBM/ISBM), as well as the design and manufacture of extrusion blow molds.
Making solid PHA material begins by engineering and creating microorganisms. At CJ Cheiljedang lab in Suwon, just south of Seoul, researchers grow and nurture microorganisms and select the strongest strain through automated machines.
Both companies have relationships that process on both platforms and this partnership will allow both companies to better and more broadly serve their respective customer base.
While a number of biodegradable materials have been proposed as a solution to the global plastic pollution problem, there is still much controversy over how the biodegradable plastic waste is disposed of.
CJ Cheiljedang, as a starter to its next generation makeover, has recently begun wrapping their tofu bundle with vinyl packaging containing their own PHA as a test use in consumer goods. But reaching economies of scale is still a long way off.
“With PHA, CJ Cheiljedang hopes to play a leading role in changing the paradigm of the global materials market,” CJ Cheiljedang’s communications team told ABC News. “'Going green' is an inevitable trend in all industries.”
Michael Bohning, President of Creative, commented, "Big 3 has an outstanding reputation in the industry, and our customers as well as our team members will benefit greatly from the experience and expertise Big 3 brings to the table. We can offer our customers expanded mold design and manufacturing capabilities as well as reduce lead times through improved capacity management."
With over 30 years of experience building extrusion blow mold (EBM) tooling, Creative Blow Mold Tooling designs and builds EBM tooling from idea to 3D design engineering and development to superior consumer packaging for some of the largest brand owners in North America. Using Computational Fluid Dynamics simulation technology, Creative can improve mold performance and customers' ROI, while bringing innovative packaging solutions to the marketplace.
For more than 40 years, Big 3 Precision Products has focused on the IBM/ISBM marketplace. It has manufacturing and engineering/sales facilities in Millville, NJ; Dearborn, MI; St. Joseph, MO; and Holliston, MA. Capabilities include industrial automation, material handling equipment, metal stamping, general machining, injection blow molds and injection stretch blow mold tooling. The company has CGMP certification for sampling with labs at Centralia, IL, and Millville, NJ. Injection blow mold sampling is available at the Millville and Holliston facilities.
As a primary supplier, each company will be able to tap into the CoE for engineering and manufacturing leadership, project management and technical support. The primary supplier will be responsible for program management and manufacturing. The newly formed alliance will be a partnership of the companies' technical capabilities and expertise.
“Ideally, it is best to collect used PHA-based plastic waste and process them in an industrial compost in order to meet its biodegradable characteristics,” In-Joo Chin, president of the Korean Bioplastics Association, told ABC News.
PHA is considered a viable alternative to petroleum-based plastic because the new technology allows its plastic waste to decompose completely in the ocean and soil in a significantly shorter period of time.
CJ Cheiljedang aims to construct a 5,000 tons worth PHA manufacturing line in Indonesia by the end of this year. The global bioplastic production market is anticipated to reach up to 2.8 million tons by 2025, according to the European Bioplastics’ market analysis in 2020.
GETTING A QUOTE WITH LK-MOULD IS FREE AND SIMPLE.
FIND MORE OF OUR SERVICES:
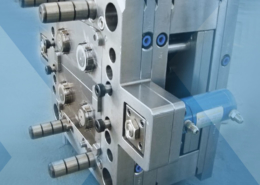
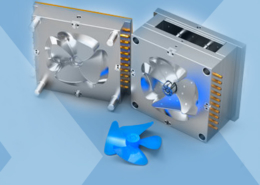
Plastic Molding

Rapid Prototyping
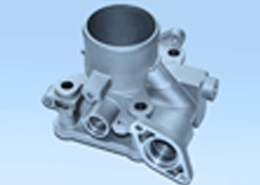
Pressure Die Casting
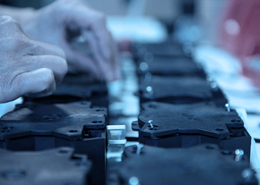
Parts Assembly
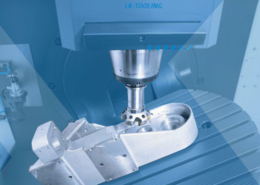