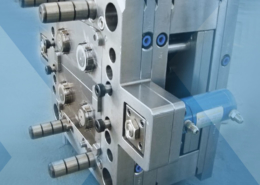
THYSSENKRUPP UHDE: German firm to establish biopolymer production facility
Author:gly Date: 2024-09-30
Three of our global locations include high-tech tool shops, which enable us to quickly develop molds from prototype to production, as well as perform maintenance and repairs. Manufacturing transfer Thinking about moving production out of China? Facing rising costs and import/export issues with medical device production in China, VEM helps clients with an expedited manufacturing transfer of plastic injection molding and assembly projects from China to Thailand with their supply chains intact. VEM has been manufacturing in Thailand for 13 years and medical device manufacturing project transfers are among our most popular services and can be set up and running within just a few weeks. For more information, read our case study under the ‘White Papers’ tab on this page. Medical plastics and device manufacturing in Thailand Manufacturing in Southeast Asia offers a lower price point, more flexibility, and a faster time to market than domestic manufacturing can provide. For more than 13 years, VEM has operated its wholly-owned manufacturing operation in Rayong, Thailand. The largest port in Thailand, Laem Chabang Port, is just a 30-minute drive from our facility and many large medical device and healthcare manufacturers are located nearby. There is an undeniable reason behind the growth of the medical device manufacturing industry in Thailand. The location is strategically attractive due to a skilled and educated workforce, a welcoming and open economy with a stable government, quality infrastructure, lower cost of labour and reduced import taxes, and ease of import/export of raw materials and components. About VEM Medical VEM currently has five manufacturing facilities across Asia, Europe and Central America. Our facility in Thailand is ISO 13485:2016 certified and specialises in medical device production and assembly. Our tool shop in Shenzhen, China, manufactures molds for our medical device clients worldwide.
A highly experienced team, best-in-class equipment and rigorous quality control help us deliver solutions for challenging medical tooling and molding applications. For more than 20 years, VEM has focused on customer satisfaction as our highest priority. Our clients range from small innovative companies to large multinational original equipment manufacturers (OEMs). Our production facility is certified according to ISO 9001 and ISO 13485, with a Class 100,000 (ISO 8) cleanroom. VEM Medical can produce small and precise molded parts for medical devices. Our medical assembly line is inspected by a stringent quality control team. A static 2K mixer for medical applications. VEM Medical can produce injection-molded parts for medical sub-assembly. Each of our manufactured devices must pass a testing procedure specified by the customer. Medical inserts can be molded in our clean room. We produce parts through complex medical tooling. Our team sub-assembles a tube connection for a breathing device. Many different parts can be moulded in our Class 100,000 cleanroom. Medical plastics and device manufacturing VEM is an integrated partner from design assistance and design for manufacturing to finished device production and assembly. Our fully owned tool shops, cleanroom production, assembly and sub-assembly capabilities provide rich opportunities to partner with us, no matter which stage your product is in. Our experienced team uses the newest equipment and automation, including brands such as Arburg, Toshiba, GF, Hexagon and Makino. Being transparent when producing parts is what makes us stand out. Not only will we set up the production in accordance with all your needs but we can also help to improve process quality and reduce cycle times. In-house medical tooling VEM’s in-house medical molds have helped us develop medical parts for molding and assembly for years. Our fully owned mold manufacturer consistently gives us complete control over molds and materials, allowing for optimal quality control. Optimisation, rigorous quality testing, and a professional approach to solving problems have always been our key approaches. Our molds are used worldwide by large medical companies, including Danaher Corporation, Cepheid, Foamtec Medical and Freudenberg Medical. Cleanroom molding and assembly VEM can offer services in design assistance, prototyping, production mold making, injection molding in a white room or cleanroom, component sourcing, assembly, testing and packaging. Both inside and outside our cleanroom, we have room and equipment for various sizes of injection machines. Our cleanroom is built in a modular way, which allows us to be flexible and increase size as quickly as possible according to customers’ needs. Three of our global locations include high-tech tool shops, which enable us to quickly develop molds from prototype to production, as well as perform maintenance and repairs. Manufacturing transfer Thinking about moving production out of China? Facing rising costs and import/export issues with medical device production in China, VEM helps clients with an expedited manufacturing transfer of plastic injection molding and assembly projects from China to Thailand with their supply chains intact. VEM has been manufacturing in Thailand for 13 years and medical device manufacturing project transfers are among our most popular services and can be set up and running within just a few weeks. For more information, read our case study under the ‘White Papers’ tab on this page. Medical plastics and device manufacturing in Thailand Manufacturing in Southeast Asia offers a lower price point, more flexibility, and a faster time to market than domestic manufacturing can provide. For more than 13 years, VEM has operated its wholly-owned manufacturing operation in Rayong, Thailand. The largest port in Thailand, Laem Chabang Port, is just a 30-minute drive from our facility and many large medical device and healthcare manufacturers are located nearby. There is an undeniable reason behind the growth of the medical device manufacturing industry in Thailand. The location is strategically attractive due to a skilled and educated workforce, a welcoming and open economy with a stable government, quality infrastructure, lower cost of labour and reduced import taxes, and ease of import/export of raw materials and components. About VEM Medical VEM currently has five manufacturing facilities across Asia, Europe and Central America. Our facility in Thailand is ISO 13485:2016 certified and specialises in medical device production and assembly. Our tool shop in Shenzhen, China, manufactures molds for our medical device clients worldwide.
Being transparent when producing parts is what makes us stand out. Not only will we set up the production in accordance with all your needs but we can also help to improve process quality and reduce cycle times. In-house medical tooling VEM’s in-house medical molds have helped us develop medical parts for molding and assembly for years. Our fully owned mold manufacturer consistently gives us complete control over molds and materials, allowing for optimal quality control. Optimisation, rigorous quality testing, and a professional approach to solving problems have always been our key approaches. Our molds are used worldwide by large medical companies, including Danaher Corporation, Cepheid, Foamtec Medical and Freudenberg Medical. Cleanroom molding and assembly VEM can offer services in design assistance, prototyping, production mold making, injection molding in a white room or cleanroom, component sourcing, assembly, testing and packaging. Both inside and outside our cleanroom, we have room and equipment for various sizes of injection machines. Our cleanroom is built in a modular way, which allows us to be flexible and increase size as quickly as possible according to customers’ needs. Three of our global locations include high-tech tool shops, which enable us to quickly develop molds from prototype to production, as well as perform maintenance and repairs. Manufacturing transfer Thinking about moving production out of China? Facing rising costs and import/export issues with medical device production in China, VEM helps clients with an expedited manufacturing transfer of plastic injection molding and assembly projects from China to Thailand with their supply chains intact. VEM has been manufacturing in Thailand for 13 years and medical device manufacturing project transfers are among our most popular services and can be set up and running within just a few weeks. For more information, read our case study under the ‘White Papers’ tab on this page. Medical plastics and device manufacturing in Thailand Manufacturing in Southeast Asia offers a lower price point, more flexibility, and a faster time to market than domestic manufacturing can provide. For more than 13 years, VEM has operated its wholly-owned manufacturing operation in Rayong, Thailand. The largest port in Thailand, Laem Chabang Port, is just a 30-minute drive from our facility and many large medical device and healthcare manufacturers are located nearby. There is an undeniable reason behind the growth of the medical device manufacturing industry in Thailand. The location is strategically attractive due to a skilled and educated workforce, a welcoming and open economy with a stable government, quality infrastructure, lower cost of labour and reduced import taxes, and ease of import/export of raw materials and components. About VEM Medical VEM currently has five manufacturing facilities across Asia, Europe and Central America. Our facility in Thailand is ISO 13485:2016 certified and specialises in medical device production and assembly. Our tool shop in Shenzhen, China, manufactures molds for our medical device clients worldwide.
VEM Medical provides plastic injection molding, in-house tooling, prototyping, assembly, testing and more for medical devices, plastics and components.
Evanesce Packaging Solutions offers another highly sustainable product: the first mass-produced biodegradable straws made of modified polylactic acid (PLA) that are on par or cheaper than paper straws, offer significantly improved durability, and home-compost within 90 days. The company’s South Carolina plant will be capable of producing millions of compostable straws daily.
Manufacturing in Southeast Asia offers a lower price point, more flexibility, and a faster time to market than domestic manufacturing can provide. For more than 13 years, VEM has operated its wholly-owned manufacturing operation in Rayong, Thailand. The largest port in Thailand, Laem Chabang Port, is just a 30-minute drive from our facility and many large medical device and healthcare manufacturers are located nearby. There is an undeniable reason behind the growth of the medical device manufacturing industry in Thailand. The location is strategically attractive due to a skilled and educated workforce, a welcoming and open economy with a stable government, quality infrastructure, lower cost of labour and reduced import taxes, and ease of import/export of raw materials and components. About VEM Medical VEM currently has five manufacturing facilities across Asia, Europe and Central America. Our facility in Thailand is ISO 13485:2016 certified and specialises in medical device production and assembly. Our tool shop in Shenzhen, China, manufactures molds for our medical device clients worldwide.
Both inside and outside our cleanroom, we have room and equipment for various sizes of injection machines. Our cleanroom is built in a modular way, which allows us to be flexible and increase size as quickly as possible according to customers’ needs. Three of our global locations include high-tech tool shops, which enable us to quickly develop molds from prototype to production, as well as perform maintenance and repairs. Manufacturing transfer Thinking about moving production out of China? Facing rising costs and import/export issues with medical device production in China, VEM helps clients with an expedited manufacturing transfer of plastic injection molding and assembly projects from China to Thailand with their supply chains intact. VEM has been manufacturing in Thailand for 13 years and medical device manufacturing project transfers are among our most popular services and can be set up and running within just a few weeks. For more information, read our case study under the ‘White Papers’ tab on this page. Medical plastics and device manufacturing in Thailand Manufacturing in Southeast Asia offers a lower price point, more flexibility, and a faster time to market than domestic manufacturing can provide. For more than 13 years, VEM has operated its wholly-owned manufacturing operation in Rayong, Thailand. The largest port in Thailand, Laem Chabang Port, is just a 30-minute drive from our facility and many large medical device and healthcare manufacturers are located nearby. There is an undeniable reason behind the growth of the medical device manufacturing industry in Thailand. The location is strategically attractive due to a skilled and educated workforce, a welcoming and open economy with a stable government, quality infrastructure, lower cost of labour and reduced import taxes, and ease of import/export of raw materials and components. About VEM Medical VEM currently has five manufacturing facilities across Asia, Europe and Central America. Our facility in Thailand is ISO 13485:2016 certified and specialises in medical device production and assembly. Our tool shop in Shenzhen, China, manufactures molds for our medical device clients worldwide.
“The amount of energy required during production is similar to thermoforming processes,” says Horne. “We employ heat recovery systems in our baking process that have evolved. Our environmental footprint is kept to a minimum.”
VEM currently has five manufacturing facilities across Asia, Europe and Central America. Our facility in Thailand is ISO 13485:2016 certified and specialises in medical device production and assembly. Our tool shop in Shenzhen, China, manufactures molds for our medical device clients worldwide.
The product color can be a white like a standard EPS or gray or look like a brownie, depending on what type of fiber is used.
VEM has been manufacturing in Thailand for 13 years and medical device manufacturing project transfers are among our most popular services and can be set up and running within just a few weeks. For more information, read our case study under the ‘White Papers’ tab on this page. Medical plastics and device manufacturing in Thailand Manufacturing in Southeast Asia offers a lower price point, more flexibility, and a faster time to market than domestic manufacturing can provide. For more than 13 years, VEM has operated its wholly-owned manufacturing operation in Rayong, Thailand. The largest port in Thailand, Laem Chabang Port, is just a 30-minute drive from our facility and many large medical device and healthcare manufacturers are located nearby. There is an undeniable reason behind the growth of the medical device manufacturing industry in Thailand. The location is strategically attractive due to a skilled and educated workforce, a welcoming and open economy with a stable government, quality infrastructure, lower cost of labour and reduced import taxes, and ease of import/export of raw materials and components. About VEM Medical VEM currently has five manufacturing facilities across Asia, Europe and Central America. Our facility in Thailand is ISO 13485:2016 certified and specialises in medical device production and assembly. Our tool shop in Shenzhen, China, manufactures molds for our medical device clients worldwide.
“At that time, I felt that we should ban expanded polystyrene (EPS) packaging because of this elegant alternative solution,” he relates. “The technology is so fantastic I left politics to acquire it then surrounded myself with great people to take it to a commercial level. One of the things that always worried me as a regulator was the fact that many of the products that were considered sustainable weren’t. This is.”
Evanesce’s durable food trays and cups made from a starch and fiber dough are "baked like a cookie” and home compostable in 90 days.
Thinking about moving production out of China? Facing rising costs and import/export issues with medical device production in China, VEM helps clients with an expedited manufacturing transfer of plastic injection molding and assembly projects from China to Thailand with their supply chains intact. VEM has been manufacturing in Thailand for 13 years and medical device manufacturing project transfers are among our most popular services and can be set up and running within just a few weeks. For more information, read our case study under the ‘White Papers’ tab on this page. Medical plastics and device manufacturing in Thailand Manufacturing in Southeast Asia offers a lower price point, more flexibility, and a faster time to market than domestic manufacturing can provide. For more than 13 years, VEM has operated its wholly-owned manufacturing operation in Rayong, Thailand. The largest port in Thailand, Laem Chabang Port, is just a 30-minute drive from our facility and many large medical device and healthcare manufacturers are located nearby. There is an undeniable reason behind the growth of the medical device manufacturing industry in Thailand. The location is strategically attractive due to a skilled and educated workforce, a welcoming and open economy with a stable government, quality infrastructure, lower cost of labour and reduced import taxes, and ease of import/export of raw materials and components. About VEM Medical VEM currently has five manufacturing facilities across Asia, Europe and Central America. Our facility in Thailand is ISO 13485:2016 certified and specialises in medical device production and assembly. Our tool shop in Shenzhen, China, manufactures molds for our medical device clients worldwide.
“We've been working with partners on coating systems as well,” Horne says. “For those that require longer oxygen barriers, we've worked with a couple of partners, which is how we started on the biopolymer side. Depending on the requirements, we can either coat, laminate, or simply add the barrier as a raw ingredient.”
VEM Group, a global tooling and molding provider to the medical device and consumer goods industry, has been selected by Manufacturing Outlook magazine a Top 10 Injection Molding Service Companies 2021.
VEM Medical is a full-service contract manufacturing organisation for medical plastics, devices and components. We partner with medical device companies across three continents to provide plastic injection molding, in-house tooling, prototyping, assembly, testing and more. A highly experienced team, best-in-class equipment and rigorous quality control help us deliver solutions for challenging medical tooling and molding applications. For more than 20 years, VEM has focused on customer satisfaction as our highest priority. Our clients range from small innovative companies to large multinational original equipment manufacturers (OEMs). Our production facility is certified according to ISO 9001 and ISO 13485, with a Class 100,000 (ISO 8) cleanroom. VEM Medical can produce small and precise molded parts for medical devices. Our medical assembly line is inspected by a stringent quality control team. A static 2K mixer for medical applications. VEM Medical can produce injection-molded parts for medical sub-assembly. Each of our manufactured devices must pass a testing procedure specified by the customer. Medical inserts can be molded in our clean room. We produce parts through complex medical tooling. Our team sub-assembles a tube connection for a breathing device. Many different parts can be moulded in our Class 100,000 cleanroom. Medical plastics and device manufacturing VEM is an integrated partner from design assistance and design for manufacturing to finished device production and assembly. Our fully owned tool shops, cleanroom production, assembly and sub-assembly capabilities provide rich opportunities to partner with us, no matter which stage your product is in. Our experienced team uses the newest equipment and automation, including brands such as Arburg, Toshiba, GF, Hexagon and Makino. Being transparent when producing parts is what makes us stand out. Not only will we set up the production in accordance with all your needs but we can also help to improve process quality and reduce cycle times. In-house medical tooling VEM’s in-house medical molds have helped us develop medical parts for molding and assembly for years. Our fully owned mold manufacturer consistently gives us complete control over molds and materials, allowing for optimal quality control. Optimisation, rigorous quality testing, and a professional approach to solving problems have always been our key approaches. Our molds are used worldwide by large medical companies, including Danaher Corporation, Cepheid, Foamtec Medical and Freudenberg Medical. Cleanroom molding and assembly VEM can offer services in design assistance, prototyping, production mold making, injection molding in a white room or cleanroom, component sourcing, assembly, testing and packaging. Both inside and outside our cleanroom, we have room and equipment for various sizes of injection machines. Our cleanroom is built in a modular way, which allows us to be flexible and increase size as quickly as possible according to customers’ needs. Three of our global locations include high-tech tool shops, which enable us to quickly develop molds from prototype to production, as well as perform maintenance and repairs. Manufacturing transfer Thinking about moving production out of China? Facing rising costs and import/export issues with medical device production in China, VEM helps clients with an expedited manufacturing transfer of plastic injection molding and assembly projects from China to Thailand with their supply chains intact. VEM has been manufacturing in Thailand for 13 years and medical device manufacturing project transfers are among our most popular services and can be set up and running within just a few weeks. For more information, read our case study under the ‘White Papers’ tab on this page. Medical plastics and device manufacturing in Thailand Manufacturing in Southeast Asia offers a lower price point, more flexibility, and a faster time to market than domestic manufacturing can provide. For more than 13 years, VEM has operated its wholly-owned manufacturing operation in Rayong, Thailand. The largest port in Thailand, Laem Chabang Port, is just a 30-minute drive from our facility and many large medical device and healthcare manufacturers are located nearby. There is an undeniable reason behind the growth of the medical device manufacturing industry in Thailand. The location is strategically attractive due to a skilled and educated workforce, a welcoming and open economy with a stable government, quality infrastructure, lower cost of labour and reduced import taxes, and ease of import/export of raw materials and components. About VEM Medical VEM currently has five manufacturing facilities across Asia, Europe and Central America. Our facility in Thailand is ISO 13485:2016 certified and specialises in medical device production and assembly. Our tool shop in Shenzhen, China, manufactures molds for our medical device clients worldwide.
Different fiber sources may be used that are often considered waste from food production operations, for example, bagasse or rice husks.
For more information, read our case study under the ‘White Papers’ tab on this page. Medical plastics and device manufacturing in Thailand Manufacturing in Southeast Asia offers a lower price point, more flexibility, and a faster time to market than domestic manufacturing can provide. For more than 13 years, VEM has operated its wholly-owned manufacturing operation in Rayong, Thailand. The largest port in Thailand, Laem Chabang Port, is just a 30-minute drive from our facility and many large medical device and healthcare manufacturers are located nearby. There is an undeniable reason behind the growth of the medical device manufacturing industry in Thailand. The location is strategically attractive due to a skilled and educated workforce, a welcoming and open economy with a stable government, quality infrastructure, lower cost of labour and reduced import taxes, and ease of import/export of raw materials and components. About VEM Medical VEM currently has five manufacturing facilities across Asia, Europe and Central America. Our facility in Thailand is ISO 13485:2016 certified and specialises in medical device production and assembly. Our tool shop in Shenzhen, China, manufactures molds for our medical device clients worldwide.
Rick Lingle is Senior Technical Editor, Packaging Digest and PlasticsToday. He’s been a packaging media journalist since 1985 specializing in food, beverage and plastic markets. He has a chemistry degree from Clarke College and has worked in food industry R&D for Standard Brands/Nabisco and the R.T. French Co. Reach him at [email protected] or 630-481-1426.
VEM Group, a global tooling and molding provider to the medical device, automotive, and consumer goods industry, has expanded operations into Eastern Europe. The wholly owned manufacturing plant is located in Plovdiv, Bulgaria, which is the cultural capital and second largest city in Bulgaria.
He believes there will be more industrial composting infrastructure in the coming months, driven by the popularity of corn-based polylactic acid (PLA) and other compostable biopolymers and as the circular economy continues to develop.
Company founder Douglas Horne was an elected government official in British Columbia, Canada, when he came across the technology. It so profoundly changed his way of thinking about packaging that it prompted Horne to change careers.
The technology adapts standard food processing equipment.“We’re taking technology that's been around for years and adapting it to use a different dough for making packaging,” says Horne. “The dough is formed by a ‘waffle-iron’ type of molding system into a tray or other packaging shape using the same kind of tried-and-true machinery that makes Twix candy bars, cookies, and other food products. We have a mechanized batch process using equipment from Bühler to produce hundreds of items at a time that are then baked in an oven.”
VEM’s in-house medical molds have helped us develop medical parts for molding and assembly for years. Our fully owned mold manufacturer consistently gives us complete control over molds and materials, allowing for optimal quality control. Optimisation, rigorous quality testing, and a professional approach to solving problems have always been our key approaches. Our molds are used worldwide by large medical companies, including Danaher Corporation, Cepheid, Foamtec Medical and Freudenberg Medical. Cleanroom molding and assembly VEM can offer services in design assistance, prototyping, production mold making, injection molding in a white room or cleanroom, component sourcing, assembly, testing and packaging. Both inside and outside our cleanroom, we have room and equipment for various sizes of injection machines. Our cleanroom is built in a modular way, which allows us to be flexible and increase size as quickly as possible according to customers’ needs. Three of our global locations include high-tech tool shops, which enable us to quickly develop molds from prototype to production, as well as perform maintenance and repairs. Manufacturing transfer Thinking about moving production out of China? Facing rising costs and import/export issues with medical device production in China, VEM helps clients with an expedited manufacturing transfer of plastic injection molding and assembly projects from China to Thailand with their supply chains intact. VEM has been manufacturing in Thailand for 13 years and medical device manufacturing project transfers are among our most popular services and can be set up and running within just a few weeks. For more information, read our case study under the ‘White Papers’ tab on this page. Medical plastics and device manufacturing in Thailand Manufacturing in Southeast Asia offers a lower price point, more flexibility, and a faster time to market than domestic manufacturing can provide. For more than 13 years, VEM has operated its wholly-owned manufacturing operation in Rayong, Thailand. The largest port in Thailand, Laem Chabang Port, is just a 30-minute drive from our facility and many large medical device and healthcare manufacturers are located nearby. There is an undeniable reason behind the growth of the medical device manufacturing industry in Thailand. The location is strategically attractive due to a skilled and educated workforce, a welcoming and open economy with a stable government, quality infrastructure, lower cost of labour and reduced import taxes, and ease of import/export of raw materials and components. About VEM Medical VEM currently has five manufacturing facilities across Asia, Europe and Central America. Our facility in Thailand is ISO 13485:2016 certified and specialises in medical device production and assembly. Our tool shop in Shenzhen, China, manufactures molds for our medical device clients worldwide.
VEM is an integrated partner from design assistance and design for manufacturing to finished device production and assembly. Our fully owned tool shops, cleanroom production, assembly and sub-assembly capabilities provide rich opportunities to partner with us, no matter which stage your product is in. Our experienced team uses the newest equipment and automation, including brands such as Arburg, Toshiba, GF, Hexagon and Makino. Being transparent when producing parts is what makes us stand out. Not only will we set up the production in accordance with all your needs but we can also help to improve process quality and reduce cycle times. In-house medical tooling VEM’s in-house medical molds have helped us develop medical parts for molding and assembly for years. Our fully owned mold manufacturer consistently gives us complete control over molds and materials, allowing for optimal quality control. Optimisation, rigorous quality testing, and a professional approach to solving problems have always been our key approaches. Our molds are used worldwide by large medical companies, including Danaher Corporation, Cepheid, Foamtec Medical and Freudenberg Medical. Cleanroom molding and assembly VEM can offer services in design assistance, prototyping, production mold making, injection molding in a white room or cleanroom, component sourcing, assembly, testing and packaging. Both inside and outside our cleanroom, we have room and equipment for various sizes of injection machines. Our cleanroom is built in a modular way, which allows us to be flexible and increase size as quickly as possible according to customers’ needs. Three of our global locations include high-tech tool shops, which enable us to quickly develop molds from prototype to production, as well as perform maintenance and repairs. Manufacturing transfer Thinking about moving production out of China? Facing rising costs and import/export issues with medical device production in China, VEM helps clients with an expedited manufacturing transfer of plastic injection molding and assembly projects from China to Thailand with their supply chains intact. VEM has been manufacturing in Thailand for 13 years and medical device manufacturing project transfers are among our most popular services and can be set up and running within just a few weeks. For more information, read our case study under the ‘White Papers’ tab on this page. Medical plastics and device manufacturing in Thailand Manufacturing in Southeast Asia offers a lower price point, more flexibility, and a faster time to market than domestic manufacturing can provide. For more than 13 years, VEM has operated its wholly-owned manufacturing operation in Rayong, Thailand. The largest port in Thailand, Laem Chabang Port, is just a 30-minute drive from our facility and many large medical device and healthcare manufacturers are located nearby. There is an undeniable reason behind the growth of the medical device manufacturing industry in Thailand. The location is strategically attractive due to a skilled and educated workforce, a welcoming and open economy with a stable government, quality infrastructure, lower cost of labour and reduced import taxes, and ease of import/export of raw materials and components. About VEM Medical VEM currently has five manufacturing facilities across Asia, Europe and Central America. Our facility in Thailand is ISO 13485:2016 certified and specialises in medical device production and assembly. Our tool shop in Shenzhen, China, manufactures molds for our medical device clients worldwide.
VEM Group, a global tooling and molding provider to the medical device and consumer goods industry, will exhibit at the upcoming trade fair Design & Manufacturing West, also known as MD&M West. This event is the leading U.S. tradeshow and conference for the medical device manufacturing industry which takes place August 10-12 in Anaheim, California. VEM will be exhibiting in Hall D, booth 3327.
For more than 20 years, VEM has focused on customer satisfaction as our highest priority. Our clients range from small innovative companies to large multinational original equipment manufacturers (OEMs). Our production facility is certified according to ISO 9001 and ISO 13485, with a Class 100,000 (ISO 8) cleanroom. VEM Medical can produce small and precise molded parts for medical devices. Our medical assembly line is inspected by a stringent quality control team. A static 2K mixer for medical applications. VEM Medical can produce injection-molded parts for medical sub-assembly. Each of our manufactured devices must pass a testing procedure specified by the customer. Medical inserts can be molded in our clean room. We produce parts through complex medical tooling. Our team sub-assembles a tube connection for a breathing device. Many different parts can be moulded in our Class 100,000 cleanroom. Medical plastics and device manufacturing VEM is an integrated partner from design assistance and design for manufacturing to finished device production and assembly. Our fully owned tool shops, cleanroom production, assembly and sub-assembly capabilities provide rich opportunities to partner with us, no matter which stage your product is in. Our experienced team uses the newest equipment and automation, including brands such as Arburg, Toshiba, GF, Hexagon and Makino. Being transparent when producing parts is what makes us stand out. Not only will we set up the production in accordance with all your needs but we can also help to improve process quality and reduce cycle times. In-house medical tooling VEM’s in-house medical molds have helped us develop medical parts for molding and assembly for years. Our fully owned mold manufacturer consistently gives us complete control over molds and materials, allowing for optimal quality control. Optimisation, rigorous quality testing, and a professional approach to solving problems have always been our key approaches. Our molds are used worldwide by large medical companies, including Danaher Corporation, Cepheid, Foamtec Medical and Freudenberg Medical. Cleanroom molding and assembly VEM can offer services in design assistance, prototyping, production mold making, injection molding in a white room or cleanroom, component sourcing, assembly, testing and packaging. Both inside and outside our cleanroom, we have room and equipment for various sizes of injection machines. Our cleanroom is built in a modular way, which allows us to be flexible and increase size as quickly as possible according to customers’ needs. Three of our global locations include high-tech tool shops, which enable us to quickly develop molds from prototype to production, as well as perform maintenance and repairs. Manufacturing transfer Thinking about moving production out of China? Facing rising costs and import/export issues with medical device production in China, VEM helps clients with an expedited manufacturing transfer of plastic injection molding and assembly projects from China to Thailand with their supply chains intact. VEM has been manufacturing in Thailand for 13 years and medical device manufacturing project transfers are among our most popular services and can be set up and running within just a few weeks. For more information, read our case study under the ‘White Papers’ tab on this page. Medical plastics and device manufacturing in Thailand Manufacturing in Southeast Asia offers a lower price point, more flexibility, and a faster time to market than domestic manufacturing can provide. For more than 13 years, VEM has operated its wholly-owned manufacturing operation in Rayong, Thailand. The largest port in Thailand, Laem Chabang Port, is just a 30-minute drive from our facility and many large medical device and healthcare manufacturers are located nearby. There is an undeniable reason behind the growth of the medical device manufacturing industry in Thailand. The location is strategically attractive due to a skilled and educated workforce, a welcoming and open economy with a stable government, quality infrastructure, lower cost of labour and reduced import taxes, and ease of import/export of raw materials and components. About VEM Medical VEM currently has five manufacturing facilities across Asia, Europe and Central America. Our facility in Thailand is ISO 13485:2016 certified and specialises in medical device production and assembly. Our tool shop in Shenzhen, China, manufactures molds for our medical device clients worldwide.
And there’s one more distinction. “Because of the way it’s made, a unique feature of the packaging is that there’s a circle molded on the bottom,” he points out. “That could help distinguish our compostable products from other types of packaging at a municipal waste facility.”
In considering composting from a regulator's viewpoint, Horne suggests “we likely don’t want everyone to have a compost heap in the backyard.”
“I don’t see FPI members as competitors,” Horne says. “I see them as future partners, and I see us growing by licensing our technology and gaining widespread adoption as quickly as possible.” He’s in discussions with a highly interested, major foodservice packaging supplier.
The R&D operations are in Vienna, Austria. However, having manufacturing capability in the US is critical, Horne emphasizes. “We’ll move to new molded starch production in early 2022 after we upgrade to our full-scale machines to make millions of units next spring.”
There is an undeniable reason behind the growth of the medical device manufacturing industry in Thailand. The location is strategically attractive due to a skilled and educated workforce, a welcoming and open economy with a stable government, quality infrastructure, lower cost of labour and reduced import taxes, and ease of import/export of raw materials and components. About VEM Medical VEM currently has five manufacturing facilities across Asia, Europe and Central America. Our facility in Thailand is ISO 13485:2016 certified and specialises in medical device production and assembly. Our tool shop in Shenzhen, China, manufactures molds for our medical device clients worldwide.
“EPS and other plastics have done so well in the market is because they're inexpensive, versatile, and can be made into many shapes and forms,” says Horne. “Our products are comparable, though perhaps slightly higher in cost because of the value-added attributes.”
VEM Europe, part of VEM Group, a global tooling and molding provider to the medical device and consumer goods industry, will exhibit at the upcoming trade fair Interplas, September 28-30. It is the UK’s leading plastics industry event, an exciting showcase for technologies, manufacturing processes and services essential to the plastics sector. VEM will be exhibiting at booth C69.
“Another exciting aspect of the technology is that the starch and fiber don’t have to come from a specific source,” Horne divulges. “The ingredients are a variable supply-and-demand factor to further keep costs low by using the cheapest available fiber source.”
The novel packaging is a molded starch-and-fiber product different than everything else including thermoformed fiber products, according to Horne. “It looks and feels like a traditional thermoformed plastic tray."
“One of the exciting that we're getting into now is a deeper product: cups that look like they’re made of EPS,” discloses Horne. “These cups offer insulative properties for foodservice markets.”
Optimisation, rigorous quality testing, and a professional approach to solving problems have always been our key approaches. Our molds are used worldwide by large medical companies, including Danaher Corporation, Cepheid, Foamtec Medical and Freudenberg Medical. Cleanroom molding and assembly VEM can offer services in design assistance, prototyping, production mold making, injection molding in a white room or cleanroom, component sourcing, assembly, testing and packaging. Both inside and outside our cleanroom, we have room and equipment for various sizes of injection machines. Our cleanroom is built in a modular way, which allows us to be flexible and increase size as quickly as possible according to customers’ needs. Three of our global locations include high-tech tool shops, which enable us to quickly develop molds from prototype to production, as well as perform maintenance and repairs. Manufacturing transfer Thinking about moving production out of China? Facing rising costs and import/export issues with medical device production in China, VEM helps clients with an expedited manufacturing transfer of plastic injection molding and assembly projects from China to Thailand with their supply chains intact. VEM has been manufacturing in Thailand for 13 years and medical device manufacturing project transfers are among our most popular services and can be set up and running within just a few weeks. For more information, read our case study under the ‘White Papers’ tab on this page. Medical plastics and device manufacturing in Thailand Manufacturing in Southeast Asia offers a lower price point, more flexibility, and a faster time to market than domestic manufacturing can provide. For more than 13 years, VEM has operated its wholly-owned manufacturing operation in Rayong, Thailand. The largest port in Thailand, Laem Chabang Port, is just a 30-minute drive from our facility and many large medical device and healthcare manufacturers are located nearby. There is an undeniable reason behind the growth of the medical device manufacturing industry in Thailand. The location is strategically attractive due to a skilled and educated workforce, a welcoming and open economy with a stable government, quality infrastructure, lower cost of labour and reduced import taxes, and ease of import/export of raw materials and components. About VEM Medical VEM currently has five manufacturing facilities across Asia, Europe and Central America. Our facility in Thailand is ISO 13485:2016 certified and specialises in medical device production and assembly. Our tool shop in Shenzhen, China, manufactures molds for our medical device clients worldwide.
A dough is created from a mix of 60% starch, 35% fiber, and 5% other ingredients that Horne indicates is the “secret sauce” that makes this work.
Our experienced team uses the newest equipment and automation, including brands such as Arburg, Toshiba, GF, Hexagon and Makino. Being transparent when producing parts is what makes us stand out. Not only will we set up the production in accordance with all your needs but we can also help to improve process quality and reduce cycle times. In-house medical tooling VEM’s in-house medical molds have helped us develop medical parts for molding and assembly for years. Our fully owned mold manufacturer consistently gives us complete control over molds and materials, allowing for optimal quality control. Optimisation, rigorous quality testing, and a professional approach to solving problems have always been our key approaches. Our molds are used worldwide by large medical companies, including Danaher Corporation, Cepheid, Foamtec Medical and Freudenberg Medical. Cleanroom molding and assembly VEM can offer services in design assistance, prototyping, production mold making, injection molding in a white room or cleanroom, component sourcing, assembly, testing and packaging. Both inside and outside our cleanroom, we have room and equipment for various sizes of injection machines. Our cleanroom is built in a modular way, which allows us to be flexible and increase size as quickly as possible according to customers’ needs. Three of our global locations include high-tech tool shops, which enable us to quickly develop molds from prototype to production, as well as perform maintenance and repairs. Manufacturing transfer Thinking about moving production out of China? Facing rising costs and import/export issues with medical device production in China, VEM helps clients with an expedited manufacturing transfer of plastic injection molding and assembly projects from China to Thailand with their supply chains intact. VEM has been manufacturing in Thailand for 13 years and medical device manufacturing project transfers are among our most popular services and can be set up and running within just a few weeks. For more information, read our case study under the ‘White Papers’ tab on this page. Medical plastics and device manufacturing in Thailand Manufacturing in Southeast Asia offers a lower price point, more flexibility, and a faster time to market than domestic manufacturing can provide. For more than 13 years, VEM has operated its wholly-owned manufacturing operation in Rayong, Thailand. The largest port in Thailand, Laem Chabang Port, is just a 30-minute drive from our facility and many large medical device and healthcare manufacturers are located nearby. There is an undeniable reason behind the growth of the medical device manufacturing industry in Thailand. The location is strategically attractive due to a skilled and educated workforce, a welcoming and open economy with a stable government, quality infrastructure, lower cost of labour and reduced import taxes, and ease of import/export of raw materials and components. About VEM Medical VEM currently has five manufacturing facilities across Asia, Europe and Central America. Our facility in Thailand is ISO 13485:2016 certified and specialises in medical device production and assembly. Our tool shop in Shenzhen, China, manufactures molds for our medical device clients worldwide.
The word evanesce means to disappear. “That defines the company and our product: Evanesce Molded Starch technology is the essence of what we do,” he explains.
VEM can offer services in design assistance, prototyping, production mold making, injection molding in a white room or cleanroom, component sourcing, assembly, testing and packaging. Both inside and outside our cleanroom, we have room and equipment for various sizes of injection machines. Our cleanroom is built in a modular way, which allows us to be flexible and increase size as quickly as possible according to customers’ needs. Three of our global locations include high-tech tool shops, which enable us to quickly develop molds from prototype to production, as well as perform maintenance and repairs. Manufacturing transfer Thinking about moving production out of China? Facing rising costs and import/export issues with medical device production in China, VEM helps clients with an expedited manufacturing transfer of plastic injection molding and assembly projects from China to Thailand with their supply chains intact. VEM has been manufacturing in Thailand for 13 years and medical device manufacturing project transfers are among our most popular services and can be set up and running within just a few weeks. For more information, read our case study under the ‘White Papers’ tab on this page. Medical plastics and device manufacturing in Thailand Manufacturing in Southeast Asia offers a lower price point, more flexibility, and a faster time to market than domestic manufacturing can provide. For more than 13 years, VEM has operated its wholly-owned manufacturing operation in Rayong, Thailand. The largest port in Thailand, Laem Chabang Port, is just a 30-minute drive from our facility and many large medical device and healthcare manufacturers are located nearby. There is an undeniable reason behind the growth of the medical device manufacturing industry in Thailand. The location is strategically attractive due to a skilled and educated workforce, a welcoming and open economy with a stable government, quality infrastructure, lower cost of labour and reduced import taxes, and ease of import/export of raw materials and components. About VEM Medical VEM currently has five manufacturing facilities across Asia, Europe and Central America. Our facility in Thailand is ISO 13485:2016 certified and specialises in medical device production and assembly. Our tool shop in Shenzhen, China, manufactures molds for our medical device clients worldwide.
A dough made from starch, fiber, and little else that’s baked into compostable packaging using patented technology by Evanesce Packaging Solutions is a breakthrough recipe for sustainable packaging.
VEM Medical is a full-service contract manufacturing organisation for medical plastics, devices and components. We partner with medical device companies across three continents to provide plastic injection molding, in-house tooling, prototyping, assembly, testing and more. A highly experienced team, best-in-class equipment and rigorous quality control help us deliver solutions for challenging medical tooling and molding applications. For more than 20 years, VEM has focused on customer satisfaction as our highest priority. Our clients range from small innovative companies to large multinational original equipment manufacturers (OEMs). Our production facility is certified according to ISO 9001 and ISO 13485, with a Class 100,000 (ISO 8) cleanroom. VEM Medical can produce small and precise molded parts for medical devices. Our medical assembly line is inspected by a stringent quality control team. A static 2K mixer for medical applications. VEM Medical can produce injection-molded parts for medical sub-assembly. Each of our manufactured devices must pass a testing procedure specified by the customer. Medical inserts can be molded in our clean room. We produce parts through complex medical tooling. Our team sub-assembles a tube connection for a breathing device. Many different parts can be moulded in our Class 100,000 cleanroom. Medical plastics and device manufacturing VEM is an integrated partner from design assistance and design for manufacturing to finished device production and assembly. Our fully owned tool shops, cleanroom production, assembly and sub-assembly capabilities provide rich opportunities to partner with us, no matter which stage your product is in. Our experienced team uses the newest equipment and automation, including brands such as Arburg, Toshiba, GF, Hexagon and Makino. Being transparent when producing parts is what makes us stand out. Not only will we set up the production in accordance with all your needs but we can also help to improve process quality and reduce cycle times. In-house medical tooling VEM’s in-house medical molds have helped us develop medical parts for molding and assembly for years. Our fully owned mold manufacturer consistently gives us complete control over molds and materials, allowing for optimal quality control. Optimisation, rigorous quality testing, and a professional approach to solving problems have always been our key approaches. Our molds are used worldwide by large medical companies, including Danaher Corporation, Cepheid, Foamtec Medical and Freudenberg Medical. Cleanroom molding and assembly VEM can offer services in design assistance, prototyping, production mold making, injection molding in a white room or cleanroom, component sourcing, assembly, testing and packaging. Both inside and outside our cleanroom, we have room and equipment for various sizes of injection machines. Our cleanroom is built in a modular way, which allows us to be flexible and increase size as quickly as possible according to customers’ needs. Three of our global locations include high-tech tool shops, which enable us to quickly develop molds from prototype to production, as well as perform maintenance and repairs. Manufacturing transfer Thinking about moving production out of China? Facing rising costs and import/export issues with medical device production in China, VEM helps clients with an expedited manufacturing transfer of plastic injection molding and assembly projects from China to Thailand with their supply chains intact. VEM has been manufacturing in Thailand for 13 years and medical device manufacturing project transfers are among our most popular services and can be set up and running within just a few weeks. For more information, read our case study under the ‘White Papers’ tab on this page. Medical plastics and device manufacturing in Thailand Manufacturing in Southeast Asia offers a lower price point, more flexibility, and a faster time to market than domestic manufacturing can provide. For more than 13 years, VEM has operated its wholly-owned manufacturing operation in Rayong, Thailand. The largest port in Thailand, Laem Chabang Port, is just a 30-minute drive from our facility and many large medical device and healthcare manufacturers are located nearby. There is an undeniable reason behind the growth of the medical device manufacturing industry in Thailand. The location is strategically attractive due to a skilled and educated workforce, a welcoming and open economy with a stable government, quality infrastructure, lower cost of labour and reduced import taxes, and ease of import/export of raw materials and components. About VEM Medical VEM currently has five manufacturing facilities across Asia, Europe and Central America. Our facility in Thailand is ISO 13485:2016 certified and specialises in medical device production and assembly. Our tool shop in Shenzhen, China, manufactures molds for our medical device clients worldwide.
Facing rising costs and import/export issues with medical device production in China, VEM Medical helps clients with an expedited manufacturing transfer of plastic injection molding and assembly projects from China, where costs continue to rise, to Thailand with supply chains intact.
GETTING A QUOTE WITH LK-MOULD IS FREE AND SIMPLE.
FIND MORE OF OUR SERVICES:
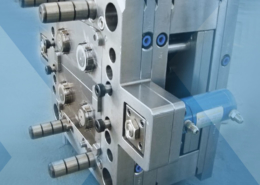
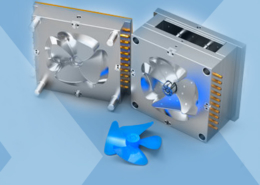
Plastic Molding

Rapid Prototyping
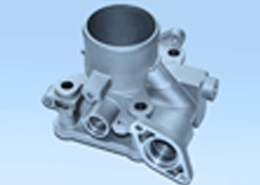
Pressure Die Casting
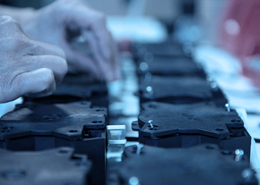
Parts Assembly
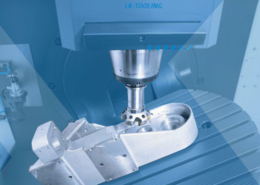