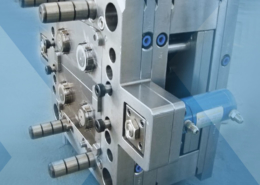
This Kickstarter Aims To Bring Injection Molding To Your Desktop - 3d printed pl
Author:gly Date: 2024-09-30
We pay considerable attention to cosmetic defects. This is one area that design engineers do not understand well. There is a lot of information on designing mechanical structures, but aesthetics is often overlooked.
This sidebar to CW’s August 2024 feature article reviews this technology for more efficient composites manufacturing and why it aligns with Koridion active core molding.
“We’re getting a resounding response from airframers and others in the market,” claims Herr. “This technology gives engineers the flexibility they want to design a very robust yet lightweight, load-carrying part.” He explains this is one reason why Commercial Aircraft Corp. of China (COMAC, Shanghai) is fully engaged and actively looking at where PEEK can replace heavy, costly metals.
“We could mold PEEK over PEEK, but it doesn’t fuse together,” says Herr. Fusion of the matrices requires a substrate with a lower melt temperature than the overmold. “If you don’t fuse the two, you don’t consolidate the part,” Herr points out. “So, we needed a low-temperature processing PAEK that has PEEK properties.” Think of PAEK as the polymer family — Victrex can make different formulations, each with a specific molecular weight, melt temperature and Tg — with PEEK being one species. Thus, Victrex developed the PAEK A250 polymer, with a melt temperature of 305°C (see Table 1, at left). “We have enabled not only overmolding with PEEK,” claims Herr, “but also the ability to achieve PEEK-type properties at processing temperatures similar to PPS or PEI with current equipment.”
Six U.S. companies have proven their recycling technologies for composites and rare earth elements, and will be supported for relevant scale demonstration and validation.
The first project is underway to recover carbon fiber used in an A330-200 aircraft, which will then be regenerated for other end uses by HRC.
The company’s portfolio includes everything from beverage caps to currency cassette modules for ATMs. Recently, we sat down with Karl Stillman, regional sales director at Rosti, to talk about part design and how to with contract manufacturers.
This collection features detail the current state of the industry and recent success stories across aerospace, automotive and rail applications.
A new polymer and a hybrid process enable production of complex, high-load-capable, fiber-reinforced brackets and clips in minutes.
Additionally, stitch-bonded non-crimp fabrics (NCFs) provide manufacturers and asset owners even more ways to gain a competitive advantage with products built specifically for the environments and loading conditions in which they will be utilized. Join Vectorply Corporation and Creative Composites Group (CCG) for this in-depth webinar detailing the process of engineering NCFs to build composite parts that will stand the test of time. Unlike steel, concrete and wood, composite NCFs can be optimized utilizing various fiber types, architectures and substrates to achieve the specific goals of their application efficiently. High corrosion resistance, strength and stiffness, and longevity can all be accomplished with custom-designed laminates for these heavily abused applications. Vectorply Vice President of Engineering Trevor Gundberg and Creative Composites Group Chief Sales Officer Dustin Troutman will share their industry-leading expertise on the process of laminate design and part production. Attendees can expect to learn when to use composite NCFs in their production process and the wide range of fiber-reinforced plastic (FRP) composites that Creative Composites Group produces for the industrial and infrastructure markets. Whether you want to learn more about utilizing NCFs in your production process or why CCG’s extensive product line may be the choice for your project, this webinar is the place learn the process and how to take the next steps. Agenda: Distinct advantages of non-crimp fabrics versus alternative materials How to design laminates for specific processes such as pultrusion and infusion Real-world success spotlights of NCFs in industrial applications
Whether you’re exploring new applications or seeking to gain a foothold in emerging markets, Carbon Fiber 2024 is where you’ll discover the insights and connections needed to shape your business strategy. Register now.
For example, we conduct finite element analyses on snap fits, load-bearing members and pressure vessels. We can simulate various bonding technologies, welding methods and mechanical fasteners under dynamic loading conditions. We like to take a holistic view of the assembly process and the product’s operational conditions. Only by understanding risks can we advise our customers and add value to the product.
Program will focus on sustainable, next-gen wing solutions, including in wing design and manufacturing and advancements in carbon fiber-reinforced composite materials.
“The design flexibility is huge,” he adds, noting the same bracket made with forged metal would require a significant amount of machining. “That’s easy to beat with a 2-3 minute injection molding.” Kneath concedes there is a tooling cost, but says the payback is usually pretty quick. “Most aerospace companies will say they don’t have the volumes for injection molding, but we’ve been injection molding aerospace parts for 40 years, and know how to design tooling that balances cash and performance requirements.”
Initial demonstration in furniture shows properties two to nine times higher than plywood, OOA molding for uniquely shaped components.
Based in Malmö, Sweden, Rosti Group is a global injection-molding company and contract manufacturer to some of the world’s leading manufacturers in the packaging, consumer appliances, business machines, home automation, medical and automotive sectors. An exhibitor at the 2020 virtual ASSEMBLY Show, Rosti operates production facilities in China, Germany, Malaysia, Poland, Romania, Turkey and the UK.
During this CW Tech Days event, sponsored by Composites One, experts will offer presentations to review and evaluate the composite materials, processes and applications that should and will be considered for use in the infrastructure and construction markets.
Stillman: The most common input is on part design for moldability. Rosti’s core competence is injection molding. We have an extensive knowledge base that we draw upon for every new project. As a contract molder and manufacturer, we have exposure to many different designs and materials, so we are well-versed in what works and what does not work. With the help of our certified Autodesk Moldflow engineering team, we can quickly identify areas that will result in molding defects and proactively design these out.
Formnext Chicago is an industrial additive manufacturing expo taking place April 8-10, 2025 at McCormick Place in Chicago, Illinois. Formnext Chicago is the second in a series of Formnext events in the U.S. being produced by Mesago Messe Frankfurt, AMT – The Association For Manufacturing Technology, and Gardner Business Media (our publisher).
To demonstrate the process, Tri-Mack needed a part that would deliver the message. “There are so many brackets used in aerospace,” says Kneath, “and we’ve made a simple bracket with thermoplastic composites, so we decided to design a complex bracket shape that would also bear significant load.” The design is loaded in three axes and incorporates four mounting points that rely on co-molded metal inserts in the PEEK overmold, the latter a typical feature of Tri-Mack’s unreinforced thermoplastic brackets. “We load the aerospace-grade, carbon fiber-reinforced PAEK substrate and four metal inserts into a standard injection mold,” describes Kneath. “We use a standard process to inject VICTREX PEEK 150CA30” — 30% carbon fiber-reinforced compound — “over the substrate, and minutes later, we have an integrated assembly that marries the performance of PEEK composites with the cost efficiency of injection molding.” (See photo at left.) Initial testing shows a very robust bond between the PAEK and PEEK matrices. “This will build confidence in the engineering community as they start to design parts exploiting this technology,” Kneath asserts.
Thermoplastics for Large Structures, experts explored the materials and processing technologies that are enabling the transition to large-part manufacturing.
Stillman: These test can predict, on a statistical basis, whether our prototypes or our production processes are going to exceed the product’s quality requirements. We strive to be 100 percent confident in our process setup prior to production. In fact, we have developed a six-step process to qualify parts with as wide a process window as possible to ensure production stability. We also monitor the injection molding process.
Stillman: One of the key steps in any new project is fact finding. In many cases, we’re only molding the parts, which will be assembled at the customer’s site. However, it’s very important to know the eventual assembly method, because that enables us to add value to the design. Knowing the downstream value chain and operations is key in our analysis.
Stillman: This depends on the design intent of the part. Over and above the standard dimensional checking and our statistical process control, we measure surface roughness to single-digit nanometer deviations for optical parts. We assess mechanical strength for safety-critical parts. For in-mold decorated parts, we assess chemical resistance and scratch resistance of the artwork. We do peel strength testing for overmolding.
Cevotec, a tank manufacturer, Roth Composite Machinery and Cikoni, have undertaken a comprehensive project to explore and demonstrate the impact of dome reinforcements using FPP technology for composite tanks.
Reliable news and information on where and how fiber-reinforced composites are being applied — that’s just the start of what you get from our team here at CompositesWorld.
Stillman: To be honest, the occasions where we do not offer design recommendations would be an easier number to quantify. The truth is, we provide recommendations and suggestions to our customers more often than not.
“About 3-4 years ago, we recognized that compression-formed laminates did not offer the design flexibility and manufacturing efficiency being sought by aircraft designers,” says Tim Herr, aerospace strategic business director for PEEK supplier Victrex Polymer Solutions (Cleveleys, Lancashire, UK). Drawing on the high-temperature-capable, high-performance resins’ 25-year history in the aircraft industry in both filled and unfilled injection molded plastic parts, such as mounts and spacers, tubing, housings and electrical connectors, Herr’s Victrex team and aerospace parts manufacturer Tri-Mack (Bristol, RI, US) began to explore the concept of injection overmolding as a means of overcoming the limitations inherent in thermostamping of preconsolidated blanks.
Stillman: Yes, this happens several times per year. It’s all about understanding the boundary conditions of the parts, such as geometric envelope, usage conditions and assembly processes. From there, we dive into the design to realize a workable solution. This may result in significant design changes. There might be material changes, process changes or one part may have to be separated into two parts. We always find a solution by working closely with the customer.
Advanced Engineering is the UK’s largest annual gathering of engineering and manufacturing professionals. The event will help you to source new suppliers, network, build connections and learn about the latest industry developments all in one place. Get involved and exhibit alongside 400+ exhibitors offering solutions and products across all industries and sectors to help improve your productivity and inspire creativity. With over 9,000+ of your peers due to attend and ready to network with and inspire you, this is the event you can’t afford to miss!
Finally, we think about assembly. What are the tolerance stack-ups? How do moving parts interact? Can the parts be easily assembled? Can error-proofing features be added?
Explore the cutting-edge composites industry, as experts delve into the materials, tooling, and manufacturing hurdles of meeting the demands of the promising advanced air mobility (AAM) market. Join us at CW Tech Days to unlock the future of efficient composites fabrication operations.
Low-melt polyaryletherketone (LMPAEK) unidirectional tapes provide outstanding thermal and fire protection, demonstrating their effectiveness through rigorous testing. These tapes are fire, smoke and toxicity compliant with FAR25.853 and meet OSU Heat Release Rate standards. The tapes were tested under ISO 2685/AC 20-135 Change 1, meeting the fireproof criteria. Additionally, they met UL 2596 requirements for battery thermal runaway tests. These tapes are crucial for high-temperature applications showcasing their resilience and safety in both aerospace and automotive applications. Part of a broader range that includes films and compounds, Victrex LMPAEK materials are valued for their excellent processability and weldability. They offer versatile solutions for complex needs beyond traditional structural parts, such as: thermal runaway and lightning strike protection, heat sinking, and intricate bracketry. Victrex LMPAEK materials facilitate automation and high-rate production while addressing performance and sustainability challenges. With reduced environmental impact, lower weight and cost-efficiency, they meet the evolving demands of the transportation industry and support innovative design solutions. Agenda: Introduction to LMPAEK ecosystem, highlighting unidirectional tapes Thermal and fire protection performance: applications and benefits Material forms and processability Sustainability and efficiency Conclusion and future innovations
In contrast, injection molding of neat thermoplastics produces complex components in minutes, but limits the molder’s ability to optimize part functionality. “What’s great about this hybrid process,” Kneath points out, “is that you can put the material where you need it, vs. standard injection molding, where you can’t really selectively reinforce parts easily.”
Jetcam’s latest white paper explores the critical aspects of nesting in composites manufacturing, and strategies to balance material efficiency and kitting speed.
An on-demand mapping tool for anisotropic materials and polymer material fracture prediction model, i-Lupe, aims to help predict impact, crash behaviors.
An overview of ASTM Standard Guide D8509, and its coupon-level mechanical testing of design properties for analyzing composite bolted joints.
Aerospace manufacturer joins forces with composite materials company to achieve sustainable manufacturing practices that overcome traditional composite layup tooling.
Celebrating National Composites Week 2024, CW looks at how composites are being used to provide the next generation of energy.
However, that’s just the tip of the iceberg. We have learned from past experience that part designs do not always behave the same way when we transition from printed prototypes to molded parts. There are a number of reasons for this. The print material does not behave the same as the molded resin. The layering process results in anisotropic properties, which are not as homogeneous as molded parts. The molding process results in shrinkage and molding stresses in the parts.
Whether you’re exploring new applications or seeking to gain a foothold in emerging markets, Carbon Fiber 2024 is where you’ll discover the insights and connections needed to shape your business strategy. Register now.
Best performance at least weight: The hybrid molding process uses a flat, lower temperature VICTREX PAEK composite substrate overmolded by short fiber-reinforced PEEK with co-molded metal inserts. The resulting finished bracket is as much as 60% lighter than comparable metal components. Source: Tri-Mack
How the predictive tool “CZone” is applied to simulate the axial crushing response of composites, providing valuable insights into their use for motorsport applications.
Stephen Heinz, vice president of R&I for Syensqo delivered an inspirational keynote at SAMPE 2024, highlighting the significant role of composite materials in emerging technologies and encouraging broader collaboration within the manufacturing community.
New aircraft is expected to deliver wind turbine blades from 105 meters up to expand the reach of wind energy and achieve global climate goals.
CW Tech Days are virtual events dedicated to the topics impacting the composites industry today. Access past event recordings and register for upcoming Tech Days.
“Solving the problem of quick COVID diagnostics testing is one of our priorities at Rosti,” says Karl Stillman, regional sales director at Rosti Group. “We are delighted that our 72-hour 3D printing capabilities made it possible for our customer to produce test kits quickly and cost effectively.”
In the composites industry, use of polyetheretherketone (PEEK) has recently experienced an uptick in thermostamped aircraft fuselage clips and brackets made from preconsolidated blanks with woven and/or unidirectional reinforcements (see “Thermoplastic composites "clip" time, labor on small but crucial parts" and "Inside a thermoplastic composites hotbed," under "Editor's Picks,” at top right). But those who use and those who make the blanks recognize their limitations.
We are a service provider. In theory, anyone with injection molding machines can do what we do. What makes us stand out is our customer intimacy and continuous improvement attitude. Rosti is only successful if our customers are satisfied and profitable, which translates to repeat business for us.
The composites-intensive VTOL platform is next expected to undergo a series of test flights in various conditions to validate its performance, safety and reliability, leading up to eventual certification.
Thousands of people visit our Supplier Guide every day to source equipment and materials. Get in front of them with a free company profile.
Kennametal will cover the influence of different composite materials characteristics on drilling performance and how to optimize the process. Agenda: Who is Kennametal? Hole making challenges in composite materials Innovations for hole making applications Upcoming events and academic partnerships
CompositesWorld is the source for reliable news and information on what’s happening in fiber-reinforced composites manufacturing. About Us
As production of the A350 XWB ramps up, so does manufacture of the thermoplastic fuselage clips the plane requires. HPC sees how it’s done.
Arris presents mechanical testing results of an Arris-designed natural fiber thermoplastic composite in comparison to similarly produced glass and carbon fiber-based materials.
We look at many areas of the part design. Is it feasible for injection molding? If not, Rosti will redesign the part and send an updated 3D CAD file back to customer with comments and a design analysis report showing before and after images and explaining the rationale for our suggestions to modify the design.
This is a critical success factor when engineers are trying to push design limits. We live in a world where if you are not progressing, you are going backwards. This process allows designers to “fail forward,” to iterate designs quickly and at a fraction of the traditional costs for molded parts.
Closed mold processes have many advantages over open molding. In this knowledge center, learn the basics and vital tools needed to produce parts accurately.
Rosti’s Digital Innovation Laboratory used 3D printing to create prototype injection-molding tools, which allowed engineers to have prototype parts for the test within 72 hours. Production tooling—32-cavity molds—was ready just five weeks later, and the diagnostics company began serial manufacturing of the test under ISO-13485 conditions.
Overmolding offers aerocomposites molders the advantages inherent in both molding “worlds”: Complex aerospace thermoset composites can provide desired functionality and strength at low weight but “require hand layup and autoclave processing, resulting in parts production that takes hours to days,” comments Kneath.
Herone, Spiral RTC, Teijin Carbon Europe and Collins Aerospace Almere recycle A350 thermoplastic composite clips/cleats waste into rods for the all-thermoplastic composite Multifunctional Fuselage Demonstrator’s crown.
The ASSEMBLY Show has welcomed thousands of engineers and manufacturing executives to Rosemont, IL since 2013. This interactive 3-day Show encourages participants to discover new assembly resources, automate existing processes, and accelerate their business and career while experiencing equipment hands-on, evaluating new products, learning from experts, and networking with industry professionals.
During this webinar, the audience will be introduced to a variety of fiber composite technologies — as well as the machines and equipment — from short fibers to continuous fibers, from thermoset to thermoplastic, as well as the according process technology, including a special focus on long-fiber injection (LFI) and structural composite spray (SCS). Focus markets include automotive, aviation and AAM, transportation, and construction. This webinar will provide a detailed overview of according application examples. Agenda: Long fiber injection (LFI) Structural composite spray (SCS) Resin transfer molding (RTM), wet compression molding, etc. Pultrusion FiberForm
Recoat temperature, part orientation and bead geometry are some key design variables to consider for a successful and reliable large-format additive manufacturing (LFAM) process.
Cost optimization is another key area that we evaluate. Rosti has implemented many creative solutions over the years, including alternative materials, part consolidation, swapping metal parts for plastic ones (and vice versa), and the elimination of post-processing steps.
The JEC Forum DACH is a business meetings event organised by JEC The JEC Forum DACH is organised on October 22 and 23, 2024 by JEC, in partnership with the AVK, gathering the composite materials community from the DACH Region (Germany, Austria and Switzerland).
The Marservis PROeco is a mass transportation marine vessel using Bcomp natural fiber for interior parts in place of standard materials.
The composites industry plays a crucial role in developing lightweight and durable materials for a range of applications, including those critical to national defense. One key focus area is the development of advanced structural materials and manufacturing technologies that support next-generation space, missile and aircraft systems for the U.S. Department of Defense (DOD). ARC Technologies LLC (ARC), a division of Hexcel Corporation, based in Amesbury, Massachusetts, is a provider of advanced composites structures, specialty materials and other unique products that provide the U.S. Department of Defense with advanced capabilities to protect service members while in harm’s way. This team’s specialty is to understand a specific need from a program office, PEO, platform manufacturer or other offices within the DOD. With that understanding, the team can design a solution, develop a prototype for test and evaluation, perform extensive in-house testing — including electromagnetic, environmental and structural testing — and then partner with the customer through platform evaluation. The Hexcel Amesbury division has a team of engineers on staff, including mechanical, chemical, electrical and research and development specialists that can provide design, testing and manufacturing capabilities to service customer requirements from concept through production. This presentation will illustrate capabilities in advanced composites and other specialty materials structures, focusing on the Hexcel Amesbury team's niche in electromagnetic signature reduction and other unique capabilities.
How the predictive tool “CZone” is applied to simulate the axial crushing response of composites, providing valuable insights into their use for motorsport applications.
Stillman: We have customers ranging from manufacturing immaturity to international corporations that have as long a history in plastic parts as Rosti does. That said, we do have customers that surprise us and have been able to teach us about a particular design or material application. We value these interactions, as nothing is ever black and white. There are always compromises and trade-offs to be made. Conversely, we also have customers that believe they have “been there and done it all,” so extra care must be taken to prepare supporting evidence for our proposals. This would include simulation data, past product data, theoretical calculations, prototype tooling and other information.
Efficient, high-quality, well-controlled composites manufacturing at volume is the mantra for this 3D weaving specialist.
Prepreg co-molding compound by IDI Composites International and A&P Technology enables new geometries and levels of strength and resiliency for automotive, mobility.
That got us thinking: How could we get molded parts quicker and cheaper in the development phase? The answer was to print the mold, as well! It took a lot of development work, but we have perfected the process of 3D printing mold tooling. As a result, we can take a customer’s design from print to part in 72 hours. That includes design analysis, mold-flow analysis, part prototyping, tool prototyping and injection molding.
The composite tubes white paper explores some of the considerations for specifying composite tubes, such as mechanical properties, maintenance requirements and more.
Foundational research discusses the current carbon fiber recycling landscape in Utah, and evaluates potential strategies and policies that could enhance this sustainable practice in the region.
Over the last 8 months, Archer Aviation has completed a total of 402 test flights with its composites-intensive aircraft, adding to key milestones.
Explore the technologies, materials and strategies used by composites manufacturers working in the evolving space market.
Recycled fibers, in-situ polymerized PA12 and steel inserts combined in one-shot process to cut weight 40 percent at competitive cost, cycle time and safety.
CAMX 2023: Startup Weav3D will be demonstrating its two collaborative automotive demonstrator parts and present two conference papers.
Increasingly, prototype and production-ready smart devices featuring thermoplastic composite cases and other components provide lightweight, optimized sustainable alternatives to metal.
“The industry needed overmolding,” he explains, like the organosheet process now common with polyamides and polypropylene in the automotive industry (see “CAMISMA's car seat back: Hybrid composite for high volume,” under "Editor's Pick's"). Aerospace parts manufacturer Tri-Mack (Bristol, RI, US) already had begun exploring this type of PEEK processing as part of its thermoplastic composites development. The two have now demonstrated a new hybrid molding process for PEEK that uses a lower temperature continuously-reinforced Victrex polyaryletherketone (PAEK) composite as a substrate, overmolded with short fiber-reinforced PEEK, to produce a high-performance loaded bracket that is as much as 60% lighter than comparable metal components.
CompPair and Composite Recycling introduce a roof scoop made of recycled fibers to an eco-efficient rally buggy, which channels airflow to the engine for optimal, sustainable performance.
The ITHEC 2024 will take place from the 9 to 10 October 2024 in Bremen, Germany. At the 7th International Conference, more than 300 participants from around the world will be presenting and discussing newest scientific results, meet leading international specialists, share their expertise and start business co-operations in the field of thermoplastic composite technologies. The international exhibition will feature 40+ exhibitors showcasing all steps of the supply-chain. Be it materials, machines, testing, processes, or solutions. By combining the exhibition and the conference ITHEC is further fostering the inter-connectivity between science and industry.
We consider the resin, too. Is it suitable for the purpose? Will it achieve the cosmetic and functional requirements that the customer has specified or, in the absence of such a specification, what Rosti engineers envisage to be the critical functional and quality requirements.
This collection details the basics, challenges, and future of thermoplastic composites technology, with particular emphasis on their use for commercial aerospace primary structures.
“We see real opportunity to significantly expand PEEK applications in aerospace,” says Herr. And, says Kneath, “We are also exploring applications for other industries as a next step.”
Knowing the fundamentals for reading drawings — including master ply tables, ply definition diagrams and more — lays a foundation for proper composite design evaluation.
Recoat temperature, part orientation and bead geometry are some key design variables to consider for a successful and reliable large-format additive manufacturing (LFAM) process.
Prepreg co-molding compound by IDI Composites International and A&P Technology enables new geometries and levels of strength and resiliency for automotive, mobility.
CW’s editors are tracking the latest trends and developments in tooling, from the basics to new developments. This collection, presented by Composites One, features four recent CW stories that detail a range of tooling technologies, processes and materials.
The composites industry is increasingly recognizing the imperative of sustainability in its operations. As demand for lightweight and durable materials rises across various sectors, such as automotive, aerospace, and construction, there is a growing awareness of the environmental impact associated with traditional composite manufacturing processes.
Hybrid over molding design: This CAD image shows a continuous-fiber-reinforced PAEK composite (red) with a PEEK overmold (green). Source: Tri-Mack
Preconsolidated carbon fiber/PPS and PEEK and automated thermoforming enable six-figure production of connectors for the Airbus A350 XWB.
Stillman: It’s had a huge impact. 3D printing can get designs from the screen into the designer’s hands quickly and cost-effectively.
Validation of 80-100% tensile strength and comparability to injection molding via Voxelfill extrusion process was achieved through plastic and fiber-filled test series.
Performing regular maintenance of the layup tool for successful sealing and release is required to reduce the risk of part adherence.
Our top two priorities are always safety and quality. These are at the forefront of all our design and process verification protocols.
JEC World 2024: Bally Ribbon Mills is displaying film-infused 3D woven joints, woven thermal protection systems (TPS) and woven composite 3D structures.
That makes creating molds for prototype parts a gamble. It can take four weeks and tens of thousands of dollars to produce traditional molds for prototype parts. As a result, engineers must be confident in their designs before committing the time and resources to make molds.
A combination of Airtech’s 3D printing materials and Ascent’s production capabilities aim to support increased use of composite additive tooling in spaces like defense and aerospace.
In the Automated Composites Knowledge Center, CGTech brings you vital information about all things automated composites.
“This is an enabling technology, offering so many opportunities beyond brackets,” says Kneath, adding that, given PEEK’s mechanical and elevated-temperature performance and chemical/corrosion resistance, there are few areas where it’s not a suitable solution. “We could be talking more complex housings or different types of panels with very thin, overmolded fiber-reinforced ribs.” Tri-Mack also sees opportunities in the process for imparting multi-functionality. “We have evaluated technologies that would add lightning strike protection (LSP) paths or EMI shielding. This is typically done with secondary coatings or by adding a metallic layer to the layup,” Kneath says, but Tri-Mack is now exploring how to do this via the compounds used in the hybrid processing.
This session is designed to demonstrate the benefits of ultra polymers for aerospace applications with real case examples of Syensqo's polymer portfolio. Agenda: Introduction to ultra polymers (PAEK, PEKK, PEEK, PAI) key features Application of ultra polymers in aerospace: concrete examples Benefits of ultra polymers: enhanced performance, durability and cost-efficiency
In these sessions, experts will discuss the emerging hydrogen economy and the opportunities for composites in this lucrative space.
American Bureau of Shipping (ABS) certifies use of jointly developed CFRP repair technique on FPSO and FSO industrial systems, addressing traditional steel restoration challenges.
Because the substrate blanks are multi-ply composite layups, they are easily tailored for specific properties and/or load handling. For example, Tri-Mack has the ability to place and orient UD tapes in the blanks, using in-house automated molding cells. In fact, the company’s Advanced Composites Center, adjacent to its main plant, was designed specifically to enable automated layup, consolidation and thermoforming of composite materials in conjunction with its legacy injection molding capabilities, to replace both metals and thermoset composites in aerospace applications.
Prepreg co-molding compound by IDI Composites International and A&P Technology enables new geometries and levels of strength and resiliency for automotive, mobility.
CompositesWorld’s CW Tech Days: Infrastructure event offers a series of expert presentations on composite materials, processes and applications that should and will be considered for use in the infrastructure and construction markets.
Stillman: Other than variation in costs, different materials have different properties. For example, polycarbonate should not be used with alkaline aqueous solutions or aromatic and chlorinated hydrocarbons, since these would degrade and weaken the part. Whenever we work with multi-material assemblies, we assess the chemical compatibility to ensure that there will be a chemical bond between them. In cases where chemical bonding cannot be achieved, and the materials cannot be substituted, we would recommend design changes to facilitate mechanical bonding.
Suppliers of thermoplastics and carbon fiber chime in regarding PEEK vs. PEKK, and now PAEK, as well as in-situ consolidation — the supply chain for thermoplastic tape composites continues to evolve.
“Our idea was to combine the chemical resistance and moldability of thermoplastics with the high performance and light weight of composites,” says Tri-Mack director of sales Tom Kneath. “Only then can thermoplastic composites penetrate into new applications where plastic alone cannot go because of the mechanical properties required.” But the organosheet process is not without issues. Traditional steps include preheating a preconsolidated thermoplastic laminate to remelt temperature, transfer to an open injection mold, closing the mold to thermoform the blank to shape and then injection overmolding with fiber-filled melt to provide the finished three-dimensional surface. As presented by Alan Wood at the 2nd International Conference and Exhibition on Thermoplastic Composites (ITHEC 2014, Oct. 27-28, Bremen, Germany), Victrex had to work through an array of issues, including support of the substrate during preheating, control of fiber orientation during forming, potential restriction to a uniform blank thickness to ensure matrix melting, and the development of polymers that would indeed fuse together during overmolding.
EU project will develop bio-based, repairable and recyclable vitrimer composites and advanced sensors for highly reliable, sustainable wind blades.
CompositesWorld’s Tech Days: Design, Simulation and Testing Technologies for Next-Gen Composite Structures is designed to provide a multi-perspective view of the state of the art in design, simulation, failure analysis, digital twins, virtual testing and virtual inspection.
Sponsored Content is a special paid section where industry companies provide high quality, objective, non-commercial content around topics of interest to the ASSEMBLY audience. All Sponsored Content is supplied by the advertising company and any opinions expressed in this article are those of the author and not necessarily reflect the views of ASSEMBLY or its parent company, BNP Media. Interested in participating in our Sponsored Content section? Contact your local rep!
CompositesWorld's Carbon Fiber conference offers you cutting-edge information and access to industry experts in streamlining manufacturing costs, market outlooks and forecasting, and more. You will make invaluable contacts as you meet and network with the industry's most innovative and influential leaders at Carbon Fiber. __PRESENT
Stillman: First, we need to clarify what the customer’s objectives are. Is the product manufacturable? What can Rosti do to optimize cost to customer, operational performance for Rosti, and sustainability for all.
Analyzing structural resonance of the aircraft under various loads becomes a critical step in obtaining flight certification.
Continuous fiber-reinforced thermoplastic composite targets full circularity in aircraft interior applications, with FST, impact resistance and toughness features.
Victrex also proved fiber orientation can be maintained during forming and that there is the potential for variations in substrate laminate thickness, which enables local tailoring of stiffness in the final part. The process requires less energy than anticipated, with substrate preheating typically maintained at 200°C.
Base Materials introduces a high-performance, toughened epoxy tooling board designed for thermoforming and vacuum forming processes, direct-to-part applications and more.
Rosti Group has helped a global molecular diagnostics company to begin manufacturing a COVID-19 saliva test, providing laboratory-quality results in 15 minutes. This will allow nonmedical personnel to obtain fast, on-site detection of the coronavirus at the point of need.
Whether you need a six-axis cobot for machine tending or a desktop Cartesian robot for dispensing adhesive, you’ll find it at The ASSEMBLY Show. Before you hit the show floor, tune into this exclusive panel discussion featuring executives from four of the nation’s top suppliers of robotic technology: FANUC, Janome, Schunk, and TM Robotics.
A report on the demand for hydrogen as an energy source and the role composites might play in the transport and storage of hydrogen.
GETTING A QUOTE WITH LK-MOULD IS FREE AND SIMPLE.
FIND MORE OF OUR SERVICES:
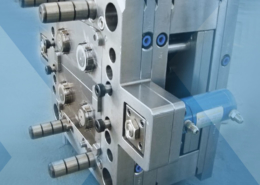
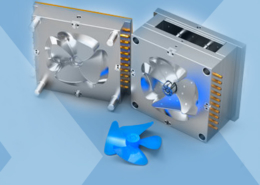
Plastic Molding

Rapid Prototyping
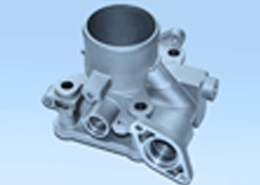
Pressure Die Casting
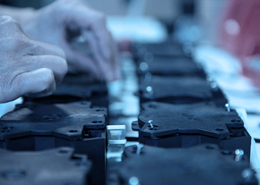
Parts Assembly
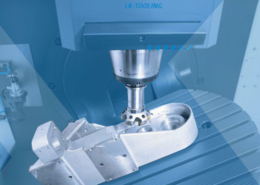